Whether youre upgrading your boats electrical system or simply adding on a new piece of equipment, the question of which wire to use arises. Following the most common advice, “buy only high-quality marine-grade wire,” is ambiguous and can be unnecessarily expensive. Other suggestions are more explicit, recommending tinned multi-strand “Boat Cable” labeled “UL 1426 Type III,” which indicates that a wire is finely stranded (Type III) and complies with Underwriters Laboratory (UL) standard UL 1426, the wire standard most commonly applied to boats. When it comes to a vital systems component, paying more for a high-quality product is excellent advice. However, it is important to recognize that the term “marine-grade” is a marketing construct and that there are a variety of wire types that exceed government and industry standards for onboard wiring. Because these types of wire can be 10- to 15-percent less expensive than high-quality boat cable, PSwanted to determine whether any of these other options would be acceptable for the cost-conscious sailor.
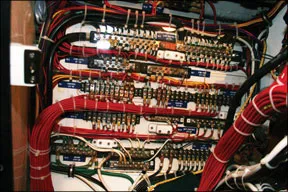
In July of 2010, PS published the results of a six-month saltwater chamber torture test of wire, crimp connectors, and corrosion inhibitors. Using a moisture chamber designed to mimic years of use in a harsh marine environment such as a bilge (see Test Details, page 15), the test focused on the durability of tinned wire, non-tinned wire, and various wire connectors. It also examined whether using a corrosion-inhibiting product could help extend the life of these wires and connections.
Although the UL 1426 says the wire “may” be tinned, most boat cable bearing that label is tinned, and this adds to the cost. In tinned wire, each strand is “dipped” in a protective alloy coating. Tin is expensive, as is the process of tinning, but this sacrificial coating has been proven to extend the life of wire, particularly in moist environments. Is the extra expense of pre-tinned wire worth it? Are there other approved varieties of pre-tinned or untinned wire that might hold up as well? Thats what PS hoped to find out.
As we reported in July, after six months of accelerated testing, some of the non-tinned wire in our test showed little sign of corrosion. There were very few failures, so we extended the test to one year, and this yielded some much more interesting results. After 12 months of exposure (the equivalent of several years in real-world use), some wires clearly did better than others, and some corrosion-blocking products stood out as superior. Interestingly, the best rust preventers after the first six months were not the best in the long term.
For system conductors, the American Boat and Yacht Council (ABYC) Standard E-11 recommends wire that meets UL 1426, or that the insulating material meets the temperature rating requirement of Society of Automotive Engineers (SAE) J378 Marine Engine Wiring, and either SAE J1127 Battery Cable, or SAE J1128 Low-Tension Primary Cable. The ABYC standard also lists three different tables of conductors that are also acceptable. The ABYC standards specify insulation ratings, number of strands, color coding, and the size of wire required to prevent excessive voltage drop. For those contemplating re-wiring a boat, a good understanding of the voltage drop tables and wire standards, explained well in Nigel Calders “Boatowners Mechanical and Electrical Manual”($35, International Marine 2005) is crucial.
What We Tested
For this review, PS tested the three types of wire approved by the ABYC: Ancor tinned boat cable (UL 1426), untinned automotive primary wire (SAE J378) from Southwire, and machine tool wire (UL 1015/1230), also from Southwire. Marine boat cable (UL 1426) is finely stranded and uses high-quality insulation that is impervious to water and oil, and is resistant to oxygen permeation. It is not always tinned. Automotive primary wire is untinned, and because SAE standard sizes are smaller than the American Wire Gauge (AWG) sizes used by the ABYC tables, you need to compensate for this when calculating voltage drop.
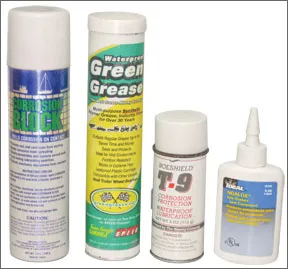
Machine tool wire (MTW), used in demanding industrial applications where moisture and oil are present, has slightly thicker strands than SAE wire. Strands can be tinned or untinned. The U.S. Coast Guard and the National Electrical Code (NEC) also approve all three of these wire types for onboard applications not directly connected to vibration sources such as motors. It is important to recognize that there are varying degrees of quality among wires that meet the same standards. The number of wire strands (more strands yield a more flexible wire), voltage rating, and temperature ratings of the insulation, for example, can vary. Insulation temperature and voltage ratings are particularly important for high-voltage applications or engine-room use. For most applications, wires stamped “105 C dry,” “75 C wet,” and “600V” will be more than adequate. Lower voltage and temperature ratings also will work in many cases, but the cost savings is negligible.
One question testers wanted to answer was whether the thicker strands of the machine tool wire might hold up better to corrosion than the thinner strands of non-tinned automotive wire or tinned marine wire. They were also interested in the value of the tin coating on marine wire versus plain copper primary wire.
PS tested only well-formed crimps made with a ratchet crimper. These meet the industry standard, are easy to make, and have proven very reliable. Most of the terminal fittings for this test were tinned copper fittings made by Ancor (ring crimp connectors and terminal blocks) or Ideal (heat-sealed crimp connectors and push-on connectors). We also tested a limited number of tin-tin spade connections. We tested two types of terminal strips. Three samples used tinned copper terminal strips, and one set used an aluminum terminal strip. Although aluminum is not an accepted terminal material, a significant number of older boats use the mast as a ground conductor for lighting circuits.
The last order of business was corrosion preventers. The variety of corrosion preventers has ballooned since the days of Cosmoline, the thick greasy rust preventative that dates back to the Civil War (and is still available under the name RustVeto 342). In our two-part test of electrolytic corrosion sprays (April and September 2007), we found six products that stood out: Unshielded T-9, Corrosion Block, Corrosion Pro Lube, CorrosionX, CRC Heavy Duty Corrosion Inhibitor, and TC-11. For this test, we focused on five samples that represent a cross-section of the three most common types: Boeshield and Corrosion Block, representing spray-on and other thin-film products; No-Ox-Id and Green Grease, representing thick terminal or bearing greases; and Noalox, representing thick greases with sacrificial metal or other chemical components. All of the products except Noalox, which contains aluminum powder and is weakly conductive, can be defined as dielectric compounds. They block the flow of oxygen, water, and most importantly, electrons. Without an electric current, there can be no galvanic corrosion.
Evaluation of the Samples
While the six-month report was based on non-intrusive inspections of the terminals and wires in each sample, this one-year report involved a bit of surgery. Once it begins, corrosion can creep up the wire behind the insulation where it is invisible. To see which wire type or wire and coating delayed or prevented this process, we stripped the insulation back 3/4-inch from the terminal on each sample to check the wire condition. Testers also unbolted all of the fittings from the terminal strips and looked for corrosion under the fittings. As in the last comparison, testers also checked continuity and resistance using a 10-amp lighting load. Power was supplied by the house bank of a boat plugged into a shorepower battery charger. A multimeter capable of measuring a 10-amp current was placed in series with the samples and a 100-watt nominal 12-volt deck light. Current varied from 8.0 to 8.3 amperes, and the voltage varied from 13.2-13.3. Resistance was determined by measuring the voltage difference across the test samples and applying Ohms Law: Ohms = volts/amperage.
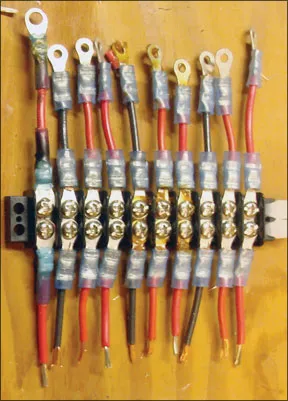
Photos by Drew Frye
What We Found
Because the materials investigated are inherently corrosion resistant, we knew we were in for a lengthy project. Here is a recap of our earlier findings, plus those of our one-year report, which is also presented in the accompanying tables:
2 weeks
At this stage, tin is clearly protecting the copper by becoming a sacrificial anode. Some loss of tin from crimp connectors was apparent on unprotected samples as deposits under the samples. It was clear that in the presence of uncontrolled galvanic corrosion, tin plating provides short-term protection. Bare copper wires begin to darken unless protected with a coating or a sacrificial layer. The thinnest of the anti-corrosion coatings began to fail almost immediately, as evidenced by darkening of the wire under the coatings.
Three months
The tin coating begins fading away. It protects by being sacrificial, and only the most effective treatments are able to maintain good-looking ring terminals. All of the wire ends are looking poor; however, the tinned wire looks noticeably better.
Six months
Surprisingly, as ugly as the wires and connections had become visually-and nearly all of them looked very bad-only one complete failure was observed and no small increases in resistance were observed. All of the bolted terminal connections showed less than 0.05 Ohm resistance. Only the un-treated push-on connector had failed, indicating the effectiveness of an anti-corrosion coating for this connection and the vulnerability of this type of connector.
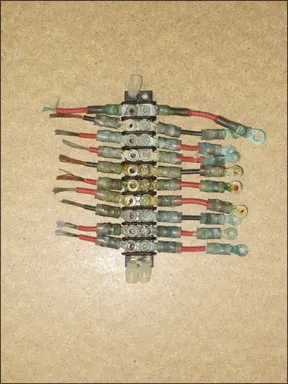
At the six-month mark, it was clear that untinned copper does not deteriorate as quickly as some anecdotal reports contend, particularly if it is well insulated, and well sealed at the connectors. Faults or voltage drops are more likely the fault of crimp connection, or deterioration at the wire ends, which can be a much simpler fix than a wholesale rewire.
While heat-shrink protection of fittings adds reliability to any connection, those with conventional connectors held up well at the six-month mark, suggesting that these are overkill for “dry” connections-fans or lights in the main saloon for example. The best application would be truly wet areas where immersion and stray currents are likely, although these are not good locations for connections anyway. For the best protection against moisture intrusion, heat sealed butt connectors do a very good job of positively sealing the wire from the surrounding water electrolyte and prevent stray current hazards and damage.
One year
Although none of the remaining wire or terminal samples failed continuity testing, their outward condition would have led one to believe that the entire length of wire was shot and needed replacing. That opinion changed once the testers unscrewed each wire from its terminal block, and stripped the wire insulation back about 3/4-inch.
Tinned wire suffered less visible corrosion than bare copper wire, and interestingly, none of the preventative treatments appeared to have improved the tinned wires corrosion resistance. Machine wire suffered considerably less damage under the insulation than SAE wire. The difference in strand size and difference in insulation may both play a part.
Corrosion inhibitors proved very effective on aluminum junctions. . . but they should be reapplied frequently. When disassembling the aluminum terminal strips to check under the screws for 1-year corrosion, testers noted that all of the samples disintegrated. As we saw in the six-month report, the heat-sealed crimp connections offer excellent protection in damp conditions. Even the least-expensive untinned SAE wire remained pristine behind the seal.
As for the corrosion preventatives, Boeshield provided less visible long term protection than other spray products, and it faired little better than untreated samples. It did, however, protect the push-on connector. This was a surprise,
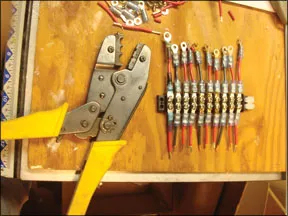
since Boeshield did well for the first six months. Corrosion-Block provided significant protection for both wires and terminal block screws under very tough conditions. Terminal grease provided some protection in torture chamber conditions for wires and excellent protection for terminal block screws. No-Alox did not perform as well. Again a surprise, as this product showed promise in the beginning.
Conclusion
Its important to keep in mind that although our test spanned only 12 months, the conditions it replicated were comparable to many years of real-world exposure. The exception would be any connections that are located in the engine room bilge, which might see the same sort of abuse in real time. Tinned wire clearly performed better in our torture test. However, no wire or crimp failed, so all three types can be considered suitable options for onboard wiring. However, keep in mind that if cheap SAE wire is exposed to corrosive conditions for several years, it is most likely to fail over its full length, turning black under the insulation. Replacing a crimp will mean replacing a length of wire, not an exciting proposition.
The machine tool wire performed much better; the thicker strands and better insulation shrugged off the effects of moisture and salt. This wire grade appears to be an economical and widely available alternative to tinned marine wire. Machine tool wire is not approved for high vibration applications-direct connection to engines and motors or battery cables. However, it is approved for use in all other marine locations, and you can buy pre-tinned grades.
Ultimately, if you are looking for the wire that best resists corrosion over the long-haul, particularly in wet locations, high-quality tinned UL 1426 “Boat Cable” is the right choice. When the wire insulation was stripped back, it was clear that the tin helped delay the wicking of corrosion along the length of the wire. Although the thicker strand wires in the machine tool wire proved effective defense against corrosion, the finer strands in Type III boat cable generally crimp better, forming a gas-tight, water-tight mass at the crimp-apparent at the microscopic level. Over the course of thousands of heating and cooling cycles, moisture can creep up the tiniest crevices. We did not observe this effect at any of our crimps; however, opting for the more flexible, finely stranded Type III only adds about 10 percent to the cost, making it a sensible first choice.
In the field of rust preventers, Corrosion-Block did well for a light product. However, the heavy terminal grease No-Ox-ID was the only product to provide lasting protection on the terminals, primarily because it didnt rinse off as easily. The best value? In consideration of the small amounts used and cost of troubleshooting or repairing a single failure, it is worth paying more for the better coating. Use Corrosion-Block where access is limited and No-Ox-Id terminal grease or a similar heavyweight for all terminal block screws where moisture is possible.
Ultimately, the key to long-term protection is at the terminal. Connections that are well sealed will greatly prolong the life of ordinary automotive wire, while the best tinned wire will fail prematurely if terminal connections are not well sealed. The most important consideration seems to be making a good tight connection. That we had no crimp failures in true torture chamber conditions speaks volumes for a good tight crimp, where the strands and the terminal are essentially welded together by the pressure of the crimp.
I had a failure of one out of about 20 connections on a vertically mounted terminal block. This wire corroded at the unsealed (all were older pre-heat shrink technology) connection to the loop connector.
This wire, to the lowest terminal, did NOT have a “drip loop” to reduce condensation from going up to the crimp connector.
CorrosionX – ?