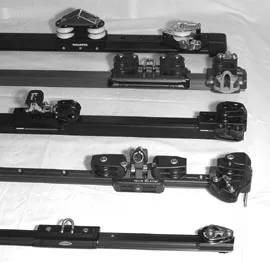
A dozen years ago, in the July 1993 issue, PS reported on mainsheet traveler systems. Though we’ve kept up with developments in this realm during the interim, we haven’t offered a comprehensive evaluation of these important sailhandling systems since then. The time has come.
Properly installed and functioning mainsheet travelers are versatile devices, offering sailors a number of key advantages over simple mainsheet rigs traditionally used aboard sailing craft. These newer systems permit you to sheet to windward in light air to enhance your vessel’s pointing ability; they allow you to depower the sail in puffy conditions without touching the mainsheet; and they enable the mainsheet to be substituted for a vang when sailing upwind.
In that earlier article, we listed four reasons why mainsheet traveler systems are so appealing: “almost frictionless cars,” “modular system components that let you lead the mainsheet and control lines in virtually any configuration,” “installation so simple even a child can do it,” and, “almost unbelievably low prices.” Those observations also apply to today’s mainsheet travelers, and equipment evolution in the intervening years has rendered the bulk of these products even more efficient.
What We Tested
PS gathered products from five of the six companies most recognized for fabricating or selling this kind of sailhandling equipment for midsized boats in the U.S.—Antal Marine (represented in the U.S. by Euro Marine Trading), Harken Yacht Equipment, Lewmar, Ronstan, and Schaefer Marine. The sixth, Garhauer Marine, opted not to send us a traveler because the company is in the process of introducing a new system that wasn’t available in time for our test. (We’ll evaluate that in a future issue.) Two other companies were considered—Frederiksen (now part Ronstan), which did send a car and track for a smaller size boat, and Rutgerson, of Sweden, which wasn’t able to provide products in time for our test. (We’ll also examine that later.)
From each company we requested a section of track, a car appropriate for that track on a sailboat 34 to 36 feet LOA, and equipment for a 4:1 control line. The track, we told them, should be four feet long and would have to span a 28-inch opening (as in a cockpit footwell or companionway application), unsupported. We will note here that those travelers set forward for mid-boom or three-quarter-boom mainsheet arrangements are thought to be subjected to greater loads than those set up for boom-end sheeting. Each of the manufacturers whose products we tested offer guidelines for various applications, including working load limits, and buyers should take care to purchase a system rated for their intended application.
Test Methodology
For this test, instead of fitting our specimens to an actual boat, we built a jig to evaluate several parameters. We initially wanted to quantify how much force would be required to move the car along its track if the attached 4:1 mainsheet were under a 400-lb. load. We also wanted to know how much each manufacturer’s track would flex in this application. We also closely examined each unit with the following areas in mind: electrical isolation, sliding smoothness, track strength, flexibility of mounting, car control, mainsheet block attachment and support, center of effort angle (see sidebar), instructions, form and fit, and cost.
Each traveler system was secured to a 2 x 6 board on our jig using four points of attachment. We used a varying array of fasteners as required by the design of the track (some require countersunk machine screws and some hex-head bolts).
For our initial experiments regarding side force, we mounted a spare track and traveler car at the top of our jig and attached a Dillon dynamometer to it. The mainsheet purchase from the car and track under test was led up to the dynamometer. We put the mainsheet under a load of 400 lbs. and led the 1:1 traveler control line outside the jig via a hole bored in its side to a spring scale (see photo at right). Then, by way of repeated pulls, we quantified the force necessary to pull the car along the track. We learned early on that the force required, given this configuration, was almost inconsequential. In most instances it didn’t exceed 12 lbs. to start the car rolling, and once rolling, the force required to pull it was much less than that. This, we surmised, is a testament to the engineered efficiency of the bearing systems used in these travelers.
Then, using the dynamometer, we led the mainsheet to a point 16 feet above the traveler and forward by about three feet. This, we felt, would simulate the force vector, (but not the exact force) exerted on a traveler car with the mainsail let out on a close reach, essentially introducing a torsional component to the load. We then resumed our pull tests using the spring scale and learned that for all but one of the units we tested, there was little difference in the force required to move the car along the track.
To gauge track deflection under load, we led the mainsheet to a fixed point on the upper support of the jig, and using the dynamometer to measure, we again applied 400 lbs. of upward force with the purchase system. Using digital calipers, we gauged the deflection, first measuring the position of the tracks when unloaded and then when under load.
As a final evaluation, we attempted to determine smoothness by sliding each car back and forth on its track by hand through multiple cycles. Using this method we determined a ranking for that car and track assembly that seemed most smooth, and judged all others against it. This aspect of our test relates more to elegance of design than function, but a product that works more fluidly is likely to function well for a longer period of time than one that’s susceptible to binding or increased friction.
What We Tested
Antal Marine’s 4113 traveler car ($652 including toggle) is milled from aluminum that is hardcoat anodized. The 4510 track ($140) is anodized as well. The system is rated for boats up to 36 feet LOA. Interestingly, we noted that this car represented the lone product in our test that is assembled with its aluminum parts isolated from its stainless parts by way of nylon bushings or washers. Galvanic corrosion with these products can occur when the anodized layer is compromised (through scratching, or cracking, which might be brought about by over-tightening a stainless fastener). This is a small, but important aspect, indicative of Antal’s attention to detail.
This car is also the only one in our test that utilizes two races of ball bearings to resist friction along the track. The lower layer bearings are Torlon balls, where the highest loading exists. The top bearings are Delrin. The car rides along the track with the bearings making contact with the track in two grooves. The lower groove with the Torlon balls sustains the upward forces, while the top groove with the Delrin bearings comes into play with side or torsional loads. This car prevailed in our smoothness test, principally because the second layer of bearings allows it to roll with minimal friction when under a torsional load. An additional feature we like is the fact that the car’s end caps are engineered in such a way as to keep the car on the track should the ball bearings fail.
The company engineers the system with an access port on each side of the car so that the bearings can be removed from the races and replaced simply by backing out a stainless Philips head machine screw. Three cars in our test allow the user to remove the bearings without taking the car off the track, and this one is the easiest. We think that facilitating this operation will promote better maintenance over time.
The toggle attaching the mainsheet block is fashioned from a bent stainless steel plate that surrounds a thick phenolic rubber bushing, which controls and buffers the fore and aft movement of the support. This toggle plate is connected to the car by way of a 7/16″ stainless steel pin. The car was fitted with double blocks for the control line (4740 $147 each).
Antal offers either plunger stops for this system, or 1:1, 2:1, 3:1 or 4:1 stackable control sheaves. Additionally, cam cleats can be mounted either at the track ends, or on the car carriage itself. The 4250 control sheaves ($184 each) Antal supplied are milled from aluminum and hardcoat anodized. They mount on a rectangular channel that fits over the track and has a soft but resilient urethane pad (4280 $11 each) to cushion the impact between car and end piece. On top is a broad aluminum plate with holes bored in it for the servo cam cleat (4410 $77 each) to be positioned at one of three angles. The only drawback of this assembly is that the channel piece has two lengths of stainless steel threaded rod set in it for securing to the boat, but these can’t easily be removed.
In our tests, the Antal track experienced the greatest deflection, but we acknowledge that it’s not meant to run unsupported across any expanse, and should be fastened every four inches via the pre-drilled holes. Euro Marine Trading told us the track should be installed with a support member like a stout section of teak to aid it in spanning any space.
Euro Marine Trading didn’t send any instructions with its traveler system because the company doesn’t ordinarily sell direct to the end user, but usually supplies its travelers to riggers for installation. Nonetheless, there’s nothing complicated about installing this system except that the cars are shipped on a short piece of loading track and installers must be careful to slide them onto the track without losing the bearings, because they are not captive. This system, with all its parts, can be purchased whole for $900.
Harken Yacht Equipment in Pewaukee, WI, offered its 1618 high beam track ($108) with a 1627 car and toggle ($196.30), and 1633 double sheave control end fitting with cam cleat ($265 each). These parts are rated for use on boats up to 34 feet. The track, car, and end fittings are all milled from aluminum that is thereafter hardcoat anodized. The track comes with eight rectangular washers (Harken calls them “bolt slides”) intended to fit over 1/4″ mounting bolts and slide into a channel in the bottom of the track (see photo pg. 14). The advantage of this approach is that the fasteners can be placed wherever it’s most convenient and appropriate, but Harken recommends spacing them no less than 4″ apart, with two on either side close to where the span begins.
The car rides along the track on recirculating Torlon ball bearings that are held captive by twin stainless steel clips so that the car may be removed from the track without worrying about the balls dropping out. The clips are made from 17-7 stainless that is heat-treated to improve strength. Having captive ball bearings is a handy feature for installation and we think it would enhance maintenance as well. With the car removed from the track, the bearings can be snapped out of the races one at a time if they require replacement, and new ones snapped back in. Harken’s car is the only one among those we tested that is engineered in this way.
To achieve the least friction, the Torlon balls bear on grooves in either side of the track. Harken’s advertising touts the car’s low-profile design, which means that the pivot point of the toggle attachment isn’t far above the surface of the track where the bearings sit. In fact, Harken’s car has the lowest center of effort angle (see sidebar) of all those PS tested, which means that it has a very efficient load transfer under side loading. This takes place when the boom is anywhere off centerline.
Though Harken’s car has end caps that will tend to keep it on the track should the bearings fail, these are not as large or as close-fitting as those on the Antal and Lewmar cars.
The 1627 car is fitted with a stout, stainless steel toggle to both support and connect the mainsheet blocks. This toggle is investment cast from stainless rather than bent out of a plate, but not unlike the Antal toggle, it surrounds a durable urethane support bushing that also limits and buffers the fore and aft travel of the toggle. The toggle has “ears” on either side which are formed to accept stainless steel clevis pins where control blocks (2638 $49.80 each) can be attached. Harken claims that attaching the controls to the toggle instead of the car reduces the loads on the car.
Harken’s 1618 track experienced the least deflection of all the ones tested, though it was essentially in line with that measured on Lewmar and Schaefer’s tracks. This track lacks the holes that would enable it to be fitted with pin-stop controls, though the company does offer those for this size traveler. It also offers single or double sheave control ends fabricated from its patented Carbo material, or single or double sheave controls built of stainless sides. These control units sit on an anodized aluminum base and mount with a single screw fastened to the track, so there’s no need to bore additional holes in the boat.
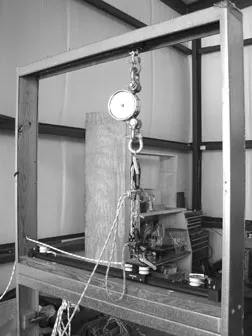
Harken also accompanies its products with detailed diagramed illustrations that enable DIY owners to install the equipment without confusion. And Harken is one of two companies that also sells its traveler system in kit form (car, control blocks, and end fittings), minus the track. The system we tested lists for $933.90.
Lewmar is revising its mainsheet traveler systems, and the new system is described by the company as an amalgam of the old Ocean and Racing systems, which are still available. The company sent us its track 29162315 ($114) and 29432300 car ($212), fitted with two double control line sheaves 29172012 ($65), and two end fittings 29472836 ($129 each). Each end fitting consists of an anodized aluminum base with two nylon sheaves, a Ronstan cam cleat, and a cast stainless becket. All these parts are rated for use on boats up to 36 feet.
The car body and end fittings are milled from aluminum and thereafter hardcoat anodized. The track is extruded and mounts in the same way as Harken’s, with 3/8 hex-head bolts meant to slide into a channel in the bottom of the track. Lewmar specifies mounting the bolts on 4″ centers, with at least three mounted on either side of the span. The bolts are to be mounted with washers underneath their heads, and washers should also be set underneath the track for each bolt. No fasteners were supplied, but the equipment arrived with the car already on the track and the end fittings in place as well.
Measuring 3.43″ wide by 1.56″ tall by 8.25″ long, Lewmar’ car is the largest one we tested. It’s nonetheless a low-profile car, which utilizes recirculating Torlon ball bearings that ride in grooves on either side of the track. The body of the car is complemented by twin tubes that contain the ball bearings as they rotate back toward the track, and twin end caps, which can be removed to service the balls. These end caps are also milled from aluminum alloy. On top of the car, six holes are tapped to accept the bolts that thread through the control sheaves and affix them to the car. The outermost holes on either end of the car are fitted with stainless inserts so that galvanic corrosion will not seize the bolts over time. PS wondered why the other two holes hadn’t been treated in the same manner. Lewmar does coat the bolt ends with a synthetic lubricant before assembly as a protective measure against seizing. The control sheaves themselves are made of a hard nylon and turn on bushings rather than bearings.
The mainsheet attaches to the car by way of a stout stainless steel D shackle contained by a pin held captive inside the car. (Lewmar also offers a forged stainless steel toggle not unlike the one on the Harken car.) The shackle articulates fore and aft, and twin urethane pads attached to the car keep the shackle from banging into and damaging the aluminum.
Lewmar accessories include friction stops that can be used on this track, which are activated by a winch handle. However, most sailors would likely opt for traveler controls with multiple part purchases, and for that reason the company offers one or two-sheave control end fittings, either with or without cam cleats. These fittings mount to the track by way of stainless steel Allen-head bolts that thread through holes tapped into the end fitting and simply tighten on the top of the track to lock the fitting in place. Lewmar treats them with Loctite to ensure that they won’t release. These bolts also serve as the axle for the sheaves’ bushings and to lock the cam cleats in place. Collectively, these end fittings represent engineering that uses the fewest number of parts for a number of functions.
Lewmar also sells its traveler system in kit form, with three sizes offered to accommodate boats up to 44 feet. The kit includes a different car and end controls from the one we tested, and because it’s intended for retrofits, no track is included. The system we tested sells for $669.
Ronstan provided its RC 12204 Series 22 low-profile car ($140), along with its RC 1224 Series 22 high-profile track ($93), which is rated for boats up to 33 feet. The company also sent its 12284 end fittings ($95 each). These have a single sheave and no cam cleats. Ronstan does offer double-sheave fittings—the RC00411 control sheave ($54 each)— with the option of a stainless steel arm, fairlead, and cam cleats, RC00421 ($72 each). We used all of that to calculate the price shown in our chart.
This is the lone track that we tested which didn’t come with pre-drilled mounting holes. Ronstan has other tracks that are pre-drilled, but feels that spanning applications require a degree of customization regarding the location of the mounting holes, and thus leaves the drilling up to the installer. The lack of holes also enhances the strength of the track for spanning purposes. Having the flexibility to drill your own holes can be an advantage for custom installations, but because properly countersinking a hole and getting it in the right location requires care and the precision of a drill press, we feel Ronstan’s strategy will have limited appeal for DIY owners. Ronstan also manufactures a high-profile track (no. 1225) for spanning greater distances.
Ronstan’s car and end fittings are milled from aluminum alloy and then hardcoat anodized. Like the majority of its competitors, the car also operates on recirculating Torlon ball bearings. Alloy end caps are screwed to each end of the car with stainless fasteners. The company claims these can be removed to service the ball bearings without having to remove the car from the track, but it’s not easy to do. Though these end caps would also tend to keep the car on the track if the bearings were to fail, they aren’t as beefy as those on the Lewmar and Antal cars, nor do they fit as closely to the track as the ones on those cars.
This car had the lowest profile of all those we tested—at just 1.01 inches high—and is also the lightest one at 8.1 oz. Like most of the other cars in our test, it’s versatile in that any of several control line attachments can be made. On either side of the mainsheet attachment shackle are tapped holes where a single or double control block could be attached. The mainsheet is attached to the car by way of a stout stainless steel shackle that pivots on a pin inside the car. This shackle articulates fore and aft, but there is no provision to keep it from hitting the side of the car. However, Ronstan does offer a stand-up spring kit to resolve this issue.
Ronstan’s end fittings fit over the track, and are pre-drilled for countersunk fasteners. Mounted atop by way of stainless bolts and nuts are alloy sheaves that turn on Torlon ball bearings, all kept in place by stainless plates. The inboard end of the fittings have urethane knobs installed that protrude out to accept the impact of the car should it slide all the way to the end unimpeded.
The system we tested sells for $675.
Schaefer’s traveler system arrived fully assembled, complete with two 12′ sections of 3/8″ braided control line. We’ll state right up front that this system is overbuilt for our test due to the fact that it’s rated for boats up to 45 feet in boom-end applications (up to 42 feet for mid-boom applications). The 72-92 ball bearing car with double stacked Delrin sheaves ($471.75) that is the heart of this system, is rated for a safe working load of 3,750 lbs., almost 1,500 pounds more than the other beefiest car in our test. Admittedly, this system is an apple among oranges for comparison purposes, but Schaefer’s next size down is only suitable for boats up to 27 feet long.
Schaefer’s 42-84 track ($180.75) was also the beefiest in our test. Fashioned from extruded aluminum alloy that is hardcoat anodized, it measures 1.5″ high by 1.5″ wide, and a four foot section weighs 4 lbs., 12 oz. This track, which is treated with a Teflon coating to reduce friction and wear, deflected fractionally more than Harken or Lewmar’s tracks, which are both similar in size. Schaefer’s track has countersunk holes (for 1/4″ fasteners) on 4″ centers. It also came with two 74-91 track end stops ($20.35 each), a 74-83 double control with cam ($120.60) and a 74-84 double control with cam ($120.60). A 78-49 stand-up adapter to connect the mainsheet is optional ($76.25).
Schaefer’s car, which is milled from aluminum alloy that is also hardcoat anodized, is almost 5.5″ long and weighs 2 lbs. 8 oz., making it the true heavyweight of our test group. Three stainless steel wheels are affixed on either of its inside surfaces. These wheels, which rotate around stainless axles on stainless steel ball bearings, run along the upper and lower ledges of the track as the car moves. The mainsheet connects to the car by way of a stand-up, spring-loaded adapter through which a clevis pin is inserted. (This piece we didn’t request, thus didn’t test.) The mainsheet can also connect to that same clevis pin, which pierces holes bored in the apex of a stout triangular bracket that is bolted to the top of the car with three stainless bolts. The outermost of these same fasteners are used to support the sheaves on the car for the traveler control system. The body of the car is not engineered (as are the others we tested) to remain on the track in case the axles or bearings fail, but in over 20 years of making this design, Schaefer says there’s never been a failure.
For traveler controls, Schaefer offers a combination of options including a dead-end bail, a single sheave, or a double sheave. These are mounted on track ends that fit over the track and are fastened to it by way of stainless machine screws that are threaded into holes tapped into the track. The track ends provided to us for our test had no buffering system, so car and end fitting will meet metal-to-metal, which isn’t a desirable arrangement.
The control sheaves are made of Delrin. Sandwiched between stainless steel plates, they roll on Torlon ball bearings. The track end controls include similar options, with the sheave-cam combination pre-drilled, allowing three different cam positions.
Though we deemed Schaefer’s car and track system nearly bulletproof, it does have one limitation. Two factors affect torsional loading: the width of the track, and the height of the car’s center of effort, defined as the pivot point of the cars toggle or shackle. Schaefer has a wide track and the highest center of effort angle (see sidebar) in our test. This means that when the boom is off centerline with the force vector extending along the mainsheet being other than vertical, Schaefer’s traveler system will experience higher torsional loads than its competitors.
The Schaefer system we tested retails for $934.40. Add the stand-up adapter ($76.25), and it totals $1,010.65
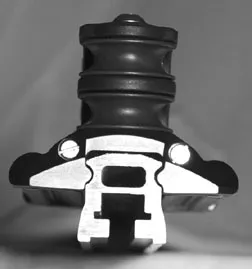
Conclusions
All of the products we evaluated appear to be well-engineered and suited to the task of controlling the mainsheet orientation on a mid-size sailboat. We found their overall functionality and load capacities to be more than acceptable, and didn’t discover any flaws in concept or workmanship. That said, several of the products stood out from the others due to their engineering. Schaefer Marine’s wheel-bearing car appears to take the old-school approach, eschewing ball bearings in horizontal races and beefing up the car material. At its narrowest, the aluminum car is nearly a third of an inch thick (.323″), and on the sides, where the wheels are affixed, it’s almost a half inch (.414″). From a visual perspective, its engineering seems almost crude alongside its competitors, but there’s a lot to be said for the reliability of a stout, simple device when you’re well offshore in big winds and waves. And Schaefer likes to point out that Torlon bearings do degrade over time, whereas stainless ones last much longer.
Each of the other cars and tracks appear to be the products of complex engineering. In the case of Antal Marine’s car, this is evident in the use of two races of ball bearings. This car took top honors in our two car smoothness tests. With Harken’s car, advanced engineering has resulted in captive ball bearings and the lowest car center of effort angle in our test. Lewmar’s car is also highly engineered and thoughtfully assembled. And Ronstan’s car has achieved its minimal profile—it is the smallest one we tested—through improved engineering. However, we felt that Ronstan’s decision to have the installer drill his or her own holes in this track was more a drawback than an advantage. These holes must be precision drilled, and once they’re done, the track’s anodized surface is compromised.
Overall, we like the advanced engineering of Harken’s car and we applaud the company for including diagramed instructions with its products. The bullet-proof fabrication of Schaefer’s system is also appealing, but we cannot overlook that it has the highest car center of effort angle in our test, no buffer to withstand impact between car and end fitting, and the highest price.
Antal would be our No. 1 choice save for its price. For those sailors who want elegant engineering, a fractionally smoother car, and better corrosion resistance—and don’t mind paying a premium for all that—this is the choice. Harken’s would rank second. For the rest of us, it’s hard to resist Lewmar’s more accessible price. Lewmar builds a car that is also elegantly engineered, though it is quite long, which lessens the amount of distance it can move the mainsheet. Still, at $230 less than Antal’s system, we think we can live with a little less efficiency.
Also With This Article
“Value Guide: Mainsheet Travelers”
“Center of Effort”
Contacts
• Antal Marine (Euro Marine Trading), 401/849-0060, www.euromarinetrading.com
• Harken Yacht Equipment, 262/691-3320, www.harken.com
• Lewmar Inc., 800/362-7212, www.lewmar.com
• Ronstan, 727/545-1911, www.ronstan.com
• Schaefer Marine, 508/995-9511, www.schaefermarine.com