The first sign of cordage use dates back about 28,000 years. Archeological findings in Europe have carbon dating confirmation of twine imprints found in clay shards. The Egyptians (circa 4,500 BC) appear to be the first to utilize rope-making tools, and for millennia, natural fibers such as hemp, manila, sisal, jute, cotton, and others were the material of choice when it came to making laid or twisted rope.
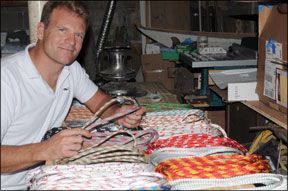
Photos by Ralph Naranjo
The playing field changed in 1935 when DuPonts young research director Wallace Carothers and his team came up with a synthetic polymer dubbed nylon, a fiber that soon found its way into stockings, toothbrushes, and the capable hands of rope manufacturers around the world. Polyethylene terephthylate, another long-chain polymer, was synthesized in Britain in the 1940s, and eventually found its way into the DuPont lineup as Terylene in 1951. Terylene was rechristened Dacron, and the new polyester fiber soon joined nylon on the rope walks of cordage manufacturers around the world.
Dacron proved to be much less stretchy than nylon, 90 percent as strong, and more resistant to ultraviolet (UV) rays. Nylon and Dacron grew to be nautical buzzwords indicative of the rope of the future, at least up until chemical engineers with post doctoral degrees and ample grant dollars got serious about conjuring up new fibers. Today, Spectra, Vectran, Technora, and a whole host other tongue-twisters are the new, new thing in fiber technology. Truly stronger than steel, and 10 times lighter, they offer much less stretch and double or triple the tensile strength of the synthetic prototypes nylon and Dacron. Unfortunately, some also have inherent downsides such as reaction to UV, creep (permanent deformation under stress or heat), and the reluctance to be wrapped around a tight radius.
Fiber to Rope
For centuries, cordage was made in a time-honored tradition that began with fibers being spun into yarns, twisted together into strands, and finally twisted again in the opposite direction combining the strands into a rope. The opposing twists locked the bundle in place, and when tension was added to such three-strand laid ropes, the yarns torqued and rubbed against one another in response to elongation.
When it comes to making running rigging aboard sailboats, laid rope takes a back seat to braided line. The 26 samples of rope we evaluated for this test, all fall into what can be called braided rope. We looked at 24 ropes with braided covers that comprised eight, 12, even 24 tows combined in patterns ranging from loose to tight weaves. Most incorporated a braided core, although a few ropes had parallel-strand cores. Two samples of Amsteel, a single-braid rope, were included in the test for comparative purposes. By doing away with most of the twist involved in laid rope, braided lines tend to have less stretch, and the fiber bundles can be better aligned with load paths.
In early Dacron braided line, the tensile strength was usually evenly distributed (50-50 split) between the cover and core. Todays crop of high-tech lines often favors an uneven load distribution between the cover and the core. One example of this approach is found in a type of braided rope known as kernmantle, which comprises a braided cover and a high-tensile, parallel-strand core. In this design, the tensile strength is often split 70-30, with the core carrying most of the load. Such load sharing means that even when abrasion has jeopardized the outer cover, the cordage still retains most of its original tensile strength. Mountaineering rope-just like anchor and mooring line-can be engineered to retain such a cache of tensile strength in the center.
The flip side of this approach, however, is that once the cover of a sheet, guy, or halyard frays, it is time to replace the line regardless of how much tensile strength is still left deeper in the core. So cordage manufacturers have been engineering braided rope comprising a tough, abrasion resistant cover and a core that meets the required tensile strength. In addition to careful selection of cover fiber, engineers have turned to anti-abrasion urethane coatings that reduce the damaging effects of abrasion, UV, and acid rain. In this round of testing, testers directly measured the abrasion resistance of each line, tested its resistance to stretch and observed how it coiled, handled, and behaved on a winch drum. (See “How We Tested.”)
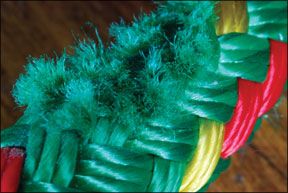
A Note on Breaking Strength
Breaking strength figures listed in the above table are astounding and represent the end of the line both figuratively and literally. At that point, the line has elongated as far as its elastic and plastic limits allow, and when it exceeds its yield, the result is an explosive bang. According to the Cordage Institute, the rope industrys amalgam of technical gurus, safe working loads (SWL) are five to 12 times less than the breaking strength for non “lifeline” uses. When used as a safety line, the SWL is calculated by dividing the breaking strength by 12 or more. The reason for this seemingly hyper-conservative safety margin is because shock loading can cause the static tensile load to skyrocket, and there needs to be plenty of safety margin to compensate for these momentary spikes.
What We Found
With so many lines to consider, we grouped the products by material and construction, more or less keeping the apples, oranges, and bananas in separate boxes. We began the process by sorting the rope into three fairly distinct performance groups (low, mid, and high tech) based upon their fiber content. Once sorted, the ropes were evaluated for their elongations, abrasion resistance, and handling. Results are tabulated on the pages above.
There were similarities among the types of ropes manufactured and marketed by different companies. For example, each offered a polyester double braid that afforded excellent UV stability and handling characteristics at a bargain price. However, these lines were also the most prone to elongation under even modest working load, and were poor candidates as halyard material.
Testers confirmed that high-modulus fibers and new coating treatments do enhance performance traits in rope. Theres no question that fibers such as Technora, Dyneema, and Vectran boost the breaking strength of rope and lessen stretch, but theres also a flip side that needs to be taken into consideration. Many of these fibers have an inherent stiffness and tendency to hockle that makes them hard to coil and handle. Notice that many of the higher performing ropes scored low for handling.
Whether you should make low-stretch or easy-handling a priority will depend upon the ropes application. A conventional all-Dacron 7/16-inch halyard may easily have 60 feet of its length in tension, and with normal sailing conditions, halyard stretch could be as much as 16.4 inches. Swap out the all-polyester halyard and replace it with a high modulus, 3/8-inch diameter rope such as Yales Maxibraid Plus and the stretch is reduced to 4.1 inches.
This four-time reduction in elongation makes a big difference in mainsail draft control. The last thing a crew wants is more draft in the mainsail just as a gust fills in. The bottom line when it comes to halyards is that its worth putting up with a line that coils like a tree branch, if once it is winched into place, it resists elongation as well as wire.
Sheets on a cruising boat are quite a different story. Most short-handed, long range passagemakers arent obsessed with continuous trimming and turn the drudgery over to an autopilot. Sail trim consists of an occasional look at sail shape and telltale behavior. Eliminating the last bit of stretch in a sheet is of little advantage, but having a line that can put up with the abrasion, UV harassment, and the fatigue that adds up during days, or weeks at sea is a vital asset. Handling ability is another key factor, especially with so many lines leading to the cockpit. A halyards can’tankerous demeanor is tolerable, since the rope is effectively a set-it-and-forget-it one-act play. But sheets are handled more often, and easily coiled tails are always appreciated by every crew.
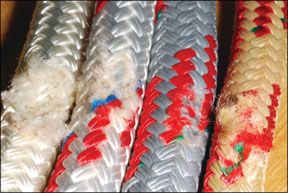
Top Picks
Ultimately, when all the stretching, abrading, and coiling was done, testers were able to find some clear choices based on price range and offer some general guidance for those who are shopping for new cordage.
Budget ropes: At the low-tech and lower cost end of the spectrum, Samsons SLX 456 nudged ahead of competitors. Yales Yacht Braid, New England Ropes Sta-Set and Novabraid XLE were all high- quality polyester double braids. Each made the grade as an easy-to-handle general purpose cordage, but none was optimized for use as a halyard material. The reason Samson SLX topped our list was its superior showing in the abrasion test, a feature of its cover construction and proprietary coating process.
Sta-Set X by New England Ropes took polyester cover-and-core technology to a higher performance level, keeping the price down but sacrificing some handling ease and abrasion resistance in the process. The cover has an odd feel, and coiling is not as easy as with the other all-polyester products, but stretch has been reduced significantly and tensile strength was upped by 10 percent or so. This has been accomplished through the use of parallel yarns in the core. The bottom line is that this is an all-polyester line that can be used as a halyard, and it retains the price-point advantage found in all polyester ropes.
Mid-range value: Five of the products we tested are grouped as mid-price, mid-level performers, and the stats speak for themselves. Our favorite in this grouping was New England Ropes VPC. This line isn’t as nice to handle as the all-polyester braids, but it has 50 percent less stretch, superior abrasion resistance, and a price that is half that of the top contenders. Yales Vizzion rated a solid “Good” across the board but had a lower breaking strength. New England Ropes T-900, a low-stretch and high-tensile strength alternative, was especially stiff to handle, and its smaller-diameter 5/16-inch version was more prone to cover abrasion. Samson entered a larger 7/16-inch diameter sample of XLS Extra-T, and even with the extra diameter advantage, its stretch was greater than VPC. However, this tuned-up XLS has many excellent attributes. It slips onto and grips a winch drum nicely and handles very well, making it an excellent choice for sheets-if you can handle the extra expense.
Big bucks for the best:The skys the limit at the upper end of the cordage range. In fact, rope made with esoteric PBO (Zylon) is so costly that we left it out of our evaluation altogether, calling the game at line that pushed to $4 foot in the discount houses. In this grouping, we find rope with the highest breaking strength, the most cover abrasion resistance, and the least stretch. Evidently, you do get what you pay for when it comes to cordage. The reason New England Ropes Endura Braid and Yales Maxi Braid Plus topped our list was that they delivered the three features mentioned above, but also garnered high marks for handling.
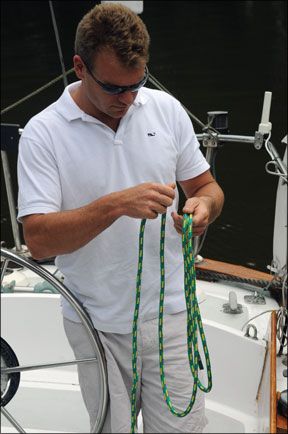
Samsons Amsteel was hard not to like. The 15-foot section of 5/16-inch single braid Dyneema took abrasion testing in stride, was soft and supple, weighed in at just 5.5 ounces, and had little more bulk than a handful of shoelaces. Yet it was strong enough to support a pickup truck with a couple of J/24 keels in the bed. The downside was how the all Dyneema line behaves on a winch drum. Its lubricity or slipperiness combines with a coating that glazes under pressure, creating a line thats difficult to set and ease on a winch drum. Despite this complaint, it makes a superb halyard-just use a winch with a well-textured drum face. Its also worthwhile to keep a good supply of this line in the damage control kit, for emergency lashings and jury-rigging.
Conclusion
The least surprising verification from our testing was the inverse relationship between stretch and cost. Esoteric, low-stretch fibers come with a higher price tag, and the old saga of paying more for performance played out in spades. However, the real surprise came when PS started looking to fill in the “street” prices for specific products. Searching West Marine, Defender, Mauri Pro, PYacht, Jamestown Distributors, Boat Locker, and a few other sources, testers discovered a wide range in discounted prices per foot. In some cases, there were 60-percent variations for the identical product. The figures in our table serve as a good guide, but smart rope buying is most certainly a shop-around enterprise.
Dont buy more tech than youre going to put to use. From our perspective, it makes sense to invest a little extra in a good mainsail halyard. Unless youre a hard-core competitor, the genoa that rides in a roller-furler luff grove doesn’t need as much no-stretch chemistry. When it is blowing hard, and the jib is partially furled, the load dynamics spread out to the entire foil headstay and halyard, and some luff sag is expected. Those who still fly a conventional spinnaker will love the reduced stretch of high-tech cordage in an after guy. Lighter weight, no water absorption, and smaller diameter light air sheets can also improve ghosting performance. A lightweight mainsheet with good handling characteristics and a low desire to twist can also be worth the investment.
In short, the polyester double-braided lines are like hubcaps over steel rims-just plain practical. Ratchet up to lines with less stretchy fiber blends in the core, and youve arrived at an all-around good compromise. For those who don’t choke on the $3-per-foot pricetag for hundreds of feet of line, there are spools of great technology just itchin to make sailing faster, easier, and more costly.