In “Stopping Wood Rot,” December 2023, Practical Sailor busted the myth that you can reliably seal wood with epoxy. Some sailors have suggested that penetrating epoxy is different because it soaks into the wood.
True, penetrating epoxies can soak into cracks, rotten wood, and very open-grained wood better than conventional epoxies. This is because they are made with low molecular weight resins to reduce the viscosity, measured in centipoise (cps). A lower cps means less viscosity. Conventional epoxy has 850 cps, penetrating epoxy has 100 cps, varnish has 80 cps, and water has 1 cps.
Penetrating epoxies also have a very slow cure rate (days instead of hours). Unlike conventional epoxies, penetrating epoxies soak into the surface of raw wood. Unfortunately, penetrating epoxies are weak—about five times weaker than conventional epoxy—and about the same tensile strength as varnish. The formulas can’t be hot coated (recoated before full cure) with conventional epoxies even within the same brand. You must wait for the full cure time of 3-5 days, and then scrub off the amine blush, a waxy biproduct of epoxy as it cures.
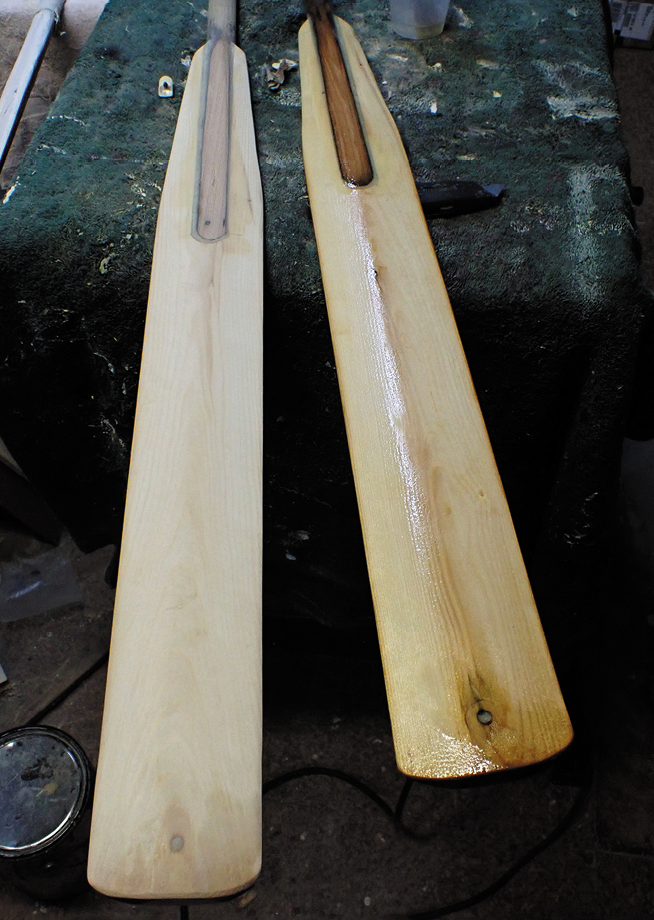
Epoxy of any viscosity can’t penetrate damp wood. In fact, nothing will penetrate wet wood; the pores are already full. Except for underwater epoxies, exposure to water will make epoxy weaker.
Epoxy can’t kill rot. No matter how deeply the epoxy penetrates, there will always be an area of infected wood between the epoxy and the good wood. This is where the rot begins again. If you want to stop rot you must keep the wood very dry (less than 20 percent moisture) or treat with an antimicrobial like Borax (see “Wood Rot Prevention Eight Years Later,” PS December 2023). Penetrating epoxy applied to end grain can help with that. But so can conventional epoxies and varnish.
So what good are penetrating epoxies? We set out to answer that question.

WHAT WE TESTED
Our test group included penetrating epoxies from Total Boat, West System, System Three, Abatron, and Boat Life (Git-Rot). We diluted samples with acetone to compare penetration depth and strength with undiluted products. For comparison, we tested Total Boat Slow Epoxy, West Systems Fast Epoxy, Total Boat Wood Sealer, Total Boat Gleam 2.0 varnish, and Minwax Helmsman spar varnish.
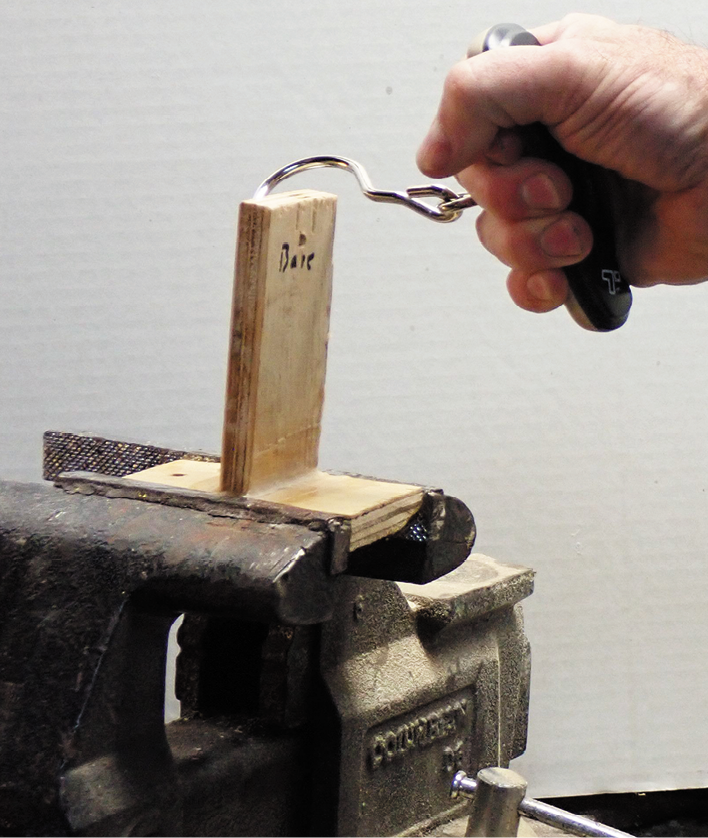
HOW WE TESTED
We coated samples of exterior plywood with the epoxies and varnishes and left them to weather in the shade for a year. Because epoxy will quickly degrade from UV, we also coated samples with four coats of Gleam 2.0 and left them in the sun. We evaluated adhesion by breaking a 90-degree bond between two wood samples. We cast solid round pucks of each product to test material strength and hardness. To check penetration, we added a dye to each product and then coated the ends of a pine plank, balsa core, exterior plywood, and rotted deadwood from a small tree.
All samples were allowed to cure for five days and scrubbed to remove amine blush before bonding or overcoating with varnish. We waited two weeks before strength testing. Samples were sliced endwise with a table saw and explored with an ice pick to gauge the hardening effect and extent of epoxy penetration.

OBSERVATIONS
During winter or in humid regions, fully drying wood for treatment will take weeks or months. If the wet wood is a core material, just drilling a few holes in the outer laminate isn’t enough. The damaged area will need to be opened. Once you have opened and exposed the wood, you might as well replace it with good core. [Editor’s note: We are currently testing claims that vacuum pressure and limited heat can dry core.]
GENERAL GUIDANCE
Do not apply stain before your penetrating epoxy. It can block penetration. Similarly, epoxy has an amine blush that can spoil adhesion. You must remove the blush with water using a scrubbing pad before bonding or painting over epoxy.

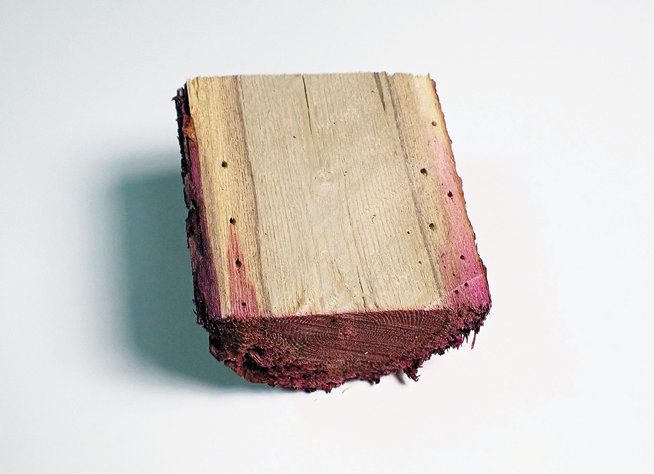

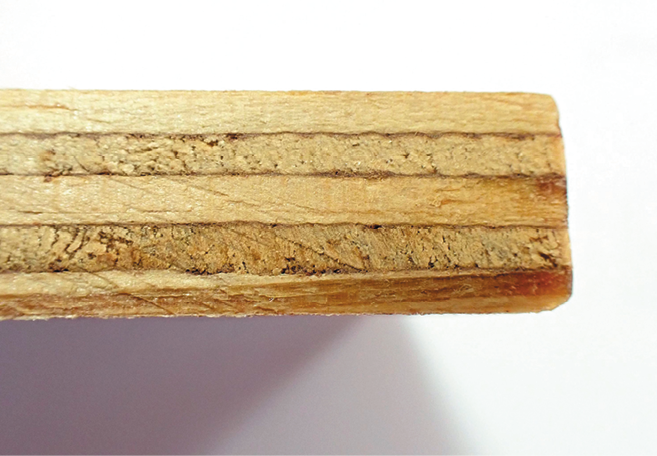
PENETRATION
We liberally applied both penetrating epoxies and wood sealer to the coupons, allowing a few minutes for it to soak in and then applying more. In all cases, they absorbed fully before curing, leaving a mat finish. Abatron Liquid Wood was the exception, leaving some glossy patches. Penetrating epoxies can take a day or more to cure, but after 20 minutes they begin to gel and no longer penetrate the wood. Slow and very slow cure epoxies are in the middle, soaking in effectively for 10-20 minutes and curing in 1–2 days. An advantage of slow cure epoxies is that they can be hot coated within the green cure window without removing the amine blush.
Penetration across the grain in plywood is less than 1/16-inch. Solvents in the epoxy may go a bit farther, but when samples were sliced open, testers found no evidence of cured epoxy beyond 1/16-inch. Even the thinnest products did not penetrate deeply beyond the surface. No product will cross a glue line in plywood laminate. Sap and gum lines also stop penetration.
Penetration along the grain in plywood was extremely variable. We dipped the ends of ½-inch exterior plywood samples and ¾-inch pine boards in three solutions—penetrating epoxy, wood sealer, and penetrating epoxy diluted with 20 to 50 percent acetone. Each sample was dipped ¼-inch deep into a pool of dyed solution and withdrawn after 30 seconds.
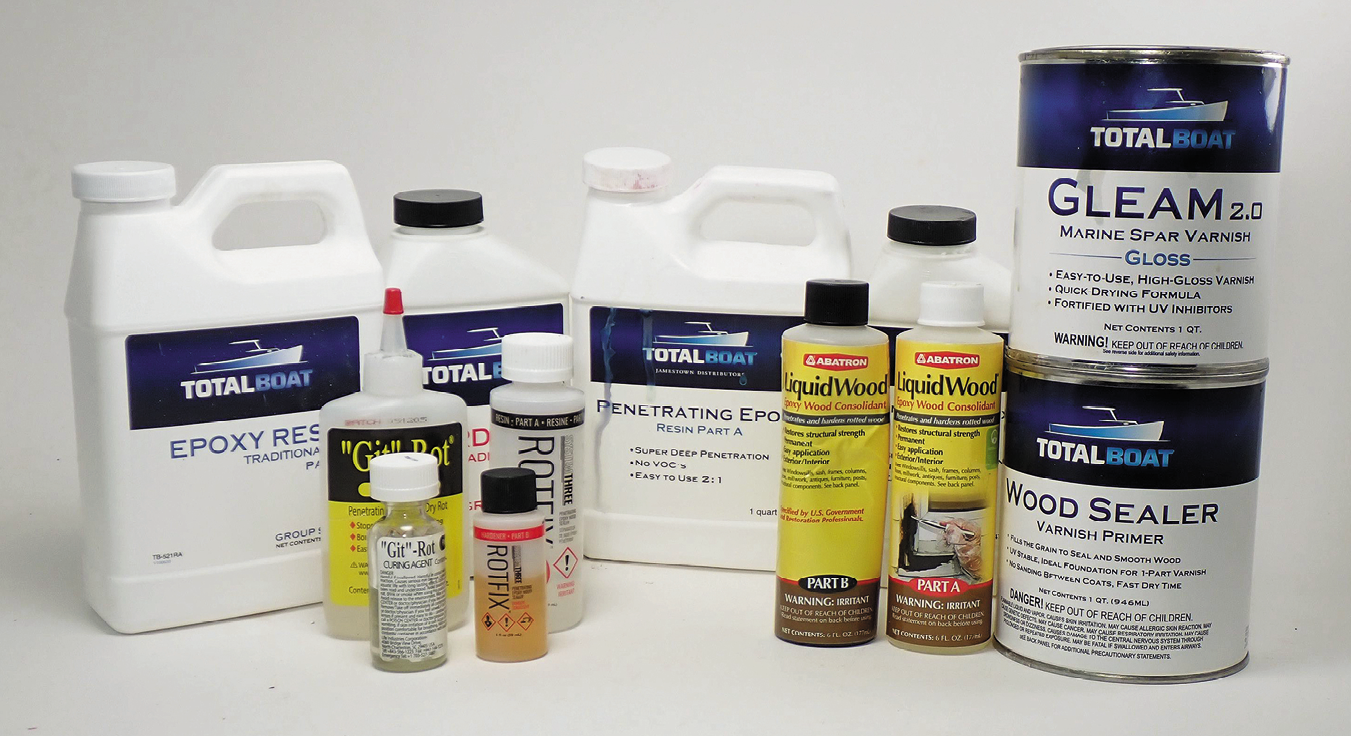
The penetrating epoxy sometimes crept as far as ¼-inch into good wood, sometimes a little farther into plywood because of tiny cracks in the veneers. Penetration into rotten wood is much greater, up to an inch or more, but this is highly variable, and by the time it exceeds 1-inch, surely the wood is soft and mushy.
Testers saw deeper penetration into end-grain balsa. Acetone can wick several inches up a stick of balsa in a matter of seconds. Penetrating epoxy, however, only penetrates a few hundredths of an inch. Balsa’s cell structure filters out the polymer required for bonding, and thinning epoxy with acetone doesn’t change that. Epoxy thinned with acetone will appear to wick up a balsa stick in a demonstration, but that is only the solvent portion.
We soaked sections of fiberglass laminated balsa core samples in penetrating epoxy diluted with acetone and dyed red. It did not penetrate across the grain at all. We also soaked sections that had delaminated due to stress. In these samples, the end grain was not penetrated at all. This is because the end grain is sealed with the bonding epoxy used during the original lamination. The conclusion is that penetrating epoxy will only soak into balsa if the balsa is both dry and very severely rotted, and then only through fractures and voids. Yes, water can soak into balsa core, but this takes years.
DILUTION
Although fast cure epoxy penetrated 30–60 percent farther when diluted with 50 percent acetone (that absolute maximum recommended), the actual zone of hardened wood, as determined by careful probing with an ice pick, did not extend more than 20 percent farther than epoxy without acetone and only a little farther than undiluted slow cure epoxy.
Dilution with solvent extends the time for curing, even with slow epoxy. We left ¼-inch thick pucks in the mixing cups so that we could evaluate them for hardness, flexibility, and strength. Instead of curing in the usual 1–2 days, the acetone/penetrating epoxy blend took weeks to transform into a weak, rubbery material. Even after three months, the acetone-diluted pucks remained weak and rubbery. Diluting epoxy with 10–50 percent acetone reduced strength by 70–98 percent.
By monitoring loss in weight, we determined that the full drying process of a ¼-inch thick layer at 70F is about four weeks. Of course, the drying period of infused wood will be far less, but the loss in strength will be the same. Acetone may aid a little in penetration by delaying gelling by about 20–30 minutes, but it does not add strength.
MATERIAL STRENGTH
We tested strength by breaking the thin pucks and calculating an approximate tensile strength. The calculated strength of the West Systems 105/205 puck was within 1 percent of the manufacturer’s reported value. The calculated strength values of the penetrating epoxy pucks were slightly greater than manufacturer reported values, an artifact of their greater flexibility and the use of a different test method.
Testers made two key findings regarding material strength: penetrating epoxies are 70–80 percent weaker than conventional epoxies, the tensile strength of any epoxy diluted with acetone drops to less than that of varnish and even sealants. We found that dilution with 50 percent acetone weakens epoxy by 95–98 percent. The blend cures to a weak, rubbery state.
BOND STRENGTH
We theorized that the lower tensile strength of penetrating epoxies might compromise bond strength if the wood was coated first. We applied one coat of each product to our wood samples and then bonded them at 90 degrees using West Systems 105/205 epoxy thickened with colloidal silica. We did not test wood sealer or varnish.
In every case, the epoxy held, and either the wood itself or the plywood glue failed at 35–42 pounds. The typical across-grain wood strength is 700–1,000 psi, much less than that of conventional epoxies, so we expected the wood to fail first. But it appears that the penetrating epoxy did increase the strength of the wood surface. Fully sealing the bonding surface before gluing, therefore, seems like a potential use for penetrating epoxy—so long as the sealed surface is later prepped as directed for best adhesion (washing away amine blush, and if recommended, scuffing the surface).
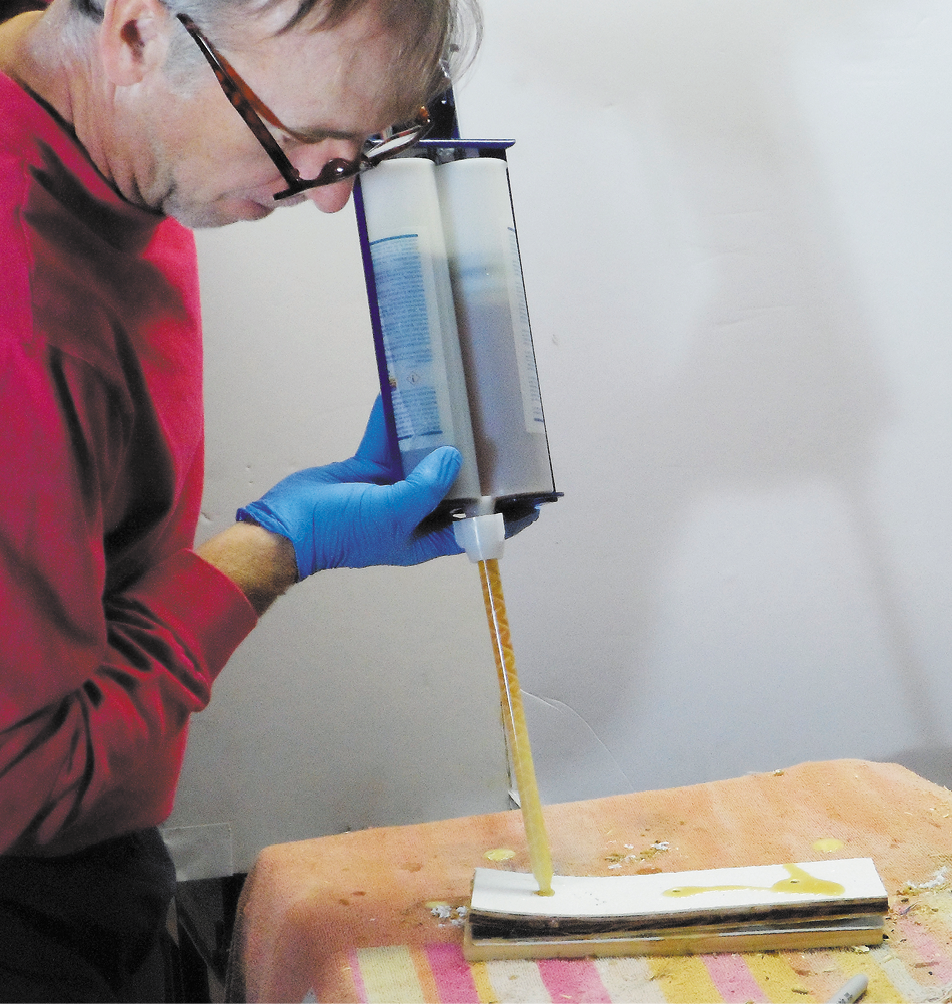
INJECTION
When injecting into rotten wood, drill at an angle to make a larger reservoir with more surface area. The epoxy cures very slowly, so be prepared to continue refilling the holes for 30 minutes, until the epoxy begins to gel.
An advantage of slow cure and penetrating epoxies is there is no exotherm (they don’t get excessively hot and begin to bubble during curing). Filling deck holes with fast epoxy invariably results in overheating and bubbling, weakening the result. Slow and penetrating epoxies can be injected into large voids without danger of overheating. However, we do not recommend penetrating epoxy for filling drilled holes. It is so thin that it drains away, leaving voids unfilled. Slow cure epoxy is a better choice.
Epoxy can’t penetrate far simply by absorption, but it can be forced through cracks and into voids. If the voids are full of water, there is no room for the epoxy. In fact, if the voids are full of air, the epoxy cannot go far. You must drill vent holes nearby to prevent cracking. If you are drilling multiple injection points, fill them in a pattern that will force the air towards a vent.
Don’t expect epoxy to penetrate balsa core unless the balsa is both badly rotted and very dry. Injected epoxy can only fill the voids. When you hear of a deck repaired by drilling many holes and injecting epoxy, this functions by creating epoxy pillars between the laminates, or by rebonding core that was probably resin-starved when initially laminated. It does not fix the core damage (see “Can Glue Injection Fix a Rotten Core,” PS July 2020).

PLYWOOD
It is commonly believed that water wicks rapidly along the grain, but in fact, we found that penetrating epoxy only wicks up cracks formed when the veneers were peeled from logs, not up the grain per se. Thus, the absorption was very uneven. The penetrating epoxy would often penetrate ½-inch up some fissures, but not into the actual wood. This could stiffen the wood by filling void space, but in no way does it enter the cell structure of sound wood. In other words, the wood needs to be quite rotten before there is deep penetration.
EPOXY PRODUCTS
West Systems, a leading brand in DIY epoxy repair products, does not believe in penetrating epoxy, and they explain why on their website. If they thought penetrating epoxies made sense, they would sell them. Their tests, however, used penetrating epoxies for bonding as well as for sealing. Our tests used penetrating epoxy only for sealing, and then bonded using full-strength epoxy, which gave us good results.
You can thin conventional epoxy with acetone, but the resulting formulation is weaker than penetrating epoxy. We do not recommend thinning epoxy with solvents. This formula is stronger than penetrating epoxy, and in principle, the surface film is better for bonding. On the other hand, the high- molecular-weight resin does not penetrate well, even when thinned.
Adding more solvent and expecting deeper penetration is just wishful thinking. The same seems to be true of varnish diluted with excessive solvent. The varnish stays near the surface and only the solvent penetrates.
Since long term protection is a key component of this test, we did not pick an absolute winner in this round. Products that penetrated one or more of our wood samples and met our criteria for ease of application earned a “Recommended” rating. We will follow up with results of long-term exposure results in about a year.
ARBATRON LIQUID WOOD
Well-regarded in the carpentry community, this epoxy product is just a little bit thicker, slightly stronger, and faster curing than the other products in our test.
Bottom line: Recommended.
BOAT LIFE GIT ROT
Perhaps the best-known penetrating epoxy, the name makes it sound different from other penetrating epoxies, but it isn’t. The squirt bottle packaging is novel, but more likely you are going to mix up only a portion at a time.
Bottom line: Recommended. Git Rot was more expensive than other products that performed better.
SYSTEM 3 ROT FIX
This was the thickest of the group, and it did not soak in as well.
Bottom line: Recommended.
TOTAL BOAT PENETRATING EPOXY
This was the thinnest of the group and the easiest to apply, Total Boat’s product was as easy to work with as varnish.
Bottom line: Recommended for sealing and the Budget Buy.
TOTAL BOAT SLOW EPOXY
Based on the limited bonding and breaking we did with this product, it seems equivalent to other slow-cure epoxy products. Slow cure means it has some time to soak in and will not exotherm.
Bottom line: Recommended for sealing, bonding, filling holes, and injection.
WEST SYSTEM SLOW EPOXY
Long experience confirms this is a reliable product. Slow cure means it has some time to soak in and will not exotherm. It is suitable for filling holes and injection.
Bottom line: Recommended for sealing and bonding.
WEST SYSTEM FAST EPOXY
This is another reliable product. Because of the short pot life, don’t mix more than you can use in 10 minutes, and even less in warm weather. Not for filling holes or thick applications because of exotherm, and not for sealing because it cures to fast to penetrate.
Bottom line: Recommended for bonding.
WOOD FINISHES AND SEALERS
If you simply want to seal exposed wood to prevent further deterioration, varnish can do the job just as well as thinned epoxy. Thin the first coat 20 percent (or use a varnish sealer) then add another coat or two at full strength. The performance of our three wood-coating products matched that of thinned epoxy when it came to sealing. (For a more extensive comparison of varnishes and wood finishes see “Exterior Wood Finish Update at 2 Years,” PS July 2021.)
TOTAL BOAT GLEAM 2.0
Epoxies are vulnerable to UV exposure, so we overcoated all the long-term exposure samples with varnish. Gleam 2.0 Spar Varnish is slightly thinner than other varnishes we’ve tested, but applies easily, levels well, and won’t run if applied thinly. It is fast drying, but not so fast that it’s hard to keep a wet edge. You will need an extra coat or two, but it applies easily and can be recoated without sanding for up to 48 hours after the prior application, so this isn’t such a big deal. Varnishes are more flexible than conventional epoxies and thus less prone to cracking as the wood expands and contracts.
Bottom line: Recommended.
TOTAL BOAT WOOD SEALER
Used as a primer under Gleam 2.0, Total Boat Wood Sealer penetrated good hardwood (oak) less than one hundredth of an inch. Like varnish, a thin coat would soak in, but a thicker coat left some resin on the surface. Penetration into softwoods and plywood was deeper, leaving a mat surface. Like varnish, it will not fully cure without oxygen, so it is not suitable for pumping too deeply into soft, punky wood.
Bottom line: This product is very fast drying. Recommended.
MINWAX HELMSMAN
Helmsman Spar Varnish has been a middle of the road finisher in previous PS varnish testing. The familiar polyurethane Spar varnish served our needs, and the price is right.
Bottom line: Recommended.
CONCLUSION
Based on our initial testing, penetrating epoxies do not significantly penetrate or reinforce wood in the way promotional material suggests, but they are good for sealing wood and appear to strengthen epoxy glue bonds. Durability testing may tip the scales toward one approach, but at this point we favor either slow cure epoxy or varnish for most sealing applications.
Coating wood with penetrating epoxy seems to increase bond strength with plywood, so you can safely coat wood before gluing it. Wait 3–5 days for a full cure and remove the amine blush before coating. Along the grain and in slightly deteriorated wood, such as the wood core around a portlight, penetrating epoxy might have an edge.
Don’t use penetrating epoxies for laminating or bonding. They are weak and are not intended for that.
We don’t see any upside in diluting epoxy with solvents. The epoxy does not penetrate farther, and the dilution greatly weakens the epoxy.
A penetrating varnish can serve as a sealer. For wood finishing inside the cabin, use 1–2 coats of wood sealer, followed by 3–6 coats of varnish.
For exterior wood, we don’t recommend any epoxy product, even as a sealer. We’ve had too many experiences with epoxy becoming discolored and peeling underneath the varnish.
The most tempting use for a penetrating epoxy is for wood that is so weak and soft that should be replaced. For common boatyard jobs that might call for deeper penetration—stripped screw holes, bad bolt holes, sealing wood before bonding, etc.,—a slow epoxy is preferable to a penetrating epoxy. This will be much stronger, we can bond other epoxies to it without waiting a week for it to fully cure, and we don’t need to scrub off the amine blush if we want to add another coat of sealer or a layer of fiberglass.
Penetrating epoxies seem to strengthen the surface of the wood, very slightly increasing bond strength as a result. There is no harm in coating raw wood with penetrating epoxy prior to bonding with conventional epoxies. For example, it makes sense to pre-seal areas of a stitch-and-glue kayak project that might be very difficult to seal later. The only downside is the need to scrub off the amine blush before bonding, varnishing, or painting. Do not use penetrating epoxies for final coats.
Our views on epoxy injection for a core repair are mixed. Our usual preference is to replace any bad core (see “Step by Step Core Repair,” PS August 2020). Drill out a few core samples to access the condition of the core. If it’s dark, wet, and mushy, tear it out. Nothing is going to bond or cure correctly. If the balsa is solid but wet, perhaps you can dry it to a reasonable state. Polyurethane injection, such as Gorilla Glue, can work (see “Can Glue Injection Fix a Rotten Core,” July 2020).
If the deck is delaminated, but the core is intact, drying the void and injecting epoxy can provide a durable repair. This also works for small voids that sometimes follow a core replacement or other repair. However, penetrating epoxy is not always recommended, because it may drain away, leaving voids. Slow cure epoxy may be the better choice.
Penetrating epoxy will inject deeper but it’s weak, so we recommend slow-cure epoxy for any injection project. Fast cure epoxies will gel sooner and can heat up faster. Slow or very slow cure epoxy will give you more time to inject where you need to, and top off the holes as the epoxy moves in.
Penetrating epoxies are no panacea for bad wood and offer no advantage over slow-cure epoxy for most applications. When properly applied and prepped for recoating, they can be used as a primer/sealer for a compatible topcoat. They can improve bonding of plywood. How they fare over the long haul is uncertain.
VALUE GUIDE: PENETRATING EPOXY
BRAND | PRODUCT | VISCOSITY(CP) | POT LIFE (150 ML @ 75F) | FULL CURE @ 75 F* | STRENGTH (PSI)* | PUCK STRENGTH (PSI) | COST |
---|---|---|---|---|---|---|---|
Total Boat | Penetrating Epoxy ✔ $$ | 80 | 45–50 minutes | 96 hours | NA | 2300 | $58/48 oz. |
Total Boat | Penetrating Epoxy + 50% acetone | 20 | 45–50 minutes | NA | NA | 60 (bent) | $58/48 oz. |
Total Boat | Slow Epoxy ✔ | 1000 | 12 minutes | 48 hours | 8000 | Not tested | $65/32 oz. |
Total Boat | Slow Epoxy + 50% acetone | 30 | 20 minutes | NA | NA | 250 (bent) | $65/32 oz. |
West Systems | 105/205 (fast) ✔ | 975 | 9–12 minutes | 12-24 hours | 7900 | 8000 | $81/39 oz. |
West Systems | 105/206 (slow) ✔ | 725 | 20–25 minutes | 36–72 hours | 7300 | Not tested | $81/39 oz. |
West Systems | 105/209 (extra slow) ✔ | 725 | 40–50 minutes | 72–96 hours | 7300 | Not tested | $101/42 oz. |
System 3 | Rot fix ✔ | 180 | 20 minutes | 96 hours | NA | 2100 | $27/3 oz. |
System 3 | Rot fix + 30% acetone | 30 | 20 minutes | NA | NA | Not tested | $27/3 oz. |
Boat Life | Git Rot ✔ | 100 | 20 minutes | 72 hours | NA | Not tested | $126/32 oz. |
Abatron | LiquidWood ✔ | 100 | 30 minutes | 72 hours | 1400 | 1800 (bent) | $56/32 oz. |
Total Boat | Gleam Spar Varnish ✔ | 65 | NA | Weeks | 1000 | Not tested | $46/32 oz. |
Total Boat | Wood Sealer ✔ | 30 | NA | Weeks | NA | Not tested | $36/32 oz. |
Minwax | Helmsman Spar Urethane $$ | 80 | NA | Weeks | NA | Not tested | $36/32 oz. |
✔ Recommended | |||||||
$$ Budget Buy |
CONTACTS
ARBATRON, www.arbatron
TOTAL BOAT, totalboat.com
WEST SYSTEM, westsystem.com
SYSTEM THREE, systemthree.com
MINWAX, minwax.com
BOAT LIFE, boatlife.com