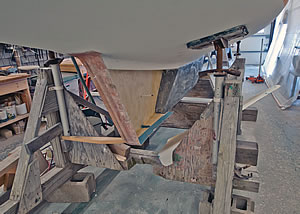
Photos courtesy of Fields and Ballentine
Modern engineering works well with many older designs. In the Stuart Knockabouts original plans, soft wood planks were mechanically fastened to hardwood frames and the its shoal-draft keel/centerboard was bolted to the keelson. Timber boatbuilding is labor intensive and the time-saving shortcuts found in molded FRP hull and deck construction have a well-proven track record. Add to this the fact that wooden hulls and decks are susceptible to rot, and its clear that Hardings vision of a fiberglass/foam sandwich Stuart Knockabout was a best-of-both-worlds solution rather than a sacrilege. The result of the FRP conversion is a stiffer/stronger, monocoque hull that required less maintenance and is much more immune to the elements.
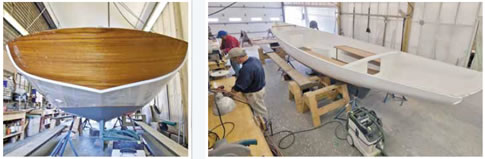
The current boats incorporate six molded elements: hull, keel, forward bulkhead, aft bulkhead, floor liner and deck. The hull-and-deck sandwich structure utilizes an Airex foam core with solid glass in-fills at key points of stress, such as where keel bolts attach and where the rudder post penetrates the hull. The one-piece hull includes an inward-turning flange upon which the deck element is seated, bedded in adhesive, and mechanically fastened. The keel, with its centerboard slot, is attached via J- or L-shaped stainless-steel keel bolts that are cast into the lead ballast. There are two 5/8-inch bolts fore and aft of the centerboard slot, and a parallel row of half-inch keel bolts running on either side of the slot. Broomfield and Sons in Providence, R.I., pour the keels.
The deadwood just aft of the ballast keel is molded in place once the ballast keel has been attached. It involves the use of a split mold (a clam shell-like setup with symmetrical sides). First, the outer deadwood skin is laid up in each of these mold halves, trimmed to smooth edges, with a deadwood foot and trailing edge part of this installation. Once the mold has been secured to the hull and the trailing edge of the ballast keel and aligned, a slow-curing, fiber-filled resin slurry is poured into the cavity through a hole in the hull on the centerline. This process bonds the two sides of the deadwood together and locks the appendage in place.
After the keel deadwood has cured, an FRP rudder post with a cutlass bearing at each end is bonded into the hull and deck. The solid, 1-inch stainless-steel rudder stock passes through the tube and is capped at the top with a bronze tiller fitting. A cast-bronze heel gudgeon captures the lower end of the stock and three welded stainless flanges are sandwiched between the FRP skins of the rudder blade.
A sub-sole FRP molded floor is bonded in place, upon which the teak sole will be fastened. Bench seats are built, and bulkheads are installed by tabbing them in from the backside for aesthetic reasons. Older boats lacked the molded sub-sole element, and bulkheads were riveted in place. The forward bulkhead is water tight for reserve buoyancy purposes, and foam flotation is built into the stern quarter. Some owners opt to have foam flotation added forward.
Fitting out requires a lot of traditional wooden boat building skill. Coamings and the transom are pre-bent to shape on jigs, and theres a serious commitment to high-quality fit and finish.
Those who appreciate examples of the shipwrights art will be pleased to see that this is a sailboat that blends modern hull construction with the aesthetic appeal of well-executed teak trim. The crew at Ballentines Boat Shop sum it up well with the comment, This whole process usually takes us about 850 hours. When I add it up, I always think there must be a quicker way, but details take time, and I think the end result is worth it.
Herreshoff would probably nod in approval.