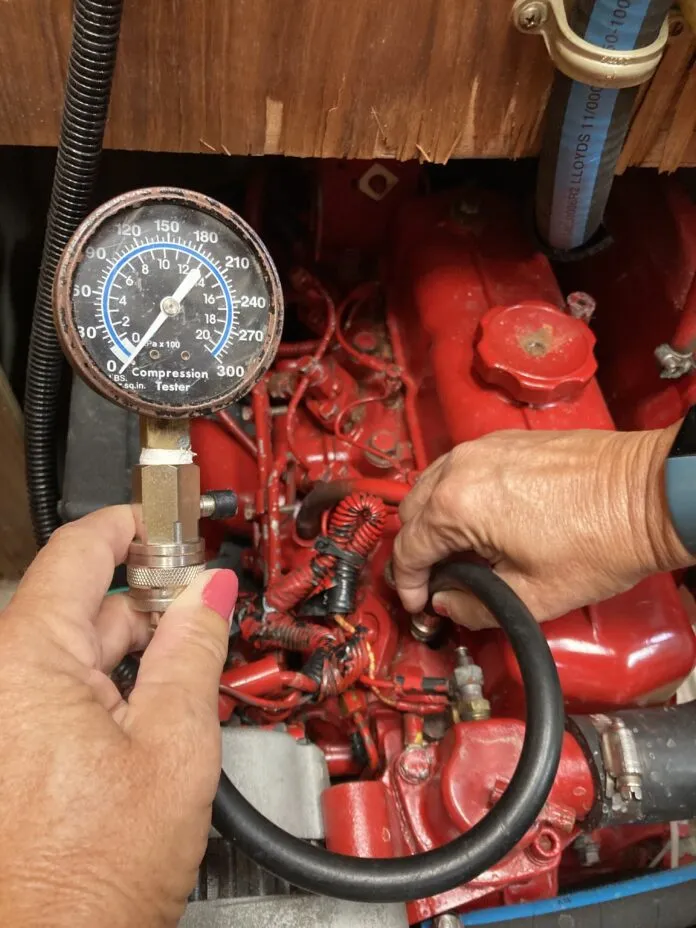
An engine compression test is an important diagnostic test that any boat owner can do with equipment that costs about $50. You can also rent a compression tester. The compression test measures the maximum pressure created in each cylinder by the pistons when the engine is cranked. The results of the test can tell you many things about the health of your engine.
WHY DO A COMPRESSION TEST?
First, a little background. For a diesel engine to work, the engine needs air, fuel, and compression. For a gasoline engine, add spark. If your engine will not start, is hard to start, runs roughly or produces smoke when it is running, the compression test is a good test to perform to help diagnose the problem quickly.
WHAT IS A COMPRESSION TESTER?
A compression tester is typically sold as a kit that has a pressure gauge, a short hose, and a variety of threaded fittings that fit the holes for glow plugs, fuel injectors, and/or spark plugs. The pressure gauge for a diesel engine will go up to 1000 psi, and the gauge for a gas engine will go up to 300 psi. The pressure gauge will hold the needle at the highest pressure it sees. A release button on the gauge will release the pressure and return the needle to zero.
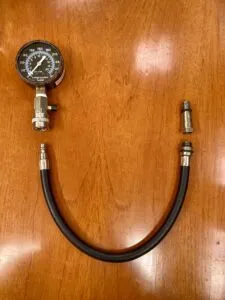
HOW DO YOU DO A COMPRESSION TEST?
- Warm up the engine to operating temperature, if possible.
- Disable the fuel flow for a diesel, or disable the ignition for a gas engine. On a diesel engine, disable the fuel flow by pulling the big red STOP knob at the helm and keep it pulled out for the test. This shuts off the fuel. For a gasoline engine like my old the Atomic 4, pull out one end of the high tension wire between the ignition coil and the distributor cap to disable ignition.
- Remove all of the fuel injectors or glow plugs for a diesel, or all the spark plugs for a gas engine.
- Install a threaded fitting into one of the holes for the injector, glow plug or spark plug.
- Crank the engine for 6 to 8 revolutions. The pressure gauge will automatically hold the needle at the highest pressure.
- Record the pressure for that cylinder.
- Press the release button on the pressure gauge to return the reading to zero.
- Repeat for each other cylinder.
WHAT CAN THE RESULTS OF A COMPRESSION TEST TELL US?
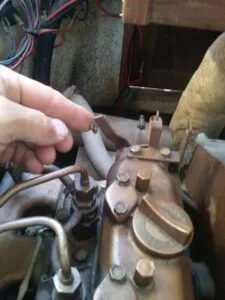
The normal maximum pressure for a diesel engine is between about 275 and 400 psi. The normal max for a gas engine is between about 125 and 175 psi. These figures depend on the design of your particular engine. I found the specifications for my Westerbeke 42 horsepower diesel engine in a technical manual that I downloaded free of charge. The manual said the pressure should be between 370 and 455 psi.
The readings for each cylinder should be within 20 percent of the average for the other cylinders. If a weak cylinder is flanked by a healthy cylinder, the problem is either valve related or head gasket related. In my case, cylinders 1 to 3 read about 400 psi, and cylinder 4 read zero. This led me to the problem of a broken valve that I saw firsthand after I removed the cylinder head.
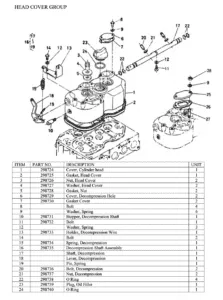
Low pressure readings could be the result of a blown head gasket. Low pressure could also be the result of piston blow-by, dry cylinder walls or valve blow-by caused by worn cylinders or piston rings, which could also cause white smoke in the exhaust. Also look for incorrect valve clearances or sticking valves. These can be checked after taking off the valve cover before attempting to remove the cylinder head. Abnormally high readings on all cylinders indicate heavy carbon accumulations. Do not forget to check if a decompression lever has been left on, if your engine is equipped with one. The decompression lever would be at the end of the valve cover on a Universal diesel. It is more common on older diesels, while my 1998 Westerbeke 42B Four doesn’t have one.
SHOULD A BOAT OWNER DO A COMPRESSION TEST FIRST?

Not necessarily. My mechanic “Diesel Don Schuler” started with adjusting the valves. I think he started with this because valve clearances that are out of timing adjustment could let unburned diesel past the valve seats and show up as white smoke coming out of the exhaust. Valve adjustment is often overlooked and not frequently done, according to Don. It is understandable of the valve adjustment on a 25 year old engine like mine could have been out of adjustment. But it did not look difficult to adjust the valves, and it looks like there are clear directions in my Westerbeke manual. All it takes is a short screwdriver (short because engine compartments are tight), an open-end wrench and a feeler gauge. It is good practice to replace the valve cover gasket after removing it, so one should have a replacement gasket on hand when adjusting the valves. Many boat owners will have the right screwdriver, wrench, and feeler gauge in their tool kit already, but not everyone has a compression test kit.
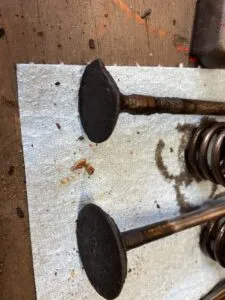
However, adjusting the valves did not solve my white smoke issue. Don also replaced all the fuel injectors as an overdue maintenance issue, since fouled injectors could have also caused white smoke. That did not solve the issue either. We ended up replacing all of the valves and valve guides, head gasket, exhaust manifold gasket, and air inlet manifold gasket, not just the broken exhaust valve on the #4 cylinder. After fixing the engine, including re-adjusting the new valves, I note that my Westerbeke now purrs like a BMW.
CONCLUSION
In my case, the compression test was crucial in diagnosing the root cause of my engine problems. My engine had low power and was belching white smoke. Removing the valve cover and adjusting all the valves did not resolve the matter. The compression test found zero pressure in one cylinder and normal pressure in the others. This led us to believe that the problem was the head gasket or one of the valves, which we confirmed when we removed the cylinder head and found a broken exhaust valve. The white smoke was unburned diesel escaping through the exhaust. If the problem lay elsewhere, such as stuck piston rings or worn cylinders, the remedy would have required removing the entire engine from the boat to access the underside of the engine. That would have been much more expensive, and much more disruptive to our lives as live-aboard cruisers.
What is the impact on the pistons/rings if you only replace the valves on an older engine? How do you know that you did not also have a piston/ring issue?
The process outlined in this article is incrementally stepped so the least expensive and quickest solutions are first tried. This is the standard way of approaching the white smoke problem.
First, the injectors were replaced and compression test is done to see if the problem is fixed.
Next the head is removed and the valves and head gasket are replaced to see if the problem is fixed.
Last, the engine is removed for a complete rebuild.
Each step can cost ten times the previous one so completing each step, then testing before advancing to the next is the most prudent way to proceed.