Stainless steel is a miracle for boaters. It’s reasonably strong, stays shiny, and requires minimal maintenance. But savvy boaters also know it’s not corrosion-proof, only corrosion resistant (see “Marine Metal Warning,” PS February 2007). In fact, for many applications it is inferior to silicon bronze, the copper alloy that has served mariners for decades, (see “A Look at Stainless Steel vs. Silicon Bronze,” PS September 2014).
To ensure you get the maximum life out of your stainless steel, it helps to understand how stainless steel material resists corrosion and what we can do to protect it. In this report, we’ll compare several products that can be used to passivate stainless steel, a process that effectively stops surface corrosion in its tracks and offers longer-lasting protection than any wax or polish.
Because stainless steel contains high levels of chrome and nickel, instead of rapidly rusting in seawater like plain carbon steel will do, it forms a very tough oxide coating that is virtually corrosion proof. But this is only the case when the material isolated from other metals and exposed to air. Eliminate oxygen, and serious pitting is possible, often critically weakening the below-deck portions of chainplates. Pair it up with a dissimilar metal, even a different stainless alloy, and both surface staining and pitting can follow.
Corrosion often starts at welds because the heat allows iron to migrate to the surface, iron migrates to the surface, and pitting can start. Shackles and blocks commonly mix 300- and 400-series stainless in search of economy and the best mix of physical properties. Your stanchions may be made of 316 stainless, but it’s a fair bet the mounting bolts are 18-8, which lacks the 2-3 percent molybdenum that gives 316 superior resistance to seawater.
Passivation
Simple exposure to water and oxygen is normally sufficient to build a robust oxide film on 304 and 316 stainless. However, grinding and drilling can often start corrosion, caused by either overheating or the transfer of bits of iron from a contaminated drill or grinding wheel. In these cases, natural oxidation, polishing, and even common rust removal acids are not enough to stop the corrosion. To cure this, we need to use a specific process to leach away iron from the surface and from a microscopic layer below.
The industry standards for passivation are ASTM A967 and AMS 2700. These standards describe two general processes, using either 25-45 percent nitric acid or 4-10 percent citric acid. Our technical editor, Drew Frye, has used both processes to passivate chemical processing equipment. Nitric acid is cheaper than citric acid, but given the biting odor and the harm it does to other metals, we can’t recommend it.
Fortunately, testing has proven citric acid is just as effective, and much safer, requiring only common sense precautions. Diluted to 5 percent for soaking, it is no stronger than lemon juice (6-8% citric acid). Thickened brush-on products are typically 10-20 percent acid solutions and work more quickly. The acid will not only remove surface staining, it will leach iron from the top few layers and encourage the growth of a robust oxide film, protecting the steel far longer than waxes.
Controlling the process
The main factors influencing passivation are time and temperature. Do not increase the concentration beyond about 15%; testing has shown it doesn’t help. Twenty minutes of soaking is sufficient, but a few hours are better. The temperature should be above 70F, but 50-60F works if you wait and keep it wet, which is easy in cooler temperatures. NASA settled on 5 percent citric at 180F for two hours, which we liked for fasteners and fittings. For hardware with polymer parts such as blocks, the temperature should not be more than 120F.
ASTM lists five specific citric acid procedures. We tested using the three most relevant:
Citric Acids for Passivizing Stainless Steel
Maker | Milliard | Milliard | Nitric Acid | Spotless Stainless | Stellar Solutions | Stellar Solutions | Stellar Solutions | Stellar Solutions | Flitz |
---|---|---|---|---|---|---|---|---|---|
Model | Dry crystals | Dry crystals | 6% solution | Spotless Stainless | Citrisurg 77+ | Citrisurg 2310 | Citrisurg 2250 | Rust Rescue 200 | Premium Pollish |
Active Ingredients | Citric acid, 100% | Citric acid 100%, gelled with fumed silica | Nitric acid, 6% | Citric acid, 17% gelled | Citric acid, 10% slight gel | Citric acid, 16% gelled | Citric acid buffers | Calcium sulfate petroleum | Fine compound and wax |
Price | 8.5 | 8.5 | 35 | 24 | 26 | 26 | 26 | 28 | 10 |
Quantity | 32 oz. | 32 oz. | 16 oz. | 22 oz. | 22 oz. | 22 oz. | 22 oz | 32 oz. | 2 oz. |
Cost per Oz. (As Used) | 4 cents per ounce | 8 cents per ounce | 37 cents per ounce | $1.09 per ounce | $1.18 per ounce | $1.18 per ounce | $1.18 per ounce | 88 cents per ounce | $5 per ounce |
Citric 1: 4-10 percent citric acid, heat to 140-160F, soak for 4 minutes minimum
Citric 2: 4-10 percent citric acid, heat to 120-140F, soak for 10 minutes minimum
Citric 3: 4-10 percent citric acid, heat to 70-120F, soak for 20 minutes minimum. (This procedure is the one recommended by the commercial products we tested.)
AMS 2700 lists these citric acid procedures:
■ 4-10 percent citric acid, 140-160F, 4 minutes minimum
■ 4-10 percent citric acid, 120-140F, 10 minutes minimum
■ 4-10 percent citric acid, 100-119F, 20 minutes minimum
■ 4-10 percent citric acid, 70-100F, 30 minutes minimum
Some have called chemical passivation a poor man’s electro-polishing. They really aren’t the same thing. Also known as anodic leveling, electro polishing uses electric current to remove 5-10 microns (0.0002 to 0.0004 inches) of material, preferentially from the peaks. This is a micro-polishing method, so the surface must already be smoothed with 400 grit and have no burrs; and the process will only improve surface smoothness about 50 percent.
However, this can make a big difference in corrosion resistance because it deprives crevice corrosion of an easy starting spot (see “Maintaining Stainless Steel,” December 2011).
What We Tested.
We tested Citrisurf 77 Plus, Citrisurf 2310, and Spotless Stainless as commercial products, and nitric acid, citric acid, gelled citric acid, oxalic acid, CLR (lactic acid), and Barnacle Buster (phosphoric acid) as DIY alternatives.
We also tested Flitz Liquid Polish as an example of a top performing metal polish and protectant. You will find these acids in many of the commercial products on the market, such as Davis FSR Fiberglass Stain Remover (see PS, November 2008) or Ospho, which found in most hardware stores.
How We Tested
Each of the products was tested on a selection of corroded 316 and 304 stainless fasteners, deck hardware, railings, and cutlery. We varied the temperature of the citric acid treatment, from 50F to 180F. We tested for effects on brass and aluminum, in case of spills or misuse on chrome-plated parts. We then observed for six months.
Observations
Wear gloves and eye protection. Although citric acid won’t burn you immediately like stronger acids, it will slowly dissolve your skin, can harm your eyes, and will sting like a son of a gun when it finds a cut.
Don’t let it dry. Citrisurf 2310 and Spotless Stainless are gelled to keep them in place. To prevent drying you can either add more, wrap it with plastic wrap, or mist lightly with tap water. Generic citric acid solutions can be gelled using Cabosil (see DIY sidebar. No harm occurs when they dry, but they will be less effective.
400 series steel. Spotless Stainless and Citrisurf warn against use on 400 series stainless because it can cause cosmetic discoloration. We tried Spotless Stainless and Citrisurf 77 Plus on a variety of rust-stained kitchen knives. Although 95 percent of the samples came out looking like new, one blade was significantly discolored. The problem is the low 2-3 pH. Citrisurf 2250, formulated for 400 series stainless, is buffered to a pH of 3-4, solving the problem. Always test a small area first.
Heavy corrosion. A plastic scraper can help knock off heavy corrosion, but anything more aggressive will scratch the stainless and require re-polishing. Brushing with a stiff synthetic brush midway through the treatment removes loosened corrosion and improves results. Only a quick brush is needed, not heavy scrubbing.
Pitting. Don’t expect miracles with severe pitting. If prolonging the treatment doesn’t help and the part is thick enough, try sanding out the rust stains and polishing, followed by a good citric acid soak. The goal of passivation and polishing are to prevent pits; they can’t repair the damage or make them disappear once they become severe.
Cautions. Keep the acid off aluminum, carbon steel, and galvanized steel. Although not as aggressive as stronger acids, citric acid will cause some spotting if it stays too long. As with any strong cleaning chemical cover or pre-wet things you would rather not damage. Keep a hose handy.
Post treatment. Rinse liberally. The thickening agent leaves a white powdery residue you may have to wipe off.
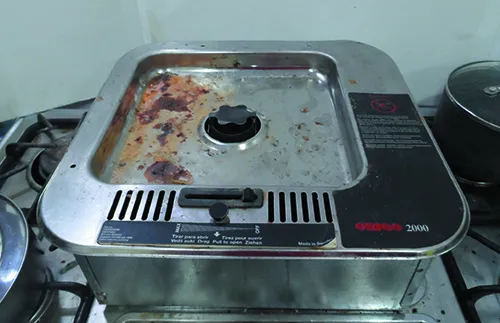
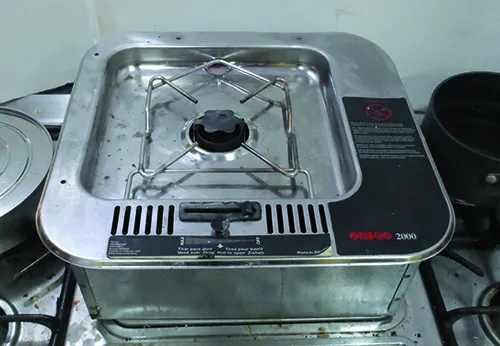
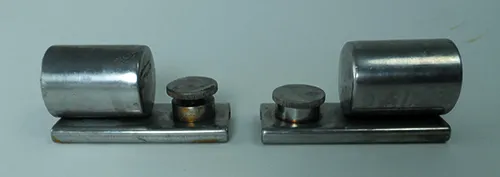
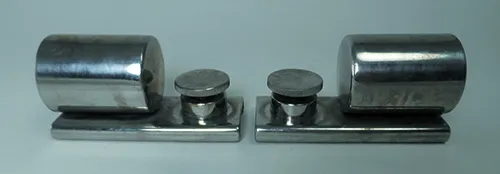
Other Acids and Safety
In addition to safety hazards, acids are also corrosive to metals, and there are obvious risks when cleaning stainless parts. It can drip or splash onto an aluminum toe rail or spar, it can cause corrosion under chrome plating (the base metal is typically brass, bronze, or Zemak, which is largely aluminum), and harm dissimilar components within a mechanism.
Testers put samples of aluminum and brass in properly diluted Barnacle Buster (phosphoric acid), nitric acid, CLR (lactic acid), and citric acid for one hour at 70F. Not surprisingly, nitric and phosphoric acid are tough on aluminum. In “Descaling Solutions for Boats” (PS August 2017) we learned that CLR (lactic acid) was the best commercial product for removing scale from aluminum without damaging the aluminum. Nitric acid was also hard on brass. Both lactic acid and citric acid were safe on brass and aluminum.
Although we did not specifically investigate this test, our observations when cleaning some brass alloys on the boat suggest citric acid products are probably also superior for cleaning corroded brass, bronze, and copper as well. More testing is needed.
Phosphoric acid actually removes rust faster than citric acid. If corrosion is very heavy, try Barnacle Buster or other rust removal agents first, but then passivate with citric acid for lasting protection. Oxalic acid was moderately effective and lactic acid was ineffective.
Strong acids are damaging to nylon. Keep all rust removers away from nylon sails and rodes. Polyester and Dyneema sheets and halyards are not affected by acid, so you can safely treat snap shackles without removing them.
Finally, don’t forget that old stainless parts that have been subjected to high sustained or shock loads, including standing rigging, mainsheet tackle parts, lifelines and steering gear, may also have work-hardened or fatigued. The former makes them more brittle and the latter may have started micro-cracks. Both can invite corrosion, and neither can be repaired by passivation.
Bottom line: Citric acid is safe for Citric acid is safe for plated parts and mechanisms that contain bronze or aluminum parts. Staining of aluminum is possible, though no damage occurred during testing.
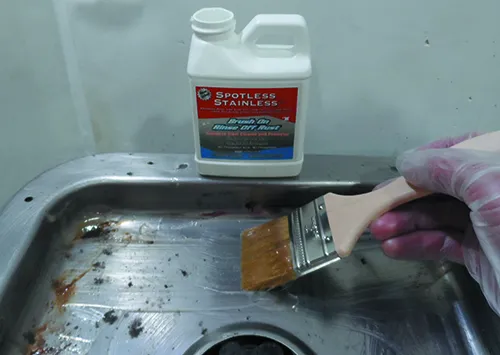
temperature. Do not increase the concentration; testing has shown it doesn’t help.
The active ingredient in passivating treatments is citric acid, and this is all you need for parts that can be disassembled and soaked. However, if you want it to remain active long enough to work properly on railings and installed fittings, you’ll need a thickener that does not react with nor is affected by acid. Here it is:
Gelled Citric Acid Passivating Solution
- 10-20 percent citric acid
- 1-2 percent by weight fumed silica
Dissolve the citric acid in warm water. Add the fumed silica (also called Cabosil M-5) and mix. A simple rule of thumb is 1/2 cup of fluffed fumed silica plus one cup of the citric acid solution. This will make 1 cup of gelled passivating mix. For a thicker solution add more silica. For a sprayable solution that will cling and not bead up, add less.
Citric acid is available in grocery stores or online. Fumed silica is available through chandleries, fiberglass supply houses, and online. We bought a 15-pound bag 10 years ago, and we’ve been working our way through it ever since, thickening epoxy and cleaners.
Spotless Stainless
About 2 to 3 times stronger than lemon juice, Spotless Stainless will sting if you get it in your eyes or on a cut, but it’s relatively safe to work with. It is gelled so that you can brush a thick coating on severely corroded areas. Because the citric acid is more concentrated, you can re-moisten it with a plain water mist as it dries and still maintain effectiveness.
Bottom line: This is our Best Choice for stain removal and lasting protection.
Citrisurf 77 Plus
Citric acid formulated with just enough gel agent to make it cling and wet out. It contains slightly less citric acid that Spotless Stainless, but we cannot document a difference in effectiveness, and industry testing suggests that more than 10 percent citric acid is unnecessary. This product is recommended and sold by Suncor, a major supplier of stainless steel boat parts.
Bottom Line: A Recommended product.
Citrisurf 2310
This is basically the same product as Citrisurf 77 Plus with more gelling agent added, making it better suited to painting and spraying on hardware that is still mounted on the boat.
Bottom line: This is another Best Choice for easy stain removal and lasting protection.
Citrisurf 2250
This product is formulated at a slightly higher pH for use on 400 series stainless. We couldn’t tell much difference, but Citrisurf 77 seemed a little faster and more effective. This is technically the better choice for stainless cutlery, for example, which may be discolored by Citrisurf 77, Spotless Stainless, or stronger citric acid solutions.
Bottom Line: In the field of citric acids, this one did not stand out. Citrisurf 2310 is a better choice for 316 stainless, but Citrisurf 2250 is a good choice for galley knives.
Stellar Solutions Rust Rescue
Rust Rescue is recommended where pitting may be present and additional corrosion protection is needed. Wipe on and let dry. We used it on a heavily pitted stove burner liner.
Bottom line: Without a control, it is hard to say how effective this will be, but the active ingredient, calcium sulfonate, is known to be effective. We’ll report back.
DIY Formula Using Citric Acid
This is the active ingredient in citric acid based stainless cleaners. Follow the concentrations recommended by ASTM and NASA—a 4-10 percent solution for soaking in hot water. Increase the concentration to 10-20 percent for spray or brush-on applications to allow for locally heavy corrosion.
However, if you spray this solution on polished stainless, it simply beads up and runs off. To keep in place, you must either add a thickening agent or wrap the corroded areas with rag strips soaked in the solution (see “Citric Acid? Why Buy Formulas that You can Make?”).
Bottom line: Our Budget Buy, and the leftovers can be used in the kitchen.
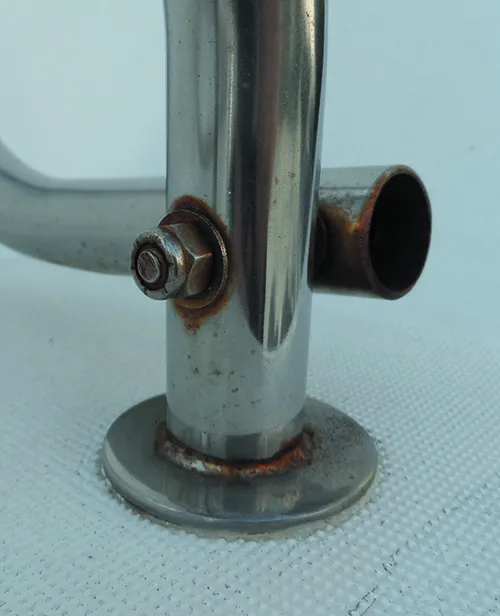
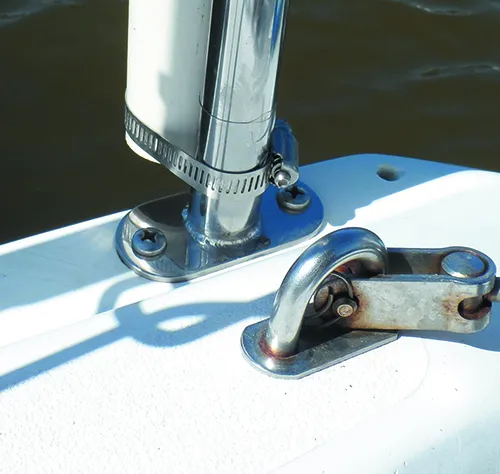
Grade 316 stainless steel contains nominally 16-18 percent chromium, 10-12 percent nickel and 2-3 percent molybdenum. Grade 304 contains nominally the same amounts of chromium and nickel, but lacks the molybdenum added to reduce pitting. Grade 18-8 is a broader grouping of alloys that contain nominally 18 percent chrome and 8 percent nickel, including 316, 304, 304L and 302 stainless, although most 18-8 steel is types 304 or 302.
Salt (sodium chloride) is the enemy of austenitic stainless steels (the type of stainless steel most commonly used in marine hardware). It is the chloride that does the damage. Salt water has about 18 times the maximum chloride levels recommended for 316 stainless. Chlorine is also harmful, but the low free chlorine levels of typical potable water systems will not affect your stainless steel tank. However, free chlorine concentrations of as little as 25 ppm can have a detrimental effect. Chloride-induced corrosion of stainless steel is complex depending on many things such as concentration, temperature, pH, etc.
Stainless rusts three times as fast in the tropics as in cold climates. Corrosion doubles for every 10F increase in temperature. The sailing season is also longer, and that means more salt exposure. Thus, an occasional sailor in the northeast may be happy with 304 fittings, while a cruiser in the tropics will not. Cold and freshwater are easy on stainless.
You may wonder, “If I’m diligent about polishing and passivating, can 304 and 18-8 replace 316 stainless?” This might work in cooler climates and in freshwater or brackish conditions, but not in salt water and definitely not for components that are sealed off and hard to inspect, such as chainplates.
Related articles: “The Great Titanium Trickle Down,” PS December 2011;
“Stainless Steel, Advantages and Ailments,” PS July 2014;
“Simple Tips for Maintaining Stainless Steel,” PS May 2014
Nitric Acid
This is nasty stuff to work with, worse than hydrochloric or sulfuric acid with a biting odor. It is also aggressive to most metals and can damage chrome-plated items. We don’t recommend it for DIY use, but we felt sure someone would ask, since it was the old standard for passivation. We tested both at the ASTM recommended 20 percent, and at 6 percent, since concentrated nitric acid is less widely available and dilution is hazardous. We found it to be no more effective than citric acid.
Bottom line: Don’t use it.
Oxalic Acid
Commonly found in marine hull and metal cleaners, this stuff is hard on the skin and toxic if absorbed. It does a reasonable job of removing surface staining, but it does little to passivate the alloy, and stains soon return.
Bottom line: There are better choices.
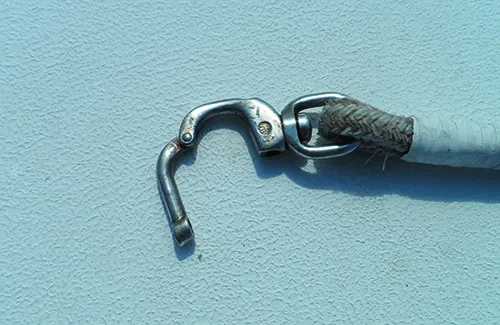
closely for micro-cracking that can invite crevice corrosion. A magnifying glass
can sometimes reveal these cracks. Using dye penetrant can also reveal trouble spots. If the age of suspect component is unknown, replacement is often the safe option (see “What’s Hiding in Your Rig,” April 2018).
Phosphoric Acid
This is another acid commonly used in marine hull and metal cleaners. Our sample product was Barnacle Buster (see “Barnacle Remover Test,” PS May 2007). It removes the rust but does not passivate as well as citric acid. It is aggressive towards aluminum and can damage chrome-plated items.
Bottom line: Save it for removing scale and barnacles.
Wichard Wichinox
We did not test this for this particular report, but we have used this on a variety of polishing jobs both on the boat and in the house. It contains phosphoric acid and surfactants, and will polish the stainless, but is not a true passivating agent.
Bottom line: Like many metal polishes on the market, this is just a rust remover, and doesn’t combat the original cause of corrosion.
Lactic Acid
Widely used in a variety of rust-stain removers, lactic acid is the active ingredient in CLR. Although we like CLR for removing scale buildup in plumbing, it is not very effective for this purpose.
Bottom line: There are better choices.
Flitz Liquid Polish
This polish is the anchor for a variety of Flitz-branded polishing products and tools aimed at auto and boat enthusiasts who seem to enjoy rubbing and buffing their pride and joy. It is representative of a universe of similar products, each of which has legions of followers (if you can believe all the online chatter). The first thing we noticed is that it was more work.
On one hand, the citric acid promise of “zero work” is only true if the stainless is otherwise clean; if there is adhesive, grease, or just plain gook, you will need to do some buffing anyway. But buffing all the nooks and crannies is tedious business.
Flitz will appeal to those who like to see progress as they work, since there is no waiting. But it also did not protect for as long; once the wax weathered away, it was just a matter of time before staining returned.
Bottom line: Too much work for big jobs. We will be testing this on gelcoat in the future.
Conclusions
We were thrilled when citric acid passivation came to the industry, replacing nitric acid and all of the accompanying nuisances. The difference in practicality for boaters is even greater. We’ve never had much interest in polishing stainless or removing stains with oxalic or phosphoric acid. They just come back. But passivation with citric acid offers real hope of protection that is more than cosmetic and produces results that last.
BARNACLE BUSTER
www.trac-online.com
FLITZ
www.flitz.com
MILLIARD BRANDS
WWW.MILLIARDBRANDS.COM
STELLAR SOLUTIONS
WWW.CITRISURF.COM
SPOTLESS STAINLESS
www.spotlessstainless.com
WICHARD
www.wichardamerica.com
I am a paid subscriber… and yet, our New Admiral at PS sends me email after email… daily for weeks.
If your goal is to make me leave; keep up the BS heavy press hard sell ON THOSE OF US WHO ***ARE*** PRACTICAL SAILOR!!!!!!!
So, safe to assume 4-10% citric acid “by weight” or volume?
Citric acid is a solid, so yes, by weight.
In standards and SDS sheets it is always percent by weight, unless otherwise specified. With water-based solutions the difference between weight and volume percent are small, because the relative density of the solution (new standard nomenclature for specific gravity) is close to 1. With solids, relative density can very widely because of differences in compaction, particle size distribution, and the properties of the solid.
When describing cleaning solutions made from common chemicals we often use volume measurements for powders, because a tablespoon seems easier than looking for a kitchen scale. The relative density of the citric acid sample we have on hand is 1.41, so one quart of a 9% citric acid solution solution will require about 4 tablespoons or 1/4 cup of citric acid powder.
Does citric acid harm gelcoat?
Pat McAtee’s question is a good one. What is the effect of a citric acid based cleaner on Gelcoat? Since most of our subject matter is attached to a boat, and most boats are fiberglass and polyester resin, is this an issue. I can think of a lot of places on my boat where there is rusty stainless bolted on to a hull part.
Citric acid (lemon juice) is completely safe for gelcoat. Because it is acidic, it can discolor aluminum, though you can use it near aluminum parts if you wet them first, do your best to keep it off them, and wipe off overspray. With precautions, we’ve used it near aluminum toe rails without trouble. We’ve slopped it all over gelcoat.
In general, acid cleaners are safe for gelcoat.
Curious; what about a natural citric acid source like a lemon? What would just rubbing a lemon over the stainless do?
Lemon juice is about 5-6% citric acid. 10-12% citric acid is recommended for passivating stainless, and some of the formulations we tested were as high as 17% citric acid. Lemon juice will work, but it will be much slower. Rubbing a lemon won’t work; the juice needs to be jelled or held in place by some other mechanism (wet rag?). Otherwise, it just runs off.
Citric acid is extracted from citrus fruit in the process of extracting flavors without the sourness. As a by-product that is low impact to separate, it is natural, non-toxic, and sustainable IMO.
Completely different question. I notice one of the test subjects is an Origo stove. I have been in search of a replacement fuel canister. Does anyone know any sources? I found this source in Europe. https://www.compass24.com/comfort/pantry-grill-oven/stoves/150526/spirit-cooker-3000-2-flame
One YouTube review says its a direct replacement. However the manufacturer says their canister is 5mm shorter than Origo. A problem that can be solved with shimming. But they do not have any canisters in stock and only ship to Europe.
Over the years, I have relied on Ospho, but it does not protect, just “cleans”. Discovered using Lime juice a couple years ago, and it works slower than ospho, but protects longer. Occasionally I have with trepedation let ospho run into lower rigging swages. On later disassembly, I observe no damage, but not comfortable with letting it into blind spots (top of chainplates etc.?). Any info on this? Are any of the acids a problem if left “wet” in contact with 316SS for prolonged periods?
No, there does not appear to be any risk with leaving passivating agents in contact with stainless for longer periods. It would be normal to store citric acid in a stainless steel tank. However, contamination with chloride (salt) is to be expected, and hydrochloric acid is bad for stainless. Like you, we have never heard of damage caused by this. We suspect that anywhere the citric acid can reach, it will also be rinsed out or diluted by the rain. It is also probable that the action of the citric acid makes the stainless more resistant.
I am still digesting all the information in this article and want to try this on my safety stanchions, especially where I added some tubing to hold jerry cans and scrub cylinders. How does polishing after performing this process affect all this?
I can try this spotless stainless, but can see us applying stainless steel polish later down the road. Is that not necessary? We like our brightwork to shine.
You do not polish with abrasives after passivization. The abrasives can re-expose iron. However, there is nothing wrong with applying a polish that is basically just wax.
I attempted to make up the DIY Passivating solution today. I believe there is some confusion in the instructions. It says 1-2% fumed silica to gel the citric acid. Then later it says you are making one cup of gelled mix but does not specify the amount of silica to the amount of citric acid. I made it up as 2% silica by weight, but it is not in any way gelled. Can you clarify?
In this context, gelled does not mean noticeably stiff, only thickened just enough so that it does not bead up and run off when sprayed onto pollished stainless. It still needs to be thin enough to spray. Please put it in a spray bottle and try it.
Thanks for this extensive article on passivating stainless steel, makes DIY so much easier and cost effective