Every fall, as the hauled-out boats are sardined into boatyards, a walking tour reveals the casualties from the underwater war. Saildrives are deeply pitted and shedding paint. Bottom paint is burned near seacocks. Folding props no longer fold. Most often, these losses are blamed on the zinc anodes-or lack of them.
The concept of sacrificial anodes is simple; connect the valuable bits of underwater metal to a replaceable hunk of more reactive (less noble) metal, so that it creates an electrical potential (voltage) difference between the anode and the stuff we want to keep. These electrons force potentially damaging corrosion reactions in the reverse direction, slowly dissolving the anode but keeping the expensive bits safe.

The process of galvanic corrosion can occur anywhere that there is a circuit between two dissimilar metals. It is greatly accelerated in the presence of salt water. As the name implies, the anodes, which are made of less noble metals like aluminum or zinc, sacrifice themselves to protect the least noble metal in the circuit.
Engine-cooling systems, sail drives, and prop shafts are the most common applications where anodes are used on sailboats. Outboard engines also require anodes to protect their aluminum lower units. Because the anodes are eaten away in the process, boat owners must replace them on a regular basis, usually when the anodes mass is reduced to one-half of its original size.
Sacrificial anodes are relatively inexpensive, but the consequences of corrosion resulting from an ineffective or depleted anode can be serious. More than one boat has sunk on its mooring due to a through-hull failure caused by galvanic corrosion. Although effective against typical galvanic corrosion, these zincs can be quickly depleted by the more potent stray-current corrosion.
The trouble lies in finding a material that will provide just the right potential, where we need it, for as long as we need it. With this in mind, we launched a long-term test of zinc anodes. We decided to skip magnesium alloys for this round of testing; while they are just the thing for an aluminum-hull boat in fresh water, they are terribly wrong for everyone else. For brackish and seawater, specialized U.S. mil-Spec zinc and aluminum alloys are required, and these are the focus of this investigation.
Aluminum (MIL-DTL-24779D) is the relative newcomer to the market, promising longer life, because aluminum has more electrons available per volume. Aluminum resists the deactivating scale deposits in brackish water and provides a slightly greater driving potential (voltage). It is also cheaper and less toxic to marine life than mil-spec zinc. The zinc versus aluminum rivalry was something we wanted to look at closer in our anode testing, which began a little over year ago in the brackish waters of Chesapeake Bay.
Anode Basics
In theory, we need to be protecting just one kind of metal. This would make it much simpler to chose the correct potential zinc and not risk overprotecting, which can have some troublesome side effects, particularly on metal and wood boats. (These are described in more detail in the Can You Have Too Many Zincs? Inside Practical Sailor blog post online.) In effect, we must choose the most reactive underwater metal and target that for protection. Thus, there are some simple rules to remember:
Avoid joining dissimilar metals. Anodes arent meant to correct big mistakes that can be fixed. It is up to us to avoid bad pairings in wiring, plumbing, and mechanical fittings. We should not blindly install brass or steel fittings up against a bronze seacock, assuming the anodes will protect the less noble material. It is better to stay with one metal, as much as possible, and when we can’t, do as much as possible to protect it from galvanic corrosion-either through the use of anodes, insulating coatings (or material), or both.
The right anode provides the right potential. For steel and bronze, zinc anodes are the common choice. For steel hulls, a good, tight coating is required to prevent hydrogen-induced paint flaking, and the voltage provided by zinc must be just right. For aluminum hulls, outboard engines, and saildrives, only aluminum anodes developed for salt water make sense. The alloy is more reactive than the alloy used in the drive and should provide sufficient potential; check with the manufacturer for specific guidance.
How many? The American Boat and Yacht Council (ABYC) directions for cathodic protection (Standard E-2), spells out the details for a compliant system, which must be capable of inducing and maintaining a minimum negative shift of -200 mV relative to the potential of the least noble metal being protected. As for size, the anode: shall be sufficient to provide continuous current output for at least the period between inspections.
If you don’t see any warning signs of poor protection, such as the rapid deterioration of your existing anode, then you can assume your existing anodes are the correct size. However, if you have any concerns about the effectiveness of your protection system, you should have it checked. This is something you can hire a surveyor to do, but a competent do-it-yourselfer with the right tools can also confirm this with a high-quality digital multimeter and a AG/AGCL reference electrode. Table II in ABYC Standard E-2 shows the following ranges of cathodic protection in millivolts (mV) for hull of various materials: fiberglass -550 to 1100 mV; wood -550 to -600 mV; -950 to -1100 mV; steel, -850 to -1100.
For the typical auxiliary sailboat, where the only important underwater metals are the prop and shaft, a shaft-collar zinc is usually enough, although several can be installed for longer life. Any metal through-hulls should be cathodically bonded (which the ABYC defines as the electrical interconnection of metal objects in common contact with water) to the engine negative terminal, or its bus, and to the source of cathodic protection, i.e. the sacrificial anode.
If the rudder has vulnerable parts, a separate zinc is advisable, since the rudder gudgeons are probably not bonded. The engines cooling system is usually protected by a separate anode (a pencil anode) that needs to be checked and replaced regularly. Metal boats require special care. An excellent paint coating (typically a two-part epoxy preceded by a hot, flame-sprayed zinc primer), and more zincs are required for steel boats. We suggest professional advice for protecting aluminum hulls.
Make good contact when installing anodes. Clean all of the surfaces to shiny metal with a scraper and wire brush. Seat the anode with a light tap from a hammer; most are sized for a tight fit, and this tap will stretch them just enough for a perfect fit. Dont forget to add waterproof grease on the bolts. Sea Shield anodes have internal threads (as opposed to an embedded nut), and even those with imbedded, stainless nuts will benefit from the added protection of grease. Never paint over or under an anode.
All anodes should be the same metal. If you decide to switch to aluminum, then switch shaft, prop, rudder, and hull anodes. Internal engine anodes can remain zinc.
Zinc guppies are no substitute. There are zinc fish that can be clipped to the boats bonding system, providing backup protection in case of failure. The problem is that they arent necessarily connected to the metal were trying to protect-most clearly the prop shaft. Regular underwater inspection is preferable to stop-gap measures.
What We Tested
We tested both aluminum and zinc collar-type shaft anodes from Canada Metals Pacific (CMP, Martyr brand), Sea Shield, and Camp Company. It has been suggested that painting the area near the mounting screws with nail polish can increase the security of the anodes as they wear, so we tested this approach with both zinc and aluminum anodes. Because zincs are such a critical component in shipping, the standards for composition are stringent. Although we did not lab test for composition, all of the zincs we tested claimed to meet U.S. military specifications, mil-spec, for composition.
For details on our test protocol, see the accompanying How We Tested.
Observations
Interestingly, the most obvious difference we noted was the zincs effect on marine growth. Within weeks, we could see that copper protected by aluminum anodes had attracted more growth than that protected with zinc anodes; although, by the end of the test period, all of the test pipes were heavily encrusted.
The unprotected copper pipe remained growth-free after one year, evidence that our unprotected copper was indeed gradually shedding ions. This shedding (.35 mils of thickness per year), though bad for the metal, was effective at protecting against marine fouling. The unprotected copper pipe also shed layers of pink scale, something no other sample did.
Clearly, anodes are good for protecting copper pipe from corrosion, but we wondered whether the anodes, by rendering the copper less resistant to marine growth, might promote growth on the inside of the tubing. Even though the outside of the protected pipes accumulated an average of one-inch of growth, both hard and soft, the insides of the pipes had no hard growth and only a light slime coating. Presumably, the lack of light inhibited soft growth and the reduced water flow allowed the few available copper and zinc ions to be effective on the inside of the pipe. If you have problems with marine growth in your plumbing systems such as air-conditioners, heat exchangers, and water-cooled refrigeration systems, you might try a zinc anode instead of aluminum.
The driving potential (voltage) and current (amperage) were both slightly higher for aluminum anodes than for zinc. However, the readings did not measurably differ between the brands tested. Additionally, since wastage rates did not vary significantly between anodes of the same material, we can only assume they used similar alloys.
Heavy marine growth made measuring voltage potential impossible, but calculations and commonsense agree that protection currents drop significantly due to wastage, scale, and growth. Since all of the copper pipes connected to anodes showed no measurable loss of material, performance was acceptable for all of the anodes we tested.
Wastage rates will vary according to the velocity of water moving past the anode, size of the metal being protected, and the quality of the paint on the protected metal. The anodes in our test will typically last one year. They should be inspected for wear regularly. The samples in the accompanying after photographs have about 75 percent remaining; conventional wisdom is that 40 to 60 percent remaining is the retirement criteria, depending on the extent of wear near the bolts.
The additional available electrons in aluminum anodes suggest they might last longer, but in brackish water, the aluminum is more active, offsetting the theoretical difference. We also noticed that only aluminum anodes attracted hard growth (on the anode itself, not the attached copper pipe), supporting that they are, indeed, less toxic to the environment.
A common concern is that the zinc may fall off, leaving the boat unprotected. None of the bolts failed when we first re-torqued and then removed them at the end of the test, but since they did not experience the vibration of actual use, this does not tell us much.
It was not obvious whether painting the area around the mounting screws increased security significantly. We tried to induce a thread failure on our three types of samples-zinc, aluminum, and those protected with nail polish-but all of them held equally well to beating with a hammer.

Zinc Anodes
All zinc-protected pipes showed more growth and more patina development in the first month of testing than aluminum-protected pipes. However, this difference became less pronounced as time passed.
Although aluminum seems to provide slightly superior protection in the brackish water of the Chesapeake Bay, we were surprised by the deep pitting on the aluminum zincs rather than the general erosion we are accustomed to with zinc anodes. On the other hand, when we tried to break both types of zincs off the pipes during a vigorous beating with a hammer, even the most corroded samples would not crack. Additionally, one could presume the lighter aluminum anodes would experience less vibrational stress on a rotating shaft than would a zinc anode. The alloys seem to have good toughness, and we would expect both zinc and aluminum anodes to stay on a shaft until the very end of their working lives (40 to 60 percent wastage).
Camp X-2
With less material and no interlock between the two halves, the Camp Companys Camp X-2 zincs are less secure and have reduced life expectancy when compared to Martyr and Sea Shield anodes. They include a copper rivet in each half of the casting, presumably to improve contact. The Camp X-2 is available in zinc only.
Bottom line: This is a discount anode that will provide protection, but its non-interlocking design means it is more likely to lose contact when wastage is extreme.
CMP Martyr
Testers liked the Canadian Metals Pacific Martyr zincs generous weight and solid interlock between the halves. The wastage rate was slightly lower than that of the Sea Shield zincs, and the robust construction at the union led testers to believe that they were destined to last the longest between changes. Only future testing, however, will bear this out, and the zincs on a well-maintained boat should never reach the point where the integrity of the union is vulnerable.
Bottom line: Thoughtful design made these zincs desirable, and their affordable cost-per-ounce adds value. They are our Best Choice and Budget Buy pick in this test field.
Sea Shield
Instead of a separate nut cast in the anode (like the Martyr brand), the Sea Shield Marine Streamlined Shaft Anodes have threads cut into the anode material itself. Though we were initially concerned that these might corrode out, they held up very well, perhaps aided by the waterproof grease we coated the bolts with during installation. They include a solid interlock in the casting.
Bottom line: These have a little less material than Martyr zincs, but the streamlined shape will appeal to racers. We Recommend them. [Editor’s note. The lower range price for these zincs was $6 to $8 online at the time of testing, not $11 as suggested in the adjacent table.]
Conclusions
Not keeping anodes in place is obviously a major mistake. Even during the short period of our test, our plain-
copper pipe lost an unacceptable amount of metal. This makes us wonder about air-conditioning tubing, which is typically not anode protected. Although we have little data on this, our calculations suggest that tubing could last 15 to 25 years without protection, and vendors we spoke with agree that this is not unreasonable. Vendors did warn that a common mistake in such systems is installing an oversized pump that increases the flow rate, and the corresponding wear on the tubing.
Although aluminum anodes held the promise of longer life due to more available electrons, they depleted just as rapidly because of their greater activity. There was also considerably more marine growth on the cathode (copper tube), no doubt the result of lower copper availability.
Whether this is better or worse may depend on your point of view; a racer might be attracted to the lighter weight of aluminum, but his bronze prop will require slightly more cleaning. Folding props can use all the help they can get, suggesting a need for aluminum anodes. Although a case can be made for the more streamlined Sea Shield anodes versus the bulkier CMP/Martyr anodes, we prefer the additional mass of the Martyr zincs, since they should last longer and the bolting arrangement gave us more confidence.
We recommend using only zinc anodes for plumbing systems and heat exchangers. The sacrificed zinc ions help keep growth at bay. We put a zinc anode in our AC system and will monitor it closely.
We are now hanging an identical matching set of anode samples in the Gulf of Mexico (Sarasota, Fla.) for a year to see whether the results will vary in full-strength salt water, as compared to this test in brackish water. Stay tuned.
For a more complete discussion on how to monitor galvanic corrosion, as well as advice on troubleshooting a wide range of marine electrical problems, the book Advanced Marine Electrics Troubleshooting by Practical Sailor contributor Ed Sherman is available from our online bookstore (www.practical-sailor.com/books).
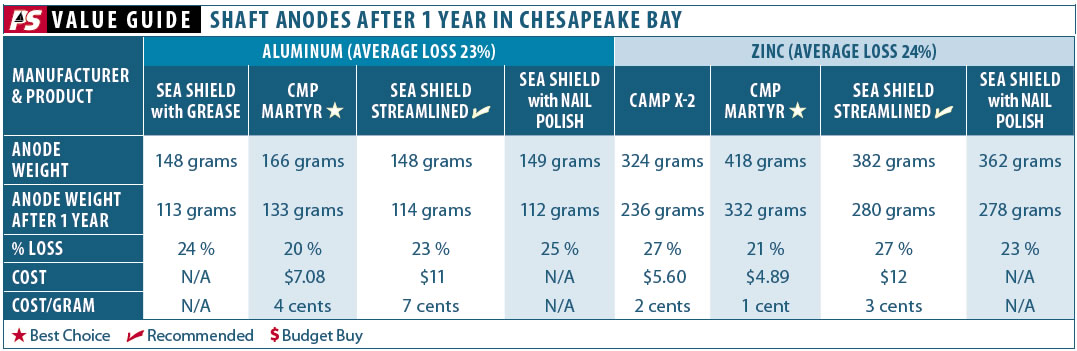
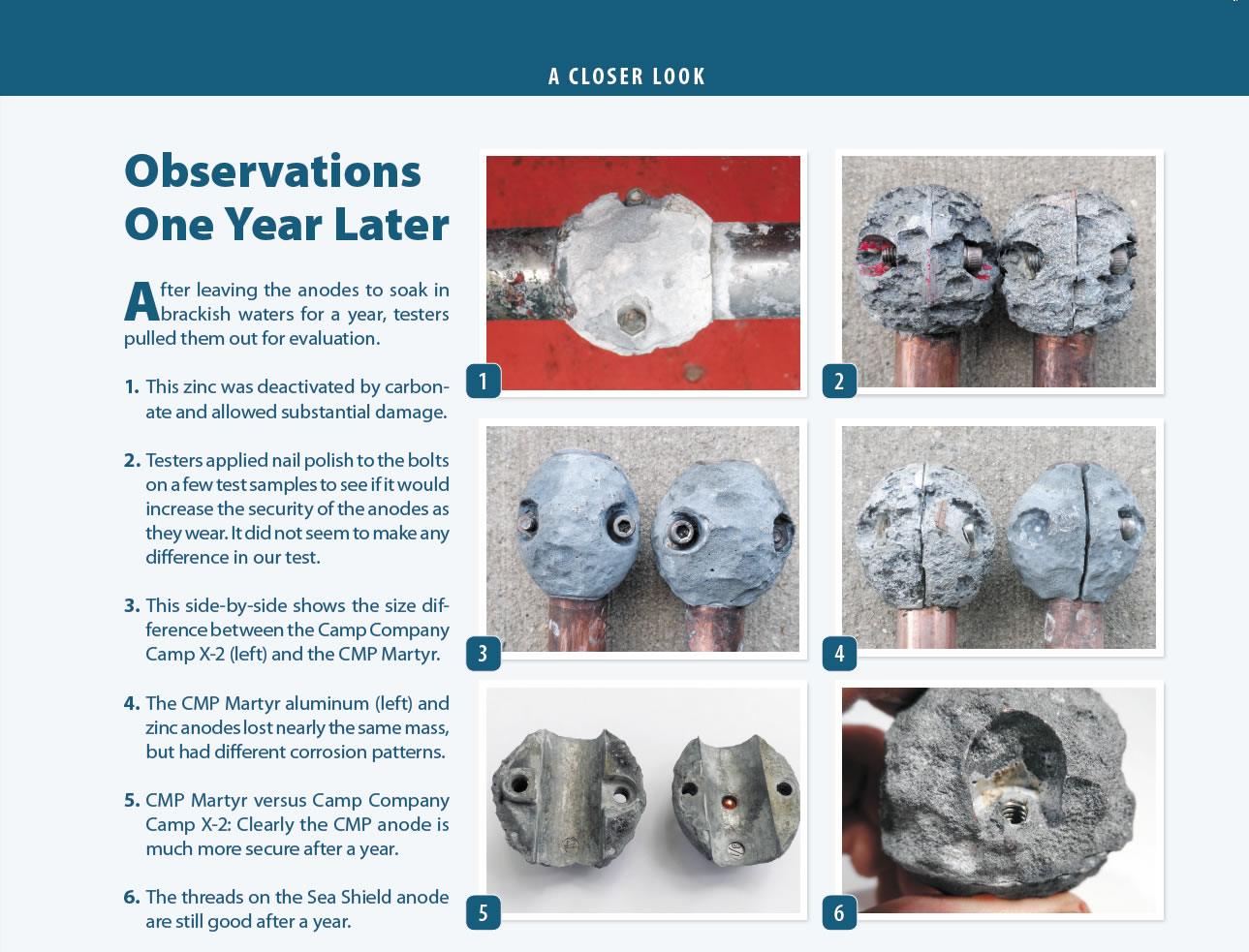
After leaving the anodes to soak in brackish waters for a year, testers pulled them out for evaluation.
1. This zinc was deactivated by carbonate and allowed substantial damage.
2. Testers applied nail polish to the bolts on a few test samples to see if it would increase the security of the anodes as they wear. It did not seem to make any difference in our test.
3. This side-by-side shows the size difference between the Camp Company Camp X-2 (left) and the CMP Martyr.
4. The CMP Martyr aluminum (left) and zinc anodes lost nearly the same mass, but had different corrosion patterns.
5. CMP Martyr versus Camp Company Camp X-2: Clearly the CMP anode is much more secure after a year.
6. The threads on the Sea Shield anode are still good after a year.