Boats are made to live on water, but that does not mean they are impervious to the stuff. Some systems, like the electrical system and the marine electronics, just do not mix with water. Other things below the deck can be quickly damaged by water.
Water comes in basically two forms: flooding and seepage/condensation. The first one presents critical or catastrophic damage and is usually obvious. It is the second one that often causes insidious damage over time
Seepage. The most likely places to get seepage are ports/windows, stanchion posts and genoa tracks. Generally, it starts because the fitting has been strained, it was badly fitted in the first place, or the passage of time has led to the caulk failure. Although ports/windows are generally not subject to high stresses due to their size, they are a common source of seepage. Often the seepage is not readily apparent, and you may just think it is a bit of condensation, but it can be seeping into the core of the coach top.
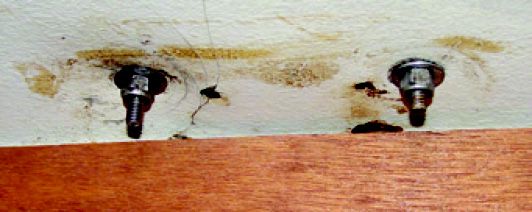
Deck fittings, when done properly, have substantial backing pads and solid blocking within the deck. However, with time, a fitting may have been moved, upgraded or added. Generally, you can see whether an adequate backing pad was used, but not whether there is sufficient internal reinforcement. Cored decks are the ones to watch most closely, especially balsa core. Balsa, or any material that can rot, will do so if water seeps in. That rot will spread across a large area without any visible damage. By the time you realize that the deck is feeling spongy it may already be too late. It is certainly going to be a major repair job. In a properly designed boat, the deck will be built with solid material, with no core anywhere deck fittings are meant to go. The reason: if you bolt something through most cored decks and then load it, the deck will compress and move enough for the caulking to fail over a fairly short time, even with substantial backing pads. This applies even with foam cores.
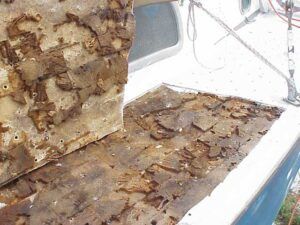
Plywood decks might be less likely to have problems, but plywood should be thought of as core material. If water gets into plywood it will wick across the laminates in the same way it would with any other core unless substantial backing plates are used to spread the load.
So the question is, have you or a previous owner moved any deck fittings without first glassing in a solid core replacement block and adequate backing pad? In my experience seepage through deck fittings causes more insidious damage to boats than anything else.
DESIGN BRIEF
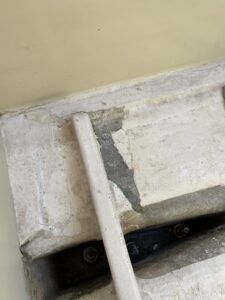
The other reason for seepage to become a problem is when a boat is used outside the designer’s parameters. Often, people will buy a boat that was designed for charter work in the Caribbean or similar area. They then want to use the boat for more serious offshore passages and find they need to upgrade winches and other deck fittings. No problem, just remove the old winch, fill any holes, drill new ones and bolt it on. All well and good: But if the designer planned the deck to take the load from a No. 30 winch and you fit a No. 40, you have now increased the load you can apply by 30%. Will the internal deck reinforcement take the extra load?
The other area where cores can cause problems is bulkheads. You may say ‘My bulkheads don’t have a core, they are solid plywood.’ In terms of damage from seepage, any laminated material should be treated as if it was cored, even below deck veneers. While decent marine plywood is pretty impervious, if water gets into the ends, it will seep along the individual veneers. You will get rot from the inside that won’t be noticeable until a major part of the bulkhead fails. Tabbing and sealing around bulkheads needs to be carefully checked each winter layup and any seepage near the bulkheads needs to be dealt with urgently.
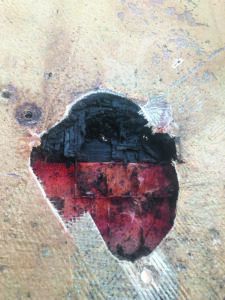
Condensation. This can be a real issue on some boats. Metal hulls and solid fiberglass hulls are effectively uninsulated. Seawater is generally colder than the air temp inside the boat so the result is condensation on the hull and possibly the deck head, which is the under surface of the deck above, and what many of you call “the overhead.” In many cases this is just annoying and unpleasant, the drip always lands on your bunk! The issue is the same as with seepage. If your boat suffers from condensation, it can creep into structures like bulkheads and sensitive systems like electronics. Unless you are going to insulate the inside of the hull, which is difficult and expensive, you cannot stop condensation from forming. Even if the boat is fully insulated there can still be a hidden issue with condensation forming between the hull and the insulation unless it the insulation is fully bonded to the hull. The only remedy is to continuously get rid of it. Gentle heat and ventilation can be effective on most boats, but some people seem to get good results with dehumidifiers. Whichever one you go for include a hygrometer, an instrument for measuring humidity. A freestanding model on the chart table is fine.
To minimize problems during winter storage you really want to try to keep the inside of the boat no more than about 5 degrees C (41 degrees F) above outside temp with a humidity of under 50%. If the boat is too warm it will encourage condensation because the difference between the inside air temp and the hull is high. Don’t overdo it, you need to dry up the condensation, not kiln dry the boat! If a boat normally has around 60% humidity when in commission, and you reduce that to 20% during winter storage the interior woodwork can shrink, warp and crack. Not a common problem, but I can see it being an issue if you shrink-wrap the boat for winter and put a big dehumidifier inside.
WHAT ABOUT FLOODING?
That deals with the insidious leaks. What about the major ones? This is quite simple. If, for any reason, your boat fills with water, it is likely to sink! We all know that. If you are sailing in bad weather, some water is always going to get below. Unless you put the mast in the water, this water intrusion should not become catastrophic. Even water up to the floorboards should not be a massive issue unless some of the electrical stuff runs through the bilges, which, ideally, it shouldn’t. There is a potential for critical issues with flooded bilges if the propane alarm sensors get submerged. In this case they may fail as they are not normally waterproof, so it might lead to a dangerous build-up of propane that you are not aware of.
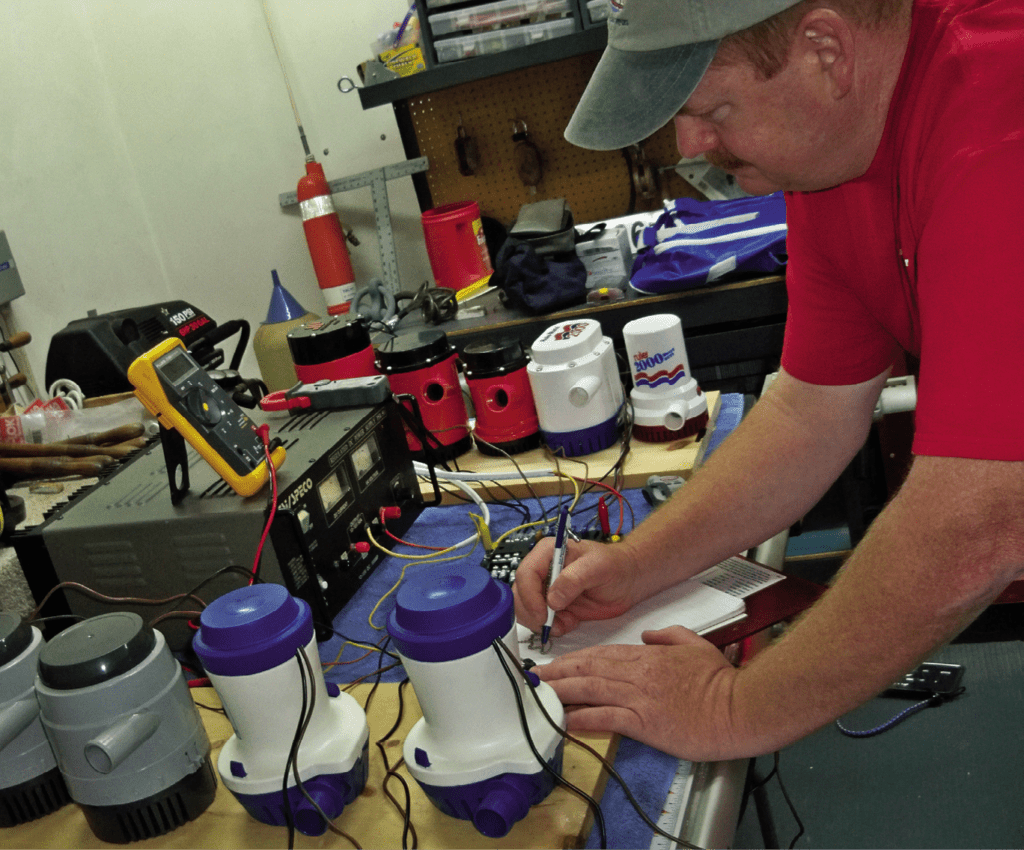
Those are all issues with water getting in through normal openings in the deck, hatches, companionways etc. But catastrophic or critical flooding should only result from a major issue like collision or hard grounding. Also, if the boat is rolled and stays inverted for some time or the companionway was not fully closed, it may get enough water below deck to mean that the next big wave will overwhelm her. This is an issue with large cockpits equipped with only modest scuppers. Cockpits hold a LOT of water.
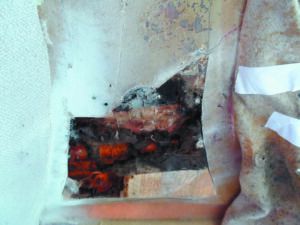
But other things can go wrong that will introduce water into the boat. If a fitting fails and the rudder comes adrift, or the prop-shaft seal fails, you will also get catastrophic flooding. A typical 35-ft. sailboat will fill with water up to the floorboards in less than 1 or 2 minutes if you remove the log impeller, which creates a 1 1/4-in. hole. How do I know that? I routinely remove the impeller to flush the bilges and check the pumps. This may be harsh, but I want to know that if a fitting fails I will have time to find and plug it before the boat sinks. I have seen lots of boats sink, including ones at boat shows, that don’t have proper bilge pumps fitted. I am including this as a ‘hidden’ issue that could sink your boat because most of the time the skipper does not realize there is even an issue. “That is the pump the boat manufacturer fitted so surely it’s adequate, right?” I am not suggesting that some boats don’t have any pumps, but a 1500-gal./hr. pump in the bilges is not a bilge pump. It is more properly described as a de-watering pump.
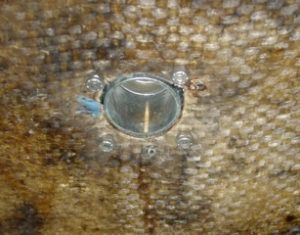
It is fine for getting rid of the water that normally gets in during bad weather, but will it be effective in serious flooding? For that, most boats will require a total capacity of at least 4,000-gal./hr. (the size recommended by the Canadian Coast Guard for a typical cruising boat). A single pump of that size will have a 1 ½– or 2-inch outlet, which is difficult to fit. If that is an issue, you can use smaller pumps, but bear in mind that they are less efficient. 2 x 2,000-gal. pumps do not shift as much water as 1 4,000-gal. pump due to the resistance created by additional hoses. You need to go up to 3x 2,000-gal. pumps to surpass 2x. Ideally, the bilge pumps should be fitted an inch or two above the de-watering pump with separate float switches linked to an alarm. This means that they normally stay dry, which makes them more reliable. If the alarm goes off, you know immediately that the de-watering pump has been overwhelmed and you have a critical flooding incident.
Don’t forget the hose clips. Poor quality single clips or perished (broken) hoses are asking for failure and major flooding. All through-hoses should be fastened with double heavy-duty hose clips (or clamps) and inspected annually. Check the hose for flexibility. If it has gone hard, it is at the end of its life. If hoses become rigid, the normal vibrations from sailing or motoring can lead to splitting. Include checking and cleaning any anti-siphon valves in any loops, as they can often get clogged with salt and debris.
The next installment of Hidden Maintenance Problems will come next week. We’ll cover common electrical issues lurking in your battery box and behind your circuit-breaker panel.