
Ever since we adopted improved fuel management methods, we’ve enjoyed a decade of no carburetor maintenance-not on the twin 9.9 hp engines that ran our catamaran, not on the dinghy kicker, and not on our trimaran. Not on any of our chainsaw or blower motors. Given the quarterly ritual wed enjoyed before, its been wonderful.
Ever since our initial studies of corrosion in August 2012 and November of 2012, we’ve kept an eagle eye on gasoline and diesel additives, researching and testing their effectiveness on reducing corrosion and gumming. Why the fanatical focus on corrosion? Because all of our research and all of our testing (see PS November 2015) suggest that the primary cause of gasoline instability, including gum formation, is metal ions resulting from corrosion of metals. We have also seen that corrosion products are the most common cause of clogging, and that these deposits are harder to remove because solvent carb cleaners can’t dissolve them.
New products have entered the market and old products have been reformulated. Frankly, we expected that all of them were going to wow us this time, with astounding ability to protect fuel systems. But alas, that was not to be. Before we get into test results, its important to review the basics.
Gasoline Management
We know we’ve gone through this before, but proper gasoline tank management can eliminate fuel system problems. Here are the basics:
Keep Water Out. Water in combination with ethanol accelerates corrosion, which is the leading cause of carburetor clogging. This means checking your filler cap for a good O-ring seal and confirming that water cannot find its way in through the vent. This is prevented with a good high loop or a P-trap style vent.
Keep Water Vapor Out. Ethanol has a propensity for absorbing water from the air during breathing. It does not have to be enough to cause separation or result in visible water precipitation to increase corrosion, only enough to allow free transport of ions. The mere 0.15 percent water used in our testing accelerated corrosion between 10 and 100 times! Silica gel vent filters have proven effective for fixed tanks (see PS February 2013), eliminating water absorption, reducing corrosion, and reducing gasoline evaporation. Portable and integral tanks can be protected by simply closing the vent anytime the engine is not actually running.
Keep Tanks Out of the Sun. UV is tough on the tanks and also catalyzes fuel deterioration. Its not good for the plastic either. Direct sun heats the tanks, increasing breathing and causing potential dangerous pressure buildup in sealed tanks. Add a cover and/or store tanks out of the sun.
Add a Filter. Some smaller dinghy kickers lack any filtration, other than a crude strainer in the fuel tank drain. Cut the line in a convenient place and insert a lawnmower filter. Easy, just a few buck, and much easier than dealing with a balky motor. Carry a few spares. Although large separating filters, such as the Racor 500 series, will work with non-ethanol gas, they will not separate water from E10 gasoline. The aqueous phase of E10 is actually 80-90 percent ethanol and is not much heavier than water. Because this solution is mostly alcohol, the hydrophobic (water separating) media in your filter will still allow the solution to pass.
In the other scenario, in which the water has completely separated out of solution in the tank, the volume of water will overwhelm your filter. You will need to pump out the tank.
Use an Anticorrosion Additive. Follow the recommendation of this article. Biobor EB and Sta-bil 360 are our top picks.
Use your fuel. Run your engine enough to go through your supply several times each season. This also freshens up the gas in the lines and carburetor.
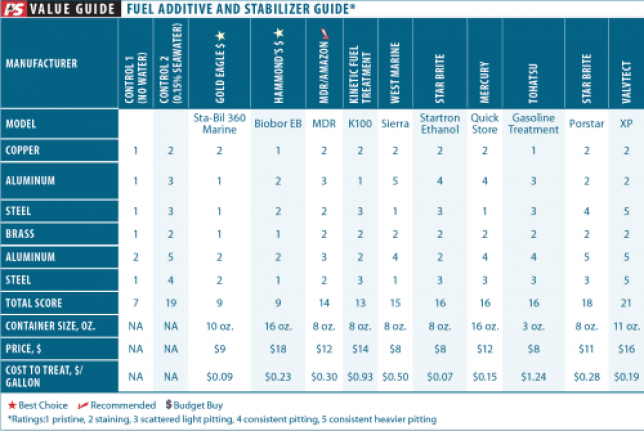
What We Tested
We collected samples of ten gasoline additives from local and on-line chandleries. We did not repeat the full set from our 2012 tests. In general, those recommendations still stand, though a few products were reformulated and re-named.
How We Tested
Fundamentally, we used the same test procedure we followed in our 2012 testing. Gasoline samples were doped with 0.15 percent of a synthetic corrosive water to mimicking the effect of seawater and rainwater contamination. Gasoline additives were dosed at the manufacturer recommended rates. Standard ASTM metal corrosion test coupons were then immersed in the mixture for two months in one liter jars that were vented in a calibrated way to mimic real world tank conditions. Samples of aluminum, copper, and steel, and aluminum, brass, and steel were galvanic coupled to mimic normal groupings in carburetors and fuel tanks.
The aluminum alloy is a casting alloy commonly used in outboard carburetors. Controls included one sample set with no corrosive water or venting, and one sample set with venting, corrosive water, and no additive. The method was developed with input from experts in the field, but has not been adopted as an ASTM method.
Observations
The sealed, no-water sample showed virtually no corrosion. Without water, ethanol gasoline is stable and non-corrosive to metals. The control sample showed considerable corrosion, and is typical of a real-world tank that has absorbed water and perhaps seen a few drops of seawater. In fact, many of the additives did not offer any obvious benefits, scoring no higher than no additive at all.
Our primary concern is corrosion of aluminum when it is coupled with brass. Brass jets and a cast aluminum bowl is a common combination, and we have seen many pitted bowls. Only a few of the additives were effective in preventing aluminum corrosion and pitting.
Copper and brass were never damaged beyond a slight patina. Steel is also a common victim, either in the form of valves or tanks. Again, only a few additives were effective. We recommend using only those additives that prevented all but the lightest, scattered pitting.
Products
Some users of these fuel treatments suggest that they help with other operational problems such as fuel tank cleanliness and general operation. We did not test these attributes. All of the products in our test were obtained anonymously new either through reputable online sources or direct from the maker.
Biobor EB
This product from longtime contender Hammonds Chemical was a favorite in our 2012 testing. It once again it provided superior corrosion protection. The treated sample compared with the no-water control. Dont confuse with Biobor JF, which is a diesel biocide.
Bottom line: This our Best Choice and is what we have been using for the last 10 years.
Sta-Bil 360 Marine
This new product from Golden Eagle has been improved since our last round of testing. Sta-bil Ethanol 360 delivers impressive corrosion protection, earning a solid tie with Biobor EB.
Bottom line: Results were right up there with Biobor JF, making it another Best Choice.
Store-N-Start
Very close in performance to Sta-bil 360 and Biobor EB, this product from MDR Amazon falls within our error bar as an equivalent choice.
Bottom line:Recommended.

K100, Kinetic Fuel Treatment
Corrosion protection was impressive, but were a little nervous about the formulation. The solvent base is primarily butyl cellosolve, which increases water stability in gasoline and inhibits phase separation. Several outboard OEMs expressed concern about the effects of cellosolve on gaskets, elastomers (fuel pumps, lines, bulbs,and intake manifolds), but they did not provide concrete limits or evidence of problems. We ran an abbreviated trial of all products adding trace contamination with acetic acid during our test development process; it was suggested that this was possible in E10. In the end, we decided the new test was too severe, but K100 succeeded in that test when all others failed.
Bottom line: This is an interesting product, but have enough questions to reserve judgement until we complete more testing.
Quick Store
In the last round, this product from Mercury Marine impressed testers, but in this round it let us down on aluminum protection.
Bottom line: Based on our results in this round, there are better anti-corrosion additives.
Tohatsu Gasoline Stabilizer
This was the most effective additive in protecting copper and brass, suggesting it protects against gum, but it let us down when protecting aluminum.
Bottom line: There are better anti-corrosion additives.
Star Tron Enzyme Fuel Treatment
One of Star brites most popular additives, Star Tron did well reasonably well in our last round of tests, but not as well this time. Aluminum protection is a weakness.
Bottom line:There are better anti-corrosion additives.
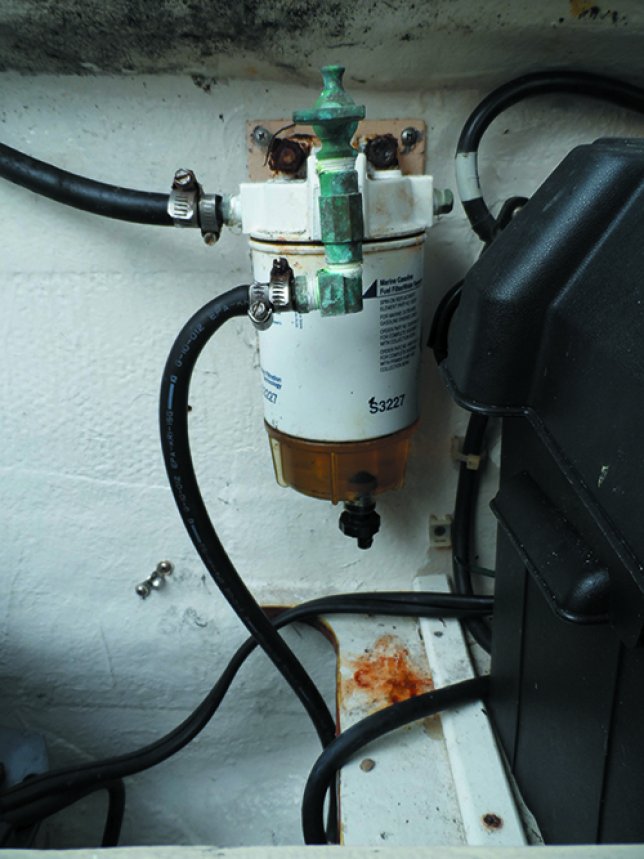
Prostar Gasoline Stabilizer
This is Star brites premium stabilizer product. As it was for many products, aluminum was a weakness.
Bottom line: There are better anti-corrosion additives.
Valvtect XP
This product from marine industry veteran Valvtect has been reformulated (previously ValvTect Ethanol Treatment) since our 2012 testing. It may do other things better, but in our tests, the protection against corrosion has declined.
Bottom line: Not recommended this time.
West Marine
Like Star Tron, this product from
Sierra was OK on steel, but inconsistent on aluminum.
Bottom line: There are better anti-corrosion additives.
Conclusion
Biobor EB and Sta-Bil 360 Marine have moved ahead of the field, providing impressive protection against corrosion of critical gasoline system components. With regular use and good fuel system management, carburetor corrosion and clogging should be a thing of the past. It has been for us.