Ever since we arrived in the tropics more than three years ago, maintaining Calypso’s vast quantities of varnished teak has been an exercise in frustration. We have gone through the seemingly endless cycle of sanding, varnishing, sanding, and varnishing again with mind-numbing regularity. Most heartbreakingly, we have seen many coats of varnish on our caprail seemingly vanish overnight during offshore passages. In just over four years since her launch, the rail has been stripped to bare wood three times, as the old finish had deteriorated to the point where it was easier to start over than to try to rescue what little remained intact.
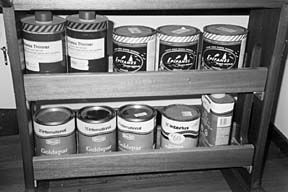
Last year, before leaving New Zealand, we determined to reclaim our peeling brightwork, and vowed to keep it looking good. This is a tall order, given the amount of varnish we have.
After four years of using Epifanes varnish on most of our exterior teak, we were ready for a change. While Epifanes gives a beautiful finish when fresh, we simply felt we were not getting the longevity we should for the number of coats applied. We also found it tricky to get the varnish to the right consistency for good brushing and self-leveling properties.
In New Zealand, we saw a beautiful Herreshoff-designed ketch with flawless varnish. Her owner used International (Interlux, in the US) Goldspar, a varnish new to us. Annoyingly, International has different names for its finishes in different countries, making it difficult to cross-reference products, especially since US-made products generally carry much more detailed labeling of ingredients than overseas products.
After reading the label on Goldspar, we knew no more about its chemical composition than we did when we started. It was only after perusing in detail all the International product information we could find that we suspected Goldspar might be a polyurethane-modified tung oil varnish. This was finally confirmed when we got our new West Marine catalog, which stated that Goldspar (now with the same name in the US as elsewhere in the world) is what used to be called Interlux Clipper Clear.
We used Clipper a few years ago on our cockpit table, thinking that a urethane might hold up better under the hard use a table gets. In fact, the Clipper held up astonishingly well on the cockpit table, retaining good gloss after almost three years. Admittedly, the table is generally protected from the sun, the big killer of any clear finish.
Before leaving New Zealand, we stripped the railcap and applied six coats of Goldspar. International recommends a minimum of five coats on exterior work, but we feel that manufacturers generally skimp on the number of coats required, perhaps to spare the boatowner the shock of realizing just how much labor is really involved in maintaining brightwork.
Our traveling schedule from New Zealand—about 6,500 miles in seven months—left us little time to maintain the varnish. We did manage to strip and refinish the cockpit coamings and several of the hatch coamings in Australia, but the rail was left to its own devices—and its six coats of Goldspar—until we got to Thailand.
We watched nervously for signs of deterioration along the way, as we traveled from 37° south latitude to 8° north. Through the broiling sun of the Tasman Sea, the Coral Sea, the Sea of Arafura, the Java Sea, the South China Sea, the Straits of Malacca, and the Andaman Sea, our six meager coats of Goldspar shone, and shone, and shone.
When we fetched up in Thailand, we were finally in one place long enough to give the rail some attention. In a few spots, the varnish had chafed through to the bare wood from the inevitable sailing dings, but the rest of the varnish film was completely intact, retained its high gloss, and showed no sign of surface crazing. When sanded, it still showed the life and resiliency that indicates a sound finish.
We touched up the dings with several coats, sanded the rail thoroughly, and applied two fresh coats of Goldspar, adding only a touch of Interlux 333 Brushing Liquid to improve flow in the hot, humid climate of Thailand. With eight coats, the grain of the rail is starting to fill nicely. Completely filled grain enhances gloss and increases longevity by providing a thicker surface film, and giving a smoother surface that doesn’t trap abrasive dirt and grit.
A plus with Goldspar is that it does not change consistency in a partially used, well-sealed can. The last bit of varnish in the can handles just the same as the varnish in a newly opened can, making consistent results easier.
In fairness, we have changed varnishing techniques as well. We have gone back to using nothing but badger hair brushes, which apply a thicker, more even coat than any other type of brush. We still use throw-away foam brushes for touching up dings.
As a control, we are stripping the finish from two identical teak Dorade boxes. The boxes are located side-by-side on the main deck, and were constructed from a single piece of teak with matched grain. They receive identical exposure to the weather. We will finish one box using a Goldspar system, the other with Epifanes. That’s as close to a laboratory test as you can get on a cruising sailboat.
In the can, Goldspar does not appear to be absolutely identical to Clipper. Our one remaining can of Clipper, now four years old, is decidedly more transparent in the can than the new Goldspar, which has almost a purple cast. On the wood, you can’t really see a difference.
Our first experience with the “new” Goldspar has left us very impressed. After almost eight months of exposure to blistering tropical sun, the finish on the rail literally looked as good as the day it was applied. Ironically, of course, that’s the best time to apply more varnish—while it still looks like new!
The one drawback we have found with Goldspar—as with all high-quality, oil-based varnishes—is that it is relatively slow-drying for purposes of sanding and recoating. The surface sets up quickly enough to resist dust and water, but remains soft for days. We have found it necessary to wait a minimum of three days after a full, unthinned coat of varnish for the surface to get hard enough to sand reasonably easily. This slows down buildup coats on new work.
You can “hot coat” with Goldspar (applying a second coat over a first without sanding before the surface cures) but overcoating without sanding simply amplifies surface flaws and forever traps dust from the previous coat.
So far, we are extremely pleased with Goldspar. It is no magic bullet for brightwork. A good-looking clear wood finish still takes an inordinate amount of work, but we are encouraged to find that we can, at last, keep up with the brightwork without investing every spare moment in the discouragingly repetitive work that is varnishing.
What a price we pay for the vanity of gleaming varnished teak! But it definitely keeps us off the streets and out of trouble. You may find other cruisers lounging around in the cockpit with a cold beer, but you’re more likely to find us with a piece of sandpaper and a tack rag.
Our next boat, I promise you, will have not a single speck of exterior wood of any type. In the meantime, we’re probably one of the few cruising boats around with custom racks under the dining table—varnished, of course—to hold the dozen or so cans of varnishes and their associated thinners that are an essential part of our cruising kit.
Contact- Courtalds Coatings, 2270 Morris Ave., Union, NJ 07083; 908/686-1300.