How much load does a keel bolt or a winch through-bolt put on a hull or a deck? How thick should the laminate be at these bolt holes? How big of a backing plate is needed?
The current practice when through-bolting hardware, keels, chainplates, or large structures such as davits, through cored laminate is to remove any core material and replace it with solid glass before adding a backing plate (and sometimes a topping plate). Sometimes, the builder replaces the core with solid laminate during construction; other times, the owner or installer does it. And sometimes, it doesn’t happen at all.
But how strong, actually, is solid fiberglass-reinforced laminate? And how does it behave when a fastener is subjected to various types of loads? If we had a better understanding of how solid laminate behaved under load, we’d have a clearer picture of things like how much core needs to be infilled, how thick a laminate should be, and how to best use backing plates and topping plates.
For this test, we merely wanted to quantify the force that causes an ordinary nut washer and bolt setup to pull through solid laminate of various materials and thicknesses. There exist minimum yacht construction standards-as set by the America Boatbuilding Standards and the European Union (through the European Recreational Craft Directive)-but a recent spate of failures, especially with regards to bolted on keels, prompted our inquiry. We didnt expect to develop any absolute guidance; we aimed only to test the soundness of common rules of thumb, such as an inch of laminate for every inch in bolt diameter, that we routinely see being used for bolted-on structures and hardware.
What We Tested
For our comparison, we used West System epoxy resin to prepare 5-by-5-inch test panels made of hand-laid, 17-ounce, biaxial fiberglass cloth. The panels were 45-percent fiberglass by weight, determined by testing. These samples were of three different thicknesses-1/8 inch (four layers of cloth), 3/16 inch (six layers), and 5/16 inch (eight layers). We also tested quarter-inch and half-inch, pre-cast, structural grade, and Garolite G10 fiberglass laminate, a material we commonly use for backing plates and framing components in larger fiberglass projects. Finally, we cut a section of 5/16-inch laminate from a scrapped boat that appeared to be an alternating mat/roving layup.
How We Tested
The square samples were centered over a wooden ring (4 inches in diameter and -inches thick) backed by a quarter-inch steel plate. This was, in effect, a -inch deep hole, or annulus. We gradually tightened the lubricated, 5/16-inch center bolt through the laminate with only a common washer to spread the load. We recorded the bolt torque when we heard the first telltale cracking sounds of laminate failure.
Typically, samples withstood an additional 20-percent of load before obvious failure, but once audible cracking began, the laminate was clearly weakened. During our testing, the torque was measured with a calibrated load cell, and this figure was adjusted to calculate load. A table detailing the resulting loads can be found with the online version of this article.
Findings
One of the most notable observations was that the bolting washers bent like tinfoil when the pressure came on, providing very little load distribution. A proper backing plate-one that is adequately sized with rounded corners and tapered edges-would help prevent point loads at hotspots. Although stainless steel is commonly used as a backing plate material, there are better, thicker materials, ranging from plywood to fiberglass, that can be tapered at the perimeter. Many types of solid wood tend to be poor backing plates because of the tendency to crack.
Both the pre-cast structural and Garolite’s G10 fiberglass failed suddenly by breaking in half in our lab tests. However, there were telltale fissures on the underside of the samples with the first cracking sounds, but this was invisible without removing the backing plate.
Our hand-laid laminate failed more gradually, with increasing popping noises, as fibers deeper in the laminate failed. There was always a visible X pattern on the bottom side at initial failure, but again, no visible evidence of internal damage on the top. The pattern was similar on all thicknesses, from 1/8-inch to 5/16-inch. Eventually, complete failure resulted with the washer and nut pulling through the laminate. As failure began, a faint pattern of laminate failure appeared on the topside, clearly visible but not breaking the surface.
Testers then added strong backing plates: 1-inch-by–inch plywood washers backed by 1/8-inch-thick steel washers. The plywood withstood the force without cracking, and the steel washers bent, although only slightly and only after fiber failure had begun. This time, the failure was pure shear, with the 1-inch washer combination pulling right through with only localized damage. Again, evidence of impending failure was visible within the laminate, though it never reached the top layer.
This last test highlights the importance of increasing both laminate thickness and backing-plate size as bolt diameter increases. Because all of the failures in our testing, and most of those we have seen in the boatyard, have been shear failures, it is critical that we balance the amount of material cross-section in the shear zone.
Bolt strength is proportional to cross-sectional area or the square of bolt diameter. If we increase the fiberglass thickness in proportion to the bolt diameter and increase the backing-plate diameter proportional to the bolt diameter, we have increased the material cross-section in proportion to the bolt strength and have maintained this balance. The right ratio will vary by application, but a 1:1 ratio for bolt-diameter to laminate thickness seems questionable if the bolt is sized to match the loads. It is possible, in principle, to use a larger backing plate and thinner laminate, within limits. (Thicker laminate and smaller backing plates can also work.)
In every case, there was only the faintest visible evidence of failure on the fiberglass test panels top, right up until the point of massive failure. Even the thinnest coat of paint would hide evidence of beginning failure. Never paint areas surrounding high-load critical fasteners.
The sample cut from the scrapped boat behaved much like the hand-laid samples, gradually failing with considerable noise. The surface finish obscured any internal damage. Here is a summary of our findings regarding various materials; the data table can be found with the online version of this article.
Structural Fiberglass
While not as strong as fiberglass that you lay yourself, McMaster Carr Structural Fiberglass (8537K45), for virtually all purposes, is strong enough, rigid, and saves labor. It has good tensile strength (25,000 pounds per square inch, or psi) and very good compression strength (34,000 psi). We used this material much like lumber when building steps for our test boats extended transoms. The structural fiberglass also makes a good backing plate, where the balance of strength to stiffness is perfect. It runs $68.71 for a 2-foot-square sheet of quarter-inch thickness.
Bottom line: This is a sturdy, economical material suitable to many purposes.
Garolite G10
Considerably stronger than structural-grade fiberglass and very dense with glass fibers, the Garolite G10 excels at holding threads and in other high local stress and high compression applications. Flexural strength is good (38,000 psi), and compressive strength is very impressive (65,000 psi). Because the G10 is considerably more expensive than structural-grade fiberglass and four times as expensive as hand-laid (materials only), we only use it when its exceptionally high density is absolutely required. It costs about $120 for a 2-foot-square sheet of quarter-inch thickness.
Bottom line: G10 offers as much strength as you can pack into a pre-cast product.
Hand Laid Fiberglass
We used backing mat in our hand-laid fiberglass samples. Our hand-laid was considerably stronger than the structural grade pre-cast and slightly stronger in tension than G10, though it was much weaker in compression; it did not withstand the compression forces under nuts particularly well. It is considerably more economical than pre-cast products once you get the hang of laminating, and you can customize it to the application by adjusting thickness where needed. Tapered edges are recommended as this reduces point loading at the edges. You can even add a lightweight core. We like this material a lot better than cloth, roving, or mat because its strong and easier to work with. It costs about $10 per 50-inch-wide yard, laminated with either epoxy or polyester resin.
Bottom line: Hand-laid fiberglass is the workhorse of the boatbuilding industry, for good reason.
Conclusions
It is telling that we never broke a bolt (except a Grade 2, the weakest sort) or stripped a thread while testing solid fiberglass plate up to one-bolt diameter in thickness. A 1:1 ratio between panel-thickness and bolt diameter, thus, would seem to promote too-thin laminate. We should have reached the bolts breaking strength, but we did not. (When testing cored sections, we broke plenty of bolts.)
Based on our findings, laminate thickness should be at least 125 percent of the bolt diameter in order to meet bolt-breaking strength. If we allow for variations in lay-up quality control (inconsistent roll-out, poor wetting, and resin-rich areas), lower strength materials (chopped strand, mat, roving), laminate that is at least 150 percent of bolt diameter for laminate thickness seems a reasonable, safe minimum.
Since we confirmed that most failures are in shear, a logical approach would be to increase the shear cross-sectional area in proportion to bolt strength. Bolt strength increases in proportion to bolt cross-section and with the square of bolt diameter. In our tests, increasing laminate thickness to at least 1.5 times bolt diameter and backing-plate diameter to at least five times bolt diameter seemed a good balance, but there are many variables that our simple test could not address.
Fiberglass does not like point-loading. Tapered or stepped backing plates with rounded corners alleviate this. Another approach is to spread the load across a larger number of slightly oversized fasteners. If larger fasteners are required because of corrosion concerns or other structural factors (as in keel bolts or chainplates), then a conservative design using bolts with large safety factors is prudent. This will reduce the point loading under the bolts and reduce the potential of stress-induced corrosion failures.
The areas around critical high-load fasteners should never be painted. Painting makes proper inspection for damages early stages impossible. Only relatively clear laminating resins should be used so that warning signs can be seen.
Backing and topping plates can help spread point loads and help provide a secure mounting location for rope clutches, turning blocks, and other types of highly loaded hardware. Care must be taken, however, to avoid the creation of an abrupt change in flexural modulus-a term that defines how a material behaves as it bends. Adding either a backing plate or a combination backing and topping plate can stiffen a panel, but it also can create a localized stress riser in the laminate where the reinforced and non-reinforced deck laminate meet. Mechanical energy is focused on this junction, and critical failures often result.
One of the best ways to avoid this problem is by tapering the backing and topping plates and tapering the transition area between solid laminate and core during construction.
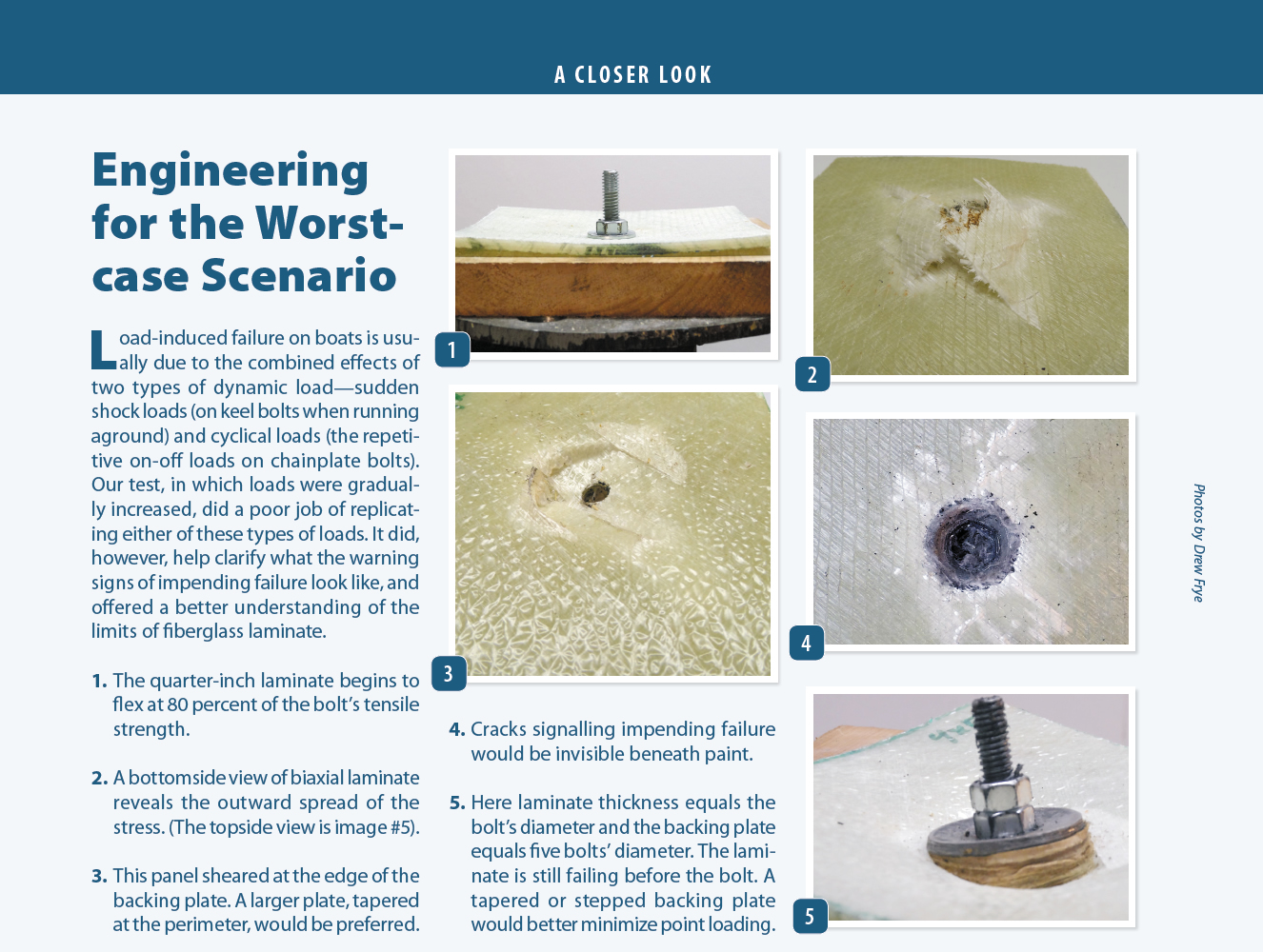
Load-induced failure on boats is usually due to the combined effects of two types of dynamic loadsudden shock loads (on keel bolts when running aground) and cyclical loads (the repetitive on-off loads on chainplate bolts). Our test, in which loads were gradually increased, did a poor job of replicating either of these types of loads. It did, however, help clarify what the warning signs of impending failure look like, and offered a better understanding of the limits of fiberglass laminate.
1. The quarter-inch laminate begins to flex at 80 percent of the bolt’s tensile strength.
2. A bottomside view of biaxial laminate reveals the outward spread of the stress. (The topside view is image #5).
3. This panel sheared at the edge of the backing plate. A larger plate, tapered at the perimeter, would be preferred.
4. Cracks signalling impending failure would be invisible beneath paint.
5. Here laminate thickness equals the bolt’s diameter and the backing plate equals five bolts’ diameter. The laminate is still failing before the bolt. A tapered or stepped backing plate would better minimize point loading.
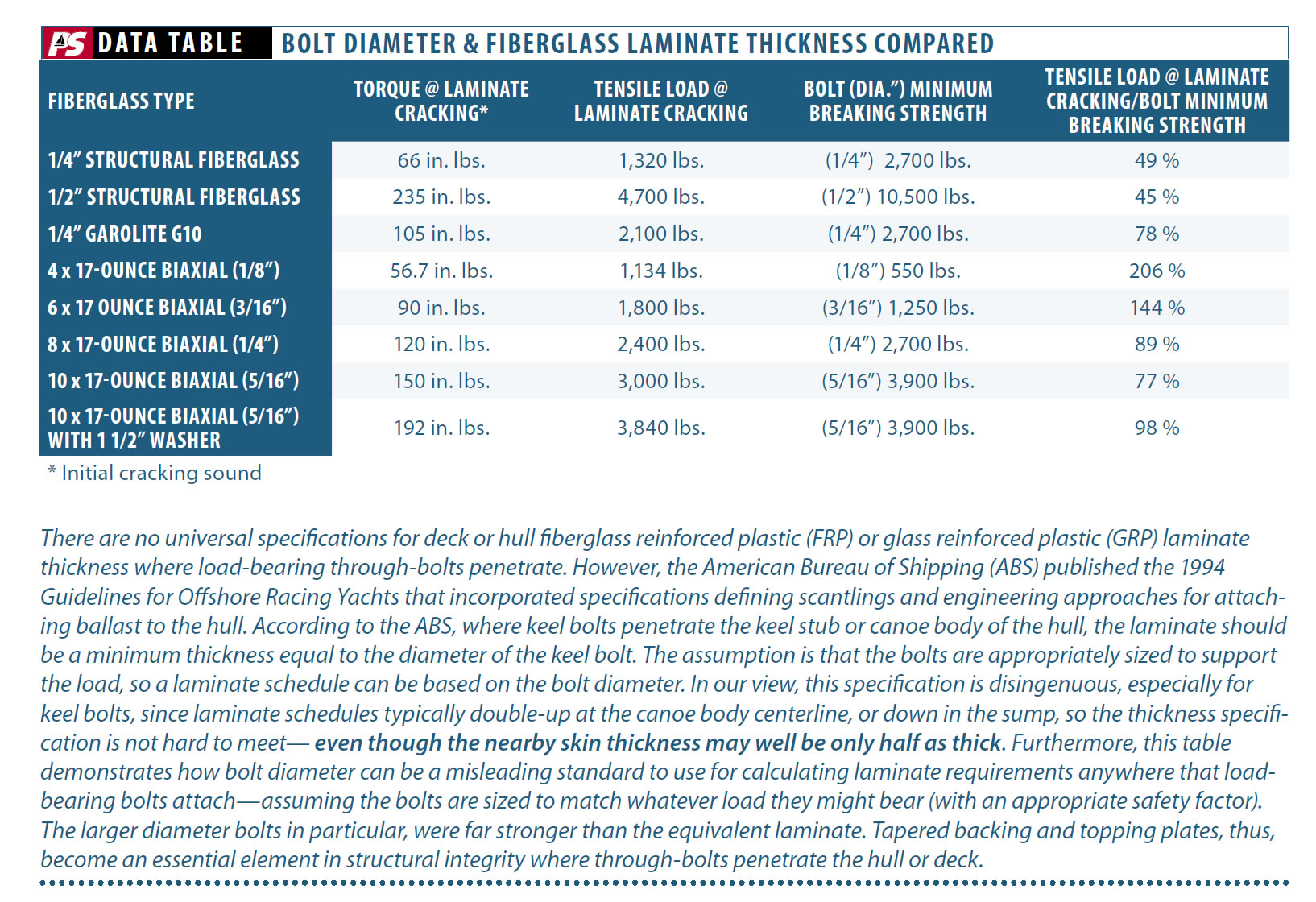