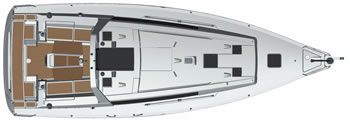
350
The building process that gives rise to the Beneteau Oceanis 41 begins in France, where digital design files stir a five-axis cutter to life, and 3D foam patterns begin to take shape. These robotically cut male plugs are used to fabricate female molds, often referred to as “tools.” The hull and deck are the major molds, but there are often 20 or more smaller tools created that are used to mold other interior and exterior components—ranging from locker lids to a plinth for the marine head. All of the tooling for each Beneteau is made in the prototype shop in France and is shipped to factories around the world.
The Oceanis 41 is built for the U.S. market in Beneteau’s Marion, S.C. factory. The hulls are laid up in a tilting, open-transom mold, and the process is tightly controlled. Once the mold surface has been polished and a release agent has been applied, an even amount of gelcoat is sprayed onto the highly polished surface. The layup crew must time the next step to begin just as the gelcoat sets and partially cures but is not yet fully hardened. The goal is to have the “still green” gelcoat chemically link with what’s referred to as a skin coat, a combination of vinylester resin and chop strand mat. These two steps produce a smooth, glossy outer hull surface and a backup barrier that acts as an impermeable water block. This two-fold, high-resin content outer layer also helps prevent unwanted fabric print through. Success hinges on well-trained spray applicators and laminators ready to use serrated rollers to manually drive air bubbles out of the laminate.
The E- glass laminate schedule for each boat is CNC machine cut and layered to add more reinforcement in high load regions of the hull. Beneteau continues to favor a solid glass hull that’s stiffened by the addition of a molded grid/liner. The latter is bonded to the fiber reinforced plastic (FRP) hull and provides both a finished inner surface as well as crucial attachment surfaces for bulkheads, interior joiner work, and even engine beds. The alignment of this crucial member is as important as the bonding process itself, and a jig aligned with the hull is used to make sure both parts properly line up.
The complex deck structure—made in a closed molded FRP infusion process—does not go on until most of the interior has gone into the boat. Components are bonded with a urethane adhesive; there’s ample surface area, and a 360-degree approach to this adhesive fastening process. Careful surface preparation and lots of adhesive R&D ensures that the parts bonded in place stay where they belong over the long haul.
The keel stub and keel bolts tie in with the grid structure, and the same goes for the upper and lower rudder bearings. Once most of the larger pieces of the interior, tanks, and engine are in place, the deck is aligned with the hull using a positioning jig, and the overhead gantry lowers the deck onto a bead of polyurethane adhesive. Mechanical fasteners are used to hold the parts in place during the curing process. Even though the adhesive quality of the sealant is strong enough to do the job all on its own, the fasteners are left for belt-and-suspenders security.