Tapping holes is a skill that requires some practice. Start with a piece of scrap metal, because mistakes in a spar are impossible to erase.
Single taps cost about $15, though you will need a handle. A small set (#8 through -inch) sells for about $60. Carbon steel taps are fine for aluminum. High speed steel is required for stainless steel. Chose starting taps for typical through-threading work. Taper and bottoming taps are used sequentially for blind holes and are harder to start.
1. Use cutting fluid (3-in-1 Oil also works for small jobs), for both drilling and tapping. This improves the accuracy of the threads.
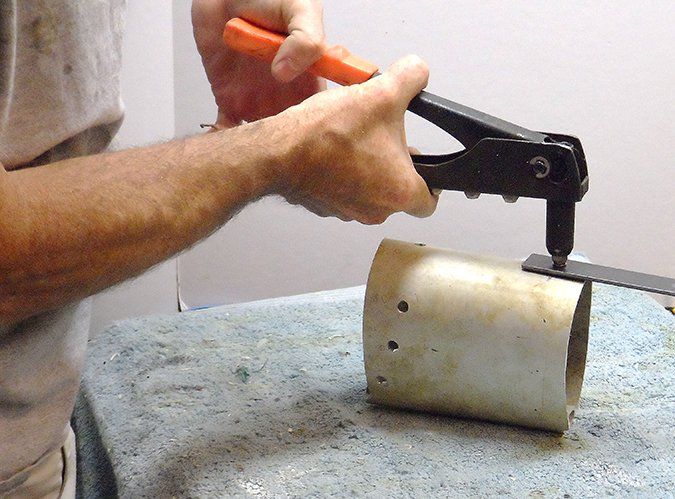
Drew Frye
2. Drill the hole square and the correct size. It is best to carefully match the tap to the fastener but drilling to the nearest 1/32-inch is generally sufficient in aluminum. A #10 coarse thread screw (24 threads per inch) calls for a #25 tap drill. A #10 fine thread screw (32 threads per inch calls for a #25 tap drill. (Most screw suppliers have a table to determine the correct tap and drill size.)
3. Start the tap with firm downward pressure, turning and resetting your hand for the next turn without disturbing the tap. Keep the tap very square. You should be able to feel the tap bite within turn, and the threads should be stable enough for full turns after about two full turns.
4. In thin materials (less than -inch diameter), continue turning until the tap is well through and is turning easily. In thicker materials you will need to clear the metal swarfs (chips). These should start to thread out through the flutes in the tap where they can be brushed away. Forcing the tap back out over larger swarfs can damage the threads in soft materials.
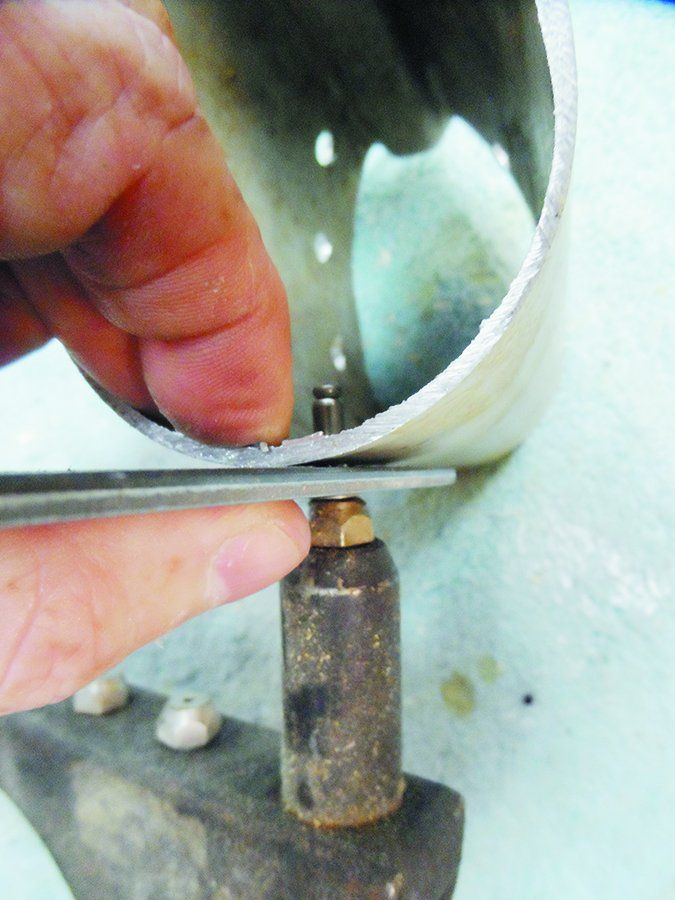
Drew Frye
5. Back the tap out gently. Blow the remaining chips out with a straw or small brush.
Machine screws threaded into soft aluminum spars need to be carefully tightened.
If you feel any decrease in resistance, stop. For testing, we used these torque values: 3/16-inch coarse-thread screw in 12 gauge aluminum (.08 inch thick), 10 inch-pounds torque; a 1/4-inch coarse thread screw in 10 gauge aluminum (.1089 inch), 20 inch-pounds torque
Riveting
Rivets are more forgiving of operator error or inexperience. So long as the hole is drilled the correct size, the rivet is the correct draw length, and the materials are pressed together when the rivet is fully upset, all that is needed is a hard squeeze. If the rivet is too long, it may fail to clench properly and will be weak. Often, repeated squeezing will correct for minor over-length situations.
If the rivet is too short, the blind end will not be able to fully upset on the backside. The fitting must be pressed firmly to the spar; if the there is a gap, this increases the draw up length and may cause failure. Although rivets are very good at drawing the hardware tightly to the spar, fit is essential. The range of close-fit for each rivet length is small.
Blind rivet tool for rivets up to 3/16-inch costs $40-$60.
Removing Fasteners
Once corrosion has settled in, removing small fasteners from aluminum is a challenge. Machine screws should be installed with anti-seize (see PS July 2018). If stuck, a few good raps with a hammer followed by an all-day soaking in PB Blaster is often helpful. Blind rivets must be drilled out, but that is usually quite easy, since the rivet guides the drill and only the head flange must be drilled off. If the rivet begins to spin, grab the head with vise grips. Failing that, either remove the head with a sharp chisel (easy if the drill made any progress) or delicately grind it off. Pry up the remaining bits of the head and punch it through. Generally the hole is completely undamaged and is reusable.