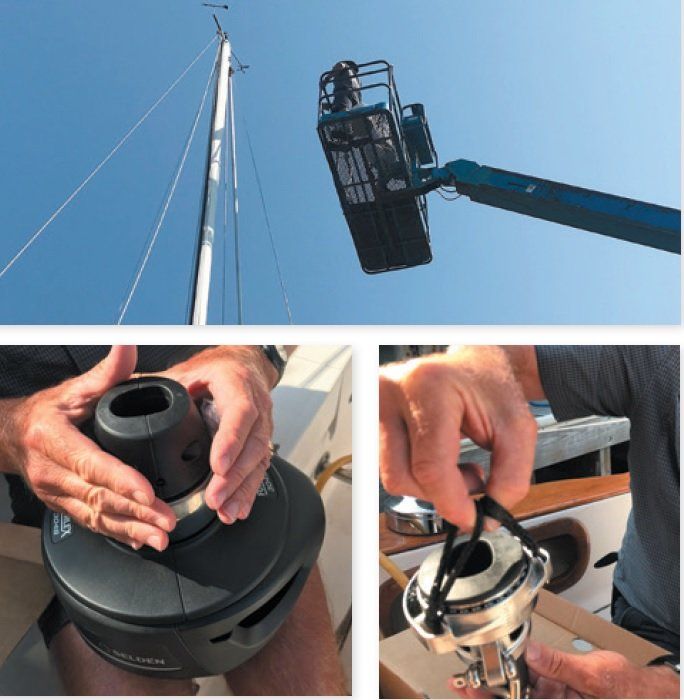
You know it’s time to swap out your old headsail furler for a new model when the springtime hoist encounters excess friction and even hard stops on its way to the masthead. That balky headsail hoist last summer and a friction-laden furling line had us consulting websites for options. Practical Sailor has made several firm recommendations of Selden gear over the years, so a Selden Furlex rose to the top in our planning.
The last time we reviewed headsail furlers in this size (see PS August 2009) and price range we came to this conclusion: Among a field of quality products, Furlex stands out for its investment cast stainless hub and bearings. We named it a Best Choice and also lauded Selden for its all-you-need approach. This article is a follow up to that recommendation, focusing on installation.
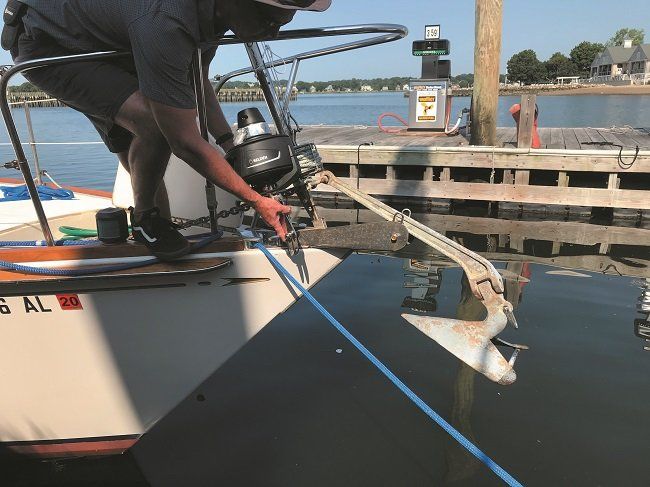
We purchased a Selden 304 with a nine-inch furling drum to replace our original Plastimo seven-inch, now destined for the Smithsonian. According to Selden literature, our boat was right on the border between the 304 and the smaller 204. We rounded up.
What’s in the box?
It’s easy to underestimate what goes into a headsail furler until you see all the bits and pieces laid out and ready for assembly. According to Selden’s Scott Alexander, a Furlex system comes as a complete package right down to the replacement forestay, nuts and bolts for the turning stanchion blocks, a Sta-Lok terminal, furling line, even a pre-feeder. The unit arrives in one large square box, a flat box with the eight-millimeter forestay, and a sizeable packing tube for the headfoil sections and full-length plastic distance tubes inside them.
The distance tube runs the length inside the foil, preventing metal-on-metal contact with the headstay.
“We started using distance tubes from the beginning of the Furlex product line in 1986,” said Alexander. “Not only does it keep the stainless wire insulated, but also keeps the forestay located in the middle of the rotation. The distance tubes don’t take any load, and don’t require servicing.”
Manuals and videos for competing units tout the fact you can use your existing headstay with their roller-furlers, but they add the caveat you’ll probably be replacing your forestay anyway—and most sailors do, which means you should factor in a trip to the rigger for a new headstay when comparing the Selden to other systems.
The Furlex (and the Harken MkIV) boast two independent ball-bearing swivels at the tack. One swivel lags behind the other when the furling line is taken up, which flattens the rolled headsail around the narrow-profile, twin-groove extrusion. Twin swivels at the drum allows the tack to lag, allowing the middle, fullest section of the headsail to furl flat around a single uniform foil. We can attest that this results in a neatly compressed, wrinkle-free roll. Having two luff grooves on a cruising furler allows for the possibility of wing-and-wing downwind sailing and quick headsail changes while racing. The Selden 304 nine-inch drum can be easily removed, a nice feature for weight conscious racer-cruisers.
Selden touts its reliance on marine-grade stainless steel ball bearings in its turning components. This avoids the potential sun damage plastic ball bearings may be heir to, and the corrosion of high-carbon steel (see adjacent article, Bearing down on furling differences).
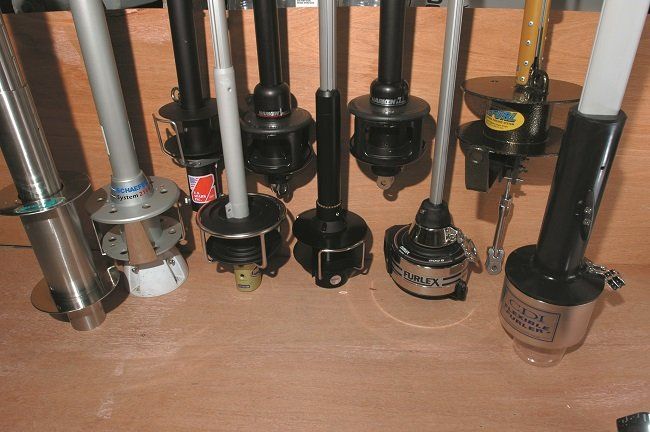
Can I do it myself?
The question remains: How much might we be able to do ourselves?
The answer is. . . quite a bit, but certainly not all. A true do-it-yourself install requires a good level of experience, a solid team and a set-up that includes a safe, expedient way to get to the masthead to detach the old furler and re-attach the new one.
The need to work aloft is often the biggest roadblock. You’ll be using your headsail halyard as a temporary forestay, so you’ll need to haul the new furler up the masthead on a spinnaker halyard while the mainsail halyard is pressed into service for the bosun’s chair. If you don’t have a spinnaker halyard (we don’t) then you’ll need to figure out a way to go aloft.
Fortunately, Norwalk Cove Marine in Norwalk Connecticut, arranged for rigger Sean Hussey to give us a hand-and for $220 we booked their Genie articulating boomlift (a.k.a. “manlift”) for the day. Getting the boat close to the manlift is the key, so call around to find a similar solution near you. Norwalk Cove also gave us the run of their rigging shop, complete with 60-foot workbench pre-fitted with measuring tape and cutting tools at the ready.
Our install was not entirely do-it-yourself, but the Selden system encouraged a great deal of owner involvement. We installed the Furlex in record time with minimal fuss using basic hand tools: a hacksaw, adjustable wrenches, pen, calculator app, and a file. The Sta-Lok terminal was fitted with nothing more than a pair of adjustable wrenches and a Leatherman multi-tool. (See PS June 2015, Step by Step: Threaded Terminal Fittings.)
“When people ask me if they can install a Furlex themselves, I ask them if they’ve ever done a Sta-Lok terminal,” Alexander said. “That usually separates the true do-it-yourselfers from the wannabes.”
The Sta-Lok swage-less terminal has multiple hundreds of thousands of sea miles and is approved by riggers, boat makers, round-the-world racers, and Lloyds of London. Like the similarly designed Norseman terminal, it offers the benefit of disassembly and inspection well down the road. Unlike a swage fitting, mechanical terminals like a Sta-Lok can be assembled at the dock without a lot of elaborate machinery.
Perhaps the most unnerving part of working up a Sta-Lok terminal, after you slide on the units threaded male barrel, is unwrapping the wire strands from your shiny new forestay to expose the core. (And lets not forget the hives caused by that no-turning-back forestay cut.) A conical wedge is then slid over the core, a small former intended to crimp the wire strands is inserted into the female receiver and the pieces are ready to be threaded back together with a liberal application of liquid thread lock (included!).
We’re glossing over some of the subtleties—like the need to expose the core a few millimeters out the end of the wedge, ensuring no wire strands become lodged in the wedge’s compression gap, and the deceptively easy task of working the wire strands back around the core.
We learned that with some solid assistance from a knowledgeable rigger (and a You Tube video: https://bit.ly/2ks4Qdw), one should fear no Sta-Lok. That accomplished, you’ll still have to be on your game when it comes to putting the rest of your new system together. (For a more in-depth look at Sta-Loks and other swageless terminals, see PS June 2015, Screw On Rigging Terminals; PS April 2015, Mechanical Terminal Pull Test; PS May 2015, Hidden Causes of Rig Failure; and the Inside Practical Sailor Blog post Mechanical Rigging Terminals, to Seal or Not to Seal?).
When we say complete . . .
…We really mean complete. Aside from the aforementioned parts and pieces, the Selden comes with all the terminals, foil sections, fasteners, joining sleeves and other elements right down to the braided furling line.
According to Alexander, “We include everything because we want to maintain the integrity of the system, with no parts that you didn’t know you had to buy.”
To specify the system that’s right for your boat you need to know the displacement, the length of the existing forestay and the pin size. We triangulated these parameters using Selden’s excellent user manual, which contains a very good worksheet to precisely establish where you’ll cut the provided 50-foot forestay. You’ll need to account for deductions like the extension legs for ground-tackle clearance. Selden’s website also has a righting moment calculator in kilo-Newtons per meter at 30-degrees of heel, which further refines the system that’s right for your boat. As mentioned, First Light was right on the cusp of a 304 or its smaller stablemate, so we over-specified for not much more money. The worry was that a nine-inch furling drum up in the pulpit might look a little horsey but it turned out fine, with plenty of clearance.
Measurements in the worksheet of this Swedish-built system are in millimeters, although the manual has both inches and feet. Metric avoids the 16ths, and 32nds, etc. Selden has a calculator to do all the math for you, yes this is only metric: http://www.seldenmast.com/en/services/calculators/furlex_calculator.html We also invited multiple parties to look over our math before arriving at the final cut, which we survived with just a dash of apoplexy. (Note to self: Next time make the final cut before lunch when all the calculations are fresh.) It’s also important to measure and cut the topmost foil section and internal distance tube. Again, the Selden worksheets and clear diagrams make this painless.
Our old Plastimo was held together with rivets, to which we were delighted to bid adieu. Selden relies on short joining sleeves that live inside the foils and bridge the gap between the foil sections. Aluminum connecting plates rest on the joining sleeves and slot into pre-drilled holes in the foils (see the related article, Measure Twice, Double-check Your Math for Perfect Fit. ). The Selden system offers a smart, clean design. The profile of the headfoil section is about 30-percent slimmer, reducing weight and windage aloft. The rivet-less system offers the advantage of a solid connection, but also keeps the foil sections a fraction apart to keep them from grinding against each other, especially downwind.
Assembly Precautions
Precautions include restraining the coiled forestay when it comes out of the box so it doesn’t flail around and cause injury; cleating, not shackling, the headsail halyard to a deck fitting forward when its used as a temporary forestay during the installation; maintaining a plus-10 degree angle between the halyard swivel and the sheavebox to avoid rig-threatening halyard wrap; spreading split pins adequately to secure clevis pins; and avoiding winching in the furling line, especially against a loaded sheet.
“Sometimes people tighten the halyard of a reefed headsail,” said Alexander. “This action doesn’t tighten the luff, but instead puts the load on the extrusion. Take a reefed sail, tighten the halyard, have some slack in the forestay and now add some big waves and you have a furling system that is taking the rig loads instead of the forestay.”
Ouch!
It helps to know what’s going on at your masthead. Will you have properly sized holes to accept your new toggle and clevis pin? Or a T-adapter (common on some fractional rigs)? Or a stemball? Still found on boats of a certain vintage. If its a stemball you’ll need an adapter. The extension link at the bottom of the system (to clear the anchor) was one of only two Selden pieces that needed to be ordered extra.
The MSRP of our Selden 304 was $4,875. It will fit masthead boats with displacements up to 18,000 pounds or fractional rigged boats up to 22,000 pounds. It includes a 5/16th wire (8mm), a bottom-end Sta-Lok terminal, an optional system-length adjuster, and everything else you’ll need including the torx bits.
What else is out there?
If you’re in the market for a replacement headsail furler you’ll have an abundance of choices that will fit your boat, your cruising style and your budget. Finding a system that’s right for you comes down to your own personal algorithm.
Racing or cruising? There are systems, like Furlex, that offer a removable drum so you can achieve a lower tack attachment typical of a racing headsail if you want to cruise the islands before Race Week. This is where the twin luff grooves come in handy.
Boat less than 30-feet LOA? You might want to consider the less expensive options from CDI, Alado, Reef Furl and Spin Tec with integral halyards and no upper swivel. (See PS September 2009, Headsail Furlers Sans Swivels.) You can use your original forestay for most of these applications, but we don’t consider that a huge advantage because most aftermarket installations will beg for a replacement anyway.
For bigger boats? Nobody doesn’t like Harken, and this proud American company will offer years of cruising and racing enjoyment. We have recommended the Harken MkIV in previous reports, and the more recent ESP line is intended for a lighter shade of cruising. In either case, you’ll have to order a replacement forestay if you decide installing a new furler is a good time to make a change. Harken literature recommends checking with a rigger on forestay condition before installation. Harken also requires separate purchases for furling lines and ratcheting stanchion blocks. As mentioned, we like Selden’s independent tack swivels at the drum end. The Harken MkIV has the same feature, but the ESP does not.
The Schaefer 2100 series is another strong option. Schaefer prefers riveted foil connections, because as they say rivets cannot freeze, strip, or back out. Rivets will need to be drilled out and replaced if repairs are needed. Again, after buying the system, you can use your boat’s existing forestay—but a new one might be in order.
ProFurl and Facnor, made in France and distributed in the U.S. by Wichard America have garnered thousands of sea miles and appear both robust and simple to install. There is one feature of the Facnor that I find particularly intriguing: A telescoping bottom foil that allows easy adjustment in foil section length without cutting. The Facnor system joins foil sections with Torx-head set screws, not rivets, which will ease dismantling if an owner is so inclined. The Facnor unit has stainless steel, no-maintenance bearings packed in grease. Like the Selden, it has an independently rotating tack fitting that results in a flatter roll.
At an MSRP of $2,149, the well-regarded ProFurl stacks up well on paper. But then you have to add a furling line, stanchion blocks, stem-end extension plates if you need them, a turnbuckle cylinder and a rigger-supplied forestay with terminals, on the educated guess your old one has seen better days. Still, that is a very attractive price for a proven furler, so adding these odds and ends might be cost effective.
Proof in the pudding
We had our friends at Quantum Sails Connecticut install a new #6 luff tape on our aging 120 percent headsail, and they executed the all-important tack cutback so the sail would fit. Raising an older sail on a new furling system tends to cast aside all rationality. It’s like putting bald tires on a Ferrari. So now we’ll have to take a hard look at the kitty for a sail upgrade.
Nonetheless, just as you get a bit of a thrill from that new-car smell, or the sight of a clean hard drive, there’s nothing like an effortless headsail hoist through a hands-free pre-feeder. And while we were expecting smooth on that first furl, we didn’t expect whipped butter.
So now were getting revved up for a set of lazy jacks, with maybe a stack pack . . . and new sails.
I better get back to work to pay for all this. . .

Assembling the foils and headstay is like any other job that involves cutting and measuring. Measure twice (at least) and cut once. It helps if you have a rigging shop with a long bench and the requisite tools at hand.
- The Selden foils, like most that are aimed at larger boats, have two grooves, simplifying sail changes.
- So-called “joining tubes” (unique to Selden) inside the foils push these stainless steel connecting plates up into pre-drilled holes in the foil section. No rivets or screws needed. The extra-long connector joins the foils adjacent to the luff feeder.
- The foil joining system allows a fraction of an inch stand off between the foil sections, which prevents any grinding, especially off the wind.
- The swaged eye of the old furler is anchored through a rod in the work bench next to a 100-foot measuring tape (set in epoxy so it won’t disappear). Getting an accurate measurement of your old system is key to building up the new, especially when it comes to getting a precise cut of your new forestay.
- To assemble the Sta-Lok fitting you insert a “cone” into the strands, which are carefully opened and unlayed using needle nose pliers. Selden has an easy-to-follow video illustrating the installation. Practical Sailor has also covered this skill in previous issues, along with some tips from professional riggers on how to maximize the hold. See PS June 2015 Step by Step: Threaded Terminal Fittings.
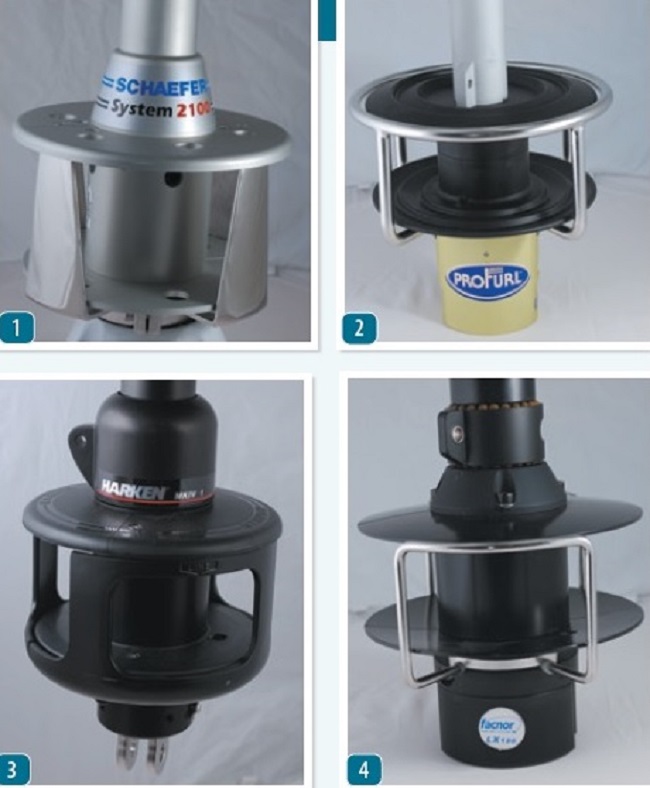
Bearing corrosion was the bane of early furlers, so our August 2009 report took a close look at this element.
1. The Schaefer’s drum and swivel features large races for its Torlon bearings.
2. The Profurl’s hardened carbon-steel ball-bearing set is packed in grease and protected by a double-lip seal. This should be checked on older units that exhibit signs of friction.
3. The Harken MKIV turns on Torlon and Delrin Balls, which are hidden away from damaging UV rays.
4. The Facnor LX 130 relies on UV resistant, self-lubricating Torlon bearings, which are easy to inspect and flush, but are exposed to the sun.
Wow, awesome article. I wonder if this paragraph is in need of a set of quotation marks?
According to Alexander, We include everything because we want to maintain the integrity of the system, with no parts that you didn’t know you had to buy.
Maybe the quotes should begin before the “We” and close after “buy”?
This is a tad confusing because without the quotes, it seems like the author of the article is saying this, rather than a third person.
Thanks. Good information. I once rebuilt an old Hood furler on the dock in Grenada. I found out that the main bearing was a wheel bearing from a GM car. It worked! It was about 15 yrs old when I rebuilt it and used it full time for another 5 yrs with no problem. Also had a boat with a Profurl ( my preference), that in nearly 20 yrs, I needed to replace the top swivel. So great luck there. Many thousands of sea miles on it. Especially where the only washing with fresh water is done by when it rains!
Love my Facnor LS 130. Super easy to install over *existing* head stay with no cutting of anything required due to the bottom ‘telescopic section’ (my head stay was less than 6 months old, hence no thought of replacing it). All of the bearings on this model are sealed. I read the instructions twice, had it installed single-handed in about 2 hours.