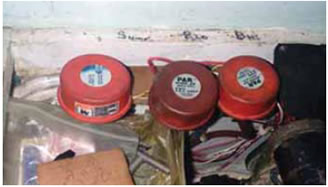
Photo courtesy of Ben Stavis
In your continuing review of bilge pumps and automatic switches, you may want to include a somewhat atypical approach that has worked very nicely on my 1964 Rhodes Reliant. It is based on the simple premise that any electrical components (pumps, wires, connectors) in the bilge are at risk of corrosion and galvanic action. Bilge electrical components can be unreliable and may cause serious damage. He[nce, there should be no electrical components below the floorboards. Here’s how I did it.
The electric bilge pump is an old PAR-Jabso diaphragm pump—the large, old type, with a belt, large notched pulley, and 1-inch hose ports. I am sure other types of diaphragm pumps will work too. Diaphragm pumps are self-priming when they are above the water, and they are not damaged if run dry. On my boat, the pump is located under a quarter-berth where it is about 5 feet above the bottom of the bilge and easily serviceable. It was fairly easy to arrange plumbing for a pipe to the bottom of the bilge and another hose to a discharge through-hull fitting aft, below the transom.
As for the automatic switch, I use a Jabsco “air pressure” switch, which is located high and dry near the pump. It has a quarter-inch-diameter tube going down to the bottom of the bilge. When bilge water comes up, air pressure in the tube rises and pushes on a diaphragm in the switch. When the diaphragm goes up enough, a micro-electrical switch closes and turns on the bilge pump. When the bilge water level goes down, the air pressure in the tube goes down, the switch’s diaphragm goes down, the switch opens, and the pump stops.
The basic principles are simple, but, as they say, the devil is in the details. Here are the details that make this system work very reliably, year after year:
1. The air pressure switch is sold with a small plastic air chamber to be mounted at the bilge bottom. A flimsy plastic tube connects this air chamber to the diaphragm switch. When bilge water with any oil, grease, etc. rises, the bilge goo quickly clogs the small hole at the top of the plastic chamber, blocking the air passageway and rendering the “sensor” inoperative. I replaced the original parts with a long PVC pipe (1 inch or more in diameter), that starts near the bottom of the bilge and terminates a few inches below the floorboard. (See “Bilge Binge,” PS, January 2006 for the last switch test.)
At the top of the PVC pipe, I have a variety of plumbing and hose fittings, so that the top of the large pipe can be connected to a small, quarter-inch tube that goes to the switch itself. With a large-diameter pipe and the small orifice 4 feet above the bilge water, there is no clogging with bilge goo.
2. I replaced the flimsy plastic tube with proper quarter-inch hydraulic hose that is strong and can be connected to reliable, air-tight fittings.
3. It is essential that the hose always goes straight up, and that it has no bends or low spots that might accumulate water and block the air pressure.
4. I used high-quality brass hydraulic fittings to connect the quarter-inch hose to the pipe. This makes it easy to separate parts for access or service and reconnect them in an airtight way.
5. The micro-switch in the diaphragm switch has low-amperage capacity. It may have limited life if it is used to turn on a pump’s fairly powerful electric motor. Thus I use the micro-switch to activate the field of a small relay. The relay (auto style from Radio Shack) is rated at 25 amps, so it has no problems handling 10-amp loads. By using this small relay, the switches for this system have been reliable for many years. (Both Jabsco, www.ittflowcontrol.com, and Groco, www.groco.net, websites say their current switches can handle over 10 amps, so maybe using a relay isn’t necessary.)
6. A diaphragm pump can become inoperative if small bits become jammed in a valve, preventing it from closing properly. Thus a strainer is needed in the pump inlet line to catch any debris. I use the Forespar Marelon engine (www.forespar.com) intake strainer. It has been very reliable in this application.
7. Another potential problem with the pump is that the valve flaps can warp and fail to seal. I used to have to buy new valves annually for my bilge pump. My new solution is that during fall winterizing, I disassemble the bilge pump (four bolts, five minutes) and remove the valves so that they cannot be affected by anti-freeze or the weight of standing water. The result: No more valve problems.
8. I installed a small electrical counter that displays the number of times the bilge pump has turned on since it was last reset. This way I have a very simple, accurate knowledge of how much water is entering the boat. I find this extremely useful.
Ben Stavis
Astarte, 1964 Rhodes Reliant
Northern Chesapeake Bay