A trailer expands the sailors horizons, but like any endeavor that involves automobiles, it adds another layer of risk and responsibility. Compared to our boats, a trailer is deceptively simple, and this often causes us to overlook the obvious warning signs of impending problems.
Last summer, Practical Sailor Technical Editor Ralph Naranjo got a firsthand lesson in what happens when you ignore your trailer for too long. He was carefully backing his Cape Dory Typhoons trailer into position at the local ramp when the wheel hub spindle sheared off the axle tube, effectively leaving him with a single-wheeled trailer that was can’ting precariously to port. Although blocking the neighborhood ramp on a Friday afternoon does nothing for one’s self-esteem, had this happened on the highway, or even when traveling on a local road at 30 miles per hour, the consequences could have been dire.
Ralph documents the reconstruction of his trailer in the January 2016 issue of Practical Sailor magazine. He also describes the important steps we can take avoid running into similar trouble or worse when we take to the roadways. Some of the most useful information on the subject came from Mike Orro the president of Triad Trailers, a company that has specialized in making sailboat trailers for more than 30 years. I’m highlighting here some of the advice that Orro shared, including key inspection points to check when preparing your trailer for a long road-trip or another season of launches.
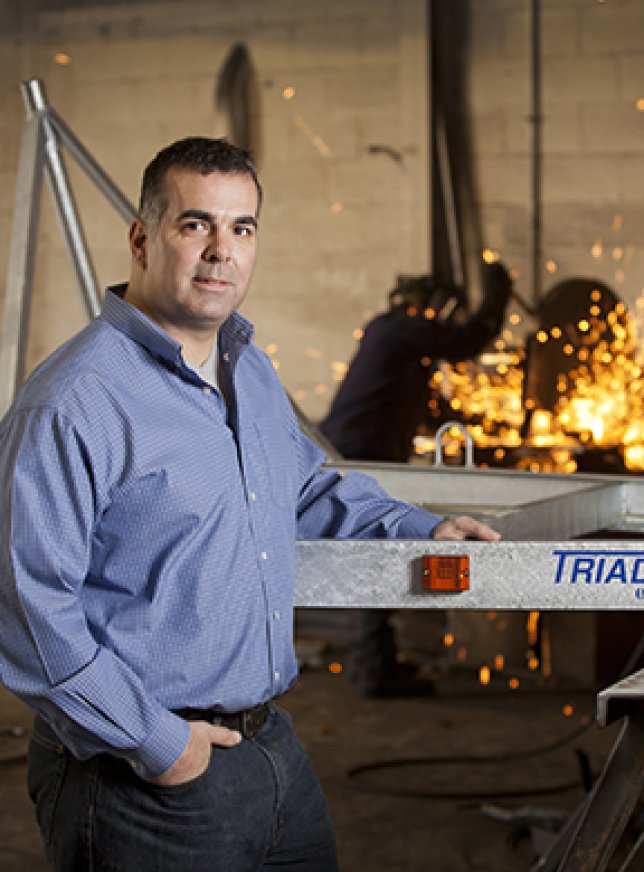
Courtesy of Triad Trailers
Hub Grease
Most boat trailers have a grease zerk fitting built into their axles that allows a user to simply attach a standard-sized grease gun and pump grease into the system. As the user continues to pump, the grease is channeled through the center of the axle, eventually exiting at the rear end of the spindle, just in front of the grease seal. As new grease continues to be pumped, the old grease will come out of the bearing cap, and it should be captured and properly disposed of. A change of color and viscosity designates when the new grease has filled the hub. If an axle is not set up with a grease zerk system, the bearings need to be repacked by hand. This requires removing the hub/drum and grease seal.
All too often, bearing greasing is neglected or never completely changed. Bearing grease deteriorates over time, losing its viscosity and eventually its ability to keep the bearings cool. Continued deterioration of the grease will ultimately lead to bearing failure. If you’re lucky, you’ll have a bearing failure that is relatively easy to repair-but you’ll need the right bearings. Automobile bearings are generally not interchangeable with trailer wheel bearings.
If you’re water launching, there is a good chance that water enters the bearing cavity. This inundation, coupled with poor quality or older grease, can wreak havoc with both the wheel bearings and the axle. Once the bearings begin to rust, they generate friction, which essentially heats up the bearing. If the current state of the grease is unable to cool the bearings, they get so hot that they can actually weld themselves to the axle spindle-a catastrophic failure. Chances are that the axle spindle (surface where the bearings ride) will be destroyed and the axle will no longer be usable.
A bearing failure puts a dent in a family vacation, while an axle failure ruins the entire holiday. Most trailer repair shops do not stock trailer axle beams, so an immediate repair is unlikely. If the axle on your trailer is not built to popular size dimensions, it can take up to two weeks to have an axle made. So check bearings and replace the bearing grease as a part of yearly maintenance. A good rule of thumb for standard bearing grease systems is to change the grease every 12 months or 12,000 miles.
Brake Check
The second most common problem that Orro said he sees is a lack of brake maintenance. Most of the problems start right at the actuator and with the brake fluid. Follow the brake manufacturers maintenance recommendations and specs regarding brake fluid. Another issue with brakes is corrosion. Boat trailers operate in a harsh environment, especially ones used in salt water. Brakes should be checked prior to the beginning of each season or at the very least annually, especially drum brakes. Disc brakes are preferred because all of the components of the brake system are exposed so potential problems can be easily seen. This is not the case with drum brakes. All of the brake components on a drum brake are hidden inside the brake drum, so its extremely difficult to see whats going on.
At a very minimum, Orro recommend, the brake fluid level should be checked and the brake system should be checked for proper operation on an annual basis. Each brake actuator should have a way to simulate the brake activation without needing to drive the trailer. Get the make and model of the brake actuator, and go to that manufacturers website and review the owners manual. In the manual, there should be instructions on how to check the brake system. If the brakes are not engaging and the brake fluid reservoir is full, its time to pull the brake drum and do an inspection. Drum brakes also need to be periodically adjusted.
Tail Lights
Though they’re not structural, trailer lights play a crucial role and should always be checked for proper operation. Components are fairly inexpensive and can usually be found at big box stores or a variety of automotive stores. Most of the time, a towing vehicles lights cannot be seen when a boat is loaded on the trailer, and trailer-mounted lights are a legal necessity. One way to prevent light failure is to mount them on extensions (PVC tubing is common) that keep them above the water when the boat is launched.
Hardware
Finally, be sure to check the hardware holding components to the trailer frame. For the most part, some surface rust is expected. But when hardware and nuts and bolts begin to flake rust, as opposed to showing a small amount of scaling, you have a serious corrosion problem, and its just a matter of time before that component fails. Flaking rust means its absolutely time to change that particular component.