Lifelines are called guardrails by British sailors, but regardless of their designation, they represent a handhold of last resort.
Situated like a fence around the perimeter of most sailboats, lifelines often go unnoticed until a crew member is hurled to leeward and frantically reaches for something to keep from going over the side. If all goes well, the properly tensioned wire or rope accepts the impact load, transferring the energy into compression and bending moments that radiate through stanchions and pulpits. The energy dissipates in the deck, and the catapulted crew remains on deck.
The system comprises more than stainless-steel tubing and wire or high-modulus rope. Theres often an array of minor hardware playing a major role. These bits and pieces act like links in a chain or a fuse in a series circuit-any one of the lesser components lets go, and the entire system fails. Clevis pins, cotter keys, turnbuckles, swages, spot-welded pulpit connections, and gate hardware add up to a lot of potential points of failure.
The International Sailing Association and Federation (ISAF) Offshore Special Regulations give considerable attention to lifeline design. For boats over 28 feet, they must be a minimum of 24 inches above the working deck and be made of uncoated wire or the equivalent high molecular weight polyethylene rope (HMPE) like Dyneema or Spectra. If socket-type bases are used, through-bolting, welding, or bonding is mandatory. Socket mounts with set screws or self-tappers have been known to work free. When using high-modulus fiber lifelines, the type of splice used should be what the manufacturer recommends; versions of the Brummel splice are often the preferred approach for placing an eye in single-braid line.
The U.S. Code of Federal Regulations 28.410 mandates that commercial vessels have lifelines, deck rails, or bulwarks that are a minimum of one meter (39.5 inches) high, with stanchion spacing no more than seven feet and no greater than 15 inches between wires or tubing. Despite the fact that human size doesn’t vary between commercial and recreational craft, the lifeline minimums are scaled back for recreational sailboats. Its a legitimate design compromise, but theres little doubt that you are more likely to go over a side thats bounded by a 2-foot-high wire railing than when youre held in check by a restraint more than 3 feet high.
We are not advocating 40-inch lifelines on 30-foot sailboats, just pointing out that the minimum standards for recreational sailboats don’t go very far toward preventing crew from ending up in the water. The recreational sailor needs to become more deck agile than the average passenger on a Block Island ferry. We learn to reach inboard for handholds, make sure that the nonskid on the deck and cabinhouse affords good grip, and avoid leaning outboard using the lifelines like a banister on a staircase.
Sailboat lifelines have jumped back into the spotlight thanks to a growing acceptance of-and some controversy over-high-modulus rope like Dyneema and Spectra being used as an alternative to stainless steel. Dyneema and Spectra are brand names for lines made from trademarked HMPE. One of the key attractions of these lightweight fibers is that they allow ropes to be made as strong as stainless-steel wire of equal diameter, yet they weigh a fraction of the wire that they replace.
Practical Sailor has launched a long-term, in-depth set of seatrials linked with lab testing at the U.S. Naval Academy to determine the value of high-modulus rope alternatives versus stainless-steel wire lifelines. In this first phase of the test, we look at the issues involved in transforming one of our test platforms, Technical Editor Ralph Naranjos Ericson 41 sloop, from wire to Dyneema SK-75 lifelines.
Steve Parola at New England Ropes has provided us with several high-modulus line options. For the first round of the comparison, we installed an HMPE 5.1-millimeter, special double-braid lifeline for the top lifeline and an Endura 12-strand single braid for the bottom. (The HMPE 5.1 is a prototype lifeline developed by New England Ropes; it is not yet on the retail market.)
Those who are already familiar with using cordage strops and lashings to attach hardware will feel more comfortable with a fiber lifeline installation. Obviously, strength and reliability are key concerns when installing a rope alternative to wire. Abrasion will become more of a concern, and each hard spot or contact point along the run of the line needs some consideration.
The bottom line is that there is a big difference between a sharp-edged hole drilled through a stainless-steel stanchion and a smoothly rounded lead at the top of the same stanchion. In some cases, what was an adequately smooth lead for stainless wire will need a bushing to protect the less abrasion-tolerant fiber rope. However, the good news is that an all-rope system is easy to set up and terminations can be made without the need for swage machines or specialized hardware.
New England Ropes, Samson, Colligo, and others offer splicing guidance on their websites, and for those who already do their own bury-type splices in double-braid line, theres no reason not to learn one of the Brummel type splices that offer an efficient way to eye splice in single-braid Dyneema/Spectra line.
What we tested
All of the rope we are using in this round of testing is either 100-percent SK-75 Dyneema or a combination of Dyneema core and Polyester cover. The tensile strength of new line is equal or greater to wire of equal diameter, and as Naranjo found out in his previous tests (see page 22), lifeline breaking strength is not the limiting variable when it comes to the failure of a regularly inspected and reasonably maintained system.
For the test, each line was attached at the stern pushpit using a D-shackle and a double turn in a spliced eye. The rope was run through the same fair leads on the stanchions that the stainless wire had been run through.
We did note that the running backstays, when eased and secured to the rail, rubbed against the lifelines. This hadnt been a problem with the wire lifelines, even though we sail more of the time with the running backstays in this slackened state. Our plan is to monitor this potential chafe point.
All of the top stanchion fairleads, and even the aftermarket lower lifeline leads, had smooth radius entry and exit points that need no modification. We intentionally chose a no thimble eye splice as the means of securing to the pushpit shackle, because we wanted to test the most chafe-prone alternative, which should be the most likely to show early signs of fiber damage. With the eye splice at one end secured to a D-shackle on the stern pushpit, the line was led forward through fairleads on top of the stanchions.
For the bow pulpit terminus, we chose a lashing rather than a more traditional eyesplice termination. Our choice was based upon a need to easily swap out lines being tested, and a splice would not fit back through the fairleads. An advantage of this direct-pulpit attachment was the elimination of a lashing lanyard, another potential weak link in the system. Our approach also allowed us to wrap the line around the pulpit leg, not simply depend on the integrity of a very small weld on a pulpit tube strap. Another sensible compromise is to splice an eye and lash the forward end, taking turns around the pulpit tube as well as engage the welded attachment point.
STS-12 is New England Ropes name for its Dyneema core polyester cover double braid line that has gained quite a following as a low-stretch, high-tech, cost-effective rope. It has proven quite durable in running-rigging applications such as halyards, sheets, topping lifts, and guys. We wanted to test the idea of a lifeline with a very UV-resistant polyester cover and an SK-75 Dyneema core. From the start, we recognized that there will be a chance that the chafe at contact points will cut through the cover. But after a few months of testing, theres no sign of such problems occurring.
STS-12 is an all-Dyneema, single-braid rope that incorporates a 12-strand weave, is friendly to Brummel splicing, and has a special chemical finish that prevents deterioration caused by UV rays. The braid configuration also more closely mimics the look of wire, and those averse to the rope look of modern fiber lifelines may want to opt for the slate gray color (one of several options) and texture of STS-12. With this line, your marina neighbor will wonder why your wire lifelines don’t stain with rust, never realizing that they are rope.
New England Ropes has come up with a specific lifeline cordage that is made up of a tough tight weave of a Dyneema cover and a Dyneema core. The ultra-tight weave of the cover makes it very tough and snag resistant, and the load sharing between the core and cover affords very good tensile strength.
How we tested
Our underway testing is as much about how these fiber lifelines function as how well they hold up in the marine environment. During the setup, we found that the transition was pretty straightforward with the major difference between reeving wire and rope being the need to avoid contact with hard, sharp edges. Underway, the behavior was quite similar. The taught, non-stretchy material replicates wire well, and the only surprise was when a ring-type retainer on a fiddle-block clevis pin decided to grab hold of the lower lifeline (Endura Braid 6 millimeter). Tacking the boat unloaded the block and allowed us to quickly remove the errant ring-ding, replacing it with one that did not have a bent-out prong ready to snag lines.
We did find that installing spliced eyes at both ends and using a lashing pennant to tension one end of the lifeline is the most sensible approach to controlling deflection. ISAF regulations stipulate that an 11-pound weight midway between supports should deflect the lifeline no more than about 2 inches. This was easy to dial in with a lashing lanyard.
But just as with wire and a turnbuckle, trying to achieve banjo-string resonance will do more harm than good. The opposite-leaving lifelines too slack-also has negative consequences. Leaving race-boat lifelines so loose that crew weight migrates to the windward topsides can challenge the structure of the system and jeopardize the crew.
As pointed out in Failure Analysis (page 22), too much bending rather than compression loading on stanchions will cause premature failure. Lifelines were never designed as hiking augmentation, and their adaptation to this brings some compromises into play. Extra care must be given to making sure components are sound and chafe hasn’t caused fiber or wire-strand damage.
During our underway testing, we quickly grew accustomed to the secure, seemingly non-stretchy rope lifelines. Stepping aboard or when grabbing in any of a dozen other different ways, they worked just like their wire relatives and afforded a user-friendly grip.
Time will tell how they handle environmental factors ranging from hands just lathered with sunscreen to the atmospheric deposition of diesel soot. According to NERs Parola, the life expectancy of fiber lifelines like HMPE will be measured in years, rather than the decades of service wire lifelines offer. We recommend checking lanyards and lashings annually, and keeping a watch for chafe damage.
After a year or so, well haul the lines weve installed into the lab and test their tensile strength to see how it compares to their original breaking strength. Part 2 of this test will include feedback from a race boat crew and similar on-the-water testing and lab followup.
Conclusion
The popularity of high-modulus fiber lifelines among racing sailors makes it clear that the approach is well suited for the meticulous sort who wants to save weight and is prepared for the more frequent replacement interval. But what about the cruiser who is more interested in robust equipment that can stand the tests of time? That is what we hope to find out.
While the changeover to fiber is not without hiccups, the material gets high marks for do-it-yourself installation. Chafe is clearly more a of a threat, but it can be mitigated.
When Naranjo cut away the stainless-steel lifelines to install a fiber alternative, he thought back to 1984, when he had installed the wire. The top wire was an oversized -inch, 7-by-7 chosen because it allowed him to bend it over a thimble and double-nicopress his own fastening.
The approach had been DIY-simple, easy to inspect, and had certainly passed the test of time. The new fiber makeover weighed mere ounces compared to the 10 pounds of wire and hardware he was abandoning, and yet, the breaking strength of the line was better than the 7-by-7 heavyweight stainless.
At the onset it seems to us that lashing, splicing, and stitching can ensure as much security in the system as one gains with a shackle and turnbuckle, perhaps even more. But the final answer to which is better lies in the longevity of the system and what type of dropoff we see as the rope ages or chafes and the marine environment takes its toll. We will carefully inspect lanyards and lashings, scrutinize metal on fiber chafe, UV, dust dirt, and the effect of atmospheric deposition-and then take our test lines to the lab and see whats left.
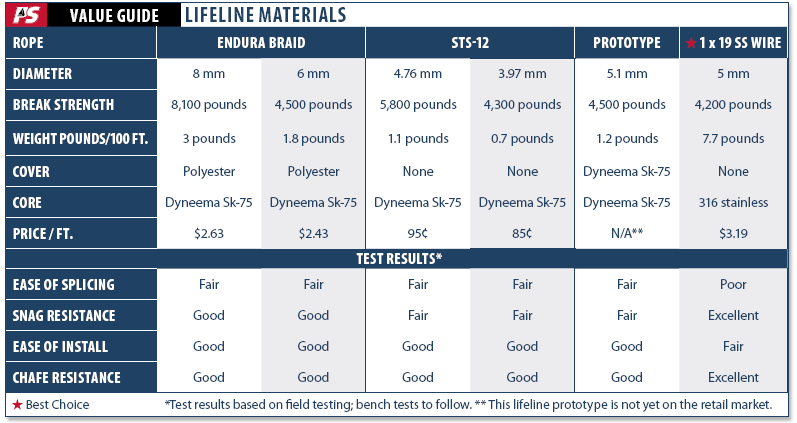
The longevity of bare (for easy inspection) professionally rigged stainless-steel lifelines remains our first choice for cruising boats; our recommendations regarding high-strength, low-stretch fiber lifelines is pending the results of more testing.
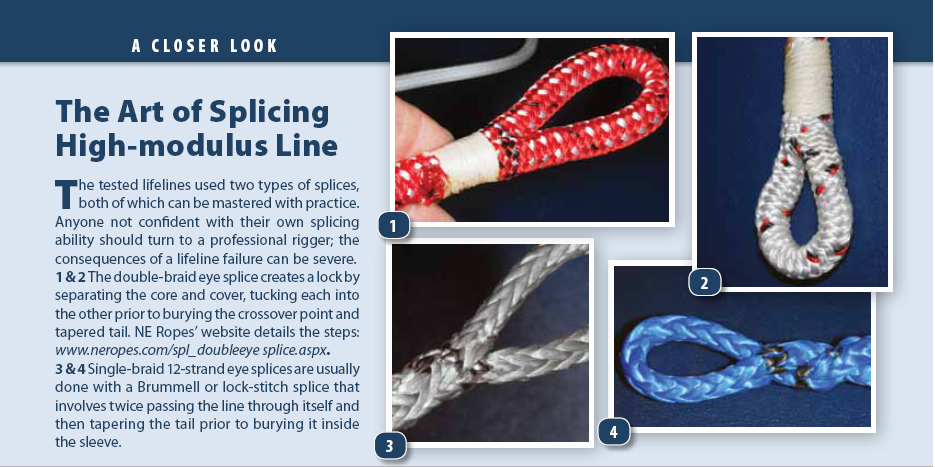