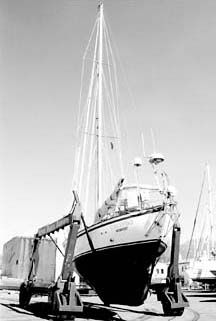
We had covered almost 12,000 miles in the last year by the time we arrived in Marmaris, Turkey in early summer. The Micron CSC bottom paint that we applied last year in New Zealand was pretty much history. I was anxious to repair the dings in the keel that resulted from our grounding in the Red Sea. I was concerned that the large amount of motoring we had done in the last year-more than a third of the distance traveled-might have caused excessive wear on the stern bearing. I wanted to reduce the pitch of our MaxProp slightly to get us a little higher on the engines power curve when motoring through the fickle winds of the Mediterranean.
All in all, it was time to haul the boat. Boatyards with hauling facilities are sprouting in Turkey like mushrooms after a rain. Most larger coastal towns have marinas, and most marinas feel obliged to have hauling facilities. In many cases,however, the hauling facilities are just that, and no more. If you need supplies or skilled labor, you may be out of luck once the boat is out of the water.
We decided to haul at Netsel Marina in Marmaris, Turkey, a full-service facility with a 100-ton travel hoist and a variety of skilled and semi-skilled marinetradesmen at hand should we need them. We did not expect to find any significant problems, but we did not want to be stuck hauled out on the hard waitingfor materials if we encountered any rude surprises.
The downside of hauling here was the relatively high cost associated with a more established facility. Unlike in the US, where the price of a haul is generally a straight charge per foot of length, haulout in this part of the world is charged by the square meter, which is really a more rational approach. A narrow 40-footer pays less than a 40′ multihull, for example. In our case, the cost for haul, block, and launch was about $475-probably about the same as in the US.
We contracted with Marina Technic to power wash the bottom, grind and prime damaged areas on the keel, paint the bottom (with our paint, a European-madeInternational Paint commercial product not available in the US), and polish the topsides. Marina Technic quoted us a flat rate for all jobs based on the sizeof the boat, independent of the hours required for the job. While the quote was a bit high given the amount of work I anticipated and the going labor rate inTurkey, the yard had no way of knowing what they might discover once the boat was hauled, and was covering all bets.
Generally, we leave grunt work to the yard, and spend our on time on jobs that might require a little more skill or finesse, especially if there is a languagebarrier. I have ingested enough bottom paint in 30 years of boat ownership to leave sanding the bottom to someone else. In this case, I have gotten slightly smarter as I have aged.
I wanted to deal with the MaxProp or the stern bearing myself, as these are jobs I have done several times. Although I normally dive on the bottom about every twoweeks to keep the prop clean, we were surprised at just how clean the Micron CSC bottom was when we hauled. There were barnacles on the rudder fittings, which never seem to get properly painted; a moderate layer of slime, and patches of somewhat harder green growth just below the waterline. We also had a spattering of gooseneck barnacle rings on the waterline aft-a legacy of our crossing of the IndianOcean.
Prior to hauling, I had pre-treated the topsides to remove the barnacle rings and rust stains. We use a variety of products for this job, depending on the experience we have had and the availability of products while we are cruising.
Acid cleaners are the only thing that will remove rust stains from gelcoat without polishing away the surface. Since replacing our stainless steel rubbingstrake with brass half-oval in New Zealand, we have eliminated about 90 percent of topside rust stains, but we still get some staining from our outboard lifting crane, the pole for our Mini-M dome, and the mounts for our Monitor wind vane.
We have two types of acid cleaners on board: Davis FSR Fiberglass Stain Remover, and Marykate On & Off heavy-duty hull cleaner. We have long since used up our supply of New Zealand-made Grunt-the best gel acid cleaner we have ever used-which is unfortunately not available in the US.
FSR is a relatively mild gelled oxalic acid that stays in place well on vertical surfaces and does a good job on rust stains and general gelcoat staining. On & Offis a strong liquid hydrochloric acid which runs off vertical surfaces, smokes when you pour it out of the container, and burns skin. It also is one of the few products we have used that removes barnacle rings, and it almost instantly removes the most stubborn rust stains. Carefully employed, it is a useful, powerful cleaner.
Cleaners: Cheap, and Expensive
The West Marine catalog has 10 pages of hull and deck cleaning and maintenance products. Unfortunately, once you leave the US you are limited to what you carry onboard, and what you can find locally. Surprisingly, we have found a lot of US-made maintenance products throughout the world, but the overseas price issometimes outrageous.
In Turkey, for example, we found 3M Multi-purpose Boat Soap-$10.99 in the West Marine catalog-at the local 3M distributor. We have used this before, and havefound it an excellent all-purpose cleaner for virtually everything on the boat. Unfortunately, a quart of this simple cleaner cost $29 in Turkey! Therewere cheaper local products, but it was a bit difficult to read the labels. We didnt really want to try to clean the hull with teak cleaner by mistake.
Thanks to Maryann, I discovered one cheap and effective special-purpose cleaner: plain old acetic acid, or vinegar. She regularly uses a dilute vinegar and water solution to wipe down both interior and exterior varnish.
I have struggled hard to remove stubborn saltwater deposits from our topsides with various cleaners, but. vinegar does the job almost effortlessly. Washing thetopsides with straight vinegar, applied with a sponge, removed about 98 per cent of the mineral deposits on the first pass.
Admittedly, our neighbors thought the whole operation was more than a little strange. First, I washed the topsides with soap and water. Then I applied a bluegel to sections of the hull. After rinsing that off, I applied a smoking liquid to stubborn stains. After rinsing that off, we came to the vinegar wash.
Unfortunately, you can’t get plain white vinegar in Turkey. Our entire boat, not to mention the crew, smelled like a 17-ton Turkish salad at this point. Fortunately, a final wash with soap and water got rid of most of that smell, although by now everyone on the dock was convinced, perhaps correctly, that the American crew on Calypso was stark raving mad.
We did all this work in the water, before hauling, to avoid scheduling conflicts between cleaning and painting once we were hauled. The less time we spend out of the water, the more we like it. Since none of our workers spoke a word of English, and the crew of Calypso not a word of Turkish, this proved to be agood idea in order to minimize misunderstandings.
Haulout
Hauling was an adventure in itself. In the five yearssince our launch, we have hauled on a trailer withhydraulic arms, two different travel hoists of about70 tons capacity, and a mammoth 250-ton travel hoist.
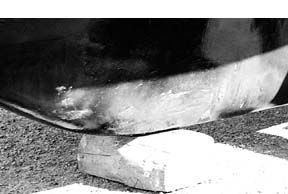
This time, we thought we were to be hauled on theyards 100-ton lift. Instead, they directed us to the ramp where hauling is done on a custom hydraulic trailer. This trailer is rated, I later discovered, for 12 metric tons-about 26,500 pounds. Fully loaded and stocked, we go about34,000 pounds, and even without full fuel, full watertanks, and with a reduced store of provisions, weweighed at least 33,000 pounds at this point, judgingby our flotation.
Despite my attempts at explaining that there was moreto this boat than met the eye, the yard was convincedthat we could not possibly weigh more than the 44-footcharter boats that are regularly hauled with thistrailer. They soon found out, however, that we were very heavy, and the overloaded trailer struggled under its burden. It was like the circus act in which a huge clown rides a tiny bicycle.
Knowing the type of margins usually built intolifting gear, I was only moderately concerned, but thelift operators were decidedly nervous as the liftstruggled to climb the steep ramp into the boatyard.
We were determined to make this a quick haul. We were out of the water, powerwashed, and blocked by noon. I taped the waterline during the yards lunch break.
After three hours of wet-sanding, the first coat ofbottom paint was applied to all of the bottom exceptthe damaged areas of the keel.
At the same time, we ground back the dings in thekeel to bright metal, and applied the first two coatsof epoxy primer. By sundown the first day, the boatlooked almost ready to go back in.
A careful examination of the keel and the keel-hulljoint showed no evidence of anything other than cosmetic damage. With an iron keel, however, it’s important to properly repair even cosmetic damage as soon as possible after an accident. Copper bottompaint on adjacent, undamaged areas of the keel canrapidly cause pitting on unprotected areas of iron. Anexternal lead keel gives you a lot more latitude inthis case.
We are very pleased at the way the original paintsystem applied by Jamestown Boat Yard in 1996 has heldup on the iron keel. After sandblasting, the keel wascoated with a quick-drying bare steel primer beforeany fairing was applied. The keel then got the samemulti-coat system of Interlux Interprotect that wassprayed on the rest of the bottom before theapplication of bottom paint. Except where we havegrounded and worn through to bare metal, the 11,000-pound keel casting shows absolutely no sign of rust.
The Second and Third Days
On the second day of our haulout, the dings in thekeel got three more coats of InternationalInterporotect, and the rest of the bottom received asecond coat of paint.
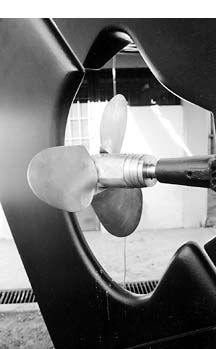
At the same time, our topsides man showed up with his helper to buff out the topsides. We also had him do a gelcoat repair to a deep gouge just under the rail. Weacquired this ding when I mistook a black steel collar on a piling in Ashkelon, Israel, for rubber fendering, Pivoting on the piling to get into the narrow slip, Iput a gouge about a foot long and over a millimeter deep in the topsides. It was not my finest day of boathandling.
Our gelcoat man’s first attempt at a repair was a good color match, but a bad repair. Frustrated at my inability to communicate verbally, we got slightlygrouchy with each other. I finally made him understand that we wanted perfection here, and he very nearly obliged. After calling him back the next day for stillmore work on the repair, he figured out that I was completely nuts, and obliged by doing a very, very good job.
We were all smiling friends after that.
Buffing out the topsides was a little less successful. The yard didnt quite understand that I wanted the topsides waxed as well as polished. Theytypically buff out with a mild polishing compound, which brings up the gloss beautifully, but offers no protection. The concept of protecting the freshly-polished surface with a coat of wax seemed a mystery to them, possibly because it meant a lot more work.
At the end of the day, I gave up trying to get my wayon this one. Instead, I cleaned and waxed thewaterline myself out of the water, then waxed thetopsides properly from the dinghy after we launched.
I figure I did about 40 per cent of the topsides work myself, even though I paid for 100 per cent of it. This is the price you pay for being a perfectionist, but it’s a price we’re willing to pay-at least for now. The topsides literally look like those of a new boat, despite having completed 25,000 miles of cruising.
That night, I applied a third coat of bottom paint in a band about two feet wide from the waterline down. I also put a third coat on the rudder and around theprop aperture, along the stem, and on the front of the keel.
The next day, I cleaned, serviced, and re-pitched the MaxProp while the bottom man painted the repaired areas of the keel. We had just a little too much pitchfor motoring against a chop, and I wanted to be able to run the engine a little higher on its power curve, despite the additional fuel consumption.
Our MaxProp VP is designed to be adjusted under water, without tools. This is a big plus for a cruising boat, which is likely to get heavier over time. You canre-pitch the prop to compensate for the additional weight on the boat without hauling.
The prop was pitched for our estimated coastal cruising displacement of 29,000 pounds. Since were pushing at least two tons more than that through the water now, the prop was slightly over-pitched.
Marine growth in the adjusting mechanism prevented me from doing this job without servicing the prop first. With a clean, well-greased prop hub, we should now beable to fine-tune the pitch in the water if necessary.
I removed one degree of pitch-about a half inch, in conventional terms. This means we will have to run the engine slightly faster for the same speed through thewater, and we will be using a bit more horsepower. We should punch through waves a bit better when necessary, however, since the engine will be putting out a bit more horsepower for a given boatspeed.
The stern bearing showed no significant sign of wear, so we left it alone for another year. We replaced it last year in New Zealand, and carefully aligned theengine at the same time.
Back in the Water
Less than 75 hours after hauling, we were back in the water. Generally, the haulout was painless and successful. Our total bill for hauling, all the work, and launching was just under $1500. Add to this the $360 that we spent on bottom paint in Cyprus, and you have a haulout at just under $2000, which was our target.
Of course, we ended up doing more work ourselves than we originally intended, but thats not unusual.
Once back in the water, we could put the finishing touches on the topsides. For us, the finishing touch is always a coat of Collinite Fleetwax No. 885. This is a hard paste wax which requires some elbow grease to apply and buff out, but it gives a superb, hard, long-lasting finish which lasts longer than anything we have ever used.
We had three cans on board when we left the US in late 1997, and we’re now down to our last half can. It must be time to head back to the USA for a refill.
In Practical Sailors test of waxes some five years ago, Collinite Fleetwax was the highest-rated product. You may have trouble finding it, as it isn’t carried by most marine catalogs. You can get information on local distributors from The Collinite Corp., 1520 Lincoln Ave., Utica, NY 13502, 315/732-2282. The web address is www.collinite.com.
While we waxed the topsides, Marina Technic’s excellent mechanics, under the direction of Sinan Umul, gave the faithful Perkins 4-108 a bit of well-deserved attention that was a bit beyond our skills.
Our three-day haulout in Turkey was the fastest ever, and was reasonable in price. At the same time, we accomplished everything we wanted to do. You can’t askmore than that.