Just weeks ago, a fellow Corsair 24 owner dismasted due to a seizing wire failure. More than once I’ve had stainless seizing wire fail while twisting it up, and more than once I’ve found cracked wires during inspections. I switched to monel wire 15 years ago and haven’t had a failure since.
Stainless is good stuff for many marine applications, but it does have its weaknesses. It is prone to work hardening and fatigue. It is vulnerable to crevice corrosion, particularly if bent. Bent rigging toggles are notorious for cracking at the bend. I replaced several forestay toggles on my Stiletto 27; each cracked in the same place, each as an incipient crack before failure. Monel wire, common in U.K. chandleries but not in the U.S., has advantages. West Marine use to carry it, but it is more expensive and was replaced with stainless some years ago.
Monel 400, the alloy most often used in marine applications, is 28 to 34 percent copper, more than 63 percent nickel, with minor amounts of carbon, iron, manganese and silicon. Aluminum and titanium incorporated in some alloys to increase strength. It has the same tensile strength as 316 stainless steel, about 550 megapascals (MPa). Monel has a somewhat duller appearance because it has no chromium. It contains no iron and thus is completely non-magnetic, as compared to slightly magnetic 304 stainless and weakly magnetic 316 stainless. It can also be identified by being completely non-sparking on a grinder. The advantages of monel for seizing wire are that it is far more ductile than 316 stainless, bending farther and more cycles without breaking. It is far more resistant to stress cracking in a saltwater environment. I’ve seen stainless seizing wire crack if over twisted, and sometimes after long exposure to seawater, but I’ve never seen this happen with monel wire. Disadvantages of monel include cost (about double 316 stainless wire and pop rivets, and much more for machine screws), availability and some difficulty in machining.
SEIZING WIRE
Diameter ranges from 0.02 to 0.04 inches, with 0.03 to 0.04 inches being most common. Use a size that will fit two to three passes through the pin hole. The wire should be carefully pulled around each wrap and snugged after each pass, before the twisting begins. If the twisting is used to pull the wire snug, the strain in the twists will be excessive and the wire will crack. The cracks may be invisible, but they’re enough to give seawater corrosion and stress cracking a place to get started. Instead, the twist should only serve to hold the ends together. Then clip the ends off about ⅜-in. long and tuck out of the way to avoid snags. Some like to tape the seizing, but this excludes oxygen and rainwater rinsing, blocks inspection and should not be needed if the tail is carefully buried.
Step 1. Run the wire through the pin and the shackle loop.
Step 2. Repeat the wrap through the pin and the shackle loop. Each pass should be pulled through and neatened with your fingers before beginning the next pass. 2-3 passes are required. Do NOT use the twisting motion of the pliers to pull the turns snug. This will only result in cracked the wire.
Step 3. Twist the wire ends together. You should be able to do the twist with your fingers and only a light finishing touch with pliers. The twist is ONLY to secure the ends. I’ve never seen a wire seizing untwist, but I have seen many with cracked wires from over twisting. Instead of covering with tape, which restricts oxygen and reduces rainwater rinsing, take a few extra moments to neatly trim and bury the end.
Malin 316L Stainless $20 0.020” 980 feet Monel $39 0.019” 200 feet Ormiston Monel $20 0.035” 30 feet McMaster Carr Monel $33 0.032” 81 feet Recommended $34 0.020” 225 feet 316L Stainless $16 0.036” 70 feet $22 0.020” 232 feet West Marine Monel (discontinued ~ 2010) ? 0.032 80 feet What we use 316 Stainless (Loos) $26 0.042 55 feet Fishing supply houses sell monel wire for for trolling and rigging baits. It is often sold by test strength instead of diameter. Test (pounds) Diameter (inches) 30 0.020 60 0.029 100 0.035
Threadlocker (or another thread locker) is another option. Locktite blue is medium strength, allowing removal with just a little extra umph on the wrench. Locktite red is higher strength and a torch is often required. We know of some smart people that have started using Locktite red instead of seizing wire. They feel it is more reliable. Sometimes they grind the heads off anchor shackle to reduce hang-ups on the bow roller side places during recovery. They aren’t averse to cutting off the shackle when needed; it’s probably time anyway.
We do not advise use Locktite on rigging screws (turnbuckles). They are prone to galling and seizing, and only an appropriate high-pressure grease or anti-seize agent should be used.
We do like Locktite blue for applications where seizing wire is impossible and when double nuts aren’t an option, such as spars and rigging where screws have worked loose before, for example if the threads are slightly worn but not stripped. It makes disassembly a little more challenging, but it also has some anti-seize properties, so it will be better than something put together dry.
You can also use Locktite blue for through bolts, locknuts and insert locking nuts.
BLIND RIVETS
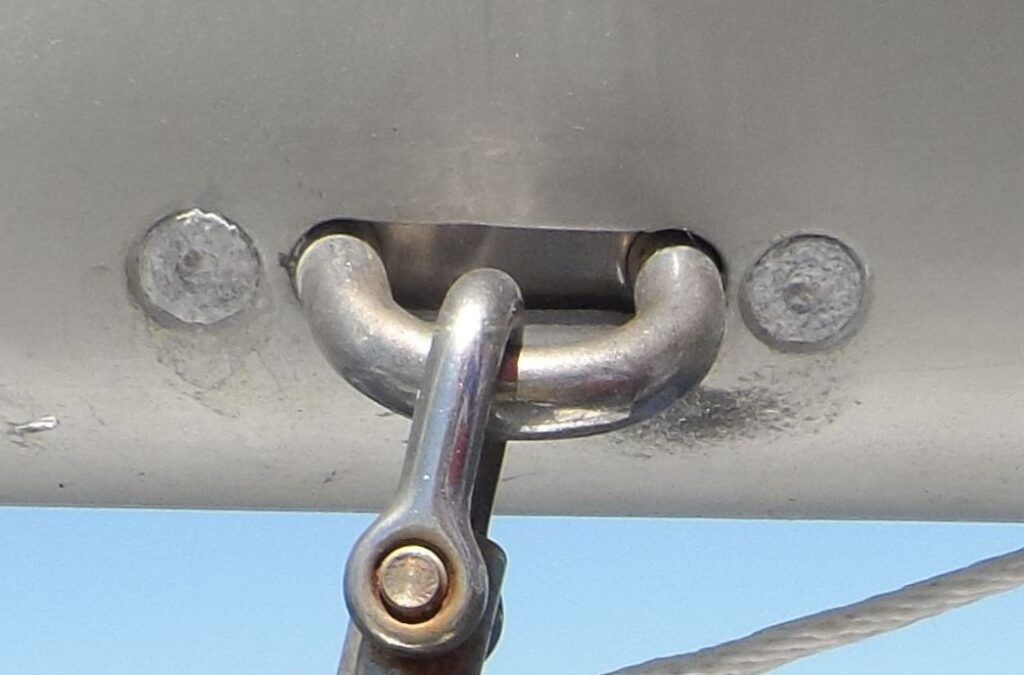
Again, monel is generally the best choice. Although close to stainless on the galvanic scale, monel has proven far less active when used on aluminum spars. Generations of Hobie Cats are held together with monel rivets. They are typically one and a half to two times the price of stainless rivets, but still only pennies each. And it’s not just Hobie.
Bearing in mind the risk of corrosion, monel pop rivets are the best choice for fastenings, particularly when attaching something to a thin-walled (< 3 mm) section. The pop rivet body should extend inside the section by 1.0 -1.5 x diameter. The pop rivet mandrel should always be punched out as these are made out of carbon steel and may discolour the mast when they rust. They are typically 1/3 to double the price of stainless rivets, but still only pennies each. U.S. Spars. Recommend and sell monel pop rivets. Sparcraft. Recommend and sell monel pop rivets.
From the Selden “Hints and Advice” publication.
RIVETS VERSUS MACHINE SCREWS
Properly installed rivets and machine screws of equal size are equal strength, with a slight advantage to rivets in thinner masts (see “A Riveting Report”). The better builders, including Hobie, specify monel rivets. Ease of removability might seem to favor machine screws, but after 20 years of corrosion, screws are often seized and drilling them out can border on impossible. 3/16-in. rivets, on the other hand, can be drilled out in seconds (the center hole provides a perfect guide). You need only drill enough to get the head off, after which the core is easily punched through. If they spin, grab the head with needle nose Vise-Grips. Ninety-five percent of the time the hole is undamaged and ready for reuse. In my experience, machine screws are for things you believe you will remove, rivets for things you believe you will not, but either is acceptable.
Monel machine screws and bolts are available, but the price will give you a stroke—typically 10 to 30 times more than 316 stainless—and the advantages are minimal. Do use a quality anti-seize agent.
COTTER PINS FOR PROPELLERS
Martec strongly advises against stainless steel pins due to corrosion risk to the prop. Johnson Marine pins are monel. You won’t find them at the chandlery or hardware store, but they are available from the manufacturer or McMaster Carr. We’ve seen stainless cotter pin failures on props, but not in the rigging (less salt exposure).
OTHER OBSERVATIONS
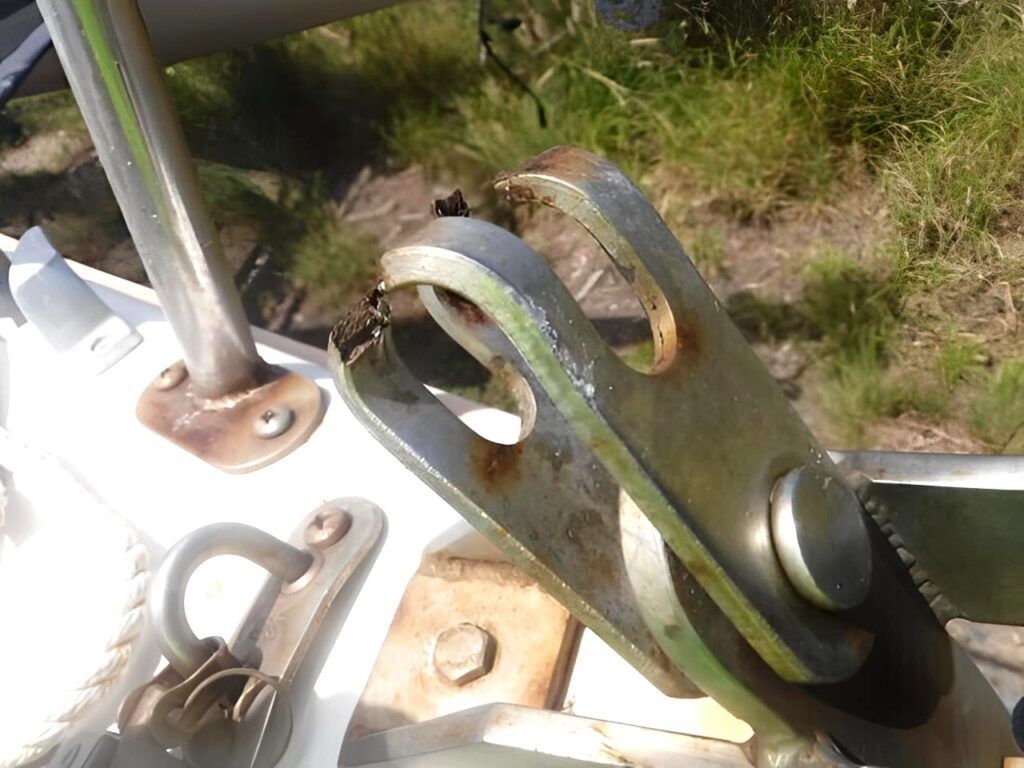
One of the most critical fittings on our Corsair F-24 test boat are the circlips that secure the 7/16-in. hinge pins in the outrigger folding mechanism. If a pin falls out, the beam will break, leading to a rapidly cascading failure, including breakage of the other beam, damage to the float, and capsize. We seem to have a failure about every other year, and the only prevention seems to be frequent inspection and premature replacement every few years. Because of the required spring properties, the best stainless alloy seems to be 15-7 PH stainless, and monel is not available. Another alternative is to replace the pins with stainless bolts and elastic insert locknuts. We did this for a few and it seems to be a permanent fix.
Monel is well proven in potable water tanks, though we have seen failures where the fabricator cut costs by using thinner material than he would have for stainless. Monel is not a good choice for exhaust systems; it does not like nitrogen oxides (NOx) and sulfur oxides (SOx), and it’s far more expensive.
SUMMARY
There’s nothing inherently wrong with stainless seizing wire. As long as you don’t over twist it and start cracks, it should last many years. Monel, on the other hand, though more expensive and harder to find, is easier to work with and will last the life of the equipment. Most U.S. chandleries only sell stainless rivets, and we’ve had good service life when properly installed, but perhaps not as good as the factory monel rivets on our beach cats. Since the major spar manufacturers all recommend monel, that settles it.
I’m troubled that most U.S. chandleries are moving away from carrying the good stuff. Same with fender washers I can nearly bend with my fingers. Selling high-test chain but not the shackles that go with it. It’s a price thing. I’m forced to keep a small stock of monel wire and rivets so that I have them. The only thing I use stainless seizing wire for is splicing fids and hooks to fish things out, where the greater stiffness helps.
Monel is higher on the galvanic series than most other materials. Consequently, it can cause accelerated corrosion in many applications. This should be considered before flatly recommending it as an alternative to other materials.
Sounds like it’s a hard material to beat for many applications. Question about rivets: what about using aluminum riviets on aluminum spars?
This always generates questions. Aluminum is slightly less likely to corrode. However, it can still corrode if the alloy is different from the spar, if the spar is anodized, or if the pin is still inside the rivet (the head of the rivet will be). I’ve seen aluminum rivets eaten away. There were some on the boom of my F-24, they were badly damaged, and drilled them out and replaced them with monel. Fortunately, it was a low-load application, because aluminum rivets are also much weaker.
For me the bottom line is that all of the spar manufacturers recommend monel. It is backed up by long experience with small boats, such as Hobie cats that live on the beach.
Superb. Excellent thorough comprehensive coverage. Articles like this one are the reason I continue to renew.
When I started sailing I was advised to use monel wire on galvanized shackles because it caused less corrosion than stainless wire. It has worked well for many years. I use stainless seizing wire on stainless parts, but perhaps monel would be preferable there too. When monel became hard to find at marine chandleries I discovered that it is used in airplanes and aeronautical suppliers carry it. Thanks for another informative article.
Dave Kallgren
Beagle, NorSea 27
The only rigging wire failures I have seen were primarily the result of over twisting and using the twisting process to pull the wire passes tight. For repetition and as the big take-away, snug each pass separately with you fingers or lightly with the pliers, and twist the finishing pigtail lightly. Standard aircraft safety wiring guidance is not more than 10 twists per inch, and about 5-6 twists to secure the pigtail. Bend to avoid snags.