Fouling is simply the growth of water-dwelling critters on your boat’s bottom, resulting in higher skin friction and a decrease in a boat’s speed and fuel economy. This growth can be soft (slime, grasses or seaweed) or hard (barnacles, mussels and other hard-shell organisms). They’re all unwelcome to the boat owner.
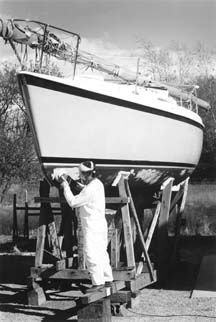
More than 2,000 species of plants and animals have been identified clinging to boat bottoms, from microscopic bacteria up to 3-foot long remora fish. All told, 13 of the 17 general classes of animal life that biologists call phyla are known to contribute to fouling.
Until recently, most hard growth was restricted to a saltwater environment (although we’ve been told that Lake Titicaca, in the Andes, has severe fouling problems). Since the inadvertent importation of zebra mussels to domestic waterways, however, the problem of hull fouling is becoming a serious concern of freshwater boat owners, too.
Keelhauling may be a thing of the past, but a foul bottom remains a source of punishment for boatowners. The toll that marine growth can take on a boat’s performance is considerable: a navy destroyer, after only six months in temperate waters, suffers a 50% increase in fuel consumption at 10 knots. A badly fouled hull can reduce the top speed attainable of a planing hull by two-thirds.
Removing this growth is also a punishing procedure; they’re bonded with a virtually unbreakable grip. In fact, the US Navy is studying the exact mechanism of attachment in hopes of developing a better adhesive for underwater use.
A Brief History
Fouling is by no means a new problem. It was reported back in 500 BC (well before any Y1K problems), and reference was made to attempts at applying antifouling of some sort, though no details of the treatment used are available. By 400 AD, a number of approaches had been tried, including cladding the hull with sheets of copper or lead, or using poisons such as sulfur and arsenic mixed with tar or wax. The same concept of coating the boat’s bottom with a material that dissolves slowly and releases a toxic coating or biocide is still the basis for almost all antifouling treatments in use today.
By the mid-18th century, the problem had been basically solved. Copper sheets fastened to a ship’s wood planking (with copper nails) had become the standard way to deal with the antifouling problem. This method worked well, minimizing growth and obviating the need for frequent hauling and scraping. It stayed in widespread use for about a century, until iron ships replaced wooden ones.
At that time, little was known about the galvanic corrosion that occurs when dissimilar metals, in contact with each other, are submerged in a liquid that, like sea water, conducts electricity. It didn’t take long to remedy that ignorance: Ships that sank because of hull failure were effective educational tools. When copper is connected to iron or steel and the whole thing is immersed in saltwater, it is the iron or steel that’s attacked, not the copper.
In 1847, the British navy was seriously considering switching back to wooden ships; at about the same time, the US Navy was experimenting with giving their iron ships a wood overcoat, to which copper sheets could be nailed. But the advantages of iron ships were too great to give up, so more practical approaches were developed involving biocides mixed with paints for applying directly to steel hulls.
Over the next century, just about any toxic material that could be mixed into a coating was evaluated for its antifouling properties. Salts of mercury, arsenic and lead were tried, but the toxicity problems they presented to the humans who applied them (and had to remove them from time to time) proscribed their use. Copper and copper salts were also tried, and became more or less standard, despite often marginal effectiveness, a limited range of obtainable paint colors, high material costs, and the necessity of launching the ship immediately after painting in order to prevent the air from deactivating the biocide.
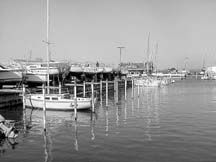
The introduction in 1960 of tributyl tin as a biocide appeared to solve all the problems. Paints with TBT appeared (at least, for a while) to provide the ideal answer to fouled hulls. The tin-based compound could be dissolved directly in the film-forming paint rather than being dispersed as an insoluble powder. The resulting paints were not only excellent antifouling coatings, but were colorless, permitting for the first time the introduction of bright-colored bottom paints. These paints didn’t have to be loaded with heavy metallic dust, and therefore were easier to apply. Tin-based paints also could be applied months before launching, and could provide multi-year protection even when the boat was hauled at the end of the season. By the end of the 1960’s, TBT paints dominated the field.
Something Happened
The joy, however, didn’t last long. By 1980 some unsettling reports began to surface concerning the damage that TBT-based paints could do to the marine environment. TBT was not only effective in killing growth on the bottom of a boat, but it was doing the same thing to fish and shellfish in the surrounding waters. It’s very difficult to create a “non-toxic biocide.” And when that biocide is expected to control the huge variety of organisms that contribute to fouling, the task isn’t just difficult; it’s nearly impossible.
One might think that any toxicity problem would be trivial, in light of the vast quantity of water on the planet, but as a point of fact, almost all the marine life in the oceans exists in coastal waters—a much smaller volume. These coastal waters are, of course, where the vast bulk of recreational boating takes place. The more boats that had tin-based compounds on their bottoms, and the smaller the area in which these boats congregated (marinas and anchorages), the worse the problem became.
Led by California, several states banned the use of TBT. In June of 1988, the federal Environmental Protection Agency announced a national ban on TBT-containing paints, taking effect in 1989 (there’s an exception for aluminum-hulled boats, which can’t tolerate copper-containing paints). Antifouling technology took a giant step backwards.
At the same time, other environmental considerations came into play. The Clean Air Act of 1990 severely limited the amount of solvents (the EPA calls them VOCs or volatile organic compounds) that can be released into the atmosphere, as well as many of the unpleasant and often toxic airborne by-products (dusts, vapors released from cleaning chemicals, etc.) associated with painting a hull. The Clean Water Act requires collection and proper disposal of non-airborne pollutants (chipped paint, sludge from chemical cleaning, excess cleaning chemicals, etc.) to keep them from finding their way into the water.
Back A Step, Forward A Step
The first bunch of post-TBT paints we tried were, frankly, not too good. Their performance was markedly inferior to the tin-containing paints they replaced.
Formulations have been improving, though, and excellent antifouling performance, generally for more than one season, is becoming the norm rather than the rare exception. Manufacturers are developing new technologies for their antifouling arsenal, and it seems like a good bet that the next round of regulation (and there’s sure to be one) will find the industry better prepared than it was in 1989.
In “traditional” antifouling paints, a biocide such as copper or copper oxide powder, is dispersed in a vehicle that “dries” by combining with oxygen in the air. To keep the mixture’s viscosity down to workable levels, solvents, which evaporate before the oxidizing cure begins, are added. Copper loadings vary from 45% to 75%, and while advertisers makes a great fuss about how much copper their products contain, we haven’t found that the concentration of copper necessarily correlates with antifouling effectiveness. Products of this type are generally described as alkyd, oil, modified epoxy or hard epoxy finishes, with no very clear dividing lines. More recently, water-based (or “thinned”) paints have begun to proliferate. The vehicle in these paints is still an oil-based resin, but is in the form of droplets suspended in water. After application, the water evaporates, the droplets of resin coalesce and the paint dries in a conventional manner. The greatest advantages of water-based paints are easier clean-up, and lowered air pollution due to reduced VOCs. Once dried, they’re as waterproof as oil or solvent-thinned paints.
Some bottom coatings, primarily the vinyl bottom paints, dry by simple solvent evaporation and do not require a reaction to oxygen. These lacquer-type coatings are less popular as bottom paints because it’s difficult to formulate a high solids lacquer without giving it a high viscosity that’s difficult to apply. Low solids coatings require more coats for any given build-up, and release more VOCs into the atmosphere. There are several other vehicles that don’t rely on oxidation or simple evaporation to form a solid film—two-part epoxies and vinylesters that don’t require atmospheric oxygen for curing. There also are water-cured resins that react with water vapor in the air to achieve a cure. These and others have been tried with varying degrees of success.
Another way of classifying bottom paints is by how readily the exposed surface of the coating is attacked by water. One popular type is referred to as sloughing, ablative or sometimes co-polymer. With these paints, the resin slowly dissolves in sea water. The outermost surface continually erodes, much like a bar of soap, so that it constantly exposes a fresh surface.
In the past, these soluble coatings were quite soft; newer ones, however, can be quite hard. In theory, at least, they have several advantages: They maintain a fairly constant release rate as long as there’s any coating left, and they’re relatively immune to surface oxidation if the boat is taken out of the water. Any changes are simply washed off when the boat is put back in service. These coatings tend to be expensive and less abrasion-resistant than the non-soluble type (if you scrub your bottom frequently to minimize slime you’re apt to remove the paint).
Non-soluble paints behave more like a sponge packed with copper particles. Water slowly diffuses through the insoluble film, dissolving particles of biocide, which then diffuses out to the surface. Non-soluble bottom paints usually require higher loadings of biocides than soluble coatings. On the upside, they’re generally more abrasion-resistant and less expensive.
Two-part paints (the only ones that we found in current production are epoxies, although polyester and vinylesters have been made with some degree of success) fall into the non-soluble class. The resins used have fairly low viscosity until they cure, and it’s possible to formulate 100% solids coatings. They don’t appear to be effective in preventing soft growth, but they last a long time (manufacturers claim about 10 years) and only require buffing with a Scotch-Brite pad before being put back into the water.
What Does The Work
By far the most commonly used biocides are metallic copper and copper oxide. There are, however, some others. Interlux uses a copper compound called copper thiocyanate in its Trilux and we’ve seen some paints in the past that used zinc oxide. “Natural” products such as cayenne pepper also have been tried, but seem to be off the market at present. The most recent trend is to incorporate an anti-slime agent in the paint to combat soft growth.
Another completely different approach is to attempt to make the hull too slippery for growth to adhere. We’ve seen excellent results from Interlux’s Veridian, a silicone rubber coating that is both effective and horribly expensive.
Some less-expensive “bio-release” products are beginning to appear. It’s quite possible that bio-releases will be the choice of the not-too-distant future. Sweden reportedly has already banned copper-containing products; can California and Washington can be far behind?
The PS Tests
As it has been for nine years, our testing was straightforward. In earlier years, we painted stripes of bottom paint on a test boat and coated keels and portions of the hulls of a fleet of Cape Cod Mercurys.
In recent years, we purchased polyester/fiberglass sheets and cut them into panels measuring 1-1/2′ by 6″. Each panel is coded with a binary code (remember the new math?) of large and small holes (painted-on identification has a bad habit of disappearing). The panels are then washed with a de-waxing solvent, sanded lightly with a fine-grit sandpaper, and washed again with solvent to remove any wax or release agent that may have been present. If a paint’s instructions called for a special pre-treatment, those instructions were followed. We then apply each product, also following label instructions for drying time and number of coats. Only one side of each panel is coated; the other side acts as a control.

Last spring, we mounted one set of panels on our raft, the Foulbottom II, which majestically rides the waves of Long Island Sound, just off Greenwich, Connecticut. These panels were in their second year of exposure, having also been exposed during the summer of 1998. Many of these same paints had been tested for three years, beginning in 1995. Unfortunately, the Foulbottom I broke its mooring chain and all panels were lost, forcing us to start over. In multiple season tests, the panels are removed in the fall, stored, prepped the next spring according to manufacturer’s instructions, and resubmerged.
A second set of panels was sent to the North Star Sail Club on Lake St. Clair, Michigan, for immersion in a freshwater environment that’s been a host to zebra mussel infestation. Our thanks to club member Robert Bethune for his assistance. These were first year panels.
A third set was prepared for Florida, but due to logistical problems they can’t be included in this report.
The actual test consisted of leaving the panels in the water until the season ended. The panels were spot-checked every few weeks to identify any really dramatic growth. In the fall, they were pulled out and closely examined.
The Results
A dizzying series of mergers and acquisitions over the past few years resulted in several paints from past years’ tests vanishing from the market. Nautical Paints acquired Rule, Interlux acquired Nautical Paints and Azko Nobel acquired Interlux.
The chart on page 8 summarizes the performance of the remaining 37 test paints, based mostly on soft growth.
This season, for whatever reasons, our usually barnacle-rich waters off Greenwich had a drought of hard growth. Where we normally see heavy concentrations of barnacles on hull bottoms and on our panels, this year there were virtually none. And, perhaps coincidentally, Lake St. Clair had a failure in its zebra mussel crop. Luckily, almost all the Connecticut samples were in their second year of exposure, while all the freshwater samples were in their first year.
In the chart, products are listed in groups based on their resistance to soft-growth fouling in saltwater, but within groups by freshwater performance. Generally saltwater and freshwater performance was comparable, although there were a few dramatic differences. Super Fiberglass Bottom Kote, which was Very Good in saltwater, was Poor in freshwater. Trilux II, which rated Poor in saltwater was rated Good in freshwater. Micron Optima, which was outstanding in its first year of saltwater exposure, was also outstanding in its first year of freshwater immersion; it dropped from Excellent to Very Good in its second year in Long Island Sound.
The top five paints include Interlux Veridian, that must be professionally applied by a yard, and Micron Optima that has not yet been approved for sale in the US. Among the three paints available over the counter in most stores, Pettit Trinidad SR rated tops—Very Good in both saltwater and freshwater. As we reported last year, Trinidad now has a specially formulated additive called Irgarol, developed by Ciba. In earlier tests, before Irgarol was added, it has always ranked high, but generally a half notch below a few others, including Pettit ACP 50, which this year fell into the second tier. The remaining two are Micron CSC Extra and Super Fiberglass Bottom Kote, both by Interlux. Interestingly, the Micron CSC Extra also has an additive, Biolux, as do Interlux Trilux and Ultra.
It would appear that these anti-slime agents are indeed effective. What we won’t know, at least until the barnacles return, is how effective Biolux is against hard growth. In the summer 1998 test, Trinidad SR with Irgarol, which has been around longer, was rated Excellent for hard growth.
Conclusion
Lastly, because fouling organisms vary geographically, paints that perform well in one location may perform slightly better or worse 20 miles up or down the coast. Unless you keep your boat in one of our test locations, the results of our tests, therefore, should not be taken as a guarantee of performance in your area.
Contacts- American Marine Coatings, 1445 Northlake Way #B, Seattle, WA 998103; 800/290-8836. Flexdel Corp., 1969 Rutgers University Blvd., Lakewood, NJ 08701; 732/901-7771. Interlux Yacht Finishes, 2270 Morris Ave., Union, NJ 07083; 800-INTRLUX. Nautical Paint Industries, 2270 Morris Ave., Union, NJ 07083; 800-INTRLUX. Pettit Paint Co., 36 Pine St., Rockaway, NJ 07866; 800/221-4466. Rappahannock Coatings, 1200 George Wood Dr., Elizabeth City, NC 27907; 252/335-5797. West Marine, PO Box 50070, Watsonville, CA 95077-0070; 800/262-8464. U.S. Paint, 831 South 21st St., St Louis, MO 63103; 314/621-0525. Woolsey/Z-Spar Marine Paint, 36 Pine St., Rockaway, NJ 07866; 800/221-4466.