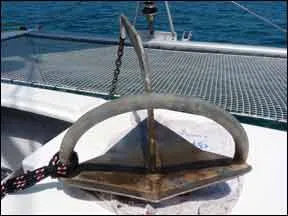
Photos by Jonathan Neeves
In the first part of this series on anchor-shank strength (PS, April 2013), we examined how the shanks of anchors that supposedly met the most stringent industry standards could theoretically bend under loads that a typical cruising sailboat could encounter. This month, we wanted to demonstrate how that might happen in a field test. But first, a recap.
In a nutshell, last months article explained how existing anchor tests are aimed primarily at commercial anchors, which have much thicker shanks than recreational anchors. We also lamented the fact that most anchor makers are not widely publicizing the details of materials and construction, and that they seldom offer useful performance criteria to help consumers make an informed purchase.
How can the shank of a supposedly high-tensile anchor bend? Our practical work on loading anchors (PS, May 2012) indicated that a worst-case scenario is a sudden dynamic load, often called a snatch load, a short, sharp loading of a well-set anchor at 90 degrees to the set direction. We found that this type of snatch-loading can be caused by wind gusts and the sailboat yawing and/or sailing at anchor-even without waves.
Add wave action to the impact of a sudden veering wind, and we have perfect conditions to produce high dynamic side-loads on an anchor shank. PS contributor Joe Minicks graphic description of the freak storm that severely damaged his boat in Greece (PS, April 2013) is a good example of the kind of severe, localized weather conditions that can impart extreme loads on an anchors shank.
Another instance when an anchor shank might be exceptionally loaded is on retrieval during strong winds or steep chop. Shortening scope during retrieval further compounds the problem. As pointed out in last months article, the difficulty in breaking out the modern, new generation anchors, poses another opportunity for a shank to bend during retrieval.
The angle of pull matters. Based on our anchor reset test (PS, February 2013), we know that when subjected to a series of gentle tugs at an angle to the set direction (up to about 150 degrees), most well-set modern anchors will slowly pivot around in the seabed. In that test, we noted that new anchors with convex, V-shaped sole designs like the Spade, Kobra, and Anchor Right Excel seemed to encourage pivoting. We also found that once most anchors are loaded at angles greater than 150 degrees, they will pull out, somersault, and reset.
Our tests on rode loads and anchor veering were preliminary fact-finding research, not comprehensive tests. This test is no different. Its principal purpose is to challenge the existing test methodologies and establish a pathway toward future testing.
Based on the findings in our previous work, we concentrated our study on a specific group of anchors and specific type of load. The anchors are regarded as super high holding power (SHHP) anchors-anchors that have demonstrated high holding capacity in a number of published tests. The load was a sudden, snatch (or dynamic) load applied at a 90-degree angle to the direction each anchor was set.
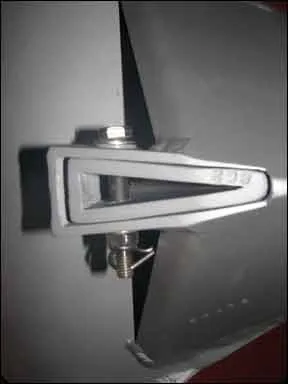
unless otherwise noted
What We Tested
For this test, we narrowed the field to a cross-section of anchor types, in a size recommended for a 35- to 40-foot sailboat. The steel anchors weighed around 35 pounds, and the alloy anchors weighed about 18 pounds.
The anchors used were a 17.6-pound Fortress FX23, a Danforth-style anchor fabricated from a 6060 alloy aluminum; a 35.2-pound Spade anchor, a concave-plough design made of 316 stainless-steel (also available in aluminum and galvanized steel); a 19.8-pound Anchor Right Super SARCA, a convex plough design made from galvanized steel (350 megapascal); a 35.2-pound SARCA Excel, a convex plough design with mild steel fluke and a high-tensile steel (ASTM 514) shank; and finally a 17.6-pound prototype aluminum alloy (5083) SARCA Excel, with a thicker shank than the steel version.
Both Anchor Right and Spade offer anchors in different materials. For Spade, the choices are steel (ASTM A572GR50), stainless steel (316), and marine alloy (AG4 or 5083). Anchor Right uses the ASTM 514 in its steel Excel anchor and 2205 in the shank of its stainless-steel anchors. It is upgrading from 5083 to 6061 in its alloy anchors.
Of the materials used, 316 stainless steel has the lowest yield strength, followed by the aluminum alloys. The ASTM 514 galvanized steel is approximately 70-percent stronger than the 316 stainless steel.
We chose to test five ostensibly reliable anchors generally representative of the styles that are on the market. The anchors are of markedly different designs and materials, except that two of the anchors are identical in design but fabricated from different materials.
Why these anchors? First, we are familiar with these anchors. We have tested all five in a number of seabeds under varying conditions. Our tester has used an alloy Spade, the Excel, and Fortress as primary anchors for a number of extended cruises. All five anchors set exceptionally quickly, and all, when well set, can require some patience to break out.
Why no CQR? Why no Bruce? Why no Delta? Because of the time involved-not to mention the inherent variables of this test-we limited the test to designs that we suspected would have a higher rate of shank failure. In simple terms, we wanted deep-setting anchors with thin shanks. We wanted results. Our intention is to use this data as a baseline for future tests of shank strength in a more controlled setting. Once weve established the loads under which an anchor shank can bend in the field, we have a better picture of what loads to apply in the lab.
The basis of the tests was to try to simulate realistic conditions as closely as possible while still making it practical to carry out the test in a reasonable time frame. For more details on how the tests were carried out, see the accompanying How We Tested.
All of the test anchors pulled out under loads of about 4,500 pounds, except the Fortress, which pulled out at slightly over 3,000 pounds.
The shanks of all anchors, except the high-tensile SARCA Excel, were bent to varying degrees. Based on the results, the galvanized SARCA Excel, with its Bisalloy 80 shank, did very well, and we expect similar anchors that use the same shank material, such as the Manson Supreme, to do just as well.
How did they do? The accompanying photographs (see Testing Snapshot) tell the story:
Not only was the shank of the prototype 5083 alloy Excel bent, but the fluke also suffered severe distortion.
The shank of the Super SARCA was bent near the fluke.
The Fortress shank was mildly bent, near the middle of the shank. The Fortress flukes showed no sign of distortion.
The Spade shank was bent and twisted, and the shank slot in the fluke showed some minor distortion.
We ran more tests, including one on a 22-pound Excel anchor that has a steel shank with a yield strength of 350 megapascals (MPa)-commonly found in cheaper anchors. It bent as expected, further illustrating the value of a high-tensile steel shank. (It should be noted that this anchor was not designed for these loads, and that Anchor Right uses the higher-grade ASTM 514 in its larger anchors.)
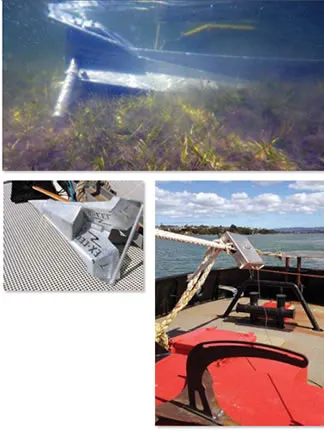
The Fortress fluke has a relatively low profile from the side and will have little, or low, resistance to a load at 90 degrees. It effectively cuts sideways in the seabed like a knife, and this might explain the lower load required to pull it out. An implication is that a Fortress will swivel with a change in wind direction much more easily than an anchor with higher-profile flukes that offer greater resistance to pivoting, such as a Supreme or Excel.
Although we do not know the precise load at which each shank bent, we do know that the Fortress shank bent at less than 3,000 pounds. Considering the limited amount of distortion, the shank looks to have bent close to the pull-out load. It seems the shank bent at or near where it emerged from the seabed when set-suggesting the seabed offers support to a shank. (More on this below.) Based on its own and independent tests, Fortress was confident that repeated tests and a deeper set would produce greater pull-out loads.
It was possible to straighten the Fortress shank for temporary use or for use as a spare, but we do not advise this as a permanent solution. This type of deformation, called plastic deformation, permanently weakens the metal. In this case, Fortress replaced the shank under its lifetime guarantee.
The failures of the SARCA and Spade shanks were not severe, suggesting they bent near the 4,500-pound pull-out load.
The severe and catastrophic failure of the alloy Excel suggest that it began bending well below the 4,500-pound maximum, although it still managed to sustain the same amount of load before releasing from the seabed as the steel Excel and stainless-steel Spade.
It would have been possible to straighten the SARCA shank for temporary use, but the complex bend in the Spade shank put it beyond repair.
Our experience with the Spade points to the advantage of a removable shank: The shank is typically an anchors weak point, but a removable shank can be easily replaced. Out of curiosity, we are considering replacing the bent hollow shank with one cut from -inch ASTM 514 steel-a material that has held up well in our testing.
The results indicate that there are two lever actions at work on most of these anchors-excluding the Fortress. There is a lever action parallel to the seabed, trying to re-orient the fluke to the direction of load. This lever action, best seen on the SARCA, stresses the horizontal axis of the shank. All anchors, except the galvanized high-tensile shank Excel, showed a degree of failure in the horizontal.
A second lever action loads the shank on the axis perpendicular to the seabed, effectively trying to twist or roll the anchor onto its side. Both the Spade and the experimental alloy Excel show distortion on this vertical axis.
The vertical portion of the SARCA shank has some support from its roll bar, and this might explain why we found no distortion of the vertical section. The Fortresss straight shank is stressed in one dimension only, having no vertical bend or L shape to its shank.
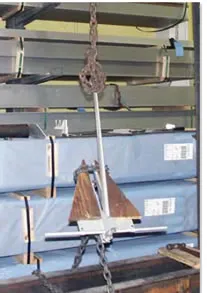
Benefits of Burying
By comparing these field tests to the controlled, graduated loading tests that we carried out for the April 2013 article, it seems likely that a deeply buried shank will be less prone to bending. Last month, we demonstrated in lab testing that a 33-pound Excels half-inch ASTM 514 shank will start bending under a load of about 1,000 pounds if that load is oriented at 90 degrees to the shank.
This 1,000-pound failure is only about 25 percent of the load applied in our seabed test, which did not cause any failure to the same shank material. We partially attribute this discrepancy to the fact that the directions of load in the two separate tests were not identical; but it also seems likely that the seabed supports and reinforces the shank in the field test. In addition, our graduated load test in the lab applied the load for a much longer period than our seabed test, allowing more time for plastic deformation to take place.
If, as we suspect, the seabed offers support to a buried shank, then a poorly set anchor-an over-sized anchor, for example-might be more prone to shank failure than a well-set anchor with a deeply buried shank (assuming the shank dimensions are roughly equal). Likewise, an anchor with a weaker shank might better resist bending by virtue of its superior ability to bury itself.
Conclusion
The tests were too crude to present any accurate rankings, but it did reinforce our conviction that anchor shanks can bend in real-world circumstances-and that there is a clear difference in yield strengths. For the sake of reporting, the amount of bending, from none at all to severe, was the following: the galvanized Excel (ASTM 514), stainless-steel Spade, Super SARCA, Fortress, and aluminum-alloy Excel.
The results clearly illustrate the significant advantages of a well-engineered shank of high-tensile steel. The failure of the stainless-steel Spade also reinforces our point that using the same template for different material necessarily imparts variability in shank yield strength. (We would not have expected to see the same degree of a failure in the much stronger galvanized or even the aluminum version of the Spade, which has a beefed-up shank to account for the difference in tensile strength.)
Interestingly, even though the Super SARCA failed in our tests, it and the galvanized SARCA Excel (along with larger sizes of the Fortress) meet Classification Society (CS) requirements for holding capacity and for proof testing as super-high holding power anchors. Based on the Spades technical specifications, we would assume that its galvanized version, if tested, would also meet SHHP requirements.
Thus, our findings further support last months conclusion that the proof testing-as it is currently conducted-has limited value to the recreational marine industry, and that buying an anchor based on this stamp of approval might engender a false sense of security.
As mentioned, we think the problem of shank strength is most acute with those anchors that have super high holding power. The relentless pursuit of high holding capacity has produced better anchors, but unfortunately, there hasn’t been a commensurate increase in shank strength. There are better materials than the ones used in many of our tested anchors-ASTM 514, 6060 alloy, and 2205 stainless-and these should be an option. We have good design, now we need better material choice and fabrication.
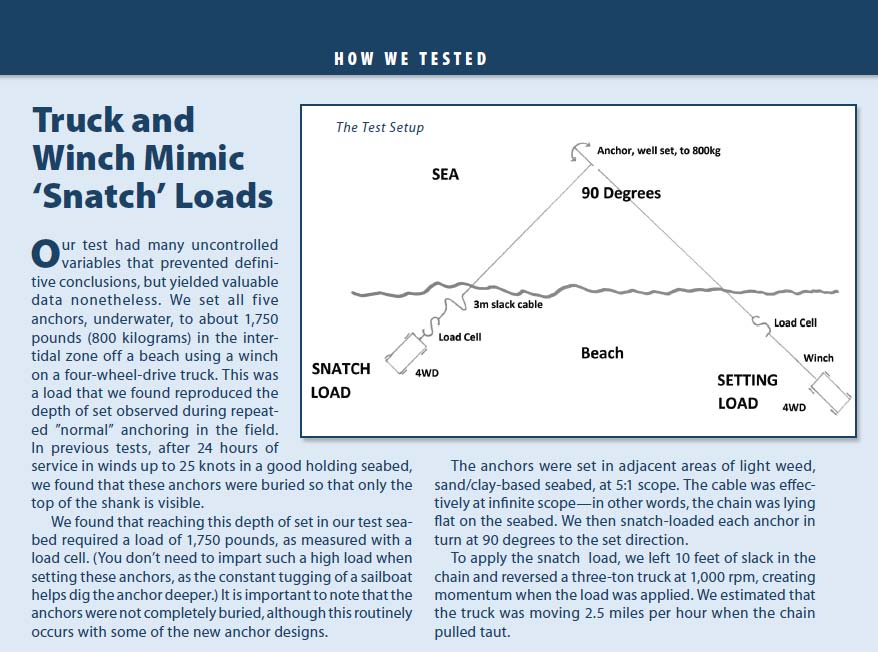
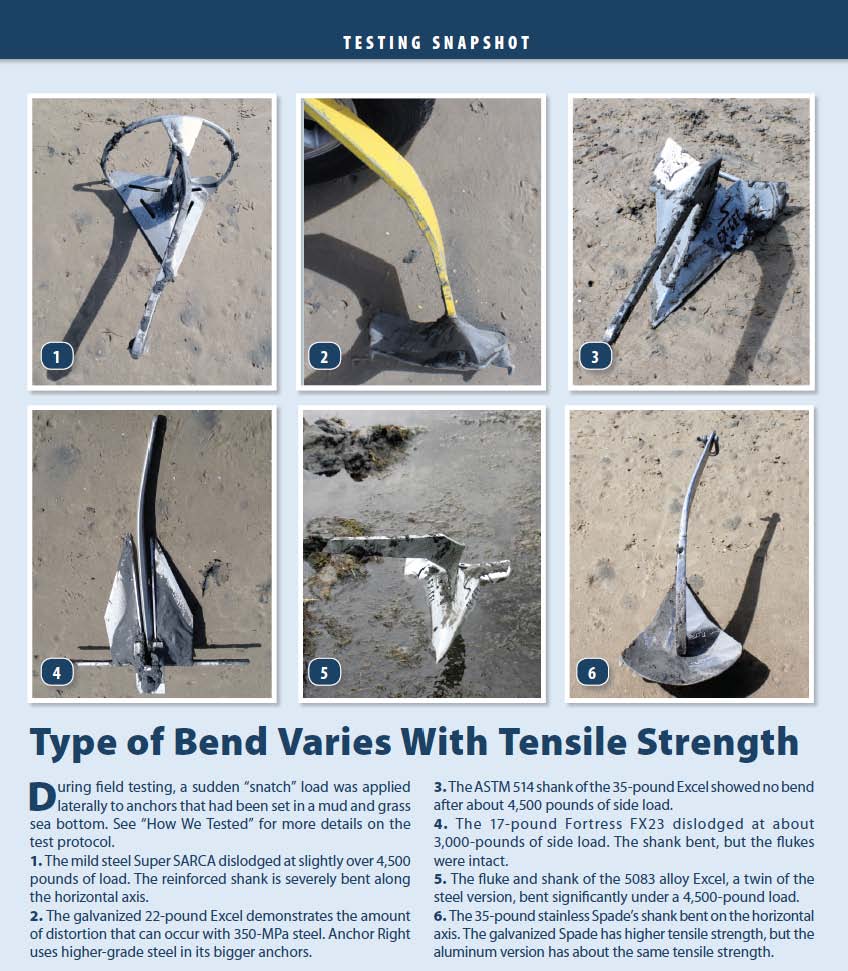
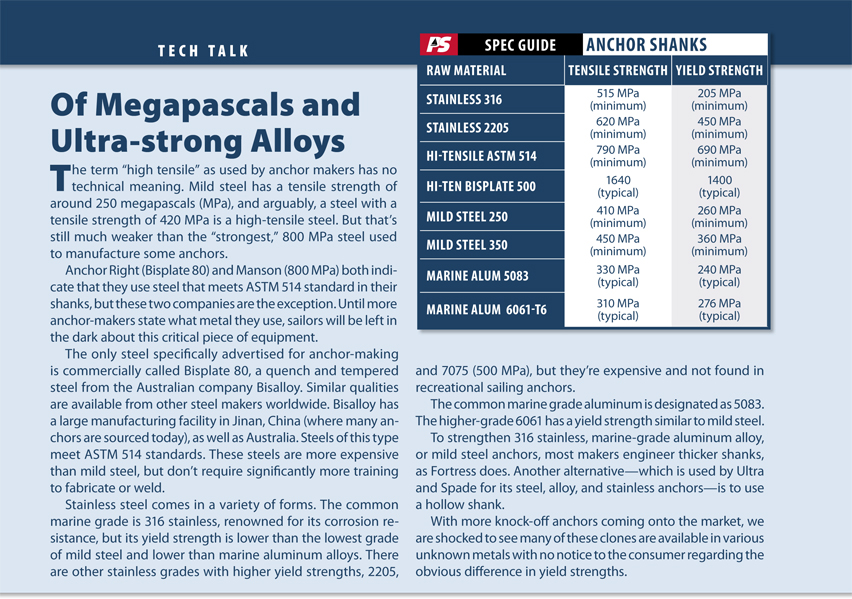
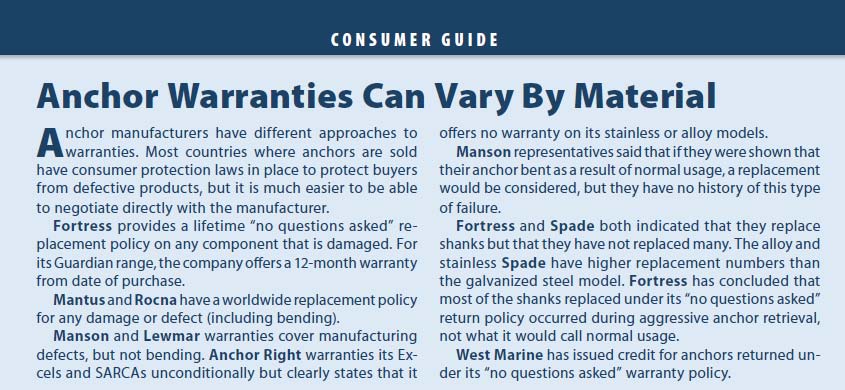
Thanks for this! Very interesting and informative.
Just a note on terminology: All the anchors you test are alloy anchors. I realise that it’s possible to deduce what you mean when you say “alloy” by reading between the lines in your ninth paragraph. But if I find the article via a web search, or search for an item of interest such as “Excel”, your misuse of the word is a bit frustrating: any comment you make about “the alloy anchor” requires digging around to see how you have chosen to redefine it.
Minor quibble on the report. Great article overall.