We don’t really know what the life expectancy of a fiberglass boat may be. There are lots of them out there that are more than 20 years old, still going strong. We do know, however, that no matter how longlived fiberglass may be as a structural material, over time the gelcoat surface commonly used in finishing fiberglass becomes porous and chalky, and has the unfortunate tendency to crack and craze. Gelcoat, in other words, weathers just as a painted surface will over time.
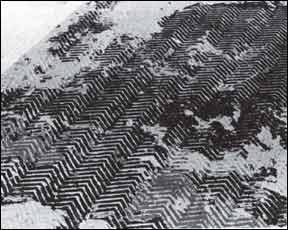
288
With topsides, a tired gelcoat surface can be restored to better than new condition through the use of polyurethane paints, which can retain color and gloss for years. Decks, however, are another story.
The molded-in nonskid surface of most fiberglass decks weathers over time like the gelcoat on the rest of the boat. In fact, deck gelcoat usually has a much harder life, since the horizontal surface of the deck is constantly exposed to the ultraviolet rays of the sun. While modern gelcoats contain fairly effective ultraviolet inhibitors to protect the gelcoat surface, they will only delay, not prevent, the gradual deterioration of the gelcoat.
The gelcoat on older boats may have little or no ultraviolet inhibitor, or its effectiveness may have long since vanished. Sooner or later, you’re going to have to face up to a deck that is faded, chalking, crazed, and worst of all, has lost a substantial portion of its nonskid characteristic. Do not despair. It doesn’t mean the end of the value or usefulness of your boat.
How Boatbuilders Make Nonskid
There are two basic methods of producing nonskid decks in the normal course of production fiberglass boatbuilding. Most commonly, in making the deck plug, the builder will glue plastic or vinyl having the nonskid pattern embossed into it onto the plug. When the mold is made, the nonskid pattern is transferred, along with the rest of the details, to the surface of the mold.
In another method, the deck of the plug is finished with gelcoat. When the glecoat begins to cure, the surface is rolled with a dry roller — like a paint roller — which tends to pull the partially cured gelcoat up in a stippled pattern. This type of deck finish is seen on boats built by C&C, for example.
In either case, in laying up the deck for a boat, a relatively thick layer of gelcoat is sprayed into the mold to completely fill the patterned surface of the mold, and then the deck is laid up in the same general fashion as the hull.
Because a lot of mold release agent must be used in a deck mold to free the nonskid sections of the deck from the mold, a brand new deck may actually be relatively slippery, and will remain so until the mold release agent is washed away.
In a few years, you may notice that although the non‑Worn molded-in nonskid can turn your decks into a skating rink in wet weather skid properties of the deck are pretty good, the deck has become stained, and doesn’t respond well to scrubbing even with abrasive cleaners. Although scrubbing may clean the decks, it also accelerates the wearing away of the porous gelcoat, and over time the cleaning cycle must be repeated at shorter intervals.
The Cure
When the gelcoat of your topsides becomes faded, chalky, or crazed, it’s a fairly simple — though expensive — matter to restore them with polyurethane paint. The same solution, however, won’t work on worn fiberglass decks. Worn nonskid will simply be made more slippery by the application of polyurethane paint. Adding a nonskid powder to the paint may give you a surface with good nonskid properties, but the trade-off is the rather unattractive combination which looks like someone spilled sand all over your fresh paint on top of the molded-in pattern.
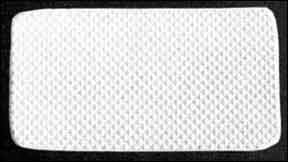
288
More radical cures will yield better results.
A number of products especially designed as nonskid surfaces for decks are available. Which you choose is as much a matter of esthetic considerations as it is of functional ones. None of the solutions is particularly cheap.
Once you have decided that your decks are bad enough to require reworking, a very basic decision must be made: do you want the newly-done deck to look as close to original as possible, or are you concerned only with providing an attractive, nonskid surface?
This is not necessarily a simple question to answer. With a series-produced boat, part of the value of the boat when the time comes to sell it is how closely the boat conforms to the “ideal” for that particular design. An obvious example of how you can reduce the value of a boat is to paint it an odd color. Perhaps you really want an orange Pearson 35, but what’s going to happen when you try to sell it? Likewise, having decks that look different from “normal” may make the boat more difficult to sell, even if the deck covering is in fact superior to that which originally came with the boat. By contrast, with a custom boat, being different is not a drawback, provided the difference is universally admired.
The majority of American-built production fiberglass boats use molded-in nonskid which resembles either a coarsely woven fabric, or a series of tightly-spaced pyramids. Over the years, the surface gradually wears down and becomes porous, and the nonskid properties may slowly deteriorate.
“Posi-Grip”, a product of Marine Innovators, (Box 608, Jupiter, FL 33468, (305) 746-0605), closely resembles the original nonskid surface of many production boats, and can be used to replace worn surfaces. With careful application, you will end up with decks so similar to their original appearance that few people, if any, will realize that the decks have been renewed.
“Posi-Grip” is a sheet of gelcoat finished with the pyramid type of nonskid surface. Ounce-and-a-half fiberglass mat is used in the layup to provide strength to the material, primarily for shipping purposes.
Total thickness of the material is about 3/32”, and it weighs about 11ounces per square foot. The base price of Posi-Grip is $4.95 per square foot, plus shipping. Sheets of Posi-Grip are 3’ by 8’.
A simple summary of the installation of Posi-Grip is that the decks are sanded, the Posi-Grip is cut to fit over the old nonskid areas, and the material is glued down with thickened polyester or epoxy resin.
In practice, this procedure is fairly involved, but it is certainly within the capability of any handy person.
For an extra $1.25 a square foot, Posi-Grip can be molded in almost any color you want, rather than the basic white. All you have to do is provide the manufacturer with a color chip.
The advantage of this option should be immediately apparent. White on white decks can be modified to reduce glare. Color schemes can be changed. Because the color is molded into the material, it will not wear off the way paint will. Posi-Grip should, in fact, last as long as the boat’s original gelcoat finish. So far, it has only been in use for four years, so really long term behavior isn’t yet known.
The first step in applying a Posi-Grip deck is to determine the amount of material needed. In most boats, the nonskid pattern does not cover the deck from gunwale to gunwale. Usually, the nonskid pattern is broken up by narrow areas of smooth gelcoat.
There are several reasons for this -some esthetic, some functional. Most nonskid surfaces are fairly difficult to clean, as dirt lodges in the pattern. The deck camber of most boats means that in rain or heavy dew, water runs to the deck scuppers along the outside edge of the deck, carrying dirt with it. Having 2” or 3” of smooth gelcoat along the outside edge of the deck, inboard of the toerail, makes the deck far easier to keep clean.
In addition, pattern matching of the nonskid could be quite difficult if the nonskid surface were continuous, rather than broken into smaller, self contained areas.
Finally, most decks simply look better with the nonskid pattern broken by areas of smooth gelcoat, and this effect can be further enhanced by having the areas of nonskid and smooth gelcoat of contrasting colors.
Because some of the nonskid areas of most decks are odd in shape, there will be some waste of the Posi-Grip material. To determine how much you need -at almost $5 per square foot, you want as little waste as possible make a paper pattern of each separate section of nonskid on the deck. By arranging the patterns on a 3’x8’ piece of cardboard, plywood, or some other scrap material, you should be able to determine exactly how much Posi-Grip you need. Allow a little extra for breakage and mistakes.
The next step is to determine the color you want. If your decks are colored gelcoat, and you wish to reproduce the original color, remember that they are likely to be quite faded. If you want to know the original color, remove a cleat or stanchion base that has been on the boat since it was built. You may be surprised at how much colors other than white will fade.
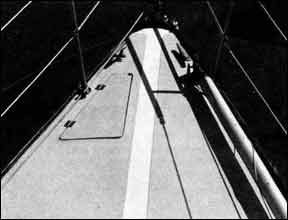
288
If the boat is currently in production, you may be able to get a sample of the gelcoat color from the builder, or he may be able to give you the manufacturer and color number. Do not, realistically, expect to duplicate exactly any color, as every batch of gelcoat or paint is likely to vary slightly in color.
The other option is to get a color card of the type put out by all paint manufacturers. Posi-Grip’s manufacturer claims they can come quite close to matching color samples.
If you’ve decided to change the color of the decks, remember that the tiny color samples provided by most paint manufacturers won’t tell you how a whole deck of that color will look. As a rule, the deck will look darker than the color sample, just because you’re seeing so much more of the color when the entire deck is painted.
Stark white is a poor color choice for decks. In bright sunlight, the reflections can be blinding. Even an off-white color that looks good in the showroom is likely to be too bright on a sunny day. On the other hand, dark colors may heat up excessively in the sun, turning the interior of the boat into an oven. Lighter shades of blue, green, and buff are traditionally used for decks. Painting the areas of smooth gelcoat between nonskid areas white, or a lighter shade still of the color chosen for nonskid areas, you should end up with an exceptionally attractive finish.
If you are going to use Posi-Grip, make all the color decisions before ordering the material, rather than trying after the fact to match a paint color to the gelcoat chosen.
Now the real work begins. For truly professional results, you should grind the old nonskid pattern off the decks, so that you have a smooth surface for application of the new material. Do not heavily grind down areas of smooth gelcoat between nonskid areas, since they will not be covered by the new material. They can be masked off from the nonskid areas both to protect them, and to provide the reference for the application of the Posi-Grip.
It is not necessary to remove all traces of the old pattern, but adhesion will be improved if the chalked surface of the old gelcoat is well abraded.
In order to make the deck look its best, it will be necessary to paint the areas of the deck not covered by nonskid. Polyurethane is the only paint to use for this, because of its longevity and resistance to chalking. You can either paint the smooth areas before or after application of the nonskid if polyurethane paint is used, but resin spills and other minor mistakes will probably mean some touching up after the fact if paint is applied beforehand. We’d paint afterwards.
When the decks are thoroughly sanded, apply the nonskid material. Posi-Grip can be cut to shape using shears or a saber saw. If you use shears, they must be heavy duty, and must be sharp, as the material is slightly brittle. The patterns you made to determine the amount of material needed are used as templates for cutting the new material. If you were smart, you marked the “up” side of each pattern, so you don’t end up with a carefully cut piece of Posi-Grip with the pattern on the wrong side.
Don’t automatically assume that the nonskid pattern is perfectly symmetrical on both sides of the boat. Make separate patterns for each area on each side.
After each section is cut out, bevel the edges of the material using a rasp or a sanding block.
Posi-Grip can be applied with either polyester or epoxy resin, thickened with cabosil to keep the resin in place. It may be necessary to use some weight to get the material to conform to the crown of the deck. Use no more weight than is necessary, so you don’t squeeze out all the adhesive.
When the individual section of nonskid is properly positioned and weighted, immediately clean up the excess resin. Acetone can be used to clean up polyester resin. Epoxy cleans up reasonably well with soap and water, before it has started to cure, but lacquer thinner does the fastest job. Unfortunately, lacquer thinner is extremely toxic, and must not be inhaled or allowed to get on your skin.
The importance of thorough cleanup before the resin kicks cannot be overemphasized. It may well be the most tedious part of the whole job, but it greatly simplifies the finishing off of the job, and can make the difference between a truly professional job and a painfully amateurish one.
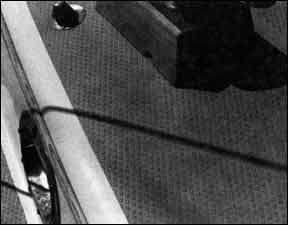
288
Never try to work on more than one section at a time. You’ll find yourself tracking resin, accidentally sliding panels, and generally making a mess. It’s far better to waste a little resin than it is to try to clean up a monumental mess.
With all the new nonskid glued down, you are ready to paint the areas of smooth gelcoat between nonskid patches.
Some touchup sanding of these areas is likely to be required, as incompletely wiped up spills of resin can affect the adhesion of paint, Once again, take time in preparation. Sand down or chip off any resin spills you missed. If you chip them off, and you used epoxy resin as an adhesive, you’ll probably take the old gelcoat off along with the chip of new resin, so be careful.
Carefully mask the edges of the new nonskid surface. Use 3M Fineline tape for best results, as paint will not bleed under the edge as it does with conventional masking tape. Use throwaway polyfoam brushes for painting.
Although this type of deck is a lot of work, and can cost a lot of money, the results can be pretty breathtaking. Doing the decks, but not the cabin top of a 35-footer would probably take three or four sheets of Posi-Grip, at about $150 per sheet for custom-colored material, which we would recommend.
You’ll also use about a gallon of resin, plus fillers, plus sandpaper, masking tape, polyurethane paint, solvents, sanding masks, brushes, and other assorted odds and ends.
Like other major projects, this is not one to undertake the year before you plan on selling the boat. You won’t get your money back unless the old decks were in such bad shape that it is impossible to sell the boat.
The Soft Solution
While Posi-Grip allows you to pretty much duplicate the original appearance of most fiberglass decks, it is by no means the only solution. Three European products, available in this country, provide an interesting alternative which can be both attractive and functional.
While the formulation and appearance of each of the three products is different, they are functionally similar. These coverings are:
-Treadmaster.
– Vetus Non-Skid Deck Covering.
-TBS 021 Non-Skid.
Each of these products is a combination of plastic resins with granular additives, giving a surface with excellent adhesion when wet or dry. Each also provides a good sound absorbing barrier, and has enough resilience to absorb impact from falling objects such as winch handles.
The distinctive large diamond pattern of Treadmaster “M”, while making it wonderfully nonskid, also makes the material less than comfortable to sit on when wearing shorts or a bathing suit, and can leave your skin looking sort of like you just escaped from a giant waffle iron. The smaller, raised circle pattern of Vetus nonskid has somewhat the same effect. The surface of TBS has a stippled surface, which is slightly softer to the touch than the other materials.
The only complaint, other than comfort, that we have heard about any of these materials is poor adhesion. Since these complaints are not universal, it may well be that surface preparation, or improper adehesive, are to blame rather than the material itself. Each company makes its own adhesive, although Treadmaster also recommends the use of epoxy resin as an adhesive, in addition to their own product.
Like Posi-Grip, each material is supplied in sheets or rolls, which are then cut to the shape of the individual nonskid panels. These soft deck coverings can be cut either with heavy sheers or a sharp utility knife, then glued down.
Surface preparation for best results is similar to preparation for Posi-Grip, so don’t expect any real shortcuts here.
Once again the amount of care taken in preparation and application largely determines the appearance and longevity of the finished product.
The only real disadvantage to any of these products that we can see is that they are “different.” Americans are used to molded-in nonskid, rather than an applied surface.
Whether you want your boat to be different, or prefer it to look like it did the day it came out of the factory, is something only you can decide. We would be far less concerned about putting a “different” deck covering on a custom boat than on a production boat.
Conclusions
Application of any of these four deck coverings is a major job. Unless you’re willing to take the time to do a really professional job, don’t even think about starting. Each covering is basically irreversible, by virtue of the surface preparation involved and the adhesives used.
This is a time-consuming project. Unless the existing deck is badly chalked or has lost much of its nonskid properties, it is a lot to bite off. Like other major projects, patience and planning are the two key ingredients. Don’t tackle the project if you’re lacking in either one of these characteristics.
A simple painting, with nonskid compound added to the paint, is a quick and dirty solution to the tired deck problem. It is likely, however, to reduce the value of your boat to whatever extent the job you do looks worse than the original, no matter how well it actually works in keeping you from slipping.
Though fiberglass lasts a long time, nothing lasts forever. Renewing worn fiberglass decks, however, can go a long way to giving your boat a new lease on life.