About a decade ago, like many sailors, we began replacing wire and low-stretch double braid ropes with super strong single-braid ropes. These ropes were made with a high molecular weight polyethylene fiber (HMWPE) commonly known as Dyneema. Amsteel SK75, a popular Dyneema single-braid, was used in our lifelines, shrouds, halyards—even in our sheets (for racing) and our ground tackle (for kedges). Dyneema soft shackles replaced our clunky metal ones.
One lingering concern we had as we made this switch was the fiber’s durability in actual use. The makers of the various ropes made with Dyneema claim their coated HMWPE fibers are resistant to chafe and UV, even outlasting stainless steel in many applications. However, most of their tests do not accurately replicate real world use on a boat. After 15 years of using HWMPE single-braid rope on our own test boats, we’re noticing that the material is more vulnerable than the manufacturer’s published data suggests.
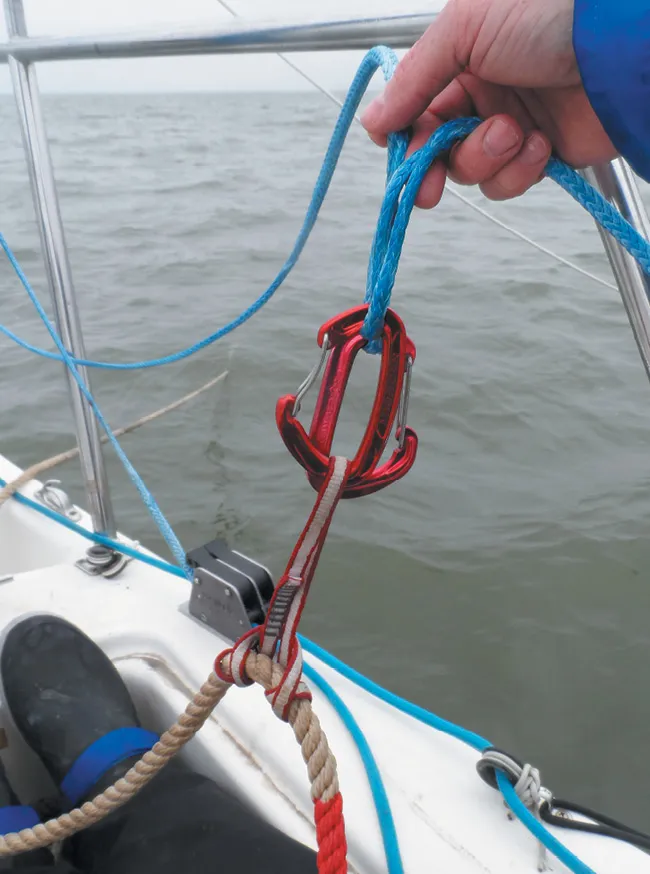
Our focus in this article is Dyneema single-braid ropes, such as Amsteel SK75 and SK78, although many of our findings will also apply to higher-strength grades. Double-braid ropes are a different animal. In a double-braid rope, the Dyneema core is protected by a cover that is more resistant to chafe and UV exposure. It’s important to remember that the cover of a Dyneema core rope doesn’t add much to the rope’s overall strength, since the core carries most of the load. Polyester covers are also prone to stripping right off the Dyneema core when a highly loaded rope is secured in a single-cam rope clutch.
UV DAMAGE
The Dutch manufacturer DSM (Dyneema is now owned by Ohio-based Avient) claimed that UV would reduce the strength by about 40 percent in four or five years, but then the rate of loss would slow and level out. But the tests were run in the Netherlands on a rack, using 8-millimeter (5/16-inch) rope. The annual UV irradiance in the Netherlands is 2.5 times less than Chesapeake Bay, home of our test boat, and most lines on our boat are smaller than 8 mm—so DSM’s data isn’t a good guide for us. In terms of UV exposure, ten years on a rack in the Netherlands would be equal to about 4 years for our test boat near Annapolis, MD, and just 2–3 years in Miami, Florida.
Rope on a test rack does not experience load cycling—repetitive cycles of tension and release that can accelerate the wear of UV-weakened fibers as they rub across each other. So, in the real world, UV damage does not level off as it does in rack testing. And any chafe points that exists in real world use will also continue to weaken a rope.

Fatigue stress caused by repetitive loads can also weaken Dyneema. But if the rope is properly sized, the effects are minimal. Colligo, a California-based company that specializes in HMWPE rigging, uses samples from rigging that has been in the field to evaluate lifespan and durability. Based on these findings, the company believes that if Dyneema standing rigging is correctly sized to minimize creep (elongation over time), it will be thick enough to resist UV and chafe (in running rigging applications, for instance) for about 10 years.
A key takeaway from the Colligo studies is that we should not choose a Dyneema rope that will match or slightly exceed the breaking strength of new wire. We should choose a larger diameter rope that is much stronger than the original it replaces, so that after 10 years of UV exposure it will have the same strength as wire that has been in service for the same period. How and in what environment you will use the rope will affect your decision.
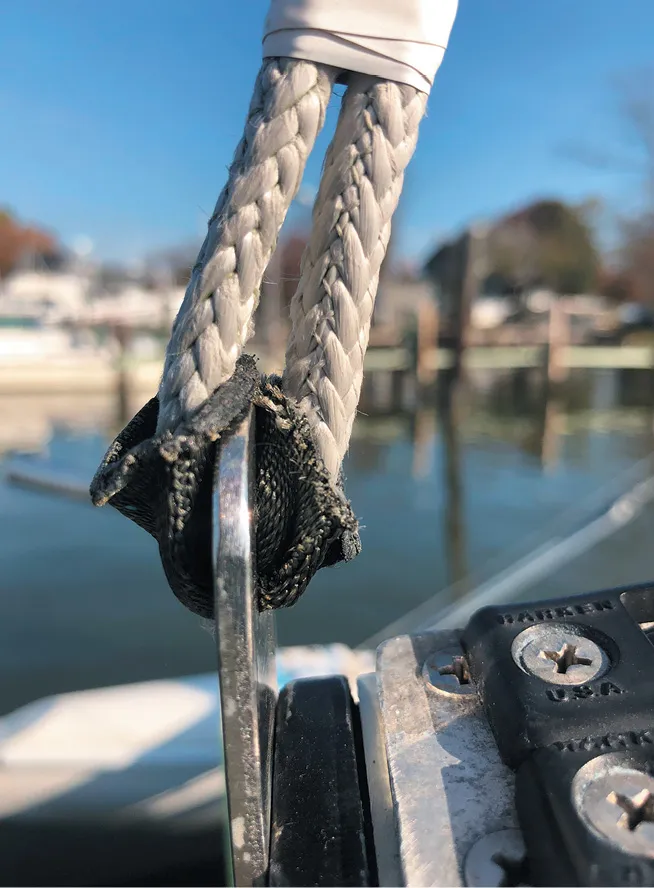
But even the Colligo’s reports don’t fully account for load-cycling. Properly tensioned standing rigging does not go through on-off load cycles, which causes rubbing between strands and accelerates wear. Often, a line in our running rigging will repeatedly go from full load to slack, and this may result in internal chafe that causes much faster degradation. Add UV to the mix, and we would expect working rigging made of Dyneema to wear much more rapidly than a shroud in Colligo’s testing.
Based on our research, UV exposure is one of the chief factors to consider when selecting a Dyneema replacement for wire. Unlike some synthetic fibers, it is not as susceptible to age and fatigue. In other words, a Dyneema rope that has been under strenuous dynamic loads, but not subjected to chafe or sunlight, might have more remaining life than we think. We recently inspected Dyneema that had not been exposed to UV but had experienced a series of high loads both on our boat (as an outhaul) and in our test rig, where it had been repeatedly loaded 20–30 percent of its breaking strength.
Upon inspection, the rope showed fuzzing where it rubbed against rough metal, and some flattening where it passed over a sheeve, but the fibers in these areas were otherwise intact. The long segments of rope that ran free of any contact looked almost new, even though it had been in service for more than a decade.
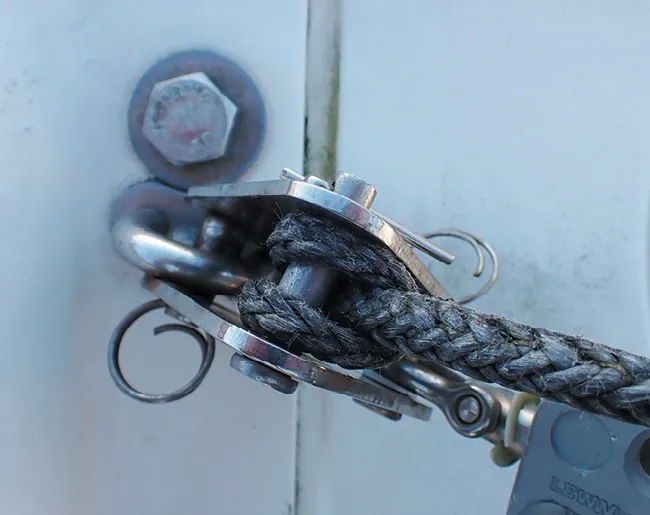
Bottom line: UV exposure is one of the chief enemies of Dyneema despite what the makers claim. Plan on replacing any Dyneema that is exposed to UV at regular 5- to 10-year intervals depending on the amount of exposure—and regardless of whether it has been subjected to Dynamic loads.
HIDDEN TOLL OF LOW STRETCH
In the wake of several reported Dyneema topping-lift failures we decided to do a little digging. After all, Dyneema single braid seems perfect for keeping the boom aloft when the sail is struck. It’s light, has low windage, is economical, and is easy to splice. Yet even when a Dyneema topping lift has a rated strength far greater than the steel or polyester line it replaces, it can fail in just three years. Meanwhile, steel or polyester topping lifts can last 15 years or more.
UV damage is a chief enemy. The topping lifts we inspected appeared chafed, but this fuzz was actually caused by UV rays, which gradually penetrated the outer layers. The other contributing cause of failure is the lack of stretch. None of the boats with Dyneema topping-lift failures had taken other measures to stabilize the boom—using boom gallows or adding another line to prevent the boom from swaying (see “a Sure Way to Secure the Boom,” see PS December 2018).

When they switched from polyester to a Dyneema topping lift and snugged the sheet down, the boom stopped swaying, so they (incorrectly) believed they had solved a problem. In fact, every time the boat rolls, the boom’s inertia puts an extreme amount of tension on the topping lift. These on-off load cycles can be repeated hundreds, if not thousands of times a day.
Because the topping lift has no stretch, the load transmitted directly to the fibers is much higher. In several instances of broken Dyneema topping lifts, the owners reported that their wire topping lift had broken previously. They switched to Dyneema but did not address the original problem—an over-tensioned topping lift that left no room for energy-absorbing stretch.
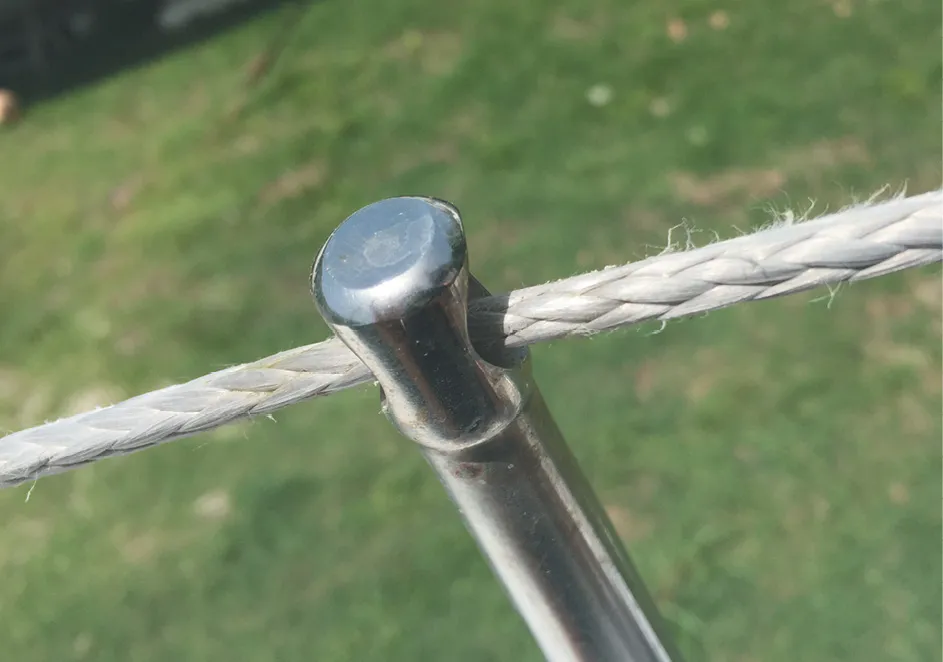
Bottom line: Dyneema looks like rope, but the lack of stretch and impact absorption can create enormous forces in unexpected places.
CHAFE
Practical Sailor chafe testing, confirmed by others, revealed that in relation to the reduction in cross-sectional diameter caused by chafe, Dyneema loses a larger percentage of its total strength than do ropes made with other fibers. In other words, a ¼-inch cut in a ½ -inch Dyneema rope will reduce the rope’s strength by a far greater percentage of its total strength than would the same cut in a nylon or polyester rope of the same diameter. When a polyester or nylon line is chafed locally, there is enough inter-fiber friction to grab the loose tails of broken strands and enough elasticity to absorb any additional load on the fully intact strands, especially those adjacent to the break.
If there is another chafe point nearby (even inches away), it doesn’t matter if the same strands are being chafed in both points. Because of the intra-fiber friction, the additional load on the strands adjacent to the break is shared with all the remaining fibers. And since it is in the grip of the adjacent fibers, even the broken segment can still absorb some of the load.
Dyneema is so slippery that when a few strands chafe through, the adjacent strands don’t have enough friction grip of the tails of the broken strands, so that the broken strands are nearly useless. Also, this slipperiness means that the intact strands directly adjacent to the break cannot fully share the load with the other intact strands in the weave. In addition, Dyneema has almost no stretch, so the strands directly adjacent to the break lack the elasticity they need to absorb the increased load. This leads to a cascade of failures: the fibers nearest to the break fail, and those next to the secondary break fail, and so forth.
In a single-braid rope made with grippy and more elastic fibers like nylon or polyester, a 20 percent loss in cross-section due to chafe results in a 20 percent loss in strength. In the same rope made with Dyneema, a 20 percent loss in rope cross-section results in a 35–40 percent loss in strength. This is also true of wire rope. When you see one broken strand of a steel cable, you know the entire cable is severely compromised and must be replaced without delay.
We saw a clear example of this when we compared a Dyneema lifeline to stainless-steel lifeline. If there was a tight radius turn in the lifeline, the steel would fatigue and fail before Dyneema. But if there was a burr on a stanchion, the Dyneema wore through and failed in short order. Sailors considering a switch to Dyneema lifelines need to know that wire lifelines will create burrs in stanchion eyes that will need to be polished smooth before installing Dyneema. A chafe protection sleeve where the Dyneema passes through a stanchion eye is also recommended. Most Dyneema lifeline failures can be linked to chafe at a stanchion eye (see “Dyneema Abrasion Test,” PS November 2018).
Bottom line: Chafe is a dangerous enemy of Dyneema. When making a switch, eliminate chafe points and add chafe protection where needed. You can mitigate the risk of chafe somewhat by sizing your rope to the same diameter or greater of the line or wire you are replacing.
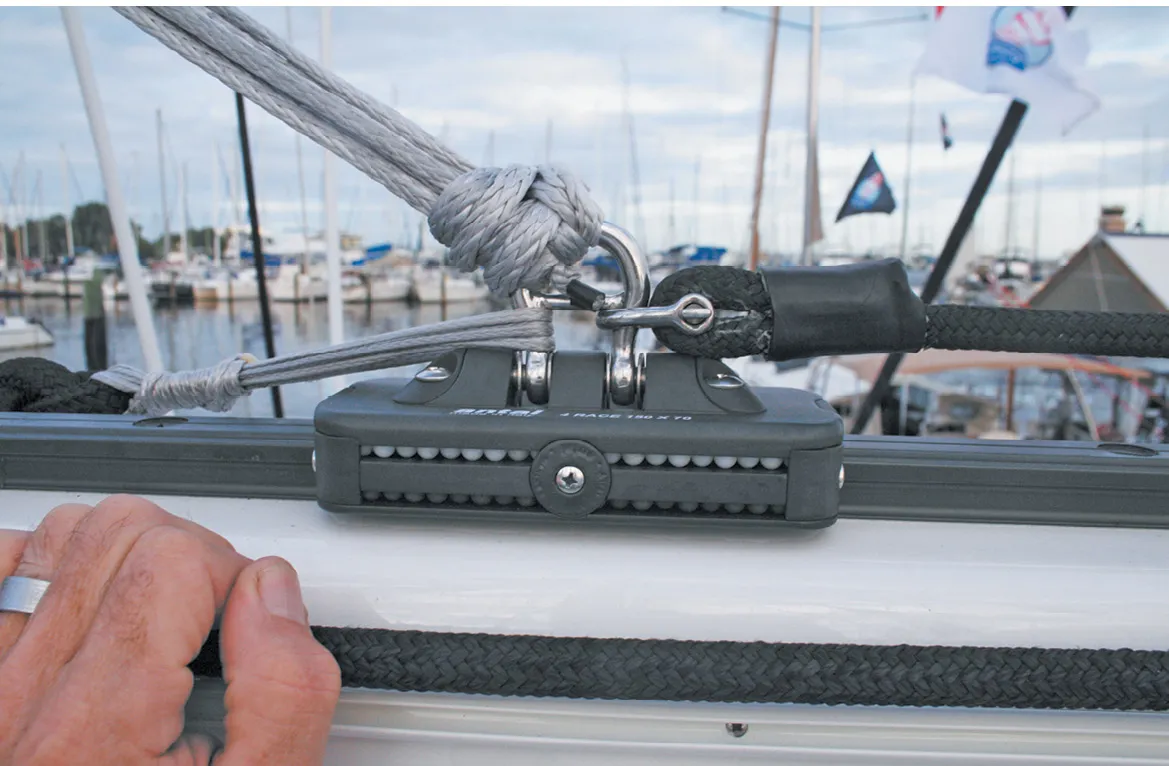
CONCLUSION
Having spent several years evaluating Dyneema products in the sailing market, we think it’s time for a frank assessment of its shortcomings. Its strength is legendary. And the variety of uses for it on a sailboat is impressive. But we also need to bust some myths regarding its durability over the long haul.
Yes, the UV resistance of Dyneema is far better than nylon, but it is not any better than polyester lines of the same strength.
The same goes for chafe. Dyneema is more resistant to chafe than nylon single braid. However, Dyneema single braid is less chafe resistant than a polyester double braid rope with the same strength. Dyneema single braid is good at resisting chafe when the movement is end-to-end rather than side to side. It’s a great choice for multipart cascade tackles using low friction rings in vangs, bobstays, and outhauls where there is very little chafe. When the abrasion is across the strands (side to side), however, polyester double braid outlasts Dyneema single braid.
In general, Dyneema shines as premium double braid product. To offset its vulnerability to UV and chafe, the diameter of the Dyneema double braid should be nearly the same as the polyester rope it is replacing, which means it will cost 3–4 times more. If you decide to switch to a much smaller diameter single-braid Dyneema rope with the same breaking strength as the rope it is replacing, know that the Dyneema rope will be much more susceptible to chafe and UV damage.
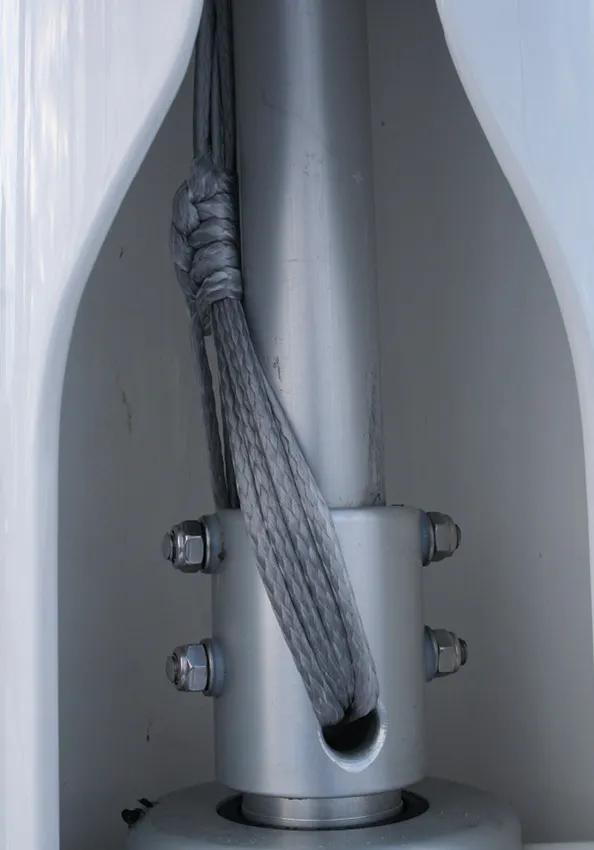
Dyneema has some great attributes: incredible resistance to fatigue, great strength-to-weight ratio, great strength-to-price ratio. We’re fans. But we need to balance these advantages against its weaknesses, especially the fact that it can fail suddenly with very few, if any warning signs. We must also recognize that single braid construction has limitations compared to more expensive double braid.
We accept some fading, and chafe in polyester or nylon ropes before we need to replace them. After 10 years, we know that polyester and nylon have lost most of their strength. With stainless rigging, one broken wire or the smallest bit of corrosion condemns a wire. Wire that has been subjected to 10 years of heavy use in a tough environment (offshore racing, for example) is probably due for replacement, but under milder conditions (freshwater summer daysails for example), it can last twice as long.
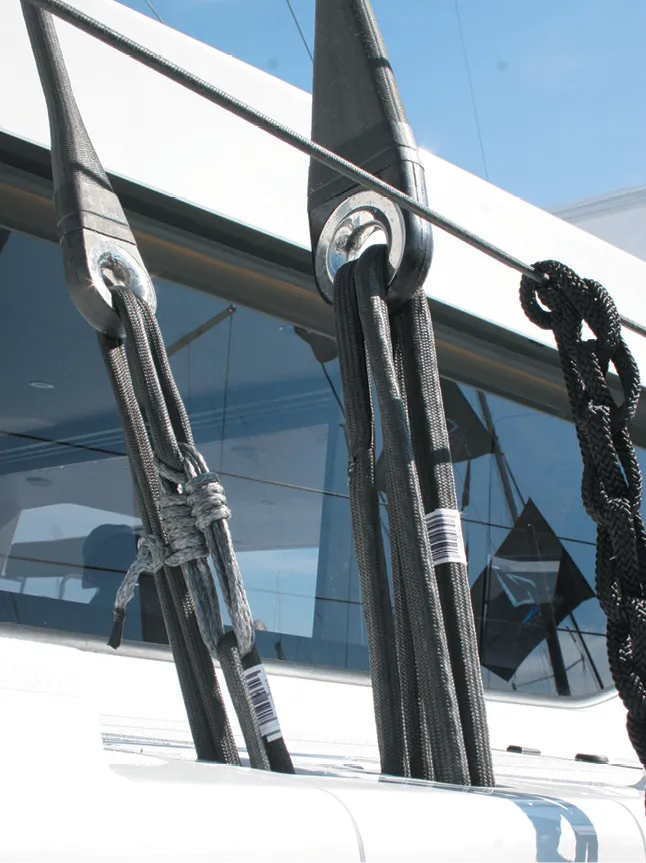
Dyneema requires a different approach to thinking about longevity. Susceptibility to UV and chafe requires careful monitoring and more frequent inspection. And because the effects of UV damage combined with chafe are not so apparent, you should plan on replacing essential standing rigging and lifelines every 10-15 years. Don’t let the laboratory tests or “real world” tests in milder environments or in less demanding applications fool you—every miracle material has its limits.
High-molecular weight polyethylene fiber ropes have revolutionized sailing. Bit by bit, the metal on our boats is going away and being replaced by fiber components that a competent do-it-yourselfer can custom fabricate to suit their specific needs. During the past several years, Practical Sailor has explored many of the potential uses for Dyneema—from lifelines to clew shackles. If you have a specific project in mind you can use the search bar on the website to access our full coverage. Here are some of the highlights of our past projects: