Practical Sailor has been testing bottom paints for 10 years now, though it sometimes seems like forever. It’s been a lot of work, but from reader reactions, the findings appear valuable enough to make the effort worthwhile.
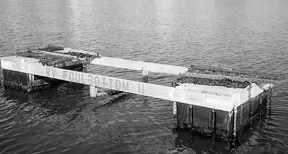
The industry’s recent pattern of mergers and acquisitions has reduced the number of major players in the marine paint field to essentially three: Kop-Coat owns Woolsey and Pettit; Azko Nobel owns Interlux, which sells the Interlux, VC, Nautical Paints, and Gloucester brands; and U.S. Paint, which owns its own line of products.
The major catalog suppliers sell paints made by one or more of these three. This hasn’t done much to reduce the number of labels or product names out there, but it has caused some name changes in product labels: Tarr & Wonson now goes under the Gloucester brand name; Gloucester Super KL is now Nautical Super KL and so forth. We’ve attempted to adjust the product names in our chart to keep up with these changes. At least one company, Rappahannock Coatings, seems to have vanished; we were unable to reach them by either telephone or e-mail. As a result, we’re dropping their four products—Rappoxy B, Rappoxy 45 Rappoxy 60 and Rappoxy 75—from the listing.
A Brief History of Bottom Paint
An antifouling paint (or treatment, to be precise, as some of the approaches aren’t really paints) is simply a product or process that eliminates or minimizes animal and vegetable growth on a boat’s hull. A wide variety of organisms like to attach themselves to the underside of a boat: More than 2,000 different species of such plants and animals have been identified.
Vegetable growth—slime, grasses and seaweed—can be characterized as “soft” growth, while animal growth—barnacles, mussels and the like—is generally “hard,” since most of the critters involved have shells. Hard growth is more difficult to remove, but both hard and soft growth can take a heavy toll on a boat’s performance and fuel economy.
As in years past, we’ll look at some of the efforts sailors have made to combat the attachment of unwanted life forms to their hulls.
The battle is an old one: As long as 2,500 years ago people were writing about the fouling nemesis. The following millenium saw several approaches that had at least partial success, including the application of copper sheets to the hull and coating the hull with a mixture of wax or tar and a poisonous material such as arsenic or sulfur.
By the mid-18th century, sheets of copper fastened to a wooden hull with copper nails had become a standard way of protecting a hull against undesired growth. This system worked well enough so that it might have been continued up to today if iron ships hadn’t come along to replace wooden ones. Copper cladding doesn’t work too well with iron ships; if you have a piece of copper in contact with an iron structure and expose both to saltwater, you get a battery. The flow of electric current from this battery removes iron from the structure and tries to deposit it upon the copper. Result? A sunken ship. The problem was so serious that the US Navy considered cladding their iron ships with wood so that copper could be applied. The British Royal Navy considered ditching iron ships altogether and going back to wood.
Over the next hundred years, experimentation progressed at a rapid rate. In an attempt to improve anti-fouling efficacy, arsenic, mercury, lead and copper were mixed into almost any liquid that would dry to form a film. Several of these worked well, but had the unfortunate side effect of poisoning the workers who manufactured, applied and removed them. Paints containing metallic copper powder and/or copper salts (copper oxide was popular) became standard, and did a reasonable job of discouraging growth without taking too high a toll on the people who handled them.
In 1960, a tin compound—tributyl tin or TBT—was introduced, and it looked like fouling problems were finally conquered. Paints with TBT, while not completely innocuous to humans, could be produced and applied with an acceptably low level of risk. TBT was soluble in paints, so that the paint didn’t have to be loaded with heavy, insoluble copper compounds that required constant mixing. TBT is colorless, so that bottom paint could be produced in any color, And a TBT-containing paint didn’t oxidize in the air, so that it was possible to paint the vessel months before launching, and to haul the boat and return it to the water without the necessity of repainting.
The bubble burst about 1980. Reports began to surface indicating that TBT was killing fish and shellfish. Many people found this difficult to believe, considering the relatively small amount of TBT that was used and the huge amount of water in the seas. The logic here is flawed, though: almost all of the marine organisms in the sea grow in coastal waters, which account for a very small percentage of the seas’ volume. And coastal waters are where the vast preponderance of recreational boating takes place.
California, followed by several other states, banned the use of TBT starting in the middle 1980s. And in 1988, the federal Environmental Protection Agency (EPA) announced a ban on virtually all TBT-containing paints. The only exceptions were for paints intended for aluminum-hulled boats and (on a smaller scale) for paints intended for aluminum outdrives and the like. This was because aluminum cannot tolerate copper-based paints.
Based on our test experience, the first paints released after the TBT ban weren’t very good. In recent years, however, the industry has progressed considerably, and nearly all paints we’ve tested will last at least one full season. We’ve found some very good multi-year products, and we suspect that when the next round of regulation comes up, paint manufacturers will be in a much sounder position than they were in 1989.
How Bottom Paints Work
A “traditional” bottom paint consists of either metallic copper powder or copper oxide mixed into a film-forming vehicle. This film is either somewhat permeable to water, allowing the water to penetrate it and reach the copper, or it’s somewhat soluble in water, with its outer layer washing off in time to expose a fresh layer of copper. This latter type is described as “sloughing” or “ablative” or sometimes a “co-polymer” bottom paint. The first type includes “hard epoxy,” “modified epoxy,” “oil” and “alkyd” paints. Both sloughing and non-sloughing bottom paints are available in water-based (more precisely, water-thinned) forms.
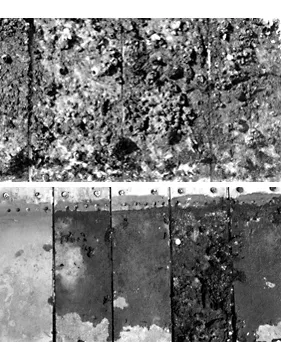
A bottom paint typically contains between 45% and 77% copper, and manufacturers make a big advertising point about how much copper their products contain. Our tests, however, haven’t shown any firm relationship between copper content and effectiveness.
There are a few alternative approaches. One is to mix the copper into a two-part epoxy or polyester resin; we refer to these as copper-loaded gelcoats. They don’t contain solvents, which allows them to sidestep EPA’s regulations on introduction of solvents (volatile organic compounds or VOCs); when mixed, the product polymerizes to become a solid. These “gelcoats” are effectively non-soluble. They tend to last for a long time (manufacturers claim 10 years) and feature very low rates of copper leaching into the water. They don’t seem to be effective on soft growth, but whatever hard growth occurs seems to be easy to remove.
Another possible approach is to provide a bio-release coating to the hull—essentially one that is so slippery that growth simply cannot adhere, or at least won’t adhere firmly. In theory, at least, the movement of water against the hull should then simply wash off any growth. In recent years’ tests, Interlux’s Veridian has worked well, but has been prohibitively expensive. This past year we added a new, lower-cost version of Veridian that’s user-applied (the older version was supplied for dealer application only), as well as a low-cost coating called Bye Bye Barnacle.
Over the years, we’ve tested paints with non-copper antifoulants, including cayenne pepper and zinc oxide. Neither of these appear to be on the market at this time. We had a brief flurry of interest in the use of zinc oxide-containing baby creams as a low-cost antifouling treatment. It seemed that they work but don’t remain on the hull long enough to be practical.
The Tests
Because bottom paints have improved over the past decade, we’re becoming more demanding in our tests. Where a paint that showed no hard growth in one season was considered to be excellent 10 years ago, we’re now considering that to be the norm, and are looking for multi-year performance to achieve a high rating. And where we started out basing our ratings only on the prevention of hard growth, we’re now considering prevention of soft growth to be an important rating factor as well.
The testing method hasn’t changed in recent years. It’s simple and, we feel, realistic. We take polyester/fiberglass panels measuring 12″ x 18″, wash them with a de-waxing solvent, sand them lightly with a fine-grit sandpaper, and wash them again with solvent to remove any traces of wax or mold-release agent. We then apply the bottom paint, following the instructions supplied with each paint. If a paint’s instructions call for a special pre-treatment, that’s what is done. Label instructions for drying time andnumber of coats required are followed. One side of each panel is coated; the other side acts as a control.
Panels are identified by drilling a pattern of holes (painting numbers isn’t a durable marking system) representing a designation in binary code. The system also keeps us impartial, because we don’t refer to the codes until after we’ve evaluated the panels.
The panels are bolted to angle iron racks, which are in turn bolted to our test raft, Foulbottom II. (Our original raft, Foulbottom, broke free from its moorings in a storm and was lost at sea with all panels aboard.)
Test Results
Our findings are summarized in the chart at left. We’d like to be able to draw some generic conclusions from the chart, but the data simply won’t cooperate. Performance doesn’t seem to be related to copper content, to whether the paint is sloughing (ablative, co-polymer) or non-sloughing (hard, modified epoxy), or to whether it’s water-thinned or solvent-thinned. And while some of the best performers are among the most expensive, price doesn’t seem to be an accurate predictor, either.
All of the paints tested performed well in resisting hard growth. This past year was a much better (or much worse, depending upon your point of view) year for barnacles than the previous year. The reverse sides of the panels were liberally coated with hard-shelled critters. With few exceptions, the treated side of each panel was completely free of hard growth, earning a score of Excellent in this category. Even the products that were judged less than Excellent—VC Offshore, VC 17 and Neptune—were rated Very Good, with only one or two barnacles per panel.
Results in resisting soft growth were not as impressive. Most were rated as Good, with a thin film of slime coating their entire treated surface. None was totally free of soft growth, but Micron Optima, Trinidad SR, ACP 50 and both varieties of Veridian—the professionally applied version and newer one intended for do-it-yourself types—were close. These five earned a Very Good rating for soft growth resistance.
Copperpoxy, the only example of a copper-filled gelcoat that we tested this time was only fair in dealing with soft growth; it proved easier to clean than did the several other paints which were also rated Fair.
Conclusions/Recommendations
The chart speaks for itself. Micron Optima, a two-part product that’s still not available in the US but is supposed to be available this summer, is best at preventing both soft and hard growth. But it has drawbacks. Once mixed, Optima has a short pot-life, so that any leftover mixture will harden before you can use it for a next coat. And the packaging we’ve seen makes it difficult to mix up less than a full quart of product. Interlux has yet to annouce a US price.
Hence, there are good and valid reasons to consider the three products that rank slightly behind Optima. Trinidad SR, Micron CSC Extra and ACP Ultima are single-component paints and, as such, are much more convenient to apply. All three earned a Very Good Rating for preventing soft growth—almost as good as Micron Optima—and were Excellent with regard to hard growth. Any of the four should do a fine job of keeping your hull clean.
We’re not sure what new environmental regulations will be forthcoming over the next few years, but we’re pretty sure that there will be some. Several European countries have already banned copper-containing paints (can California be far behind?), and there’s been talk of banning sloughing paints in general. One thing’s sure: When new products emerge, Practical Sailor will test them.
Contacts- American Marine Coatings, 1445 Northlake Way, Seattle, WA 98103; 800/290-8836. Flexdel Corp., 1969 Rutgers University Blvd., Lakewood, NJ 08701; 732/901-7771. Bye Bye Barnacles, United Energy Corp., 600 Meadowlands Parkway, #20, Secaucus, NJ 07094; 800/327-3456. Interlux Yacht Finishes, 2270 Morris Ave., Union, NJ 07083; 908/686-1300 Nautical Paint Industries, 270 Morris Ave., Union, NJ 07083; 908/686-1300. Pettit Paint Co., 36 Pine St., Rockaway, NJ 07866; 800/221-4466. U.S. Paint, 831 South 21st St., St Louis, MO 63103; 314/621-0525. West Marine, PO Box 50070, Watsonville, CA 95077-0070; 800/262/8464. Woolsey/Z-Spar Marine Paint, 36 Pine St., Rockaway, NJ 07866; 800/221-4466.
Also With This Article
Click here to view Value Guide: Bottom Paints.
Would you know if Copperpoxy is still available? Your evaluation of it doesn’t rate hard growth which I understand to be very good for multiple years. Soft growth can be easily removed without pulling the boat out of the water. I’ve read that it is no longer available from a very old online article, to finding a website for it that’s still being maintained. They haven’t replied to my email yet and it hasn’t bounced. I’m having a hard time finding this product.