Corrosion attacks anchor chain long before it has reached the end of its useful life, and corrosion begins as soon the galvanized coating fails. Re-galvanizing can breathe new life into old chain, but it is not so simple or affordable as it used to be. As we saw in our most recent report on chain (see Practical Sailor June 2014 online), some of the high-tensile grades require specialized skills to galvanize, and others can’t be galvanized at all. Even if galvanizing is an option, removing rusty old chain from the boat and delivering it to the galvanizer can make moving pianos seem like a cinch.
Chain is expensive to buy, but it can be even more costly when it fails. As we advised in our June 2014 article Looking into the High Test Myth, we recommend chain that is designated as Proof Tested chain from a supplier with a long reputation to uphold. Proof tested means the tensile strength of that specific chain has been physically tested. The chain should have a certificate from the manufacturer or a recognized testing agency indicating proof testing, and the markings on the new chain should indicate its grade (G30, G3, G40, etc.).
If you are interested in high-tensile G70 chain, which offers greater strength by weight but cannot be regalvanized, you should first read the June 2014 article to understand the pros and cons. We also recommend that you request a break test be conducted on 3-foot lengths from at least one end of the chain you want to buy. Be sure to ask to have the tested section returned to you, so you can check coating integrity. (Given the variability we found between stated and actual breaking strengths, we think break-testing is a sensible practice for G43 chain as well.)
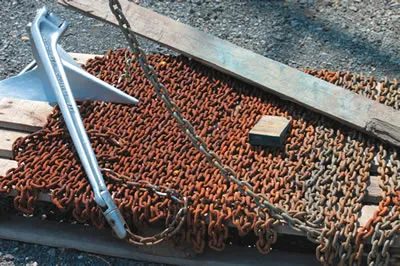
Photos by Jonathan Neeves
When we buy chain that is certified to meet certain test criteria, we know what we are getting in terms of strength. The mystery is: How long will the chain last? In nearly every chain test weve carried out (and there have been many), durability becomes a key factor when looking for the best value. And if you are going to look at durability, you have to consider galvanized coating. In this report, the first of its kind by Practical Sailor, we look specifically at galvanized coatings, hoping to shed a little light on the protective skin that keeps some chains rust-free for months, or even years longer than others.
Other recent reports on chain quality appeared in the December 2008, November 2008, January 2008, January 2007, October 2006, April 2006, and Dec. 1, 1999 issues.
What we tested
The outermost coating of anchor chain is typically a soft sacrificial layer of zinc. Underneath this zinc coating are various zinc/iron (Zn/Fe) alloy layers that are harder than the zinc, and even the underlying raw steel. The abrasion and corrosion performance of your chain depends on those Zn/Fe alloy layers, sandwiched between the raw zinc and the raw steel. To compare these coatings, we sought chain samples from a range of manufacturers and suppliers in the United States, Australia, and Europe.
From Campbell and Peerless (which includes the popular U.S. brand Acco), we looked at G30, G43, and G70-all 5/16-inch chain. From Canada Metal Pacific (CMP), we looked at 8-millimeter (the near equivalent of 5/16-inch), Grade L (G30) Titan chain, made in their Ningbo, China factory. From the Italian company Maggi, we looked at 8-millimeter G40 and G70 chain. From the Australian company Serafini, we looked at Grade L (G30) and Grade P (G40). From PWB, another Australian source, we tested Grade L (G30). All of these chains were uniquely marked, making it possible to define both quality and who makes them. For a full explanation of the grades and standards see Making Sense of Marine Grade Standards, PS June 2014 online.
We also sourced generic 8-millimeter short-link chain from China that we sourced from two different Australian chandlers, Whitworths and BCF, which imports through BLA. These chains were not marked. Neither chandler declares the source in China of their chain, and we cannot be sure they have just one source. They are effectively mystery chains.
All of the products we looked at were Hot Dipped Galvanized (HDG). We also tested some samples treated using the Armorgalv process, a unique galvanizing system that is compatible with some of the higher test chains that cannot use the hot-dip method. In this article, we offer a preliminary look at Armorgalv. We will be reporting on that test in a future issue of Practical Sailor.
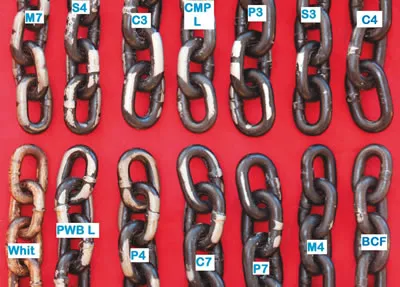
How we tested
We took 12 inches as a standard length of our samples, each was cut from the same 7-foot lengths used in our most recent tests and suspended from our test boat so that they dragged simultaneously across the bottom (fine sand with some mud) and were allowed to abrade. We had 18 samples in all.
We allowed 30 days for the abrasion testing and then stored the chain in a lidded plastic bucket (to simulate an anchor locker) for 30 days. We then resumed abrasion testing for another 40 days-for a total of 70 days of abrasion testing.
It is important to note that 70 days in our test is not the same as 70 days at anchor. It is probably more like five to six months at anchor, but this is a very rough estimate and highly variable depending on the seabed.
Anchor chain is not only subject to seabed abrasion, but it is also abused as it runs through the windlass gypsy. Poorly adhered coatings will rub off or chip as the chain passes through a gypsy. Although we did not run the chain through a gypsy, we closely examined each chain for signs of chipping and flaking after the abrasion test. The most revealing chip/flake test involved stretching each chain to its breaking point and examining links that had broken and stretched. Although chains do not undergo such extreme elongation during normal use, we feel that the ability of a coating to adhere and resist flaking while the chain is stretched is still a useful benchmark when comparing galvanized coating.
As a rule of thumb, the thicker the galvanized coating, the longer that coating should last. We measured thickness four ways: using a thickness meter that compared magnetic flux (zinc is non-magnetic), microscopically (using polished sections), using a micrometer (subtracting the known uncoated wire thickness from total thickness), and finally, using the formulas and measuring technique described in the accompanying How We Tested. We were pleased to see that all four means of measuring correlated. As in past chain tests, we also weighed links before and after exposure to saltwater testing. This gave us an idea of overall corrosion resistance, but it was hard to differentiate between mass lost from the iron link itself or the zinc coating, which we wanted to pin down.
Of course, the abrasion resistance of the galvanized coating isn’t solely a function of thickness. It is also a function of steel chemistry and the chemistry of the galvanizing bath. Because zinc is three times more expensive than the iron it protects, makers try different methods to prolong protection with thinner coatings. We couldnt confirm the coating or bath chemistry, which is why we relied heavily on a visual inspection.
The biggest problem with our test is that we only tested one small sample from countless feet that each manufacturer churns out. It was a spot check that might have just landed on a bad (or good) apple. Without months of such random spot checks, we can’t know whether the sample we tested is an anomaly or representative of all batches.
What we found
Looking at a rough correlation of our coating thickness measurements and abrasion performance, we can conclude that a coating thickness in excess of 100 microns is adequate; anything less, and you can count on a short life before corrosion sets in. If you can find chain with a well-adhered 150-micron coating, then your links are surely well protected. Based on our findings, about twice the coating weight seems to approximate to twice the abrasion resistance. Coatings that are too thick can be brittle and prone to flaking. However, some of the thickest coatings in our test were well adhered.
Surprisingly, one of the best performing chains was one of the generic Chinese chains, but the other generic Chinese chain was appalling. It lost all of its coating by the end of our test period-on every link! Although our destructive testing revealed that the longer-lasting chain had a thicker galvanized coating, by just looking at these chains new, there was no obvious way to differentiate them.
Neither of these chains are manufactured to an industry specification; neither has any marking that would allow us distinguish one chain from the other; and neither retailer we bought from would or could reveal the source of the chain. Given a total inability to differentiate these products, we cannot recommend anyone invest in a chain without marking and without specification.
A few chains showed poor adhesion of the galvanizing layer to the base steel. The Maggi Aqua 4 (G40) was particularly bad, with large flakes separating from the base. The failures came both as a result of our break tests and through our simple twist test. (See How We Tested.) Consequently, although the Maggi G40 acquitted itself well in our seabed abrasion test-it had the thickest galvanized coating of our samples-the poor adhesion of the galvanizing make us very cautious. The CMP Grade L (G30) also showed some signs of flaking, although it showed high strength for a G30 product. CMP also makes a G43 product, which we have not yet tested.
The BCF Chinese sample had some small areas of galvanized coating showing flaking-but since we cannot recommend any uncertified such product (for a number of reasons)-its not that relevant. None of the other samples showed flaking in our break test or our twist test.
Both Campbell and Peerless showed consistent coating thickness and good adhesion of the galvanized layer to the base steel. Both did well in our seabed abrasion test. Both had a generous layer of galvanizing. Based on our post-test observations, it appeared that Campbells galvanizing in the G43 category held up better than the Peerless, but the differences are minor-so small that we could not rule out some environmental or other testing variable as the cause.
Both Campbell and Peerless did a good job of galvanizing their G70. Their samples clearly held up better than Maggis G70 sample, whose thin galvanized layer eroded quickly.
Although the galvanizing did not endure as well as its G70 competitors, testers noted that the Maggis smaller diameter links were pound-for-pound stronger than the Campbell and Peerless chains. However, since you cannot re-galvanize G70 chain without compromising strength, we would prefer to see a product with a longer-lasting coating.
Overall, Maggis galvanizing leaves much to be desired. It flaked off on the G40 samples and was very thin on the G70 sample. CMP had a reasonable coating thickness, but like Maggis G40, it showed signs of poor adhesion.
Both PWB and Serafini subcontract the galvanizing process to outside sources, and both had variable results. Adhesion was good, but coating thicknesses varied, resulting in inconsistent abrasion resistance. Testers also noted that the Serafini chains welded joints were all misaligned-each by about 1 millimeter. This is something to watch out for when you buy chain.
The importance of keeping galvanizing intact became apparent as the test progressed. At the site of the first damage, where only a small area of coating was removed, the galvanizing coating on surrounding links became sacrificed at a much faster rate. The corrosion effectively spread outward from the corroded area. This implies that anyone using chain long term-liveaboards, for example-are going to lose galvanizing relatively quickly, unless they take measures to protect these areas with a cold-galvanizing spray. It also seems likely that corrosion will begin at any flaws in the weld.
The amount of abrasion we saw suggests that chain wear will be a significant problem for liveaboards who spend months on the hook. For these people, it would be sensible to measure chain links for wear. Check links every 20 feet, every six months. This routine would be especially relevant for those who opt for the smaller-diameter G70.
Conclusion
Buying the correct sized G30 chain (to match your windlass) is the most cost-effective, sensible choice for most cruising sailors. All the G30 chain we tested, except the Whitworth Chinese supply, had a breaking strength close to or greater than 4 tons. This is two to three times greater than the 1.6-ton load calculated by the American Boat and Yacht Council (ABYC) on a 35-foot boat in 60 knots of wind. Given that we want a decent safety margin, chain does deteriorate (it gets worn and strength will diminish), and 60 knots is unusual, then G30 looks more than adequate. Keep in mind that the ABYC data does not take into account any reduction in load that would be achieved through the proper use of snubbers or a second anchor. (For more on the function of snubbers in any anchoring system, see Practical Sailor November 2013 online.)
Overall, the Peerless G30 chain is our Best Choice. It well exceeds the strength requirement and has very good abrasion resistance. Both CMP and Campbell chain are also more than adequate in terms of strength, but neither is as resistant to abrasion as the Peerless G30. The CMPs galvanizing adhesion was also lacking.
Campbells G43 fared better than that of Peerless, both in terms of strength and abrasion resistance-although the abrasion resistance was not as obvious. More testing is needed to determine whether our samples are typical and represent the average, but buying from either Peerless or Campbell in the G43 Grade is a good choice.
The metric chains didnt thrill us. None matched the quality, in terms of coating performance, of the equivalent American chains (Peerless and Campbell). We are uncomfortable with Maggis G40 galvanizing adhesion. We think the coating thickness of Maggi G70 is too thin. Canada Metals Pacific was the leader here, with good coverage, okay abrasion resistance, and some flaking.
Neither the PWB nor Serafini samples could compete with either Campbell or Peerless. Serafinis chain raised many questions. Its Grade P (G40) does not meet specification for strength and has an extraordinarily low yield. Also, the welds are out of alignment, which will result in differing levels of wear, if nothing else.
Choosing metric chain is an individuals choice. One option would be to check a sample for galvanizing thickness and buy when you find a batch with a coating in excess of 100 microns. Another would be to resist replacement for another year, with the hopes that CMP and Maggi can improve their game and get the galvanizing to adhere.
We remain slightly ambivalent toward G70 chain and anyone opting for this route would need to weigh Maggis strength but only moderate abrasion resistance against the slightly lower strength of the Peerless or Campbell product and its much better abrasion resistance. Our recommendation would be American chain as it will have a much longer life. Frankly, if we were to look to high-tensile chain, we would seriously look at Armorgalv G80 (rather than HDG G70), as it is stronger after galvanizing, has greater ability to deform under stress, and has the potential to be more abrasion resistant.
Our ongoing tests of Armorgalv-coated chain so far appear to support the licensors contention that the coating is more abrasion resistant than conventional hot-dipped. In fact, the average of Armorgalv wear over the first 30 days was 50 percent that of the average hot-dipped, meaning that Armorgalv could last twice as long. However, to have twice the life, the coatings need to be the same thickness, and our examination suggests current Armorgalv coatings are too thin, and possibly not using the harder surface to best advantage.
The U.S. Navy (in some projects) and a major American utility have opted for Armorgalv instead of hot-dipped galvanizing, but this choice seems based on corrosion resistance rather than the aggressive abrasive environment of the seabed. We are looking at this issue in more detail currently and will report when the abrasion tests are completed. For high-test chains, we could not hesitate to consider Armorgalv coating (as it should allow repeated coating) and allow better strength retention. We have also found Armorgalv ideal for coating intricate parts, such as hammerlocks and specialist shackles, and will again report separately.
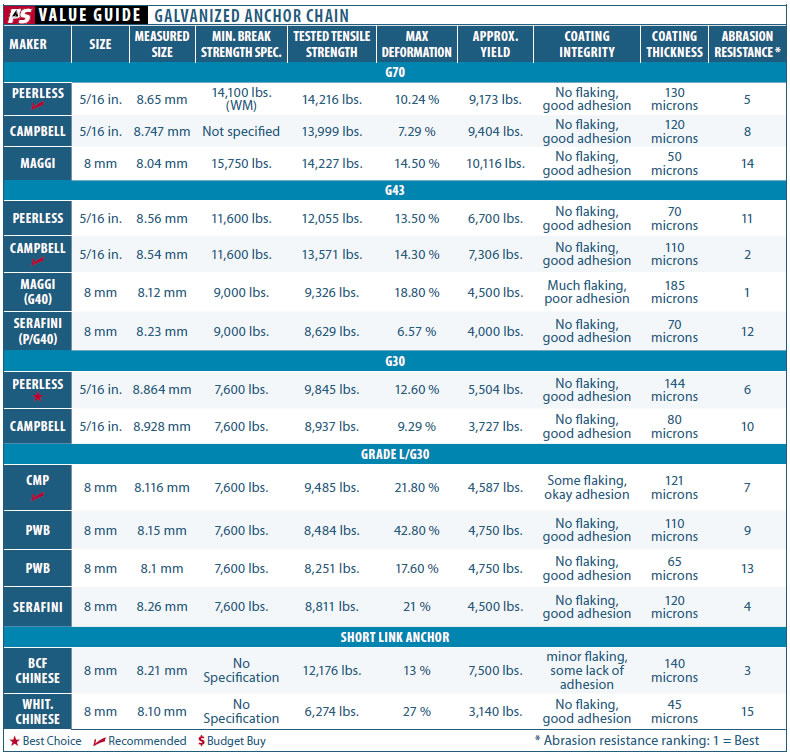
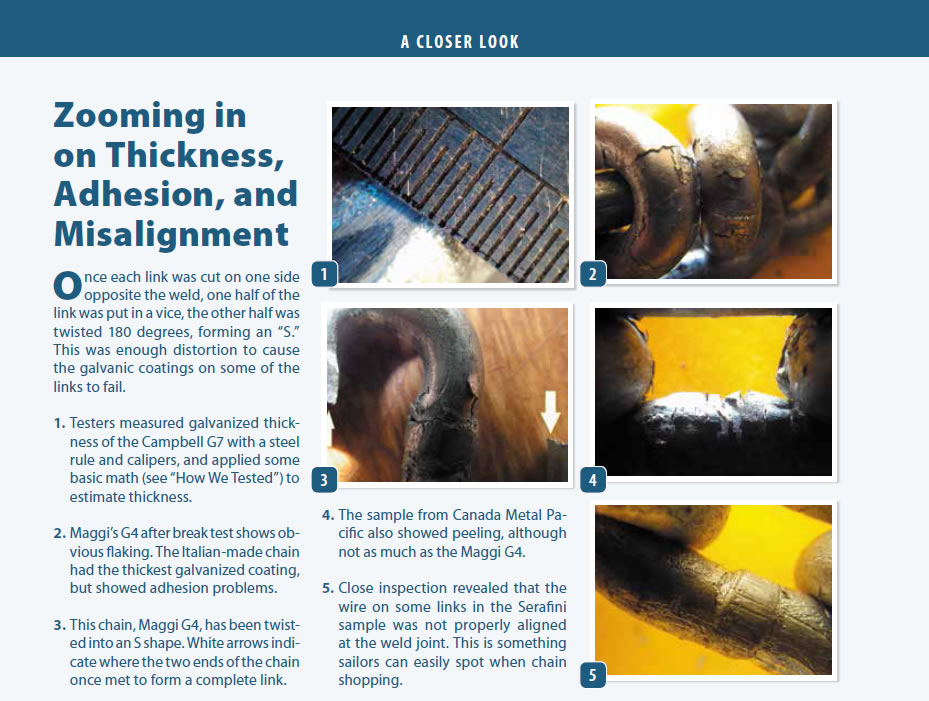
For my boat, based on the standards, I should use 3/8″ G30 or 5/16″ G4/40/43. G30 is .5lbs per foot heavier. In my case, with 300′ of chain, that’s 150 lbs. On my bow… How is that not a significant consideration? How is the extra weight, on my bow, more “sensible”? Perhaps we have different definitions of “cursing sailor”.
If g4/bbb weight ratio is 1.04/1.34, would the holding ability of 100m of g4 be equivalent to 78m of bbb in 20m of water?