Seawater and electricity love each other with a fatal attraction, and when they break barriers to get to each other, we suffer from the destruction left in their wakes. Enter aerosol corrosion inhibitors. If you spray sensitive electrical circuitry&emdash;including printed circuit boards&emdash;with the aerosol rust inhibitors we tested, theyll prevent corrosion from interrupting circuits and water from creating circuits where they arent wanted. Our test lineup included Boeshield T-9, Corrosion Block, CorrosionPro Lube, CorrosionX, CRC Heavy Duty Corrosion Inhibitor, CRC QD, LPS 1, Strikehold, TC-11, WD-40. The TC-11 was our top pick.
****
With few exceptions, cruising sailors depend on electricity to maintain their on-board lifestyles within certain parameters of comfort and convenience. But this comes at a price, one that isn’t measured merely by amp hours. Seawater and electricity love each other with a fatal attraction of the kind that makes movie plots, and when they break barriers to get to each other, we suffer from the destruction they leave in their wakes. So, it’s not surprising that a thriving market exists in products designed to keep electricity and seawater apart.
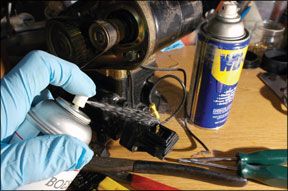
A survey of the maintenance aisle in your local chandlery will reveal several aerosol-applied coatings that claim to penetrate, lubricate, and protect electronic equipment, or prevent corrosion. Many offer to do all of these things. We selected 10 products, all of which make claims that specifically mention electrical equipment, electronics, and/or corrosion on their labels, then we set about testing how well they work.
Weve included some of the same products featured in Practical Sailors test of metal corrosion inhibitors (see PSApril 2007, “The Crusade Against Corrosion”), but we did not test Corrosion HD, LPS 2, LPS 3, or Shark Hide on the electronics. However, we did add Strike-Hold and CRCs QD.
In the April review, we tapped CorrosionPro Lube and CRC as being the best for metal protection. In the May 1, 2002 review, we favored CorrosionX MaxWax and CRC HD for metal protection, and Corrosion X and Corrosion Block to protect electronics and electrical equipment.
In general, the idea with these products is that if you spray sensitive electrical circuitry&emdash;including printed circuit boards&emdash;with them, theyll prevent corrosion from interrupting circuits and water from creating circuits where they arent wanted. And some manufacturers claim that their products “help restore” the functionality of electronic equipment that has been immersed in seawater.
A common characteristic of products marketed to inhibit corrosion or to protect electrical circuits is that they are dielectrics. Simply, that means they are insulators. When applied to a substrate, such as metal or a printed circuit, they form a thin film of insulator over its surface. Another property common to these products is that they bind to the substrate more closely than water does, by virtue of having either a lower surface tension or by a process called “polar bonding.” Either way, they physically displace water already in contact with, or prevent it from coming into contact with, the treated surface.
The high breakdown voltages of these products&emdash;from 20,000 to 38,000 volts&emdash;might suggest that they offer full protection to marine electronics operating at 12 volts. However, the ASTM D 877 standard by which these dielectrics are tested measures the voltage (alternating current at 60 Hz) at which the materials resistance breaks down between electrodes set 2.5 mm apart while immersed in the material (in its liquid form). Although the relationship between dielectric thickness and breakdown voltage isn’t linear (and for some materials gets weird at very thin layers), the fact that were working with films of thicknesses from a few micrometers down to, as some manufactures state, a few molecules, it follows that the applied potential differences they can withstand become quite small.
Also, it’s interesting to note that while corrosion protection and electrical protection rely very much on the same dielectric effect, how that protection is delivered affects how well the product performs either or both functions. The best corrosion inhibitors might not be the most suitable products for protecting sensitive electronic circuitry. Those with waxy films may attract dust and inhibit heat dissipation. Those with thin films that are gentler on integrated circuits may not withstand exposure to a hostile climate. Heres the lineup:
Boeshield T-9
According to its maker, Boeshield T-9 (http://www.boeshield.com) is intended to penetrate, displace moisture, lubricate, and protect from corrosion and rust. One of three products tested that have a waxy appearance, this popular spray is relatively heavy and dries slightly tacky.
We discovered corrosion at both battery terminals in the test radio (See “How We Tested,” above) and white deposits on the base of the antenna (which wiped off easily). There were also white deposits all over the inside of the radio&emdash;more on the connector side than the component side.
Bottom Line:
For the one-stop shopper, this product has the best combined “score” for corrosion inhibition (PS April 2007) and electrical protection.
Corrosion Block
Advertised as a product that prevents and inhibits corrosion (http://www.learchem.com/), this is a heavy, blue spray that dries thin and clear, but remains slightly tacky.
PS testers discovered some corrosion at the battery terminals and white deposits on the connector side, but less on the component side. This was the third cleanest-looking radio before our immersion test.
Bottom Line:
Another tacky customer, but also quite effective.
CorrosionPro Lube
West Marines CorrosionPro Lube claims to offer “excellent water resistance and superior rust and corrosive preventative characteristics,” and our test results bore that out. This product is delivered in a fine spray that leaves an amber-colored, waxy coating.
In our corrosion test, it remained intact through a weeks worth of freshwater dousing. We did notice corrosion at both battery terminals on the radio, and lots of white deposits on the circuit board.
Bottom Line:
Performed well with a sticky, waxy sheathing that should protect high-exposure areas.
CorrosionX
Developed to combat rust and corrosion, CorrosionX (http://www.corrosionx.com/)forms a foamy, blue-green film when it is initially sprayed on, but the bubbles eventually disappear.
This product was the second cleanest of the bunch, in testers opinions. The antenna and the entire interior circuitry were clean, though corrosion was evident on the upper battery terminals.
Bottom Line:
Quite effective at protection, but tacky to the touch. Recommended, except where circuitry needs to be handled.
CRC Heavy Duty
According to CRC (http://www.crcindustries.com/), the maker of CRC HD, this product is a “high-performance, thick-film version of CorrosionX.” One of the three wax-bearing products in our test, it comes out of the nozzle as a fine spray with some bubbles and an amber color.
After being submerged, this product appeared to have foamed, and though it looked better after drying out, it still left the circuit board messy. We found corrosion at both battery terminals, a clean antenna, but lots of white deposits on both sides of the circuit board. Nonetheless, this was still one of the most effective dielectrics.
Bottom Line:
A sticky, double-duty sheathing for those high-exposure areas, but take care it doesn’t inhibit cooling.
CRC QD
This aerosol is a petroleum distillate/alcohol-based cleaner. Its not sold as a dielectric corrosion inhibitor, but it does dry completely, and leaves no residue to retain water.
Practical Sailor
testers found corrosion at each battery terminal in the radio, along with lots of white deposits inside, especially near the on/off switch assembly. But the switch itself was less rusty-looking than most.
Bottom Line
: Use this as designed to clean electrical gear, and it may provide some protection in the bargain.
LPS-1
One of three corrosion inhibitors from LPS Labs, LPS-1 is a greaseless lubricant intended to displace moisture (http://www.lpslabs.com/). It is colorless with a broad spray range.
We found corrosion on all battery terminals, but a clean antenna. There were also lots of white deposits on the inside of the case, but the circuit board itself was quite clean except near the IC chip. The switch still had a positive “click,” but it was rusted and fragile. (This radio spent much time in surgery repairing the battery housing, during which the wires broke off. Although they were re-attached and the radio was working before it was immersed, it may not have been “hot” as long as the others.)
Bottom Line:
Questionable performance and concerns about interactions with rubber make this a doubtful choice for electrical systems.
Strike Hold
Developed expressly for cleaning and protecting military side arms, and first introduced to
Practical Sailor readers in November 2005, Strike Hold (http://www.strike-hold.com/) is marketed as a “fast-acting penetrant, demoisturant, and dry lubricant.” Its heavier than water, so unlike lubricants like WD-40 (http://www.wd40.com/), it wont float, but moves through the water to protect metal. The manufacturer claims that its harmless to plastic and carries a dielectric strength of 38,000 volts.
A problem occurred after spraying the radio with this product. It, or its solvent, softened the plastic body, and the springs that hold the batteries in blew the bottom off the battery compartment. (See “Are Plastics at Risk?”) For the record, the plastic used for the cheap radios we employed in our test is likely not used in more expensive electronic devices. The manufacturer subsequently sent us Strike Hold II (too late for this test), but even its “milder” solvent caused a Styrofoam nugget to shrink to half its original size&emdash;not a good sign given how many plastic and rubber compounds are employed in our marine electrical systems.
We also found corrosion at both battery terminals on the Strike Hold radio, and the antenna was white, but easily wiped clean. There was also a lot of messy residue on the inside.
Bottom Line:
Its appetite for plastic means we can’t recommend this product to protect electrical or electronic gear.
TC-11
The manufacturer of this product&emdash;ICC Industries&emdash;bills TC-11 (http://www.tc-11.com/) as “the best corrosion inhibitor…and penetrating oil on the market,” “…the most compatible multi-purpose lubricant,” and says that it “stops, prevents, and removes rust.”
Lofty claims, indeed, but PS testers found the TC-11 radio to be the cleanest of all. There was no corrosion at the battery terminals or the antenna, and the circuit board was generally free of the deposits seen on all of the others. It also has the most comprehensive instructions of any product we tested printed on the canister.
Bottom Line:
No messy residue, combined with effective performance, makes this our Best Choice for keeping electrical systems conducting.
WD-40
Almost as ubiquitous as duct tape, this product comes with marketing material that claims it “quickly dries out electrical systems to eliminate moisture-induced short circuits.” The manufacturer also claims that its safe to use on almost every surface, including plastic.
Our testers found that the battery terminals on the WD-40 radio were largely clean, as was the antenna, and apart from some rust-colored deposits around the IC chip, the circuit board was clean. Like all of the others, the switch was rusty, but it was by no means the worst-looking. There was certainly some degree of electrical protection, but not enough to prevent rusty residues of the switch from migrating across the circuit board.
Bottom Line:
Its better than nothing, so no harm done when you use this on electrical, rather than electronic, equipment.
Conclusions
After the radios were immersed and then dried, they were still damp inside. The products that cure the driest, like WD-40 and CRC QD, appeared to retain less moisture. The wax-bearing products (Boeshield, CRC Heavy Duty, and CorrosionPro) seemed to have foamed. They looked better after they had dried, but they were still messy. And each radio exhibited a bloom of rust around the on/off switch, which was damp. Evidently, the products that leave a moister coating hold onto the water longer, thus extending the period during which corrosion, whether electrolytic or galvanic, can proceed.
Sailors should learn from this to switch electronic gear off at the main panel when its not in use. Additionally, look for products with real on/off switches that isolate all other components from the power supply in case a user forgets to do that.
And, when using dielectrics, keep the following in mind: First, the instructions on the product labels are not always explicit. Some direct you to shake the canister, some don’t, even when the rattle in the can suggests that might be necessary, as with Corrosion Block or CorrosionX.
Of course, some of the results youll experience may be affected by the way the products are applied. The spray pattern might be wide or narrow, fine or foamy, and even when using the tiny applicator tube, surgical accuracy is not achievable. Also, a product might work best as a thin coating, but the topography of circuit boards might cause it to puddle, making more liquid products with good penetration properties better suited.
A coatings physical characteristics will influence where and how to use it, The waxy coatings&emdash;Boeshield T-9, CorrosionPro Lube (http://www.westmarine.com/), and CRC Heavy Duty&emdash;might be suitable for applications where coverage is more important than penetration, where the temperature wont cause them to run, and where youre not likely to be handling the treated parts. But you wouldnt want these in an area where theyll pick up dust, like inside the case of a PC thats cooled by a fan.
A product that is effectively dry to the touch might be appropriate in your switch panel and, if the equipment manufacturer recommends it, in and around electrical gear you might be handling.
And that brings us to an important point: Spraying the back of a fuse panel or the insides of a junction box where connections can be readily inspected is one thing. Spraying a device thats made up of printed circuits, IC chips, and other miniature components is quite another, and should not be done without the approval&emdash;preferably in writing and with specific instructions on how to do it&emdash;of the equipments manufacturer. Avoid getting these products near LCDs and membrane switches. Also, most will lift adhesive labels.
Judging by the general cleanliness of the radio, and taking into consideration the conductance test, TC-11 was the most effective product. Though it can’t prevent mixed metals from behaving badly in a saltwater environment when they have access to electricity, its still our Best Choice.
CorrosionX and Corrosion Block fared similarly on the conductance test, but the CorrosionX radio was marginally cleaner. Both form slightly tacky films, to which water actually clings. And Boeshield T-9 finished just behind these two. All three receive our Recommended rating, as do CRC Heavy Duty and CorrosionPro Lube.
I did a similar test with a number of products. I connected 12 eye terminals to a terminal strip, dunked it in brackish water, left it outside for a week, and measured the resistance and noted the corrosion. Petroleum Jelly was the best, followed by Corrosion X HD. All the others showed significant corrosion.