We expect a lot from adhesive sealants for the marine environment. They must stick to a wide variety of surfaces, including gelcoat, aluminum, wood, stainless, and plastics. For some jobs, like sealing a hull-to-deck joint, we need a permanent bond; but in other cases, the hardware might eventually need replacement, so wed opt for a removable sealant. Marine sealants must be flexible to compensate for changes in temperature and slight mechanical movement. They must resist UV, seawater, and mildew. They also must be compatible with the bonding materials, and not cause deterioration.
We recently launched a new evaluation of marine adhesives and sealants. There is no single caulk that works in all of these cases, so its impossible to declare a single Best Choice adhesive, but we decided to at least put some numbers on paper to guide you in your choices.
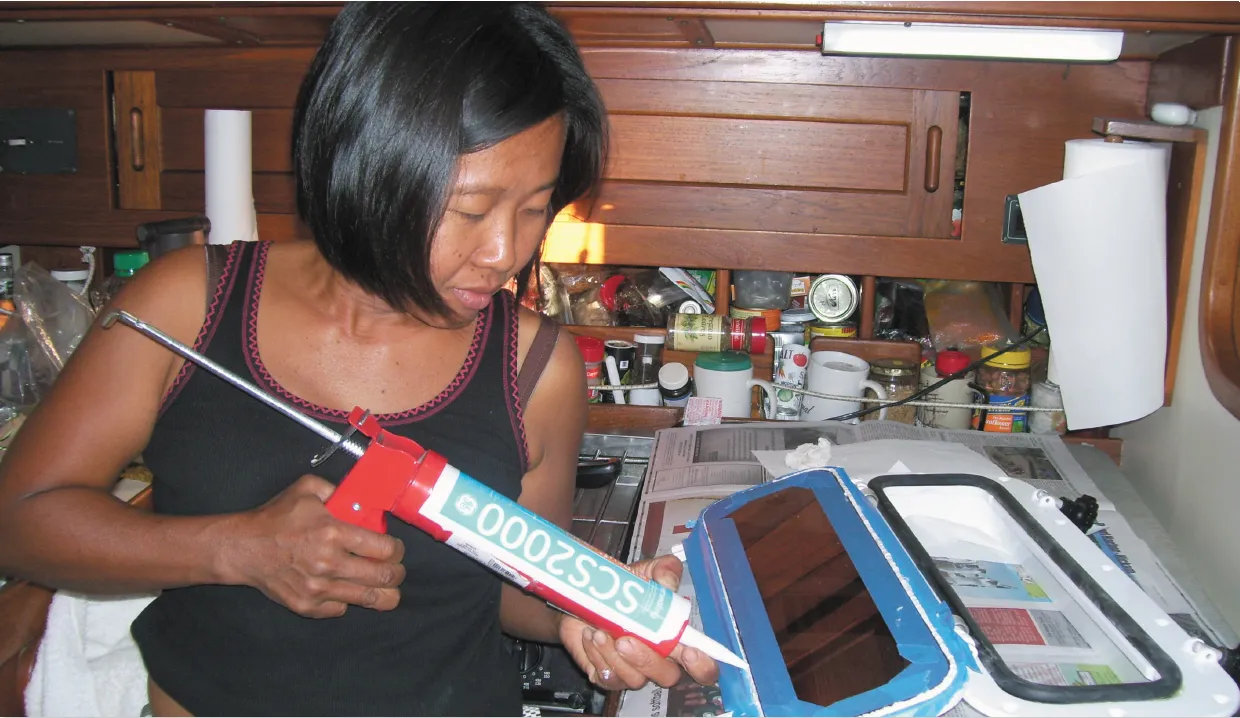
What We Tested
PS testers collected samples of 14 common caulking compounds from 3M, Sika, BoatLife, Loctite, and Sudbury, including silicones, polyurethanes (PU), hybrids, and butyl rubber. We tested them for strength, adhesion, and flexibility for this article and will be testing them for mildew resistance, ease of cleaning, and weathering resistance for future reports. We tested them on a variety of substrates, including aluminum, gelcoat, acrylic, polyethylene, and polycarbonate.
How We Tested
To test the bonds shear strength, we bonded 2- by 3-inch coupons (approximately 1.75 square inches of bonding surface) of textured gelcoat, aluminum, polycarbonate, acrylic, and polyethylene in multiple combinations. Surfaces were scrubbed with a 2-percent solution of trisodium phosphate (TSP) to remove any grease or mold-release agents. Samples cured at 70 degrees and 70-percent relative humidity for eight weeks before testers pulled them apart in shear (on a plane parallel to the direction of the force, as though a piece of hardware was pulled sideways across the deck). Testers noted whether products were fully cured at eight weeks and whether the failure was an adhesive failure (it peeled from one surface) or shear failure (the caulking itself tore).
Testers then used a bead of caulk (fillet) to bond two 2- by 6-inch strips of textured gelcoat to form a 90-degree corner. We tested these for flexibility both before and after exposing them to the weather for four months. We examined the coupons for cracking or other signs of weathering.
To determine a products shelf life, we sealed each tube with aluminum foil immediately after use and stored them in a refrigerator for six months. For long-term field-testing, we used the top-performing products in a variety of boat maintenance and repair applications. Observations will be noted at regular intervals.
Our main criteria for a marine caulk is that it should not peel from the substrate (adhesive failure), but rather it should fail by shearing and tearing. Products that do not adhere to the substrate are useful only for hardware that is well-secured by mechanical fasteners.
Observations
The test products varied in viscosity: Loctite and Sika products are generally thicker, while 3M 5200 is noticeably thinner and prone to running if applied too liberally or if a large fillet is desired. Drying time and mechanisms also varied. In the case of silicone caulk, air is required. In the case of polyurethanes, atmospheric moisture is the primary curing agent. All of the test products skinned over within a few hours, except for PL S40 and 3M 5200, both of which are notoriously slow curing. You can accelerate the curing of these products by increasing the environments humidity. Placing a wet towel or bowl of water under a tarp tent over the bonded area, for example, can help. You can also lightly mist polyurethanes to accelerate curing after the first 12 hours, even if it is still tacky.
Full-strength adhesion takes time. Several products skin over very quickly, but they remain soft inside, curing more like a latex house caulk than a polyurethane caulk. Much depends on the water permeability of the substrate. Metals and polyethylene are impermeable, while fiberglass and wood have some moisture content and cure more quickly. When testing slow- to medium-cure caulks after three weeks, testers found a number of products that were still soft in the center, so we delayed testing an additional five weeks. Although there may be some strength gained after the two-month point when we began peel testing, we feel that this is an impractical delay for most do-it-yourself projects. A caulks ability to sustain its advertised bond strength (usually stated in pounds per square inch) can vary greatly according to conditions, and the type of product being used. In our experience, most of the these products can be put into service within the manufacturers specified timeframes (ranging from a few hours to one week), but for bondlines that will be subjected to high loads, you should wait at least a month before pushing the limit of any products adhesion strength, if possible.
Only one product failed the flexibility test: the BoatLife Caulk. When we flexed the BoatLife Caulk sample after curing, it immediately de-bonded and popped loose under light pressure, leaving no residue behind. We saw the same bond failure in lab shear testing. Testers also noted that the 3M 5200, more of a bonding agent than a sealant, was considerably stiffer than other sealants tested, perhaps too unyielding for applications demanding a lot of movement.
Heat-treating polyethylene (Starboard and similar products) prior to bonding yielded significant improvements in peel strength for this difficult-to-bond material. It is an old sign-makers trick, but its relatively unknown to sailors.
Cold storage helps extend the life of partially used adhesive tubes. Seal the tip with aluminum foil immediately after use and during any pause in activity to prevent water vapor from entering. Since water is the initiator for polyurethane sealants, even a hint of absorbed water vapor can cause material in the tube to slowly thicken. Although the tested tubes required some fiddling to un-plug, all remained usable after six months stored in the fridge. Caulks with removable tips are easier to reuse, since you can remove the cured plug more readily. You can also drill out the plug.
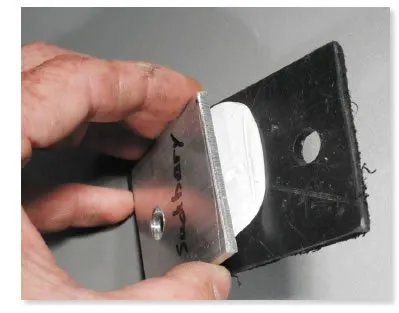
Polyurethanes and Blends
Polyurethane caulks are one of the most popular types of marine caulks. Their adhesiveness, long life, and resistance to water make them useful for bonding and high-adhesion bedding applications both above and below the waterline. Not all are designated for below-the-waterline use, however, so be sure to match the product for the job.
Loctite Marine Sealant
Very similar to 3Ms 4200 and Sikas 291, the polyether Loctite Marine Sealant is a thick, medium- to fast-cure product intended for use above and below the waterline. It demonstrated a wide range of compatibilities and very high strength in tests.
Bottom line: This tied the Sika 291 as the Best Choice for an adhesive sealant.
Loctite PL S40
Reviewed by Practical Sailor in August 2015, Loctites PL sealant series offers an economical alternative to marine products. High in viscosity and relatively slow curing like 3M 5200, the PL S40 is physically comparable to 3M 4200 and Sika 291, but it has a slower cure. Since this is not a designated marine product, were still testing it above and below the waterline, and we will report back if we find anything negative.
One PS tester has been using it for eight years for various onboard applications with good results. Although Loctite does not recommend this product for continuous immersion, it has passed industry standard tests for moderate-term immersion. In one field test, we used it for a large patch on a polyethylene fishpond liner-a tough application-and even after five years, it has shown no signs of peeling or hardening.
Bottom line: Priced right and performing well in field tests, PL S40 is our Budget Buy for an adhesive sealant.
3M 5200
The widely used 3M 5200 is known for its long cure time. For boatbuilders, a long working time can be a blessing. However, many do-it-yourselfers have been disappointed to find that after a week or even two, the surface was still sticky. The slow cure is nearly always linked to very dry conditions in a home that is heated for the winter. The solution is to raise the air humidity, even by misting the surface if nothing else is practical. Another option is switching to 3Ms 5200 Fast Cure, which out-performed other adhesives for wood to fiberglass joints in our August 2010 review. (See The Great Stickup, PS August 2010 online.)
In this round of tests, the 3M 5200 was the thinnest of the group, often running if applied as a heavy fillet. However, when it does finally cure, it is tenacious, and is more of an adhesive than a sealant. It did not bond well to aluminum or to some plastics. This may have been due to incomplete curing, even after eight weeks. We’ve also found that it does not bond to stainless steel as well as some other products.
Bottom line: Decades of proven use underwater make the high-strength 3M 5200 adhesive a professionals favorite for below-the-waterline projects. Its Recommended.
3M 4200 Fast Cure
Similar to 5200, 3Ms 4200 is not as strong but it cures faster. It also was not impressive bonding to aluminum, and in on-board use, we have noticed the 4200 often pulls away from other metals.
Bottom line: We tested other polyurethanes that will adhere better to a broader range of substrates.
3M 4000 UV
Similar to Loctite Marine, 3Ms 4000 UV is a polyether. It demonstrated good adhesion to a wide range of materials, but suffered a reversion failure during long-term testing. According to 3M this product was reformulated in 2018. However, there was no product recall, so products might have been sold after 2018.
Bottom line: The 4000 UV is not Recommended as an adhesive sealant. If you used this product prior to 2019, you should monitor it for failure. We do not recommend this product.
Sika 291
The Sika 291 is a good general-purpose polyurethane caulk with a wide range of bonding capabilities. It performed well in our tests, and it is also doing very well in a series of tests on bonding sailcloth and Sunbrella.
Bottom line: The Sika 291 tied for the Best Choice adhesive sealant pick.
Sika 295
Like Sika 291, the company’s 295 is a good general-purpose sealant. With a primer, it can be used to mount Lexan and acrylic windows. However, we like silicone a little better since the process is simpler and the silicone is easier to remove when reglazing.
Bottom line: The 295 is Recommended for bedding and as an adhesive-sealant.
Sudbury Elastometric Sealant
Sudburys Elastometric Sealant is a synthetic, rubber-based sealant whose main purpose is gap-filling and sealing, rather than adhesion. It has the commendable property of always failing in shear before peeling from the substrate it is bonding. The sole exception to this behavior was when bonding polyethylene, a notoriously difficult material to bond. However, if we had heat-treated the surface first, the caulk would have developed a strong bond, and eventually fail in shear as we saw with other substrate. The Sudbury product did show some shrinkage after several months, although it still adhered very well.
Bottom line: Recommended for bedding.
BoatLife Boat Caulk
We were surprised to see three, successive gelcoat-bonding failures in the BoatLife Boat Caulk samples. The Boat Caulk failed our flex test on duplicate shear samples, the easiest of the tests.
Bottom line: While it has a long history as a bedding sealant, we think there are better products.
BoatLife Boat Seal
A silicone/polyurethane blend, BoatLifes Boat Seal provided acceptable adhesion, and its cure was faster than most products.
Bottom line: Recommended for bedding.
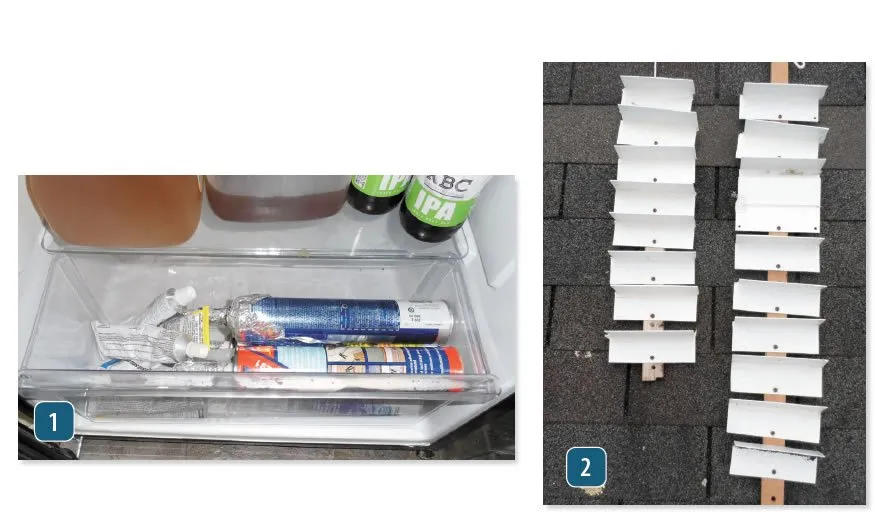
Silicones
Although we dislike silicone sealants for most marine applications, it is well-suited for mounting hatch lenses and in locations where fuel or gasoline exposure is expected. It also can work well to seal wire penetrations on deck.
BoatLife Silicone Rubber
BoatLifes Silicone Rubber has a very strong and unusual acetic acid odor. In tests, it was less adhesive than other silicones.
Bottom line: Other products adhered better in our tests.
3M Marine Silicone
With low odor and a good open shelf life, 3Ms Marine Silicone is one of the few sealants that seems to stay workable even when stored at room temperature for years.
Bottom line: With a long useful life, this caulk is handy to keep in the toolbox.
Dow 795
Dows 795 has a proven record for sealing port or hatch glazing (Lexan, acrylic, or glass). Its UV resistance is at least as good as plastic glazing, and it has better adhesive properties than other silicones. Also, it will not damage the plastics. (Some caulks can lead to crazing.) The 795 is far easier to remove than polyurethane alternatives, and by using the proper de-bonding product (stay tuned for our upcoming test of de-bonders), you will have no problems replacing the hatch glazing or portlight should this become necessary.
Bottom line: This is our Best Choice for plastic lens replacement.
Butyl Tape
Butyl tape did not meet the criteria for this test, but it is worthy of mention for several reasons. Although it has almost no tensile strength-requiring hardware fasteners-this bedding material has more than enough adhesion for sealing off deck penetrations like hatches. And because it has no strength, you can easily pry up even the largest hatch for repair or replacement. Mineral spirits can easily remove the last traces of butyl, but there is no need to do this if youre just bedding a new hatch. Just remove as much as is practical and apply more. This tape lasts forever in the toolbox, and very little cleanup is required. After tightening the hardware, simply trim the excess with a plastic knife.
A few caveats worth mentioning: Butyl tape can run in hot environments, so check its temperature rating; don’t use it below the waterline; and don’t use it in places where it will be exposed to fuel.
Bottom line: Its Recommended for bedding big hardware, such as hatches, that will have to come off someday.
Conclusions
Although this test focused on adhesion strength, don’t assume that the strongest goop is the best. Using a high-strength adhesive for bedding deck hardware can lead to expensive, time-consuming surface repairs should you need to replace the deck hardware. We couldn’t separate any of the stronger products without breaking our fiberglass test coupons. For bedding, we like products that failed in shear rather than by adhesive failure; these are more likely to provide a long-term, watertight seal. For sealing smaller hardware, where a little extra support might help, we like the Loctite PL S40 and Sika 291. Both offer mid-strength adhesion and have the ability to bond gelcoat, metals, and plastics. However, we would not recommend these for hatches and winches; you’ll never get them off. For bedding hatches, winches, and other items, we like the Sudbury Elastomeric Sealant and butyl tape. Both adhere to a wide range of surfaces, fail in shear, and are reasonably easy to separate.
For sealing glazing, we like the Dow 795 Silicone over all others. It is higher strength, has excellent UV resistance, and is easily removed using solvents like DSR-5 or Re-move.
Perhaps the most important factor in the success or failure of the caulk joint is not the caulk itself, but a matter of providing ideal conditions for bonding and sealing. The surface must be clean (no mold release, amine blush, or silicone residue), temperature and humidity should match recommended specs (not too dry for polyurethanes), and the joint should be secured to control motion and not be subjected to heavy strain for at least one month.
An upcoming report will look at products for removing adhesive sealants, and in future reports, we will be looking at adhesives mildew resistance and aging. Stay tuned.
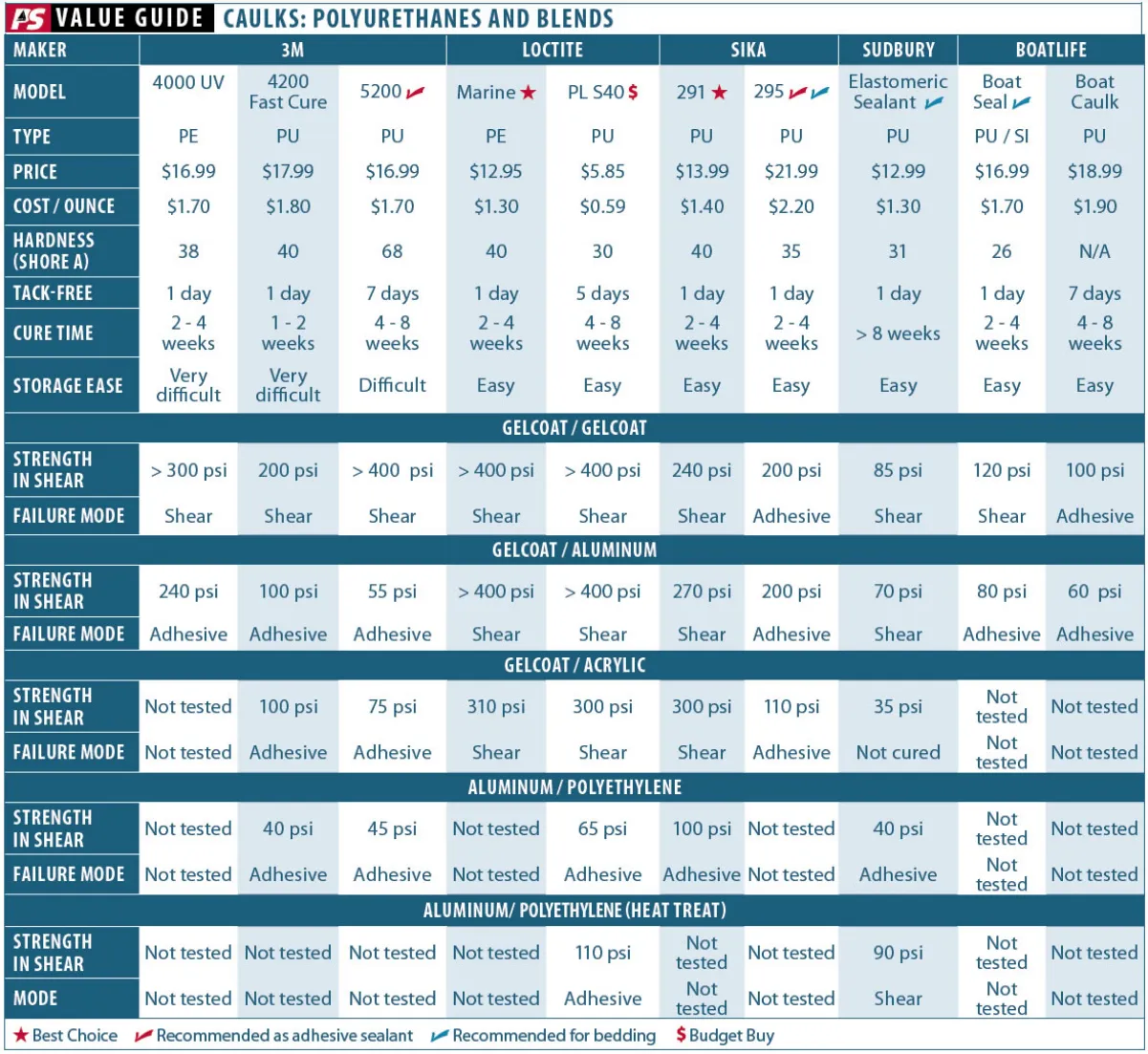
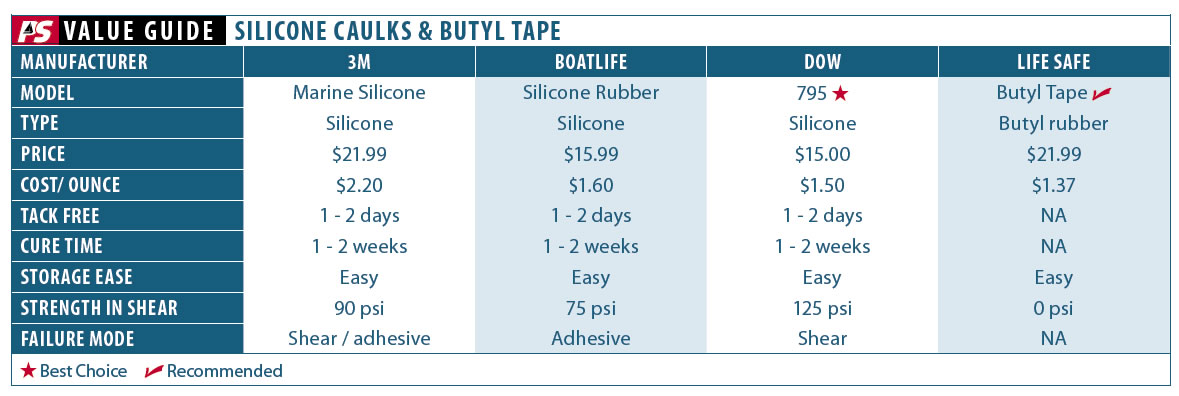
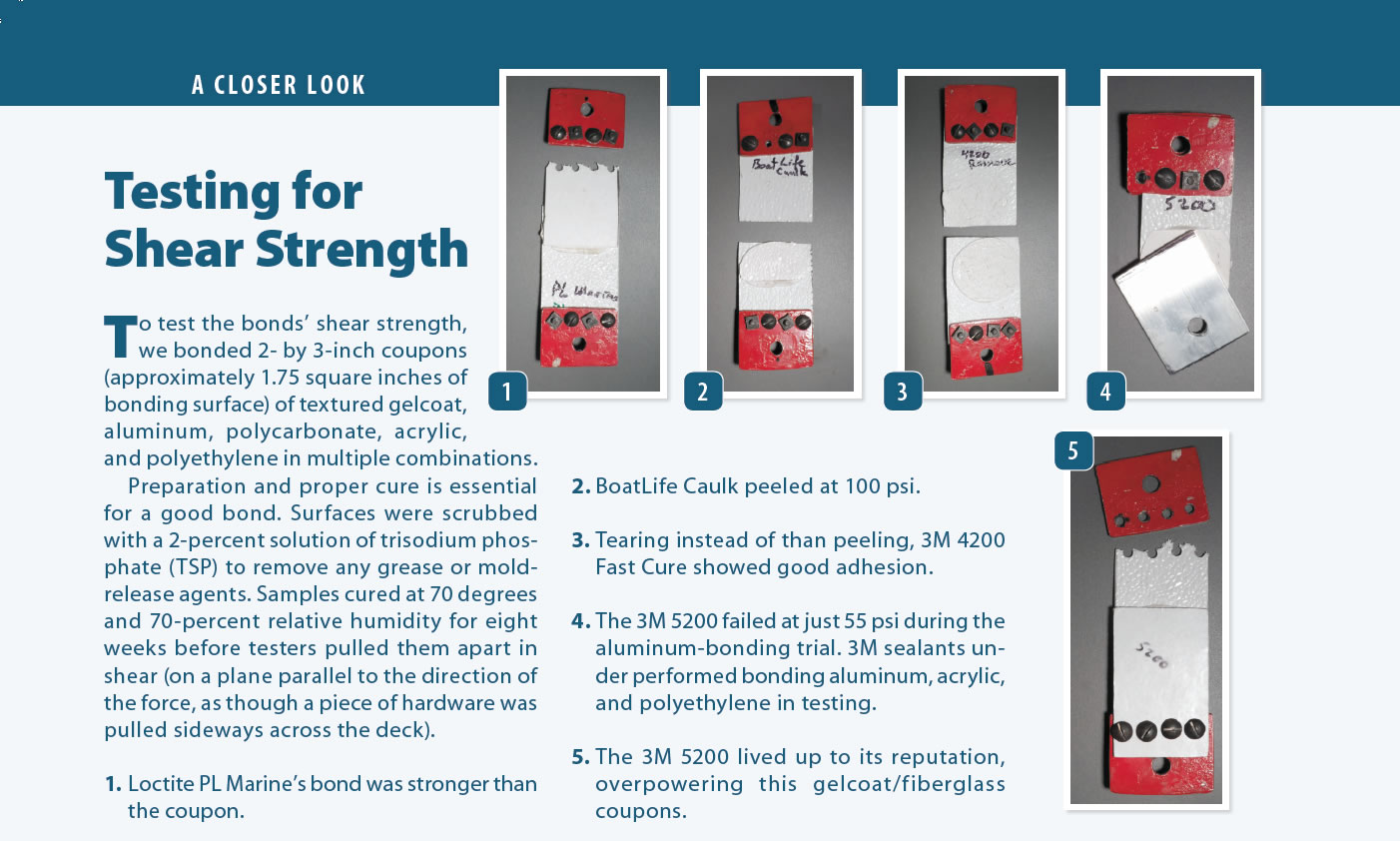
To test the bonds’ shear strength, we bonded 2- by 3-inch coupons (approximately 1.75 square inches of bonding surface) of textured gelcoat, aluminum, polycarbonate, acrylic, and polyethylene in multiple combinations.
Preparation and proper cure is essential for a good bond. Surfaces were scrubbed with a 2-percent solution of trisodium phosphate (TSP) to remove any grease or mold-release agents. Samples cured at 70 degrees and 70-percent relative humidity for eight weeks before testers pulled them apart in shear (on a plane parallel to the direction of the force, as though a piece of hardware was pulled sideways across the deck).
1. Loctite PL Marine’s bond was stronger than the coupon.
2. BoatLife Caulk peeled at 100 psi.
3. Tearing instead of than peeling, 3M 4200 Fast Cure showed good adhesion.
4. The 3M 5200 failed at just 55 psi during the aluminum-bonding trial. 3M sealants under performed bonding aluminum, acrylic, and polyethylene in testing.
5. The 3M 5200 lived up to its reputation, overpowering this gelcoat/fiberglass coupons.
Great article! I used this 3M 5200 to repair cracks on the deck, hull and stem joints of my boat and it delivered excellent results. I would recommend this for boaters to seal and bond their exterior and interior fixtures.
Liked this review (and I know its a bit dated). I, also, have found on numerous occasions that over time 5200 doesn’t bond well to stainless steel. Your statement, “We’ve also found that it does not bond to stainless steel as well as some other products.” would have been MUCH improved if the article had somewhere indicated which of those others your were referring too DOES bond well instead of leaving us dangling.
I say this as I rebed my chainplates, to which 5200 has not adhered well.
Sikaflex LOT 291 has done well in our previous tests, and is recommended by former tech editor Ralph Naranjo for bedding deck hardware like stainless steel stanchions — although butyl tape (https://www.practical-sailor.com/belowdecks-amenities/goo-vs-gaskets-for-bedding), and silicon are also used. We have several previous reports on the topic of sealants in which this is dealt with in more detail. A common problem with stainless is that it is not fully prepped and some of the oily residue from the machining process still contaminates the surface and prevents good bonding.
https://www.practical-sailor.com/boat-maintenance/caulk-and-sealant-test
https://www.practical-sailor.com/boat-maintenance/the-great-stickup-practical-sailor-tests-marine-adhesives-caulks-and-sealants
And Marine Consultant Steve D’Antonio discusses prepping SS for bonding here: https://stevedmarineconsulting.com/caulk-and-sealant-selection-and-use/
Darrell,
I have a Bayliner 3288 with lots of hardware on the stern that needs to be re-bedded with new fasteners. A lot of the hardware is below water line. When I reinstall the hardware, I believe what is needed is to re-pot all of the fasteners in their holes to (a) seal the hardware (like rudders, trim tab brackets, etc) to the transom, and (b) ensure that if a leak occurs, the interior of the holes are sealed to prevent water from getting into the plywood core.
For this application, and after reading the articles you’ve written back for a decade, would Sika 291, 295, or PL S40 be good choices?
Any tips on re-bedding fasteners through a 2″ transom, such as remove, re-drill, epoxy coating in the holes(?), and pot? I couldn’t find any PS articles about that specifically.
Thank you!
Ron W
Ronald,
Below the waterline fittings should be bedded only with an adhesive sealant that is specifically recommended for below the waterline. Of the products you list, Sikaflex 291 is the best suited for this purpose. None of the others would provide reliable service.
These best marine products you have laid down are my optimal solutions. Their essential factors, features, types, benefits, buyer guides, and other details will help me make a smart choice. Thanks for sharing!
Ottimo test. Grazie mille per il vostro contributo. Saverio
You have a lot of excellent long time-span product comparisons like this and I appreciate that you revise them over time. It would be incredibly helpful if there was a revision log, just a sentence or two summarizing the substantive changes, particularly when products initially passed your tests but failed later, or improved after reformulation. Obviously don’t care as much about knowing non-substantive revisions, grammar edits, broken links etc. thanks!
Just for clarity, I believe the BoatLife products are named “Life-Calk” (the polysulfide) and “Life Seal” (silicon/polyeurethane) not Calk and “Boat Seal.”
Regarding Butyl please remember that it shouldn’t be used where it might be exposed to any petroleum product. I’m thinking chain plates where diesel fuel might be stored on deck in jerry cans. Just a caution… It does seemingly however, remain flexible in perpetuity!