Would you trust a pencil-thin, anchor chain that touts greater strength than the locker-full of high-quality, 3/8-inch, galvanized short-link chain that youve counted on for years? Would you even want a lighter chain? After all, the chains heft creates catenary, that all-essential dip in the anchor rode that improves your anchors holding ability.
A skinny chain might not be your style, but a growing number of performance-oriented sailors are curious about ways to achieve a lighter all-chain rode. For the sake of these sailors and those with modern, lightly built boats, one PS tester is doing a long-term test of high-tensile chain that challenges conventional notions of an all-chain rode.
The staple anchor chain at most marine chandleries is galvanized, BBB G30 and G43 (high test). These are bulky, heavy chains that aid in the anchors holding by putting a reassuring sag in the rode to absorb snatch loads and reduce the angle of pull on the anchor. Short-link anchor chain (BBB), because it is heavier per foot, is preferred and is ideal, if not essential, for older-style anchors such as the CQR.
A small contingent of boaters, however, are jealously eyeing stronger, lighter (and sometimes, more expensive) chains that have been used in other industries for many years. These include G70, G80, G100, and G120 (the higher numbers correspond with higher tensile strength). Until recently, PS didnt test these chains, because costs increase with tensile strength and because their strength was significantly compromised when they were hot-dip galvanized to prevent corrosion. Now that is changing-at least with regards to G70 and G80.

Photos by Jonathan Neeves
Three articles in our online archives offer important background on this topic: Looking into the High Test Myth (PS, June 2014); Galvanized Coatings Test (PS, January 2015); and Armorgalv vs. Hot-dipped (PS, March 2015). These articles discuss our first foray into super-high-tensile chains, specifically G70 chain. A fourth article, PS Asks Who Would Even Consider G70 Chain (PS, June 2014), addresses a chief problem with stronger, lighter chain-less catenary-as well as other drawbacks that weve discovered.
What launched this series of investigations was a quest for an all-chain-rode system that was lighterweight but just as strong as the 8-millimeter (5/16-inch) chain we had on one testers boat, a Lightwave 38 catamaran based in Sydney, Australia. The chain had to meet certain criteria: It had to be easily available; it had to fit an existing or commercially available windlass gypsy (also known as a wildcat); the coating process (galvanizing, etc.) had to be commercially viable; and connectors, shackles especially, had to fit the chain without reducing the overall strength.
While G70 chain fell short of these expectations, there are some available sources of galvanized G70 chain. In the U.S., both Campbell and Peerless (available through West Marine) offer galvanized G70 in standard measurements. In metric sizes, the Italian company Maggi and Peerless offer galvanized, but the smallest is 8 millimeter (5/16 inch). Besides the difficulty of sourcing the smaller-diameter G70 chain that we sought, the amount of weight saved by switching to G70 was not as convincing in the smaller link sizes.
For example, you save less than a half-pound per foot by switching from 3/8-inch to 5/16-inch. However, when you downsize from half-inch to 3/8-inch, you save almost a pound per foot. So, if youve got 250 feet of chain in the bow, switching from half-inch G30 to 3/8-inch G70 is the equivalent of leaving Orson Welles at the dock instead of letting him tag along as bow candy, but if youre swapping from 3/8-inch to 5/16-inch chain, youre ditching Rita Hayworth.
Downsizing chain has other advantages besides saving weight. Smaller chain means more space in the anchor locker, allowing for a longer rode, or easier self-stowing (too much chain in a tiny locker creates a pile that interferes with self-stowing). Although high-tensile chains are more expensive than their conventional counterparts, the price difference may be small enough to justify all these advantages combined. For example, 5/16-inch G70 costs $6.41 per foot while 3/8-inch G30 costs $5.29 per foot. Of course, there is also the initial investment in a new gypsy ($100 to $300-plus), depending on size and brand.
Evaluating G80
Based on our initial investigation into chain, we realized that although G80 is more expensive per foot, it might be more sensible than G70. G80 chain has been available for more than four decades and is manufactured by many reputable chain makers; however, some manufacturers recently have turned their focus instead to G100 and G120. G80 is used around the world in lifting applications and is available in link sizes compatible with a windlass gypsy. Compatible connectors and attachments can be coated and still meet the minimum strength for our usage.
The anchors are another important aspect of this investigation, since the intent was to match relatively modestly sized anchors with a lightweight chain. Bear in mind that this approach runs contrary to the time-tested approach of heavy chain and a heavy traditional anchor (CQR, claw, Bruce, etc.), and not one we would encourage for a traditionalist with a heavy-displacement cruiser-a la Bob Perry, William Garden, etc. But part of the PS mission is to test new ideas, and this approach will appeal to certain sailors, especially multihull sailors. One factor that persuaded us to test this approach was the compelling holding power of some of the relatively new diving anchor designs (see PS, April 2015 online).
The owner of the PS test catamaran, which has the windage of a 45-foot monohull, has an unabashedly minimalist attitude when it comes to anchor selection. He uses a 33-pound, steel Anchor Right Excel for his primary anchor. This is supplemented by a 17.5-pound, aluminum-alloy Fortress FX 23 (assembled with the flukes set at 32 degrees), a 17.5-pound, alloy Excel anchor, and a 17.5-pound, alloy Spade A80 anchor. Each of these anchors can be used as a primary as the conditions dictate. In general, our tester likes to anchor with just one anchor, but often sets a second anchor at a 45-degree angle off the bow for extra measure. He likes alloy anchors because they are convenient to set from a dinghy.
Although this lightweight approach to ground tackle is contrary to textbook advice, it has served our tester well and is used by a number of converts. The test boat sails some 2,000 nautical miles each year, and this anchor combination has proven very reliable-with the exception of areas with heavy weed bottoms. Until recently, the tester has paired his primary anchor with heavy G30, 8-millimeter (5/16-inch) chain. His switch to lighter, 6-millimeter (quarter-inch) G80 chain reduced catenary, but because the catamaran often anchors in such shallow water, the benefit of catenary is not so great. And based on our own experience, effective catenary diminishes (or even disappears) in 30 knots of wind anyway, requiring effective snubbers (see PS, March 2016 online). Moreover, additional weight has such negative impact on catamaran behavior, the less-is-more approach made sense for our tester.
Elongation
One concern regarding the switch to G80 was whether it would be so brittle that it would not elongate enough before breaking. Materials that elongate offer a measure of safety where shock loads are anticipated-this is why nylon is preferred for snubbers, dock-lines, and anchor rodes. Elongation also warns of impending failure.
The North American Chain Manufacturers (NACM) has agreed that G30, G43, and G70 should elongate at least 15 percent before breaking, but galvanized chain is not included in this standard. However, NACM also specifies that G80, G100, and G120 chains have a minimum elongation of 20 percent, meaning the higher-tensile chains are actually less brittle. Unfortunately, these guidelines apply only to U.S.-manufactured chains. A large percentage of high-tensile chain is made in places where these standards don’t apply.
Pricing varies widely. Grade G80 chain from China is about half the price of chain sourced from America and Europe, but determining which foundry in China that it came from is nearly impossible. Chinese G80 is sometimes unmarked, or mysteriously marked, and test certificates are not always reliable. We have no doubt that some excellent chains are being made in China, but tracing the foundry and doing a comprehensive test of these chains is cost prohibitive.
This severely hampered our search for a reliable, cost-effective chain. In the end, we included 45 feet of 6-millimeter (quarter-inch) G80 from China in our test. The chain had a manufacturers mark (R8), a batch number, and a brand embossed into some of the links. Some investigative work suggested it might have been sourced from the Rudong Chain Factory in Ningbo, China. We were also provided with a batch certificate of conformity, which any responsible chain supplier should offer for longer lengths.
Hydrogen Embrittlement
The need to galvanize our test chain raised concerns about another type of brittleness: hydrogen embrittlement. In typical galvanizing, the chain is acid-washed first, and this can result in the hydrogen ions concentrating to make the metal more brittle; this is known as hydrogen embrittlement. There are horror stories, of bolts and other components used in high-profile bridge projects falling victim to hydrogen embrittlement, but our research found that hydrogen embrittlement is not a major concern in the marine industry-at least when purchasing products from a reputable source.
To further alleviate our fears, the Armorgalv process we decided to use for this test eschews acid-washing, so that even the higher-tensile metals (G70 and higher) that are presumably more prone to hydrogen embrittlement can still be coated.

Fitting the Chain
For this test, the first task was to find a high-tensile chain that would fit any windlass (imperial or metric). According to specifications from several major windlass makers, chain sized to the European standard EN 818-2 would fit a decent cross-section of windlasses that are available worldwide, including Muir, Maxwell, and Lofrans brands. We acquired a 6-foot length of 6-millimeter (quarter-inch) EN 818-2 G80 chain from Gunnebo and checked it for fit. (Note: Anyone who is considering buying new chain should always check for fit. Ideally, the sample length should be long enough that you can check that it does not slip or jump under the windlass rated load. Good chain distributors will be able to mount your gypsy and run through the complete length of chain you want to buy.)
The next step was coating the non-galvanized G80 lifting chain using the Armorgalv process. Coating chain requires heating it, and heating can reduce the strength of any metal that is forged using a quench-and-tempered process. In chains, that means any chain rated G70 and higher.
To find the optimum coating temperature, we experimented with several sample lengths of Gunnebo G80 chain. Each was Armorgalv coated at varying heating and cooling schedules. Eventually, testers found 698 degrees to be the optimum coating temperature. This temperature is commonly used for other alloys in marine manufacturing, so this was relatively affordable. (Coating temperatures might be different for chain from other manufacturers.)
We found the strength loss of the 6-millimeter G80, when testing short sample lengths, was less than 1 percent, giving it an ultimate tensile strength of 10,010 pounds. Strength losses of high-tensile chain coated with Armorgalv at higher temperatures (around 752 degrees) can be 20 percent. Fortuitously, we found that the temperature schedule at which we worked improved the chains elongation characteristics. The simple explanation for this is that the Armorgalv process advantageously re-tempers the steel, making the 6-millimeter Gunnebo Armorgalv-coated G80 less brittle than other chains we have tested. For example, check out the results of our elongation test of various chains (percentages indicate elongation upon reaching the rated ultimate tensile strength): Peerless G43, 14 percent; Peerless G30, 13 percent; Peerless G43, 14 percent; Peerless G70, 10 percent; and untreated Gunnebo G80, 7 percent. The deformation of the Gunnebo 6-millimeter (quarter-inch) Armorgalv-treated G80 (21 percent) was very close to the deformation of the Peerless/Spencer Armorgalv-coated 8-millimeter (5/16-inch) G80 that we had tested previously.
Shackles and Links
As if finding the right chain and having it coated wasnt challenging enough, it became apparent that the shackle would be our weak link. We knew we would require at least one extra shackle at the anchor since none existed that would fit both the anchor and our new, smaller chain. Although this is not a perfect solution, it is not uncommon in anchor rodes.
At the anchor, our tester used a Grade B 3/8-inch shackle with an ultimate tensile strength of 12 tons, 6 tons when side-loaded at 90 degrees. (Although a 90-degree side-load is unlikely, it is something to consider when sizing anchor shackles.) The bigger problem was that we could not find a connector that would match the strength of the new 6-millimeter (quarter-inch) Gunnebo G80 and still fit the chain links. Our tester did, however, find a connector that would at least match the breaking strength of the anchor shackle.
The missing link-so to speak-was a 6-millimeter (quarter-inch) G80 Omega link from Van Beests Excel range that had been Armorgalv coated. The resulting link was 7-percent weaker than the G80 chain in our test, 5-percent stronger than the testers previous 8-millimeter chain, and the same strength as the conventional, high-test G40 chain used for anchoring and mooring. If we were to use this combination-6-millimeter Armorgalv-coated Gunnebo G80 chain matched with the 6-millimeter G80 Armorgalv-coated, Van Beest Omega link-the rode system would have a minimum tensile strength of 9,245 pounds. This is still well above the minimum tensile strength of metric 8-millimeter (5/16-inch) G30 that our tester had been using for 15 years.
Not satisfied with having a shackle that is weaker than the chain, we wondered whether we could claw back that 7 percent loss of strength? Heres where the whole endeavor became nearly too complicated. Using a bigger Omega link was impossible as the clevis pin for the next size up would not fit the link. Upgrading to a G100 Omega link was possible, but it opened a whole new can of worms since Armorgalv-coating G100 is unproven.
The complications were at the Omega link, which acts simply as an enlarged end-link for attaching shackles and other hardware. Since the smaller clevis pin is theoretically the weak point in an Omega link, we decided to use the clevis pin for a G100 Omega link. This, too, was Armorgalv coated. It is a big risk that wed not recommend for anyone-except perhaps a PS tester willing to put his faith in preliminary lab testing. Not even Van Beest, the maker of the link and the clevis pin, would endorse this approach. [Editors note: Since this article was written, weve begun testing an Armorgalv-treated G100 Omega link; stay tuned.]
One problem that we could not overcome was that most chain and connectors are painted or powder coated. To Armorgalv the small lengths required sand blasting. This is not entirely satisfactory: It introduces an added cost; paint removal is slow and powder-coating removal even slower; and any residual paint may affect Armorgalv adhesion. We could have used unpainted or raw chain, but we would have had to buy at least 600 feet as a special order from Sweden. Van Beest rejected outright the idea of supplying uncoated connectors. In the lifting industry, upon which we were leaning heavily, coloris part of brand recognition and is also used to indicate, at a glance, that a lifting assembly, say chain, hook, swivel, and tape, is made with components of the same caliber (or rating).
The Armorgalv process depends on sand blasting to clean any object to be processed. It was critical to our test that the local Armorgalv operator was very willing to work with our tester in Australia. In the U.S., the Armorgalv licensee, Spencer Industries, has shown an interest in offering a similar service, and there are at least three other Armorgalv convertors in the U.S.

Galvanizing
In our 2015 investigation into Armorgalv (see PS, March 2015 online), testers concluded that Armorgalv coating thicknesses needed to be at least 100 microns (or more) for its abrasion resistance to compare with the best hot-dipped galvanized metals (coated at about 150 microns). We have found that the Armorgalv coating is more abrasion resistant than hot-dipped coatings, but this is of no value when the coating is too thin. We have been assured that the Armorgalv coating thickness can be easily tailored since thickness is a function of the zinc added; more zinc equals a thicker coating.
Based on our previous tests, we are confident that an Armorgalv coating of 100 microns or more will have greater longevity than the best commercially available, hot-dipped galvanized coating when applied to a short-link anchor rode. We have not done enough real-world testing to support this conclusion, but since the U.S. Navy and U.S. Army are specifying Armorgalv in thicknesses of 70 to 80 microns, we believe our confidence in a 100-micron coating is not unreasonable.
How could we confirm we were getting a 100-micron coating? The biggest challenge here was quickly quantifying the coating thicknesses of curved surfaces. The tighter curves in our small, 6-millimeter chain demands more measurements. Instead of checking every link, we decided wed focus on the ends. We ground the end-links to make them perfectly flat. Using our own flux density-coating thickness meter, we could check coating thickness of the end links at the coaters facility. The coating thickness of the ground links could then be correlated with the coating thickness of the chain by micrometer and gravimetric measurements later.
Load Testing
If youve made it this far, then youre probably wondering if all this trouble was really worth the effort. In the case of our tester, his goal was to have the same weight of rode (165 pounds), but to increase the length from 160 feet to 240 feet. More importantly, he needed to be assured that this new, pencil-thin, Armorgalv-coated anchor rode with a customized shackle setup was truly capable of matching the loads of his previous arrangement.
All of our load testing was carried out at the Australian-certified testing facility of JL Robertsons in Newcastle, Australia, the same company that carried out load testing for our previous reports on chain and shackle strength. We had a representative on site for every test.
The results of our testing are illustrated in the accompanying table, and while these are indeed encouraging, they don’t reflect some of the more notable findings. First of all, a big problem with our chain-downsizing project was a matter of perception. The links of 6-millimeter (quarter-inch) chain look tiny, more like the chain youd use on a dog leash than something to keep your floating home from being dashed on the rocks in a storm.
After years of using 8-millimeter chain, it can be daunting to accept that the newer, smaller, 6-millimeter rode is stronger. But anyone who has wielded a titanium tennis racket will understand that weight and bulk don’t always equate with strength.
Despite the G80s fragile appearance, we never really doubted its uncoated tensile strength. These chains are widely used in the lifting industry and face close scrutiny. We were more worried about the coating. Could the chain be properly coated in a way that would not compromise strength, and yet provide adequate abrasion resistance? Close measurement of the Armorgalv coating revealed that we could indeed achieve a coating thickness of 100 microns on both the chain and the links.
As it turned out, our 240-foot length did not match the initial results we saw in the strength testing of the shorter samples. The chain failed at loads between 8,400 and 8,800 pounds, a strength loss of 10 to 15 percent compared to uncoated G80 chain. This is still a smaller reduction in strength than occurs when galvanizing high-tensile chain. The fact the initial trials almost retained full strength and that a 100-micron coating is possible were nevertheless encouraging.
The good news was that the test results for the 240 feet of Armorgalv-coated, 6-millimeter chain still matched the strength of the 8-millimeter G30 that our tester had used for 14 years. In addition, elongation prior to breaking was 23 percent-better than most G30, G43, or G70 chains.
As for the shackles: The strength of the Armorgalv-coated, 6-millimeter G80 Van Beest Omega links with the G100 clevis pins was a complete success. The linkage demonstrated an ultimate tensile strength of 12,200 pounds. The Omega links, in combination with the Grade B 10-millimeter (3/8-inch) Peerlift shackles, used to connect to the anchor (whose strength needs degraded by 50 percent to account for the unlikely 90-degree side loading) are still comfortably stronger than the Armorgalv-coated 6-millimeter G80 chain.
Conclusion
Was all this trouble worth it? So far, yes, but time will tell. Our tester now has a much longer anchor rode that occupies less space and does not add any weight. It does not create piles when self-stowing using the windlass. The new, pencil-thin chain has been in use for six months with few surprises.
We re-emphasize that this project is not for the faint-hearted. Until our tester has some more anchorages under the keel-and some major chain manufacturers are willing to endorse this approach-we are reluctant to recommend it.
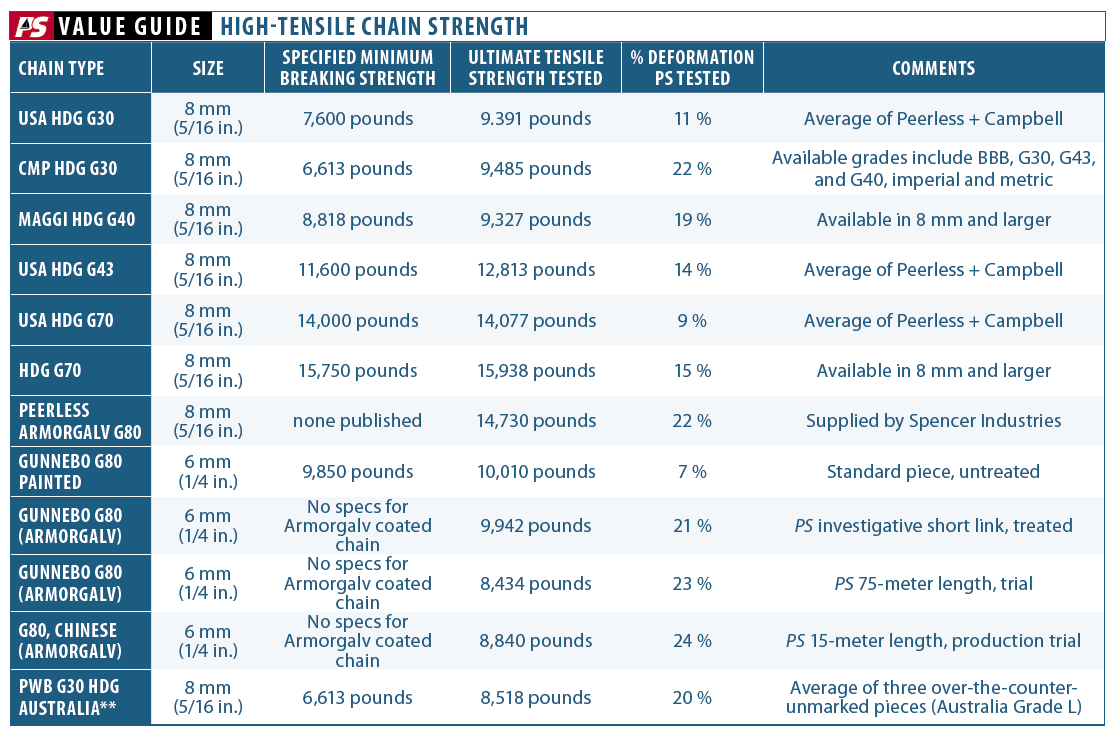
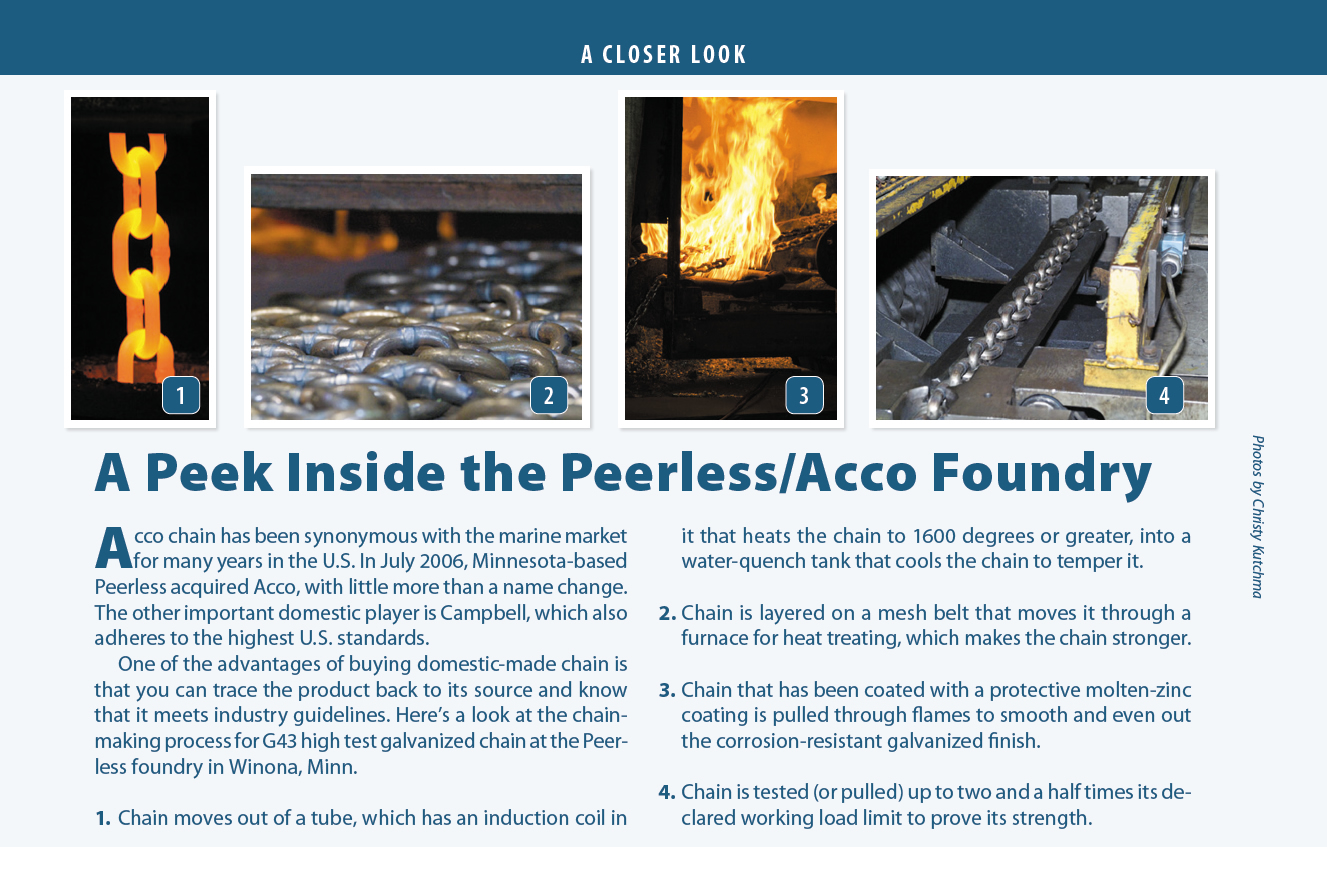
Acco chain has been synonymous with the marine market for many years in the U.S. In July 2006, Minnesota-based Peerless acquired Acco, with little more than a name change. The other important domestic player is Campbell, which also adheres to the highest U.S. standards.
One of the advantages of buying domestic-made chain is that you can trace the product back to its source and know that it meets industry guidelines. Here’s a look at the chain-making process for G43 high test galvanized chain at the Peerless foundry in Winona, Minn.
1. Chain moves out of a tube, which has an induction coil in it that heats the chain to 1600 degrees or greater, into a water-quench tank that cools the chain to temper it.
2. Chain is layered on a mesh belt that moves it through a furnace for heat treating, which makes the chain stronger.
3. Chain that has been coated with a protective molten-zinc coating is pulled through flames to smooth and even out the corrosion-resistant galvanized finish.
4. Chain is tested (or pulled) up to two and a half times its declared working load limit to prove its strength.
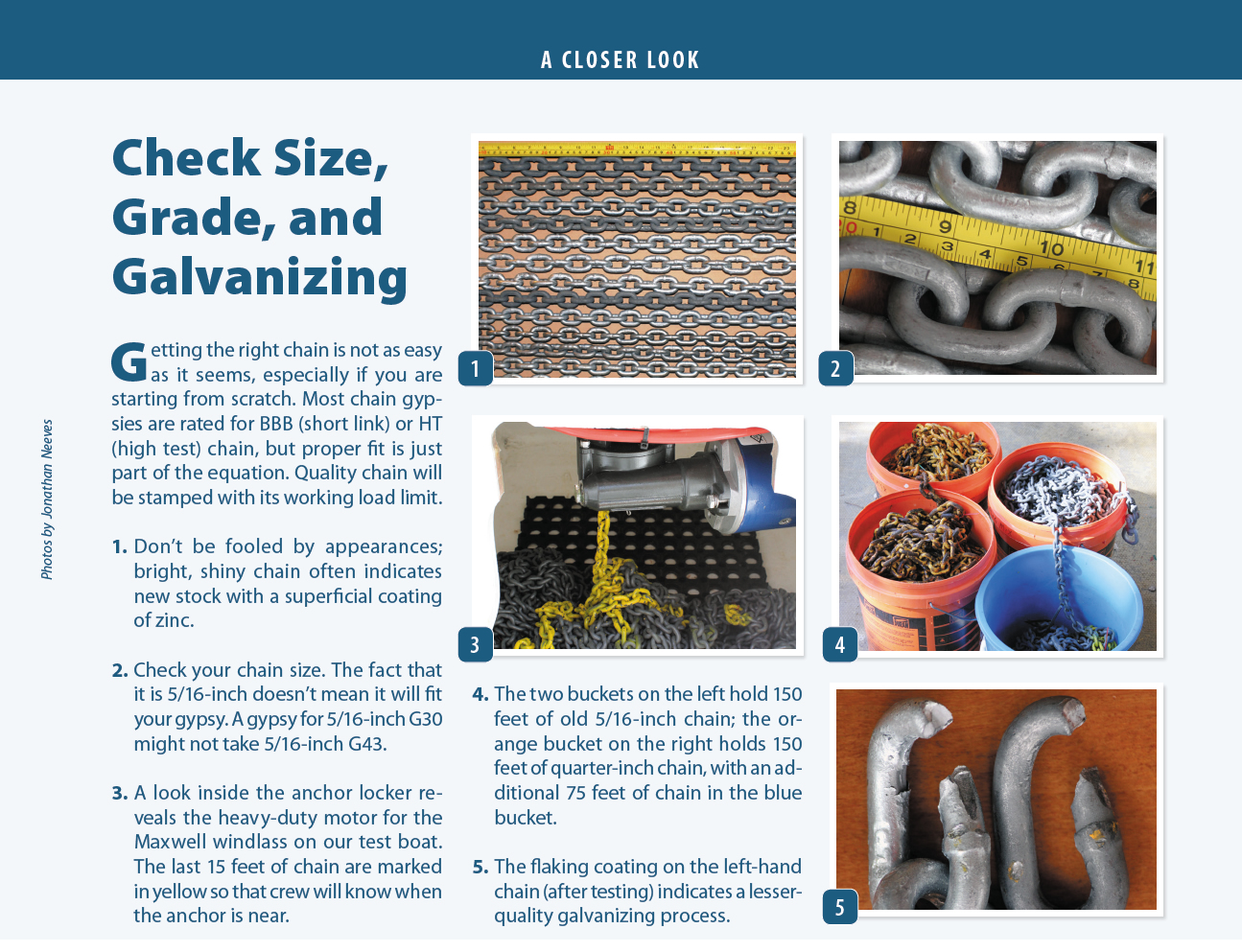
Getting the right chain is not as easy as it seems, especially if you are starting from scratch. Most chain gypsies are rated for BBB (short link) or HT (high test) chain, but proper fit is just part of the equation. Quality chain will be stamped with its working load limit.
1. Don’t be fooled by appearances; bright, shiny chain often indicates new stock with a superficial coating of zinc.
2. Check your chain size. The fact that it is 5/16-inch doesn’t mean it will fit your gypsy. A gypsy for 5/16-inch G30 might not take 5/16-inch G43.
3. A look inside the anchor locker reveals the heavy-duty motor for the Maxwell windlass on our test boat. The last 15 feet of chain are marked in yellow so that crew will know when the anchor is near.
4. The two buckets on the left hold 150 feet of old 5/16-inch chain; the orange bucket on the right holds 150 feet of quarter-inch chain, with an additional 75 feet of chain in the blue bucket.
5. The flaking coating on the left-hand chain (after testing) indicates a lesser-quality galvanizing process.
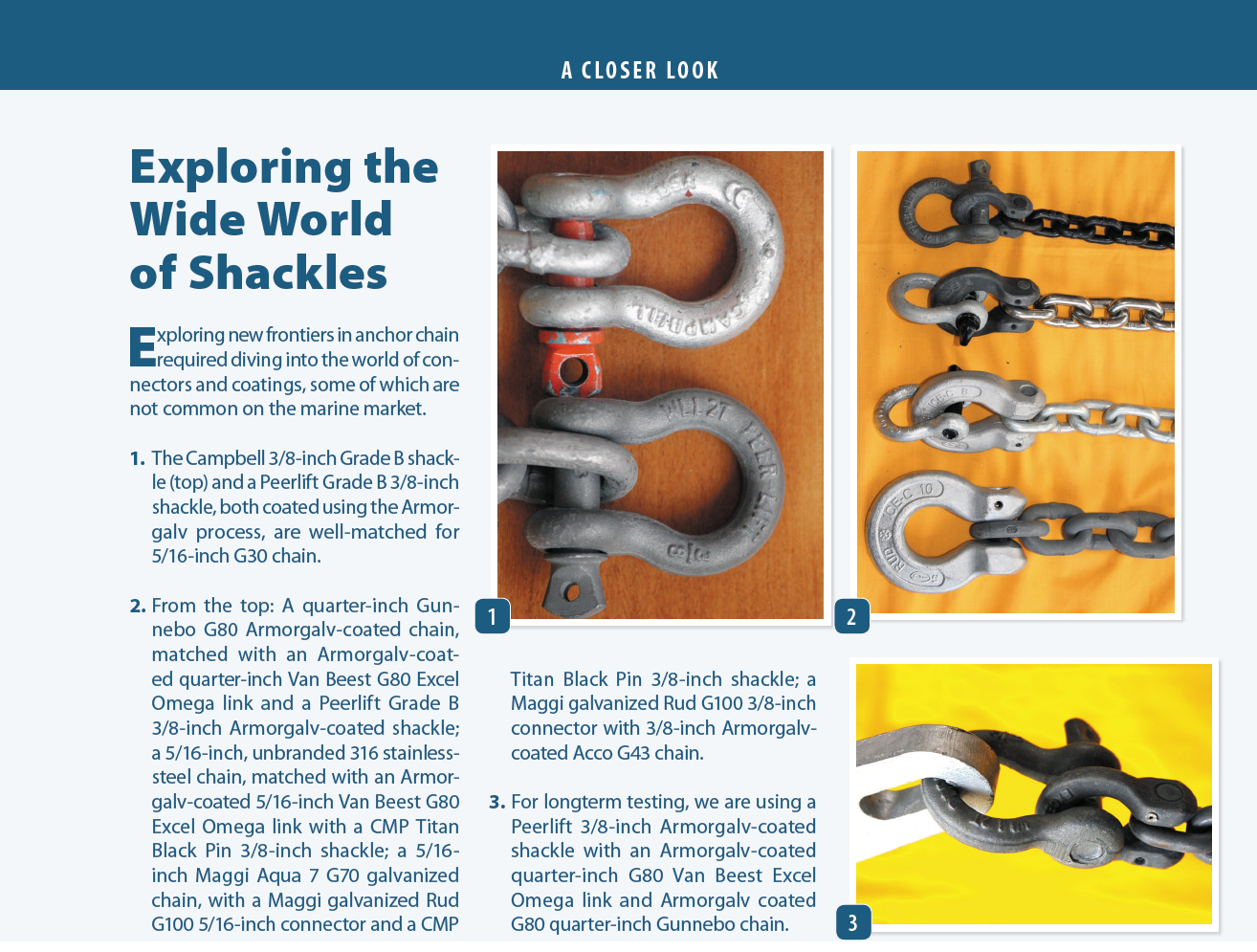
Exploring new frontiers in anchor chain required diving into the world of connectors and coatings, some of which are not common on the marine market.
1. The Campbell 3/8-inch Grade B shackle (top) and a Peerlift Grade B 3/8-inch shackle, both coated using the Armorgalv process, are well-matched for 5/16-inch G30 chain.
2. From the top: A quarter-inch Gunnebo G80 Armorgalv-coated chain, matched with an Armorgalv-coated quarter-inch Van Beest G80 Excel Omega link and a Peerlift Grade B 3/8-inch Armorgalv-coated shackle; a 5/16-inch, unbranded 316 stainless-steel chain, matched with an Armorgalv-coated 5/16-inch Van Beest G80 Excel Omega link with a CMP Titan Black Pin 3/8-inch shackle; a 5/16-inch Maggi Aqua 7 G70 galvanized chain, with a Maggi galvanized Rud G100 5/16-inch connector and a CMP Titan Black Pin 3/8-inch shackle; a Maggi galvanized Rud G100 3/8-inch connector with 3/8-inch Armorgalv-coated Acco G43 chain.
3. For longterm testing, we are using a Peerlift 3/8-inch Armorgalv-coated shackle with an Armorgalv-coated quarter-inch G80 Van Beest Excel Omega link and Armorgalv coated G80 quarter-inch Gunnebo chain.