We’ve followed countless debates about the best engine oil and the right time of year to change it, as well as quite a few debates about oil analysis. Just as controversial is the advice on oil filters, which ranges from a blas recommendation to use whatever fits, to an adamant insistence to use only original equipment manufacturer parts (OEM). Because the oil filter is sealed in a cartridge, unless your filter leaks oil into the bilge we never actually know if it did its job or not. Given the filters important role, this is unsettling.
Google oil filter testing and you will find quite a few posts and videos where a mechanic has cut open automotive filters and commented on what he found inside. To be sure, there are differences in how the filters are constructed, but were not sure apparent sturdiness is good predictor of performance. In fact, our findings broadly refute that. Ultimately, it comes down to the execution.
Disposable spin-on oil filters are all most of us have ever known. They replaced a variety of screens and paper elements that fit inside fixed housings. Over the years, improvements were made, including anti-drainback valves and bypass valves. By the 1970s spin-on filters had become nearly universal.
There are still a few screen-types on smaller engines. Add-on bypass filters providing very fine filtration also have a limited following. Meanwhile, many small engines, including many outboards smaller than 20 horsepower, have no filter at all. For this report, we will focus on spin-on oil filters used on typical diesel auxiliaries.
Filter Failure Modes
Filters can fail in a number of ways, although most are not obvious unless you cut the filter open. Here are some common failure modes:
Channeling. Under high pressures, passages within the filter media passages can enlarge where unfiltered oil can pass through. Particles that were previously captured can be set free. This is one reason a bypass valve, which allows oil to go around a clogged filter, is vital. Most of the filters we examined have valves, and all appeared functional. They must be calibrated to the engine. A few engines have internal valves and do not require relief within the filter.
Fatigue cracks. Cyclic flow can crack the filter media, allowing a breach of oil to pass through unfiltered. This problem is more commonly associated with car engines that stop and go, rather than a marine engines.
Media migration. The filter media can deteriorate, shedding fiber. This can be caused by vibrations (poor placement on the engine), embrittlement from incompatible oils, and high temperatures (see adjacent article, Oil Analysius Finds filter Fibers).
Plugging. As intervals between draining the oil sump are extended, the filter media will eventually become plugged. Premature plugging can be caused by moisture, coolant leaks, and oil breakdown.
Corrosion. The shell can rust out, though with annual changes this is unusual. We saw very minor internal corrosion affecting a few spin-on fuel filters, but never used oil filters.
Dents. If the can is dented during installation, it creates a flex spot and may crack. Buy a wrench that fits properly. Oil the gasket before installing so that you can get it tight enough without excessive strain (typically turn after hand tight).
Bypass Valve Failure. Typically grit or metal shavings can cause jamming, the most common result being a collapsed core due to overpressure. We did not see any jammed valves or damaged cores in our samples.
Anti-drainback valve. There is an elastomers diaphragm in the bottom of the filter, intended to keep the filter full when the engine is off and prevent dry starts.
It is thought that silicone valve remains more pliable than nitrile; however, the only stiffened valve we observed was on an oil filter that was contaminated with gasoline when the fuel-pump diagram failure had released gasoline into the crankcase.
If the motor sits for more than a few days, the valves importance diminishes, as the oil typically drains back into the crankcase anyway, through the paper.
Filter Media Specs
How fine a filter should we use? Don’t rely solely on a single number. The point at which a filter plugs up or creates a severe oil pressure drop can vary widely. Appearances can be deceiving.
More media (created by adding more pleats in the filter or using a taller internal cartridge) may seem like a good thing, but only if the oil can reach the space between the pleats and if the filter media is of equal quality. In other words, a filter with only half the surface area, but more open area and better media may be superior. This is not a difference you can see without cutting the filter open and testing.
Additionally, even a small change in the efficiency can result in a large change in rating. The bottom line is that all of the filters tested had ratings close to 20 microns at 98 percent removal efficiency. Thus, we focused on observable failures, not specific ratings.
With regards to brands, as far as we know, all OEMs outsource filter manufacture. These same filter manufacturers typically market several lines of aftermarket filters. However, even from a single manufacturer, the quality and design of these products can vary from line to line and even from year to year. We did not try to track down the original manufacturers for each filter, and instead simply reported the name on the can, because it was impossible to be certain of the origin.
What We Tested
To learn what fails, sometimes its best to look at product that has been in the field, not new stuff. Although inelegant, we got most of our samples from the used oil-recycling site at a local marina. Some were collected straight from sailors or marine mechanics.
How We Tested
We sliced them open with a bandsaw and visually examined the interior. We looked for corrosion, stuck relief valves, stiffened anti-drainback valves, damaged filter material, poor end seals, and failed springs. Although we noted construction details, our focus was on actual evidence of failure. In all, we cut open 61 filters, all from boats.
Observations
Despite their many common elements, the oil filters in our comparison had many significant differences.
Bypass Valves. Most filters have bypass vales, but some do not, relying on pressure relief within the oil pump. Because the valve and setting must match manufacturer specifications, do not just use any filter that fits. For example, although hydraulic or fuel filters may fit your diesel engine and have a similar micron rating, they do not have internal bypass valves.
Springs. Many filters have a coil or Bellville spring to maintain a seal (see adjacent photos). Some experts swear by coil springs, and regard Bellville springs, which resemble flat washers, as a cost saving measure. However, several of the highest quality filters do not use a separate metal spring at all, relying on the elastomers in the anti-drainback valve to provide compression. This design choice allows more room for filter media. None of the disk springs showed any signs of weakness, nor was there any evidence that filters without springs had allowed oil to bypass the filter media.
Anti-drainback valves. These valves prevent the oil from draining out of the filter. Although silicon is sometimes touted as superior, all of the valves remained pliable, except for one Sierra filter that had been highly contaminated with gasoline (we did not consider this a failure since the filter was not designed for exposure to gas). Additionally, no filter will hold oil for more than an hour or so, because it will drain through the filter media.
Endplates. Quality filters can be constructed using any endplate material. In fact, the Yamaha and Honda filters omitted the end caps entirely, bonding the media to itself to form a seal.
Although metal endplates are sometimes touted as superior, bonding filter media to metal is not always reliable. In our sample field, we found that the metal end caps on Sierra filters frequently came loose. Bonding porous paper to porous paper, on the other hand, is easy and reliable. On the Yamaha filter, for example, the top and bottom of the cylinder-shaped filter media is well-sealed with resin (see adjacent photos). We could not wiggle the smallest pick into seams.
Several manufacturers use molded rubber end caps as both seal and support. Fram end caps, on the other hand, are made of a weak fiber material that becomes friable over time. Other manufactures fiber end cap materials are far stronger and more durable.
Fiber Shedding. In many filters, as the engine hours increase (as inferred by dirty elements and dark oil), the surface of the filter media softens and fibers shed more easily. To a trained professional, this is readily apparent by viewing oil samples with a microscope.
Product Notes
We evaluated too many oil filters to review each one, and this would be of little benefit since most of the filters showed little signs of aging after a season of use. Most of the filters were well constructed, and after a season of use were just dirty.
Only two brands revealed failures, and these failures were repeated at a high rate:
Fram
The end caps were made of a weak cardboard-like material. Often the end cap material was crumbing, and in several cases, was tearing loose from the ends of the media. These same failures have been reported in the automotive press.
Bottom line: Fram filters are not recommended.
Sierra
The fuel filter samples all looked good. But apparently the heat or chemistry of used oil is not compatible with the adhesive used to attach the metal end caps. As a result, almost 60 percent of the samples we examined had at least one loose end cap, and in several cases, there was insufficient resin or the resin had cracked. Because a leak in an endcap can allow dirt to bypass the filter, this is a failure.
Bottom line: Sierra filters are not recommended.
Conclusions
Because filter fibers were the most common contaminant in used oil sludge samples, and because shedding increases with age, we recommend changing the oil at a conservative interval and never longer than one year.
You can’t necessarily judge a filter by its features. A coil spring may seem better than Bellville spring, but we never saw a spring failure and many top brands lack any spring at all, yet perform well. Metal end caps seem sturdy, but if the bond between the metal and paper fails, they become a vulnerability. All of the pressure relief valves appeared functional. Anti-drainback valve performance appeared to vary, but its hard to judge and probably not that important on boats.
The most important finding regarded Fram and Sierra oil filters. Both brands failed multiple times in ways that allowed oil to bypass the filter. However, this is not a blanket rejection of all after-market filters. Baldwin, Fleetguard, Mobil 1, K&N, MOPAR, Motorcraft, Puralator, and Wix all make OEM filters, and based on our research their aftermarket filters match or exceed OEM quality. None of the OEM filters that we examined showed sign of failure.
While we were digging into oil filters, we also cut open quite a few fuel filters. But that is the stuff of a separate report.
Finally, remember to recycle. There is good scrap in used oil filters and a landfill is the wrong place for used oil. However, in order for a used oil filter to be classified as recyclable scrap metal instead of regulated hazardous waste, it must be hot drained in the appropriate manner. Not one of the discarded filters that wed collected for testing was properly drained by puncturing either the dome end or anti-drainback valve.
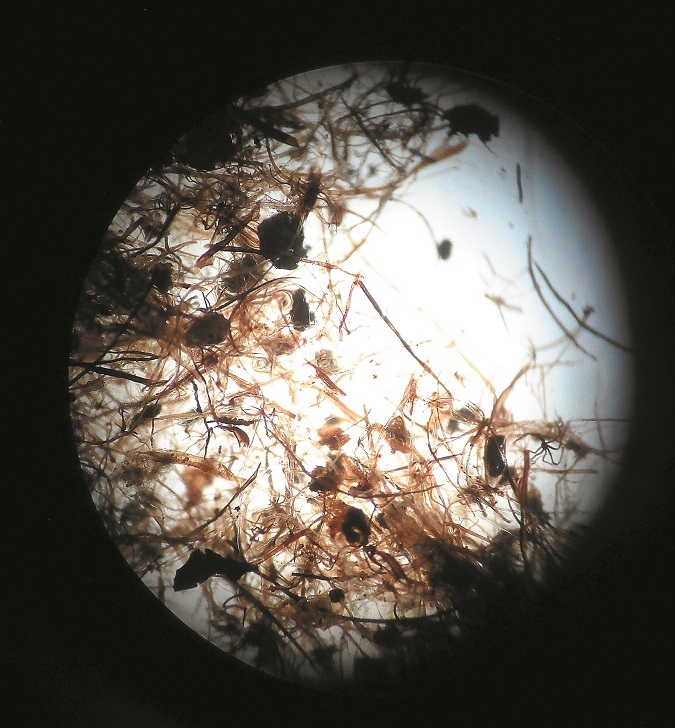
This photo of sludge from a used oil recycling plant gives some interesting clues about what really happens in used oil filters. Heavy sludge settles in storage tanks. The oil is then filtered through 200-mesh stainless steel screens. We rinsed the resulting sludge with mineral spirits to remove very fine material, such as carbon black, and soluble materials such as asphalt. Curiously, what remains, has relatively unchanged in our testers 35 years of experience with the industry. Interestingly, we found a lot of plant debris, the result of engines sucking in a lot of air. But mostly, it is fiber shed from the filters, many identifiable as common cellulose and synthetic filter media.
Its not a huge volume, only about 0.1-0.3 gram per vehicle. Can these fibers cause damage? They are not abrasive, like iron or silica particles. They can plug oil distribution passages. But most importantly, since shedding increases as the filter becomes older, its one more reason not to postpone that oil change.
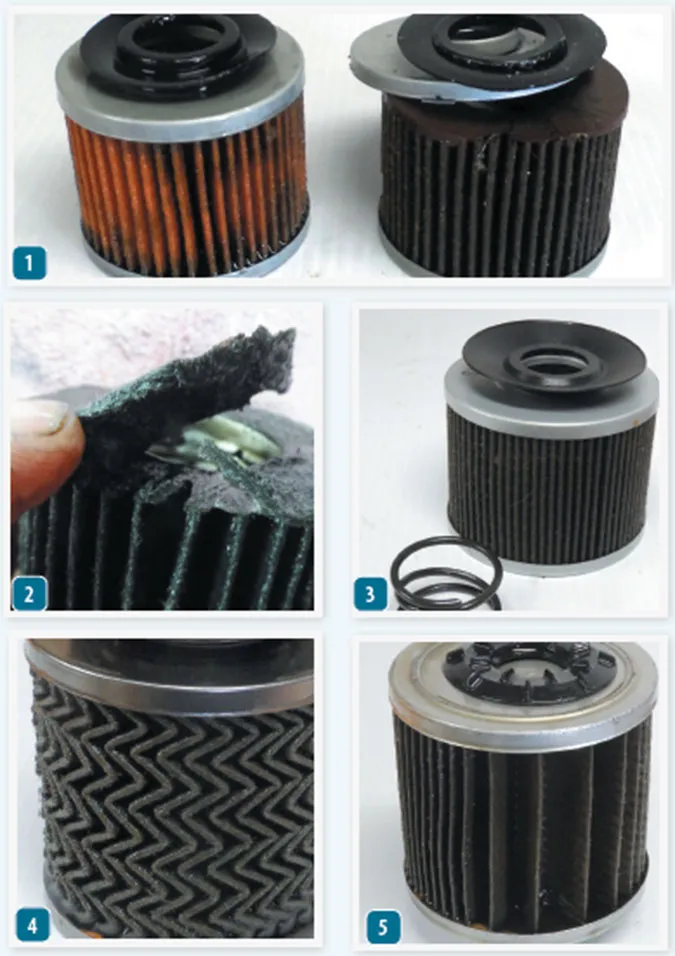
To learn what fails, sometimes its best to look at product that has been in the field, not new stuff. We got most of our samples from the used oil-recycling site at a local marina. Some were collected straight from sailors or marine mechanics. Although we noted construction details, our focus was on actual evidence of failure.
- After final examination, it became clear that Sierra oil filters were failing. On 2/3 of the samples , at least one end cap came loose. In some cases, these cracks and insufficient resin allowed oil to bypass the filter media.
- Testers also noted failures in Fram oil filters such as this one, in which the end cap is peeling away.
- Yanmars simple Bellville spring system worked well, and testers found no failures at the end cap.
- The pattern of pleats on the Volvo filte was unique to its filter.
- The Kubota diesel filter stood out from others because of its wider pleats.