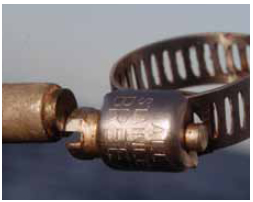
253
Stainless steel is exactly what the name says; the steel “stains less.” As PS’s February 2007 special report “Marine Metals Warning,” pointed out, stainless steel is not the maintenance free miracle material many boat owners imagine it to be.
Some stainless steel is more stainless than others. With over 500 different grades of stainless steel, only a few meet the mark for use in the corrosive marine environment. Most marine stainless steel is grade 304 or 316. Stainless steels are made up of metals with a blend of iron, chromium, and nickel. Chromium resists corrosion, and nickel resists acids.
Add a little molybdenum, which looks and feels like graphite, to the 304, and you get the more corrosive-resistant 316 stainless steel. Although 316 is near the top for rust-free steel, it is 85 percent as strong as 304. This is why bolts and screws are made of 304 and will often tarnish before the hardware they secure. Better looking than 316 is 316L. The L stands for low carbon, which is more suitable for welding.
Since 1997, Monitor self-steering vanes have been made of this metal. After many years in a saltwater environment, Monitors still look brilliant with little or no attention from owners. To get that brilliant finish, manufacturers of high-grade marine hardware give their 304 and 316 products an electropolish. Electro polishing is bathing metal in a mild acid with an electric current. It takes away all the impurities and makes the stainless shine. Old stainless-steel hardware can be removed from a boat and electro-polished again.
Some shine is only skin deep. Showing up in marine chandleries is foreign-made hardware that is bright and buff till it is installed in the saltwater environment. Here, the steel becomes “stain-fast.” Though not definitive, a magnet can help tell the quality of stainless steel. (Some higher-tensile precipitation hardened components like shackles can have weak magnetic properties.) You will find this true with many hose clamps. The band is of quality 304 or 316 stainless steel but the screw is often of an inferior 400 series and thus attracted to a magnet. The screw will rust which in turn causes the band to rust. Some hose clamps that are marked “all stainless” can’t be shaken free of a magnet.
Marine chandleries apparently do not hold their suppliers accountable for labeling. Lack of proper labeling makes it a customer-beware situation. There are manufacturers of hose clamps that get the stainless steel combination right. That quality hardware is well worth the price difference and actually proves less expensive because of its increased working life. A simple hose clamp failure can be catastrophic.
Moisture with little or no oxygen invites rust. Salt, which helps to hold moisture, is a catalyst for the process. This is why rust normally starts at the base of bedded hardware, at longitudinal joins of rolled handrails, or in pitted areas. Welded areas have a higher susceptibility to corrosion due to the heat upsetting the chromium and moving it away from the welded area. For this same reason, it is better to cut stainless steel with a sharp hacksaw, by hand, so it will not heat the metal. Sawing stainless steel with an electric cutting wheel overheats the metal. The stainless steel will rust where it was cut.
Inspecting stainless steel requires skill. What shines on the surface can hide decayed weakness within. Like termites in wood, the most unnoticeable crack can allow moisture to penetrate and rot deep into stainless. Sudden and catastrophic failure of stainless steels is common. Polishing discoloration from stainless steel can actually wipe away evidence of impending doom. Colored dye test kits and a magnifying glass can help to detect defects in stainless steel that lead to failure. But even new stainless steel boat hardware can unexpectedly fail. Stainless steel chainplates and mast tangs are notorious failure points due to cyclical loading and corrosion penetration at minute cracks.
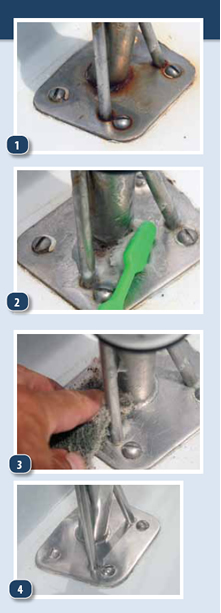
221
Most of a chainplate is hidden from view by a toggle and where the chainplate lives below deck level. In these areas, deterioration grows undetected. Removing a chainplate from the boat is the only way to properly inspect the piece. If there is any pitting or the slightest cracking, the plate should be replaced, not simply cleaned and reinstalled.
What stainless-steel deck hardware likes best is plenty of fresh water and mild soap to rinse away moisture-retaining salt and grime. On long rainless ocean passages, it can be helpful to scrub down the decks, even with buckets of seawater, to reduce the concentration of salt residue. The stainless hardware can then be followed with a wipe of a rag wet with fresh water. Chlorine is highly corrosive to stainless steel and other metals. Cleaners with chlorine should not be used on deck.
Getting out the shinola kit and buffing stainless steel before it rusts is a good practice. When rust has developed, it is still an easy exercise to buff.
Automotive stores and marine chandleries sell a variety of metal cleaners. The active ingredients of many of these cleaners is phosphoric acid or oxalic acid. These brighteners should be bought in a paste form rather than a runny liquid. A jar runny cleaner with a large lid will most certainly get knocked over on the deck of a boat, and this must be thoroughly rinsed.
When applying a paste cleaner, a tooth brush is a necessity for buffing into tight spots and working into the pores of welds. That agitation is then followed by buffing with a cotton cloth. More advanced rust might need cleaning with a green 3M scrub pad. Continued rusting in welded areas can be a sign of developing failure.
Applying automotive or fiberglass rubbing compound with a wax component to metal will help protect against corrosion, but in the real world, this protection doesn’t last long. A wipe of a light corrosion block oil is only a little more effective.
All this close, hands-on attention not only keeps the stainless looking bright but on some boats has prevented a major failure of the rigging. The close work makes it easier to inspect components, and the cleaning will often uncover cracked turn buckles, wire end fittings and other hardware before failure.