
In our upcoming test of marine sealants we looked at ways to develop bonds between common polyurethane sealants and polyethylene plastics-the kind of plastic used in a variety of marine products ranging from fuel tanks to baseplates. Starboard is one of the most common brand name high-density polyethylene materials, and it is notoriously difficult to develop a good bond with Starboard using conventional sealant/bedding compounds.
Polyethylene derives many of its best characteristics from its completely inert character. Complete chemical resistance makes it a great choice for tanks, including gasoline, potable water, and holding tanks. There is nothing to leach from the plastic, since plasticizers (phthalates) are not used. Ultra-violet resistance is reasonably good when treated with UV inhibitors. It is completely resistant to corrosion, and it is easy to machine. The downsides are that polyethylene creeps under sustained load and it cracks-making it no good for backing plates and most structural applications. Also, it can only be reliably bonded by thermo-welding. Although Sudbury and some other companies have developed sealants specifically for sealing polyethylene, most adhesives and caulks will not work with the material. This is why the tips of caulking guns are polyethylene; even un-cured caulk barely sticks.
But there is a partial solution to using an adhesive sealant with polyethylene. While the chemistry of polyethylene is stable, it will burn. If exposed to flame, the surface layer undergoes chemical changes that dramatically improve bonding. In what is known as flame treatment, a propane torch is played across the surface of the plastic until the appearance changes from reflective to dull. It is important not to overheat as the material will melt. You need just enough heat to take away the shine. A more certain way to judge the effectiveness of the treatment is to pour a little water on the surface. If the water beaded instantly, bonding will still be difficult. However, if the water sheets out for at least a few seconds, as it would on a well-prepared fiberglass or metal surface, it should hold a bond.
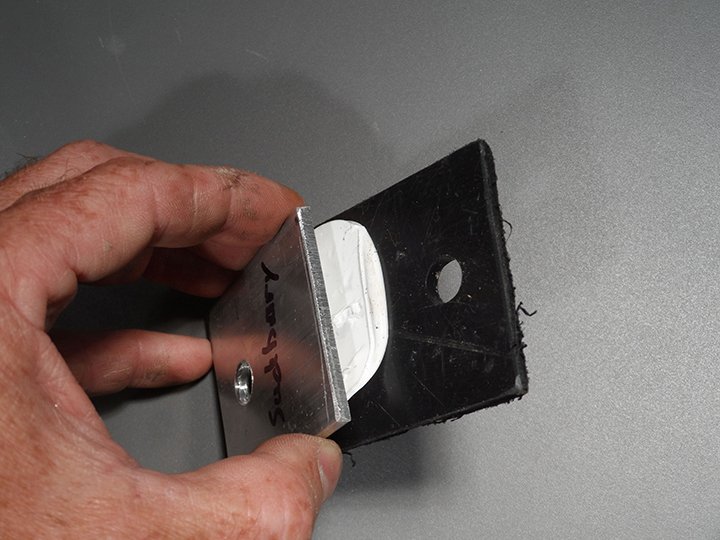
How strong is this bond? In our testing, we found the shear strength of the bond on a heat-treated piece of polyethylene to be about 2-3 times stronger than an untreated sheet. For example, the shear strength of the bond on a 30-square inch Starboard winch pad was about 900 pounds. With treatment, the bond held to about about 2,400 pounds. The pad sits beneath a winch with a maximum working load 1,753 pounds; this load is shared with the deck via the bolts. Thus, without flame treatment it is plausible that the pad will shift causing a leak, but that with treatment it probably hold tight. Not enough for true structural bonding, like epoxy to fiberglass, but enough to make bedding considerably more secure.
Could you repair a cracked polyethylene tank using this process? Sure. So long as there is enough area for the bond to develop, this could save the trouble of a complete replacement. Of course, polyethylene tanks often fail at the corners and welds, making such a repair more difficult.
Hey Sir! Interesting and helpful however, I would also recommend scuff sanding the polyethylene with some fine 320 or higher grit sandpaper to dull the finish.
Dan in Arkansas