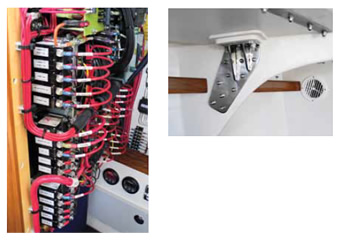
350
The Leadership 44 is built in Morris Yachts’ factory on Mt. Desert Isle, Maine, using advanced building materials and construction. Known for its precision semi-custom boat building, the company was launched in 1972 by the late Tom Morris. His son, Cuyler, is now the president and chief development officer.
Hull: The hull begins with an ISO NPG gelcoat sprayed into a female mold and a lightweight mat scrim applied to eliminate core print. Next, SP-High Modulus precut laminate and foam core are dry-stacked in order and location as determined by SP’s SmartPac B³ system, based on the designer’s files and finite element analysis. The resin is then applied using a resin-infusion technique that uses negative pressure to draw resin into the laminate. This “vacuum-bagging” process helps fill scored slots in the core with resin, increases the fiber-to-resin weight ratio and decreases void content. The art lies in making sure that resin reaches all the dry laminate on the backside of the core and the geltime allows for full wet out.
Interior and grid: Floor frames, mast-step support, and some longitudinal stiffening is developed via a molded grid that’s bonded in place with stringers running fore and aft. This combination of resin infusion, a carefully engineered laminate schedule that is matched to the loads in any given area, and an internal FRP grid deliver a strong, stiff, and relatively lightweight hull.
Deck: A similar approach to resin infusion has been incorporated in the deck, and the engineering process incudes building in high-density “in fills” in areas where higher loads are focused. Winch attachment points, track locations, chainplate regions, and other deck and cabinhouse hardware locations are also reinforced to handle the loads. The underside of the deck and cabin house becomes a finished surface with neither a liner nor covering used to hide fasteners. This cuts weight and allows the owner to more easily solve frustrating deck leaks that may occur. Acorn nuts and washers securely fasten bolts that have been cut to the right length
Hull-to-deck joint: The hull is built with an inward-turning flange that is solid FRP laminate. The core terminates just before the inward turn, and extra laminate is added to make the combined inner and outer skin a stiff, rigid flange. The deck is fastened to this flange using a combination of adhesive and mechanical fasteners. An extruded alloy toerail overlaps the outboard edge of the deck element.
Keel and rudder: A lead external ballast keel is cast with stainless-steel keel bolts aligned to fit the holes drilled in the keel stub. A garboard seam with a large surface area, a keel stub that meets American Bureau of Shipping scan’tlings, and plenty of keel bolts insure that the ballast will stay where it belongs. A “crush-zone” in the keel stub designed to absorb the impact of a high-speed grounding provides added insurance against hull damage. The carbon-fiber, semibalanced spade rudder is supported by Jefa bearings and a conventional cable steering system links the helm.
Rig: The Hall Spars, tapered carbon spar and Navtec double spreader fractional rig allow for a modern, big-main, small-jib sail plan. This eliminates the need for runners, and with a roller furling headsail, this sail combo is functional throughout a wide wind range. The spreaders are minimally swept back, and the discontinuous rod rigging ties to single well reinforced chainplates.