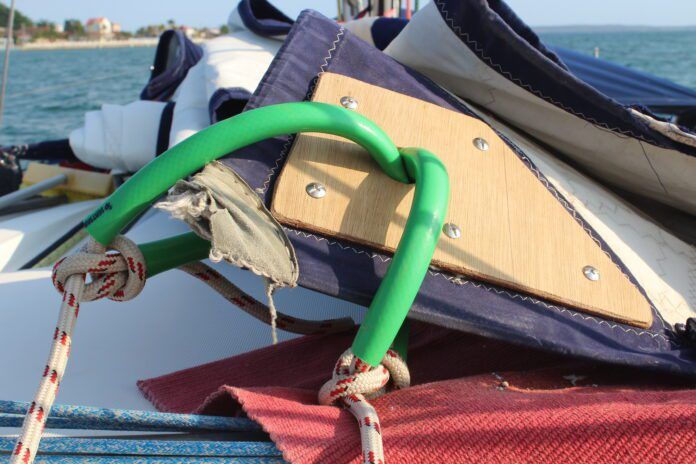
How do you manage major sail repairs in remote locations? By using whatever you have onboard to get you home—or beyond.
After an easy three-day sail from Guanaja in Honduras, we checked into Cayo Largo on the south coast of Cuba. From time to time, we’d look at the clew of our genoa and think “we must get that fixed one day.” The tape holding the ring at the clew was frayed but we thought it would last until we reached Florida. We were having a perfect sail going east from Cayo Largo when that ring holding the sheets blew out. We managed to furl the flapping genoa and hoisted our hanked on staysail, which was already rigged and ready on the deck. We were heading to Cienfuegos where, we had heard, there were competent sail makers who would be able to repair the sail.

In theory. When we checked in—it is compulsory to check in and out of each port in Cuba—we were told that there were plenty of experienced sail makers in town. Good. The only problem was that they had no materials. Bad. Now we had to work out how to fix the clew ourselves.
We carry a few sheets of marine plywood on board. The main reason is for emergency repairs if we are holed by a container or other submerged object. I realized that I might be able to do a temporary workaround for the clew headboard using some of these boards. So, while we were at anchor off Cienfuegos, I measured and sawed two triangles for a precise match of the angles where the leach and foot joined at the clew. I then drilled five holes so I could bolt the plywood to the sail. But first I glued the plywood on either side of the sail with 3M’s 5200. Perhaps it was not the correct adhesive to use, but it was the best option we had onboard. I drilled through the sail in the same five locations and bolted the plywood to the sail.
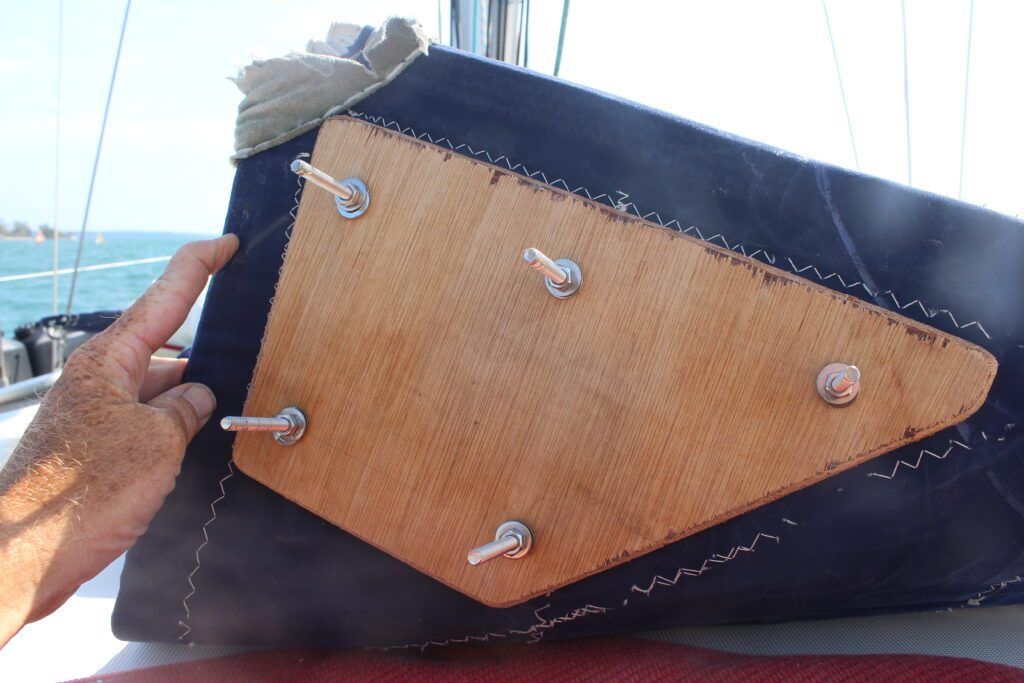
I made sure the heads of the bolts were on the inside of the furl, then cut and filed the bolts to minimise the chance of the sail fabric fouling on the bolts. This held the sail and plywood in place while the 5200 cured over the next 48 hours. I also used a hole saw to drill a 40mm hole through the boards and sail. I threaded the genoa sheets through two short pieces of reinforced tubing to prevent chafe. Then we kept our fingers crossed that the modified clew would last for another couple of months before we could get to Florida for a professional repair.
We stayed at anchor off Cienfuegos for seven days while we explored a little of the inland areas of southern Cuba. By the time we sailed again the plywood headboard was solidly in place, and the anti-chafing tubes seemed to be doing a good job. Apart from a few doubts about the integrity of the repair, the only disadvantage was the awkwardness of the non-furling boards. The clew stuck out from the forestay like a sore thumb (photo 4). But the whole process seemed to be a success.
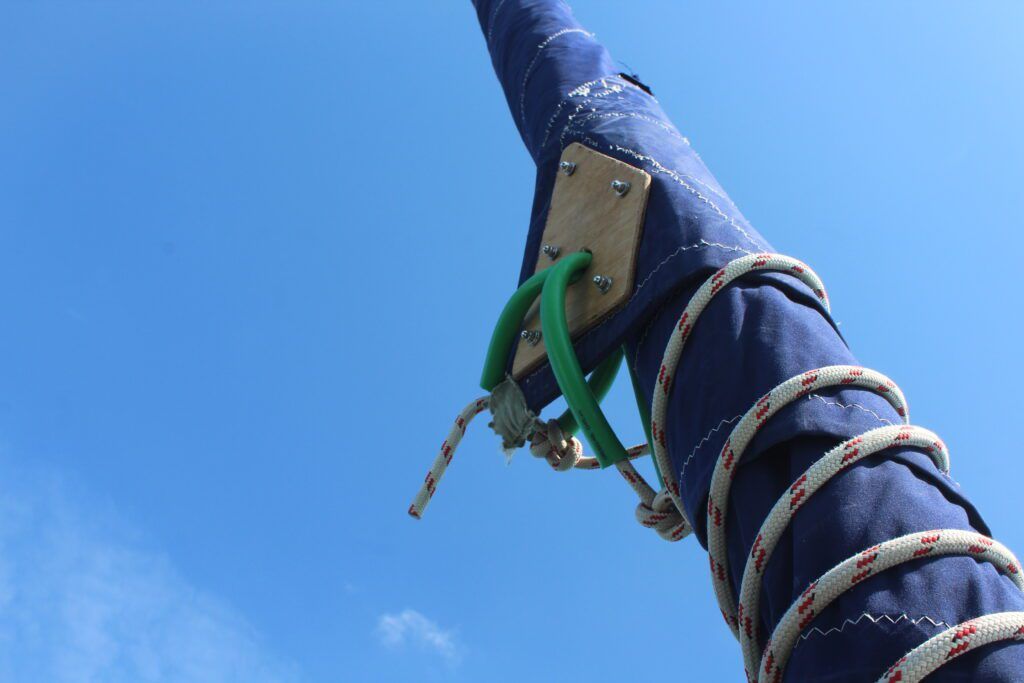
After two months of great sailing in Cuba we headed to Florida. The clew was holding up well, so we continued on to Bermuda, then Nova Scotia, until finally stopping for the winter in Deltaville, on the Chesapeake Bay in Virginia. After nearly 4,000 miles we figured it was time to get that clew professionally repaired. The sailmaker in Deltaville asked if we really wanted the boards replaced as he thought they’d continue for quite a while longer. But sails should be sails, so we now have a new clew which actually looks like a clew. And hopefully it will last for thousands of more miles.
Have you rigged something up just to get you home using only the spare parts you had onboard? We’d love to hear your story! Email us at [email protected]
Well done!