In “Stainless Steel Hose Clamps,” February 2016, we reviewed hose clamps by testing corrosion resistance and clamping security. Not a lot has changed; cheap ones may let you down, quality lasts, and the difference in cost is not so much. But it’s not as simple as choosing a quality brand.
A common surveyor comment is that all hoses should be double clamped. Only it’s not entirely true. While double clamps are generally a good idea, there are times when they aren’t. ABYC only requires double clamping in specific circumstances:
Exhaust Systems. “Every exhaust hose connection shall be secured with at least two clamps at each end to produce a secure, liquid- and vapor-tight joint. Clamps used for this purpose shall be entirely of stainless-steel metal. The bands shall be a minimum of -11/2 in. (12 mm) in width. [See table I for widths of clamps for a variety of applications.] Clamps depending solely on spring tension shall not be used.”
Fuel Fills. Double clamps are required. Continuity from the fill to the tank is also required. This is often provided by a wire integral with the hose, but the wire cannot be secured by clamping it between the hose and the barb. This can cause leaks. Pull out some wire and secure it to a screw. In the case of reinforcement wire, it will be stiff and this can be tricky.
Sanitation Systems. Hose spigots on sanitation systems are smooth, not barbed, because most sanitation hoses are stiff and do not play well with barbs. They should be double clamped.
—-
ABYC H-33, TABLE I – HOSE CLAMP WIDTHS
Outside Hose Diameter (inches) Clamp Width (inches)
Less than 7/16″ 1/4”
7/16″ thru 13/16″ 5/16”
13/16″ through 1.25” 3/8”
Over 1.5” 1/2”
—-
The USCG has no specific requirements for double clamping. ISO has requirements similar to ABYC.
ABYC does give specific advice for fuel hoses:
Barbs. There are no stated requirements.
Clamps. Flexible engine fuel hoses shall be equipped with permanently installed end fittings, such as swaged sleeve or a sleeved and threaded inserts, or may be secured with corrosion resistant metallic clamps. Clamps depending solely on spring tension of the metal shall not be used. Clamps shall be installed directly on the hose and shall not overlap each other. Clamps shall be installed at least 1/4-in. (6mm) from the end of the hose. Clamps shall have at least a nominal width as indicated in Table I.
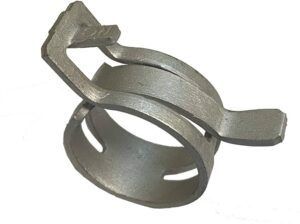
Using the correct clamp size matters. If it is too wide, there may not be room for two without overlapping or getting too close to the end of the spigot. We have seen too many hoses cut by hose clamps that extended over the end of the barb. Don’t double clamp if the correct size clamp will not fit in the available space.
Oversize clamps do not provide even clamping pressure; the screw mechanism is too large for the hose and makes a flat spot. Plastic barbs are particularly susceptible to this, becoming D-shaped over time. When the screw is moved to a slightly different location they leak like a sieve.
A barb is not required for sealing, and in fact, it doesn’t really help much. Sealing is the result of even pressure between the hose and a smooth portion of the spigot, whether barbed or plain. In fact, the primary function of a barb is to prevent the hose from creeping off. In fact, placing a band on top of a sharp barb is common cause of damage to the hose. If the barbs are overly sharp, like a knife, we recommend dulling them with sandpaper.
The spigot can never contain a thread or spiral of any sort. The leak will follow the spiral. Cut it off or fill with epoxy.
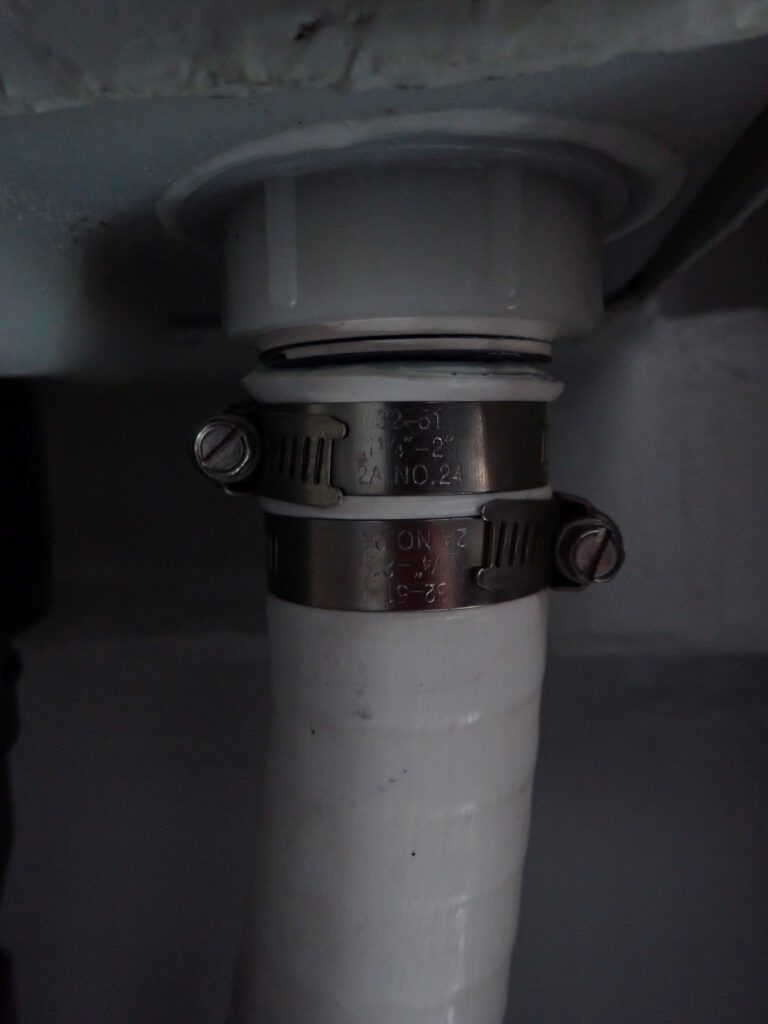
Damaged or crudely formed barbs are a common source of leaks. If not replaceable (cast as part of the assembly), carefully reform with a file to eliminate the high spots. In severe cases, where the service allows (low pressure), grinding the barb smooth may be best. In one extreme case I ground it smooth, filled the pits with epoxy paste, and then sanded smooth and double clamped. That was a decade ago. However, grinding a barb down will change the diameter of the spigot. If the hose is too tight, reducing the barb may improve the fit and reduce the need for potentially damaging heat and physical abuse. Or it may make the hose too loose. In that case, try to work with what you have, smoothing the sharp spots and filling the gouges with epoxy (filed level with the spud).
Diesel engines fuel. The inside diameter (ID) of a hose and the outside diameter (OD) of a connecting spud or fitting must meet the fitting specification in table IV, below:
—
ABYC, H-33, Table IV – MATING OF HOSE WITH SPUDS
IF MINOR OD (inches) MAXIMUM DIFFERENCE IN DIA (inches)
Less than 3/8” 0.020”
3/8” thru 1” 0.035”
Greater than 1” 0.065”
—
Hose Clamp Tightening Torque (Recommendations vary slightly between manufacturers. Not an ABYC table)
Clamp width (inches) Tightening Torque (inch-pounds)
1/4” 20
5/16” 25
3/8” 30
1/2” 35
—
Seacocks. Seacocks may be the fittings we worry the most about; they are holes in the boat. ABYC has this to say:
Seacocks are required below waterline, but not on cockpit drains or exhaust. A single clamp is acceptable except for exhaust and fuel fill. Additionally, “All piping, tubing or hose lines penetrating the hull below the maximum heeled waterline, shall be equipped with a seacock to stop the admission of water in the event of failure of pipes, tubing or hose. (Exception 2) Hull penetrations that discharge above the waterline in its static floating position and below the maximum heeled waterline and meet requirements H-27.5.3 [which says] “Hull penetrations that are not equipped with a seacock shall use reinforced piping or hose that resists kinking or collapse. [Seacocks] “will withstand 500 pounds for 30 seconds at point of greatest leverage. [Only] matching threads [will be used]. Straight to straight, tapered to tapered.”
Tightening. It is difficult to apply more than 10-20 inch-pounds with a screwdriver if the location is awkward. A cordless drill with the clutch set low is fine for running them up, but most can deliver 200-350 inch-pounds at high settings, massively over tightening the clamp and damaging the hose. A ¼-in. drive ratchet is commonly recommended. Applying moderate finger pressure (6-8 pounds) to the end of a 3- to 4-in. lever will reliably provide the required 18-32 inch-pounds or torque, and a socket holds well in awkward positions.
We do not recommend any of the clamping methods that rely on wire, whether using a proprietary tool or various kludge methods. The clamping pressure is not sufficient, not predicable, and if it were sufficient, it would cut the hose. Carry a range of sizes of spare clamps on the boat; they’ll take less space than the proprietary tool.
When double clamping, place the screws on opposing sides of the barb for more even clamping pressure, but with the screws facing the same direction for ease of access.
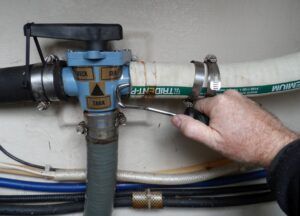
Heat, Picks, and Lubricant. Getting the old hose off can be most of the battle. Heat can help. If you cut, be careful not to damage the barb. A hose pick helps in tight spots. To reinstall, be careful not to overuse heat; you can damage the hose. A lubricant helps, but grease can damage some hose materials. You can’t go wrong with KY, which was developed as a surgical lubricant, and will dry up and go away in time, so as not to loosen the hose.
Summary. Perhaps the best reason to double clamp is not because it is required, but because some of these are critical and are in places we won’t remember to inspect. Double clamp the few places they are required, and feel free to double up other places, as long as there is good room for two clamps of the correct size.
It is always about proper installation. Prepare the barb, removing any irregularities. Choose a good clamp, of the right width and diameter. Position it correctly on the spigot and tighten to spec. Done.
Further reading: Dec 2014. https://www.practical-sailor.com/systems-propulsion/diesel-engines/stainless-steel-hose-clamps