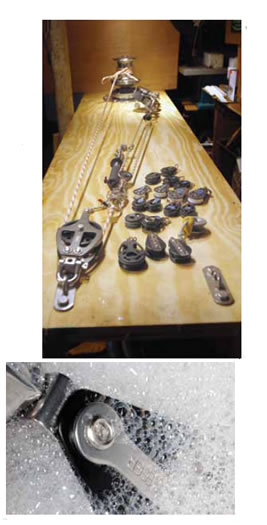
267
With some modification to our bench-test jig, we were able to place two blocks in opposition to each other, attach them via a closed loop of ultra low-stretch line and place the system in tension. The load-inducing mechanism was a vertical capstan Ideal anchor windlass capable of incrementally adding tension to the mix. A Dillon AP dynamometer was placed in series with the tension-creating tackle, and during each test, the load on the closed loop was closely monitored.
With the line and blocks loaded with 200 pounds of tension, we measured how much force it took to move the line in this closed loop arrangement. The peak load required to start the line moving was noted, but its value was less consistent than the load registered during the time when line movement was taking place. Therefore, we used the latter as the measure of efficiency and repeated each test five times in order to develop an accurate reading. The mean, median, and mode data were all quite close for each block, indicating that the measurements were quite consistent. The inline pull paralleled the line suspended between the blocks, and a conventional spring scale was used to measure the tension applied to move the line. Before and after each test, the spring scale’s accuracy was checked using a set of known fixed weights.
Once the efficiency testing was completed, we immersed the blocks in a heated, aerated saline bath devised to accelerate oxidation, crevice corrosion, and dissimilar metal corrosion. The weeklong dunk was taken in stride with only slight signs of galvanic interaction at points where stainless and alloy components met. Far more of an issue is likely to be the bearing abrasion from salt buildup—this is why manufacturers of composite-bearing blocks recommend rinsing off salt and windborne particulate material with fresh water between uses.