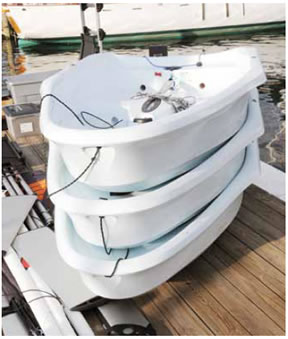
288
One of the themes seen among the new entries is a trend toward thermal-setting rather than thermal-fixing plastic construction. The latter is representative of the most common approach to fiber-reinforced plastic (FRP) boatbuilding. A process in which room-temperature liquid-resin systems are used to wet-out reinforcing filaments in what has become generically referred to as fiberglass boatbuilding.
A radical departure from wooden boatbuilding when it hit the waterfront a half-century ago, FRP construction has become the status quo. The process involves dry fiber reinforcement being placed in a female mold, and these woven, stitched, or chop-strand fibers are locked in place in a resin matrix, creating a composite material with an excellent strength-to-weight ratio, superb rot resistance, and good resistance to hydrolysis and other environmental factors. Heat derived from a chemical reaction in the mixed resin causes the transition from a liquid to a solid, thus the term “thermal fixing resin.”
Thermal-setting plastics involve polymers that are solid at ambient temperature, even on the hottest summer day. When it comes to rotational molding, ovens heat granulated plastic that’s been poured into a metal mold that’s rotated slowly on a double-axis jig. Gravity and heat (approximately 600 degrees) cause the granules to reach their melting point, and the carefully controlled rotation evenly distributes the plastic over the entire surface of the aluminum or iron mold.
The real art comes in selecting the right combination of RPM, angular tilts, and temperature fluctuation. The cooling process is as important as the heating side of the cycle, and once the mold is back to room temperature, all that’s left is the extraction of the part from the mold. This oven-based approach to boatbuilding revolutionized the recreational kayak market and has begun to do the same for the small-sailboat market.
Thermal forming is another rendition of the heat, reshape, and cool process. In this case, thin flat sheets of polyethylene or other thermo-setting plastic are heated and pressed into a mold to form complex hull shapes. The products created through these processes are tough skinned and abrasion resistant, though not as stiff or strong, on a pound-for-pound basis, as conventionally built FRP boats. The big upside for builders and consumers alike is the less labor intensive nature of the building process, a feature that can lead to lower prices and incentive to market lower-cost smaller sailboat hulls.
Hand laid-up FRP boats may hold the structural high ground, but they are also much more complicated to build. Roto-molded and thermo-formed hulls are a bit heavier, but like their kayak cousins, they have proven to be tough and durable—welcome attributes when the mix is between kids in boats and docks with hard edges. Early efforts yielded hulls that sagged during the hottest days of summer and boats that were too flexible, especially around the maststep and daggerboard entry points. Today, however, these issues have been resolved through better engineering and material selection, and as the accompanying Value Guide table shows, nearly half of the sailing dinghies in this roundup are made using thermal-setting plastic.