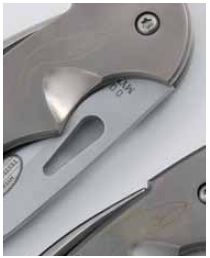
210
Titanium’s high price is only one thing that is keeping in the realm of mega-yachts and Cup boats. Some of the essential roles that lightweight metals once played in deck hardware are now being taken by high tech fibers like Spectra or Vectran. Carbon fiber laminates are also taking the place of metal fittings, at a slightly lower cost. Nevertheless many manufacturers see a bright future for titanium. Here is some feedback we got from manufacturers on this topic.
• John Franta (Colligo Marine, www.colligomarine.com): “Titanium has all the benefits of a metal, machineability, drilling, etc. and no corrosion. Particularly Grade 2 which has about the same yield strength as 316 and is not much more expensive. We make custom chain-plates out of it all the time. Our mast brackets are made from Grade 2 titanium also.”
• Tony De Lima (Forte Carbon, www.fortecarbon.com): “Titanium is a specialty material that requires an experienced machinist to cut, and titanium experienced welding shop to stick it together. Here in Ledyard, CT we are next to Electric Boat (the submarine guys) so are spoiled with experienced titanium welders. Most of our custom titanium parts are only machined and so we rely on our regular machine shop for milling. The most common parts we have made of titanium here are milled from strait bar stock and tube these include, joining ferrules and spreader bars.”
• John Myerchin (Myerchin Knives, www.myerchin.com): “By using pure titanium handles in our new folding rigging knives we have reduced the total weight of the knife, added a pocket clip and greatly reduced corrosion problem. . . .Since titanium is not a good choice for blades or marlin spikes, these components are still marine-grade stainless steel.”
• Russell Belben (Ronstan, www.ronstan.com): “We used titanium in the 1990s for the cheek plates of our runner blocks, especially for the Americas Cup boats. We rarely use titanium now for the following reasons: many classes now stop the use of titanium due to the high cost ; titanium is notoriously unreliable to weld; and titanium is very expensive relative to conventional alloys. . . . Titanium has been used effectively as a needle bearing on high load blocks making use of the materials strength advantage over the more conventional needle material Torlon.”