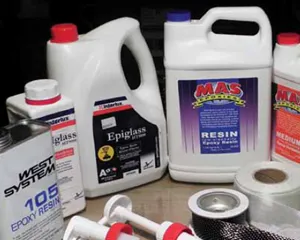
Photos by Ralph Naranjo
300
Just about every sailboat owner has at some point mixed up a batch of epoxy to fill a hole, glue parts together, or tackle a much more extensive project. Epoxy is the glue by which others are measured. It is the crème de la crème when it comes to picking a laminating matrix for high-tech structures.
Epoxy resin is a copolymer that reacts with an amine hardener, causing the mixture to transition from a viscous liquid to a solid. This crosslinking process involves a chemical reaction known as polymerization. Covalent, electron-sharing bonds are created, and the net result is a tenacious adhesive that can also have excellent water-resistant properties. Epoxy is a thermosetting resin, which means that heat is involved in the curing process. It’s the development of the three-dimensional large molecular chains and the resulting micro-grid-like structure that make epoxy much stronger than a thermoplastic.
There’s a big difference between gluing and laminating, and when it comes to sticking two materials together, epoxy’s ability to form an ionic bond wins out. This covalent electron sharing is missing when polyester resin is used as glue.
Polyester resin is a cost-effective and time-tested laminating partner in conventional E-glass boatbuilding, and it has justifiably been the mainstay of fiberglass-reinforced plastic (FRP) boat building for over a half-century. But polyester’s lower price-point advantage has been the key reason that it dominates production boat building.
A look at the resins used for constructing aircraft and high-performance boats tells just the opposite tale. In these applications, weight is the big enemy, and the product that offers a higher strength-to-weight ratio will be chosen despite a higher-cost-per-gallon. Carbon fiber and epoxy are among the most costly composites by weight, but their impressive mechanical properties and high strength-to-weight ratio justify the choice.
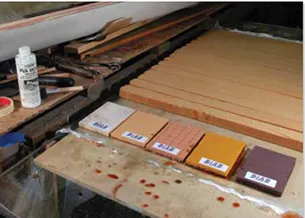
Photos by Ralph Naranjo
305
For example, the new Farr 400 is an all carbon-epoxy sailboat. Keeping weight to a minimum in an ultra lightweight race boat makes sense. Even on boats built predominately of E-glass and polyester resin, carbon masts, booms, and rudders are seen more and more often.
This month’s close look at four epoxy resins, readily available to consumers, involves both bench testing and real-world application. Our intent is to compare these products based upon their mechanical performance (strength, adhesive quality, hardness flexibility and toughness) and several key handling attributes such as wet-out, thixotropic nature (anti-sag), cure characteristics, and overall handling ability. In several of our tests, we also ran a fifth product as a control. It’s a much less expensive polyester resin (Evercoat polyester boatyard resin). This resin is similar to what is used to build many production boats and is a good point of reference in the comparison between polyester and epoxy resin.
What we Tested
The tests focused on brands aimed at the do-it-yourselfer. One major player in this market, System 3, said it was reformulating its epoxy. We will test the new formula when it is available.
West 105 Epoxy Resin has become as familiar to sailboat owners as Kleenex is to people with allergies. It’s a versatile marine-grade epoxy that blends water and chemical resistance with good mechanical properties. Over the decades, the company has combined a wide range of hardeners, fillers, fiber reinforcement, and instructional materials to turn its 105 resin into a multi-purpose product that suits a wide range of boat projects. The company’s Epoxyworks magazine is full of good advice for the do-it-yourselfer.
MAS Flag Resin is an all-purpose, medium viscosity, marine-grade epoxy that can be thickened to use as a gap-filling adhesive, fairing compound, or used straight as a fiber matrix. MAS also offers a low viscosity, 100-percent solid laminating resin specifically meant for wetting out thicker laminate schedules. Both of these epoxies use an easy-to-measure, 2-to-1 ratio for the resin-to-hardener mix. Mas epoxies don’t leave behind the waxy amine “blush” common to other epoxies, eliminating the need for washing and scrubbing between applications. They also have a great website with detailed DIY advice, the “Epoxy School,” and helpful videos (see Contacts).
Raka UV-inhibited epoxy is a custom blend of 100-percent, high solids, marine-grade epoxy that packs high strength and good watertight integrity in a medium viscosity, user-friendly resin. Raka offers fast and slow non-blushing hardeners that mix with resin at a 2-to-1 volumetric ratio, and can be blended to provide a midrange gel time. The company is also a great source of online laminating materials from tapes and cloth to Kevlar cutting scissors and mold release, foam rollers, and other handy supplies.
Interlux’s Epiglass HT-9000 is a durable marine-grade epoxy that mixes with hardener at a 4-to-1 ratio by volume. The almost odor-free resin is designed to be used for laminating, filling voids, fairing, and as a waterproofing barrier. Three different hardeners provide variations in cure time and adaptability to temperature range.
How We Tested
In order to keep variables such as ambient heat, direct sunlight, and day-to-night humidity shifts from affecting outcomes, we conducted our testing in a temperature-controlled shop environment. We repeated each test five times and averaged the outcomes as well as noted any extreme one-time measurements.
With each batch of resin, we used a new applicator brush, mixing pot, and clean squeegee. Mixing ratios and stirring the resin and hardener are critical aspects that control the final outcome. Testers closely monitored gel times and pot temperatures, and noted how these changed when different hardeners were used.
PS looked at these three main characteristics of each product:
Wet-out: The term “wet-out” implies saturation, and in this respect, it is a bit of a misnomer. Glass filaments never absorb resin; the finish that has been placed on the filaments during their manufacture bonds with the resin. The first test was a single-skin, wet-out evaluation using 10-ounce, 2-inch wide E-glass tape and 2-inch-wide, stitched, unidirectional carbon fiber. The intent was to determine the ease with which each epoxy resin saturated the woven tape and the unidirectional carbon. We measured how long it took for the white tape to turn transparent, and once cured, rated the evenness of the wet-out.
Hardness and flexibility: Ideally, cured resin will be both hard and flexible to resist impact loads and tension loads. We extracted a dollop of resin from each batch of epoxy we tested, placed it on a waxed glass table and left it to cure. These dabs of resin would later be used to determine the hardness of each cured sample. In order to limit the variables, we tested the hardness of the samples after one week of an ambient air cure.
Adhesive quality: A good resin will have tenacious adhesive properties. Bond strength was measured by laying up a 6-inch by 2-inch sample of 10-ounce E-glass tape on a glass surface free of mold release or wax, and at the same time bonding a 2-inch by 2-inch by 3/4-inch cedar block to the end of the FRP strip. This dual layer primary bond (FRP-to-glass and FRP-to-wood block) was allowed to cure for five days, and then the block was loaded with a tension measuring pulley system that put a shear load on the bonded surfaces. Both the bond release point and the mode of failure were noted.
Flexibility: Each test strip’s stiffness was measured by placing an increasing load on one end of each test coupon while holding the other end immobilized. Deflection was measured in degrees of arc, and the failure point was defined in degrees and pounds of load. The failure point was the angle where either the resin matrix failed or the fiber reinforcement sheared.
Impact resistance: This point-load test utilized a slide hammer-like jig that controlled a weighted mandrel. It allowed us to make precise impacts on each test coupon.
Findings
A few general rules prevail. Regardless of resin brand, don’t mix up too much product at once. Apply what you are planning to use from any single batch within 10 minutes or switch to a “slow” kick hardener. Resin in the pot will reach a gel state before the resin on the surface. If multiple layers of laminate, holding lots of resin, start to heat up too rapidly, use a few icepacks in Zip-lock bags to tame such runaway exothermic reactions.
One of the most important steps linked to a good laminate is referred to as “debulking” or the effort to squeeze layers of stitched or woven material together. This is best achieved through vacuum bagging, but a do-it-yourselfer can come pretty close using a serrated roller, squeegee, and careful attention to detail when wetting out multiple layers of reinforcement material. The goal is to eliminate all signs of dry spots and air bubbles. It should be noted that Mas, Raka, and West Systems also offer a lower viscosity epoxy, fine tuned for FRP lamination.
Wet-out: All of the resins we tested rated Good to Excellent in the wet-out test. Interlux’s Epiglass HT-9000 held a slight edge due to its slightly lower viscosity. After curing, all of the resins we tested showed a low air bubble content and excellent transparency. Each resin was also mixed with a variety of powdered thickeners and used as a gap filling material, fillet for bonding, and fairing compound. We preferred using a slow hardener to lessen the exothermic effect in such applications. The results of this testing will appear in a future issue.
Hardness and flexibility: Cured resin dollops and thin film smears were compared along with the single-skin test strip bends. The largest variations we found was within each brand and arose when changing from slow to fast hardeners. Switching to the faster gel-time hardener increased the cured samples’ hardness values and decreased flexibility. Engineers determining the unit schedule of any FRP structure carefully consider the need for stiffness versus flexibility when they choose a resin matrix. All of the epoxy samples rated higher in the “flex test” than the polyester control samples we also measured.
Adhesive quality: “Stuck like glue” is a phrase that took on a whole new meaning in this part of the test. The first attempt to measure the force needed to shear the bond broke the apparatus we set up to test the samples. After beefing up the test table support structure and repeatedly ripping bond samples from the surface, we saw several significant trends fall into place.
In all of the cases, epoxy provided an exceptional bond between wood and fiberglass. In shear testing, the typical failure mode was the shearing of the finish on the fiberglass tape itself. Nearly all of the epoxy-to-wood bond remained intact. The second fascinating take-away from this part of the test was that only Epiglass HT-9000 (the highest scoring in our shear test) left patches of resin stuck to the plate glass bonding table.
Flexibility: During this test, we discovered another of epoxy’s inherent attributes—its double-edged ability to retain excellent adhesive quality and elongation characteristics. On its own, this is not an overly valuable quality, as we found the dollop chips of resin to be neither much harder nor much stronger than their polyester cousins, but if you add fiber reinforcement, the whole deal changes. What happens is the flexibility of the highly adhesive resin adds enough stretch to keep the resin matrix intact as the fiber bundles comprising the laminate take up the load.
This symbiotic partnership between reinforcement fibers and resin matrix is just the opposite of what was found in the bad old days of ferro-cement boat building. In ferro-cement boats, the composite structure is based on a matrix (concrete) that will fail before the reinforcement can be fully engaged. Epoxy’s elasticity can be fine-tuned to the fibers it locks in place. Pros often post-cure epoxy composite hulls to stiffen panels and increase hardness.
Impact resistance: There’s something to be said for destructive testing—a tried and proven approach to engineering that still has its place even in an era of finite element analysis. Our point-load drop testing delivered some dramatic results and equally important lessons.
First of all, panel stiffness can be achieved through the use of core materials and fewer units of FRP reinforcement. But when it comes to keeping a floating log, bow of another boat or the ramrod at the end of our jig from penetrating a structure, there is no replacement for skin thickness.
We did find that, on a strength-per-weight basis, epoxy resin and carbon-fiber reinforcement offered the best resistance to penetration—even better that Kevlar. The latter has very good abrasion resistance, but it did not resist point loading as well as the carbon fiber/epoxy laminates.
In our initial point-load testing of a wide range of FRP sandwich samples, we found that by increasing the laminate skin thickness, we lessened the damage caused by the controlled drop test. Going from one to two layers of 10-ounce cloth on each side of the core was enough to show a significant decrease in the damage caused by the controlled impact.
The next question we asked ourselves was: Would substituting epoxy resin for polyester also improve impact resistance? Our findings showed an uptick in point-load resistance linked to the switch to epoxy. It was a distinct measurable gain, but the variation among the different epoxies was much smaller (all performing well in this part of the test).
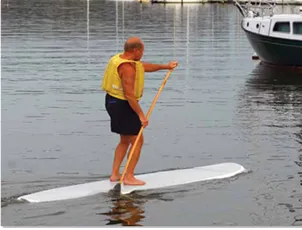
302
Conclusion
Our testing left us with some significant findings. All four resins exhibited Good to Excellent adhesive quality, and willingly wet-out E-glass and carbon fiber. Epiglass HT-9000 was the least viscous and nosed out the others when laminating multiple layers of material was the task at hand. It also had the most tenacious grip when it came to grabbing hold of an ultra smooth, squeaky clean piece of glass. In the shear testing, it was the only product that repeatedly left resin patches stuck to the glass table when the bond finally failed. In comparison, the polyester resin peeled off the glass surface as if it had been bonded to a greasy skillet. The three other epoxies all had a strong finish. West does a great job with its line of fillers and ancillary products; Mas and Raka utilize a friendly 2 to 1 resin/hardener ratio that is more forgiving when mix volumes are a little off. In the final tally, the win went to Epiglass HT-9000 and the fast hardener for its effective wet-out ability and top of the list adhesive quality, Raka took the Budget Buy prize with an $18.33/quart price tag.
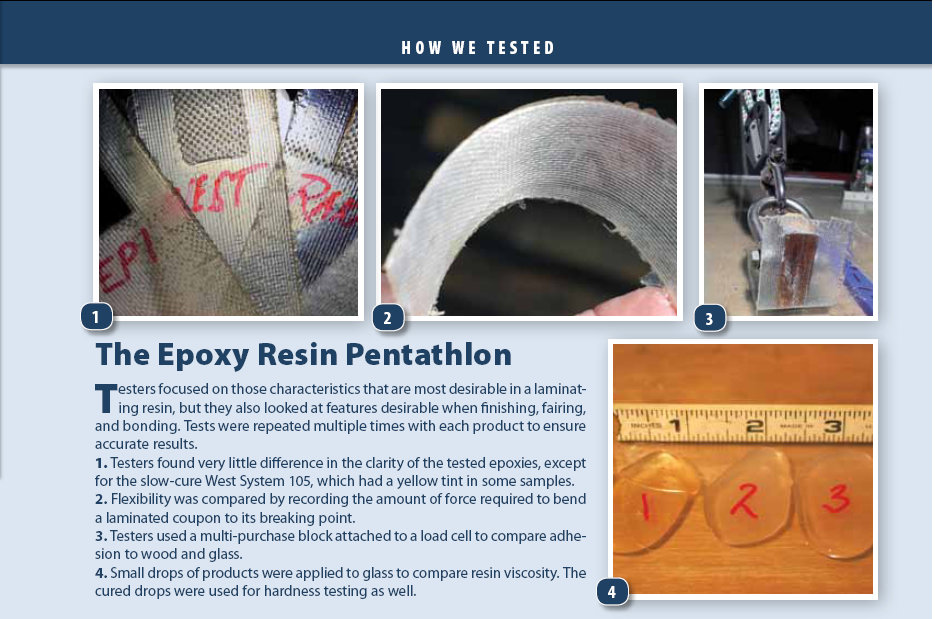
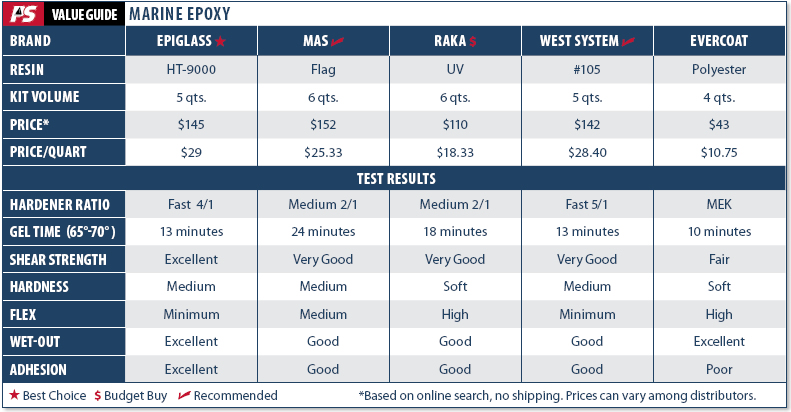
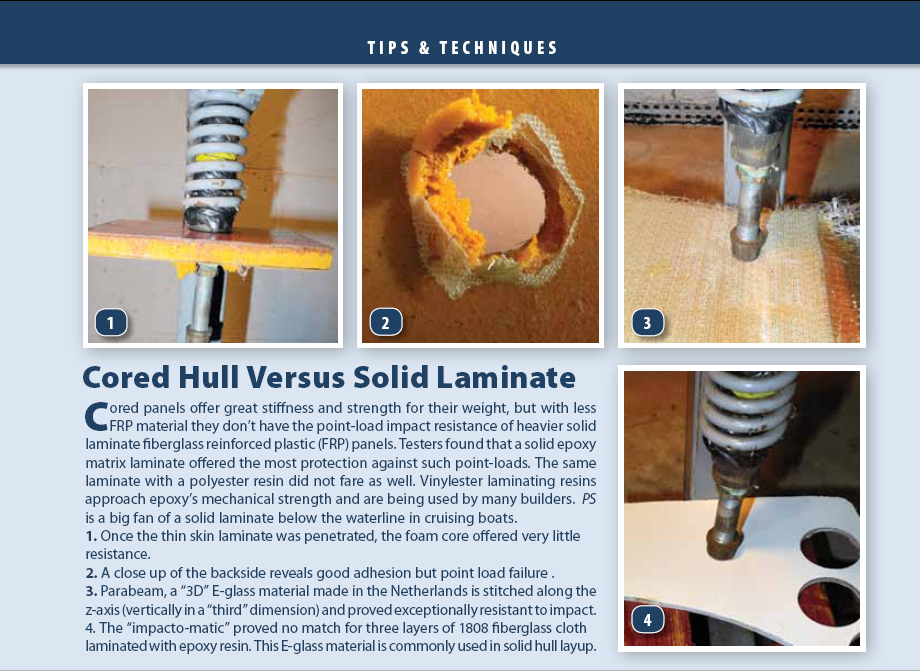
Thoroughly Thorough, enjoyably fun, Factually educational and more about scientific knowledge of sailboats than anywhere in one place.
One of the best marine epoxy coatings I’ve ever used is PC-11. It’s particularly useful if you want to make emergency boat repairs while you’re still on the water. Can stick to and bond to a variety of surfaces and materials.
I applied the Loctite epoxy brand while repainting my boat’s overboard, and it showed long-lasting, sturdy, and highly resistant results. Easy to sand and even possible to drill through it when needed for modification or repositioning.