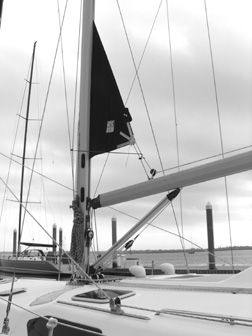
The most valuable advances in sailing hardware are those that achieve the dual goals of improving performance while also enhancing convenience. Think of the rigid vang, the ratchet block, and even some roller-furling units. Juxtaposed with the systems that predated them, these devices represent solid advances in equipment engineering.
However, some approaches to engineered convenience fall short of delivering improved performance, and that has long been the knock on in-mast furling systems. Three specific criticisms are most often heard: these systems add unwanted weight aloft due to the increased size of the spar section and its furling components; performance is compromised because the sails used in these systems are necessarily smaller than conventional mainsails due to the need to furl tightly (thus eliminating battens that would support greater roach areas); and the furling slots can whistle in strong winds.
Seldén Mast, Inc.’s in-mast furling system addresses these concerns in a progressive manner. The Sweden-based mastmaker refines its extruded aluminum sections ongoingly to achieve the optimum functionality as well as weight-to-strength combinations. The latest line of mast sections from Seldén—introduced in 2004—is being called NMP (New Mast Project). Though these spars are only marginally lighter than those the company was building previously (and certainly heavier than conventional spars not equipped for furling mainsails), they’re nonetheless a step in the right direction.
At the heart of this in-mast furling system is a patented device that evenly distributes the loads on all the stainless-steel bearings in the upper and lower furling units. Because these spars can be tuned to have up to 8 inches of pre-bend, making sure the furlers can rotate is critical.
According to Tom Sharkey, the general manager of Seldén’s U.S. facility, all of the spars and sections (spreaders included) that arrive for assembly are extruded from tempered aluminum. Each comes coated with 20 microns of anodizing, as do all the cast aluminum parts that get attached to the masts and booms—like exit boxes and winch bases, etc. These parts are also coated with a lacquer finish for extra protection. Nothing is welded to these spars as that would compromise the metal and require it to be retempered. Instead, everything is fastened with monel rivets or attached by stainless machine screws that are first treated with a coating of epoxy (thickened slightly with microballoons) to prevent any corrosion due to dissimilar metals.
We examined Seldén’s in-mast furling system on board a Hunter 460 in eight knots of breeze. This boat is fitted with a UK mainsail with no battens. To deploy the sail, you simply vang the boom down, release the mainsheet and the continuous furling control line, and pull on the outhaul. (For larger boats, the system is available with an electrical or hydraulic motor.) This boat is four years old, and it took us a couple of strong tugs to get the sail rolling, but it ultimately unfurled easily. We furled the sail back up, which took about six full pulls, and less than 15 seconds. When we unfurled the sail a second and third time, the system worked flawlessly.
Sharkey told us that the system can furl the sail with little friction even in strong winds while reaching. We found furling or unfurling the sail to be a simple, one-person task, and we like the idea of being able to reef the sail in such small increments.
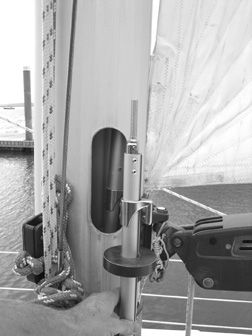
Should the continuous control line become fouled, there is a direct-drive apparatus affixed to the back of the spar just below the gooseneck as a back-up. This is a 2:1 gear mechanism that is driven by a winch handle. It has a locking switch on it that enables the user to choose between “free-wheeling” or “locked” modes. When underway in normal conditions, it would be kept on the “freewheeling” setting. If the boat were to be left untended for prolonged periods, moving the switch to “locked” means that the sail can not unfurl on its own.
But what about that criticism regarding sail size? A number of sailmakers have developed solutions to the problem of diminished mainsail area brought on by the inherent restrictions of in-mast furling systems. Doyle Sailmakers’ Swing Batten system is one, but Sharkey and his colleagues have recently been working with designers at Doyle-Ploch Sailmakers in St. Petersburg, FL, to develop sails with full vertical battens (with carbon tips for added stiffness) that both furl easily into the mast cavity and support additional sail area in the roach (see photo, above left).
Bill Durant, one of the designers responsible for many of the refinements on these sails, said mainsails can now have substantial area added to the leech, achieving up to 11″ of roach that projects beyond the erstwhile leech. His loft has built 70 of these sails in the last two years, so he feels they have the quirks worked out. That the sails are now standard equipment on Hylas Yachts is compelling evidence. And Hunter Marine, which outfits about 80% of its new boats with in-mast furling, appears to be following suit.
To ensure that the vertical battens don’t jam inside the mast cavity as the sail is unfurled, Seldén fits each spar with a guard just inside the mast slot. Additionally, the slot is off-center. This asymmetrical arrangement means that the sail will furl more smoothly on and off the foil.
Both Durant and Sharkey admit that these new vertical-batten mains don’t support as much roach area as mainsails with full-length horizontal battens, but they think it’s more appropriate to compare vertical-batten sails with others that can also be furled. “If you compare these new sails with those that have full horizontal battens,” said Sharkey, “then you also have to factor in the ease of operation, and that’s where in-mast furling is so appealing.”
So, what are the drawbacks? Cost, weight, complexity, and sail shape are crucial here. An in-mast furling spar and its attendant equipment sells for roughly 30% more than Seldén’s conventional spar. Add the increased cost of a sail fitted with vertical battens, and it’s a substantial difference. Selden is addressing the issue of weight and has minimized the complexity of its furling gear, but getting the optimum shape into a sail with vertical battens remains a challenge.
Contact – Seldén Mast Inc., 843/760-6278, www.seldenmast.com.