When it comes to the development of electric drive systems large and small, there’s a double-headed challenge. The first is the propulsion system itself, a combination of electric motor and drive train that efficiently turns watts into speed through the water. Big strides forward have been made in brushless DC electric motors sporting rare earth magnets. These cutting-edge systems rely upon a winding sensor and an electronic voltage phase controller that can swap polarity thousands of times a second and maximizes torque per ampere consumed. This new technology has sidelined the less efficient arcing-and-sparking carbon brush and armature type electric motors that have energized copper windings for over a century. Better magnets, cooler running motors, and better bearings have also helped to plus up the power-to-weight ratio of these electric/electronic motors.
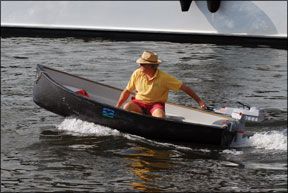
Photos by Ralph Naranjo
288
The second part of the puzzle is the acquisition of amperes to run the motor, and an interesting point is made by looking shoreside. Home central air-conditioning systems run using electric motors because of the convenience and the cost-effectiveness of the kilowatt hour that’s delivered to each house via the national grid. Currently at least, the price is much better than the all up cost of generating your own energy, electrical or mechanical. Add to this the fact that electric compressors require very little maintenance for the first decade or so, and there’s much less noise to abate. So it’s a no-brainer that electricity is the right energy source for home HVAC systems, and it garners a 99.99 percent acceptance rate among consumers. For better or worse, the grid that makes all this possible terminates at the end of the dock, and so does the seemingly endless supply of energy streaming out the end of a copper wire.
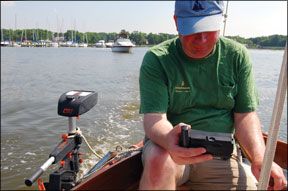
288
It’s true that big battery banks hold lots of current for consumption, but there’s an equivalent pay-the-piper reality when it comes to packing energy back into these batteries. Not alone do batteries not make any current themselves, but none are able to deliver 100 percent of the energy that is sent their way.
Even the most efficient batteries suffer energy losses due to the chemical reactions involved. They also have a percentage of loss that goes up with the time span between charging and discharging, their age, and the rate of discharge. At best, they behave like a water tank with a few small leaks. New Lithium-based batteries are more promising; solar panels continue to evolve; and fuel cells, which do create energy, are also a target for future development.
Unlike the federal budget, the energy balance aboard a sailboat needs to be maintained, or the lights go out. The bottom line of a DC electrical balance sheet begins with a simple tally of the amp-hours or watts consumed in a day. If this comes from a battery bank, add 20 percent more power to compensate for charge/discharge inefficiency.
Because electrical drive systems are both high consumers and are often linked to long run times, they dwarf the power demands of other high-current consumers such as an anchor windlass or bow thruster. The latter two devices have relatively short “duty cycles,” and much less power is used. The point here is that if you run the propulsion system on battery power, there needs to be a bilge full of batteries and willingness to put up with lower speeds and less range. If your sailboat harnesses a diesel electric drive or augments battery power with some charging assistance during the time spent under power, the range significantly increases.
Diesel fuel is an energy-dense liquid. Battery electrolyte would also qualify as the same if it didn’t require half a keel’s worth of lead to extract the potential energy. Some of the new battery technologies look more promising, but until we see more efficient solar panels, better electrical energy storage materials, or hull skin coatings that act like grease on the skids, coping with the energy needs of an electric drive will remain a very big deal.
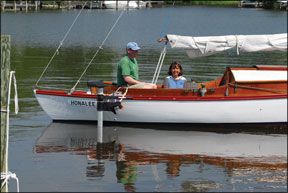
288
What we tested
The one scenario that currently works well for sailors, and definitely gets our nod of approval, is electrical propulsion for the daysailer or marina-to-marina cruiser. These are applications in which there’s both efficiency under sail and only a very modest need for a mechanical boost to cope with dead calms and getting into or out of a slip. In such cases, a 48- or 24-volt DC motor drive (inboard or outboard) can do the trick. Charging dockside while the crew sleeps, rejuvenates all involved. The next morning, there’s a refreshed crew and juice for another bout of powering.
In our effort to field test our own theories, we recently looked at a couple of new electric outboards, sea-trialed each unit, and compared them to the Torqeedo Travel 801 (T-801) that we’ve been long-term testing now for over two years.
Torqeedo T-801
In our original testing of the T-801, we saw both the merits and limitations of self-contained (battery and motor in one unit) electrical propulsion. The original work up was done using a Walker Bay RID 275, and the findings were upbeat about the thrust delivered at full speed, the near silent operation, and the handy portability of the engine. But the unit’s short run time at full speed and the snail’s pace (1.5 knots) of slow speed (the key to maximum range) left us with some ambivalence.
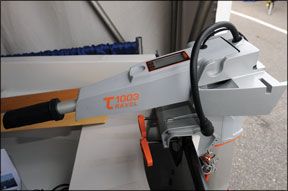
288
Since then, we have continued the testing aboard vessels ranging from kayaks and low-drag rigid dinghy hull shapes, to a 19-foot Cape Dory Typhoon and a 28-foot Herreshoff Rozinante yawl. The T-801 continues to operate reliably, no seal leaks at the prop shaft have occurred and the battery charge retention has decreased only by 5 percent. We haven’t broken any parts, and when the choice is between the Torqeedo or a gas kicker to get a daysailer out of the slip, the Torqeedo wins hands down.
In our testing, the T-801 pushed our 19-foot Cape Dory at a top speed of 4.2 knots and a the larger 28-foot Herreshoff Rozinante at 3.9 knots. This full-out speed test on heavy displacement boats eats up the battery charge in 15 minutes. The same full-throttle thrust with the Torqeedo clamped to a long, lean kayak resulted in 23 minutes of full-speed-ahead sprinting. The really encouraging news, however, is the 1.5-hour runs at 3 knots and how a dead slow boost to a sailboat can turn a flat calm afternoon into several hours of silent 3-knot motorsailing across a mirror-flat sea. Recharging the 10Ah/29.6VDC Lithium manganese battery is an overnight (eight hours) endeavor, and those needing more power can purchase another battery ($600) or opt for an adapter bracket that allows the unit to tap into a conventional lead-acid, AGM, or other 24VDC battery bank.
Torqeedo Travel 1003
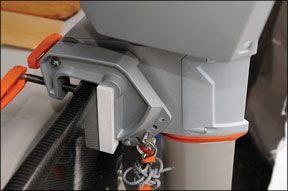
288
The new Torqeedo Travel 1003 is a significant upgrade to its predecessor, the T-801. With 30 percent more battery power, plus an increase in thrust and efficiency, the new unit is even more user-friendly. It’s rated as a 3-horsepower outboard, and the borderline flimsy plastic bracketing of the T-801 has been totally redesigned. A beefed-up, well-engineered bracket clamps the motor to the transom, and both the tilt adjustment and the battery support are more ruggedly structured. Instrumentation (charge level, speed, and GPS position) has been added and everything from the control handle to the cabling has been rethought. There’s also a second iteration of the T-1003’s double-screw transom bracket in the works. The location of the screw clamps on the original bracket did not extend as deep as necessary in some installations.
Our first demo of the new Torqeedo was on a light, round-bilged Wing Systems dinghy that literally leaped to life with a twist of the wrist. The efficient hull shape of the boat and the high thrust producing Torqeedo 1003 made it clear that electric outboards are here to stay. Instantly, this elegant rowing, sailing, or power propelled dinghy was nearly on a plane. The usual 4- to 5-knot gambol became a 7- to 8-knot quick-step, with promise of planing for the lightest of crews. Yes, such frolicking only lasts for 15 to 20 minutes, but there’s two hours worth of toodling at 3 knots and a dead slow range of about 10 miles in a flat calm.
Conclusion
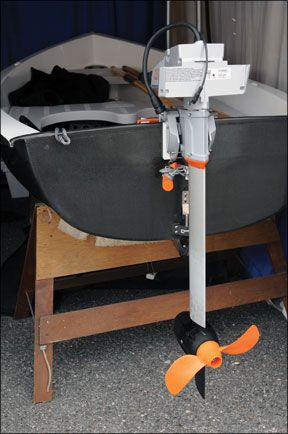
288
As with automobiles, energy efficiency has until recently been a backseat priority. Just try to row the average inflatable, even with a good set of 7-foot spruce oars and efficient oarlocks, which are unlikely to be present—the hull shape is hard to move through the water. These boats have been designed for stability and performance while on a plane, and to be pushed by an internal combustion engine with power to spare. The 4-horsepower gasoline outboard for the dinghy of the 1970s is a 9.9-horsepower today, and the crew usually wishes it held 20 stallions under the cowl. One reason why the T-1003 performed so well on the Wing Systems dingy is the efficiency naval architect Diana Russell designed into the hull. This is also why the boat is a pleasure to sail, and when oars are stroked you’re able to obtain progress as well as exercise.
A good part of the innovation behind the Torqeedo is the company’s look at the full spectrum of performance, from amps available to the prop’s behavior under varying load conditions. Recognizing early that static thrust was only one consideration, Torqeedo engineers looked at propeller behavior as it moved through the water column, not simply as a measure of bollard pull. Delivering more torque from a motor is an important part of adding speed, but some of the most substantial gains can be made with propeller efficiency, especially in the lower power end of the outboard motor world.
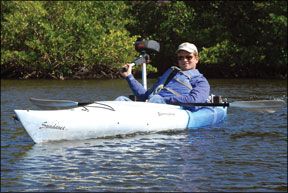
288
Many fondly recall the can’tankerous old Seagull two-stroke outboard that noisily fumed away and sported a motto promising that it was the “world’s most reliable outboard.” This claim was often debated, but what the unit did offer was a slow-turning, large diameter prop that was a thrust-producing marvel—a concept well understood by the commercial mariners. Efficiency is all about turning torque into thrust at a given boat speed. When planing becomes part of the picture, the paradigm changes: Cavitation, and ventilation become issues, and a new set of propeller dynamics come into play, but at lower speeds, large-diameter, slower-turning props still rule the day.
Electric outboards are a microcosm of the amps-for-knots effort, and big strides forward are being made. However, the pragmatist looking at dollars-per-knot, weight-per-knot, or range prior to refueling are yet to be convinced that it’s the right time to switch over. The rationale behind a conversion to electrical power still requires some less empirical reasoning. Perhaps it’s the recognition of air quality improvement linked to a move away from oil-based propulsion? Or for many, it’s the pleasure of silence extended into the powering part of a cruise that tips the scale.
I would love an update on this topic!