Dyneema fibers are given a thin polyurethane coating at the factory that reduces chafe, UV damage, and adds some stiffness. Hoping that an aftermarket coating would provide extended protection against chafe and UV damage, we decided to investigate.
A coating for Dyneema will need to be watery so that it can soak deeply into the fibers, which naturally resist absorption (hydrophobic). The resulting coating will be thin and will not stiffen the rope like full-strength coatings we’ve tested on other ropes.
The diluted coating does slightly stiffen, or “firm” the rope. Heavier coatings are sometimes recommended for industrial applications or other uses like winches where the coating helps keep out grit. We have used heavier applications on anchor rode leads for kedges and tandem rodes, when abrasion and grit resistance is beneficial (see “Doubling Up: Full-size Tandem Anchoring,” PS September 2016).
The coating won’t soak into tensioned lines like rigging, but you can apply a maintenance coat at chafe points on halyards and topping lifts. Makers of soft shackles and loops (Equiplite, INO and others) recommend coating soft shackles and loops. We would not coat soft shackles that are subjected to any flogging, as they might flog loose. We would not use them on whoopie slings, because safety is contingent upon the sling’s friction (see “Whoopie Slings for Sailors, PS April 2021).
We’ve recoated Dyneema shroud tensioners, whisker stays, anchor bridles, bobstays, and lifelines and been generally pleased with the results.
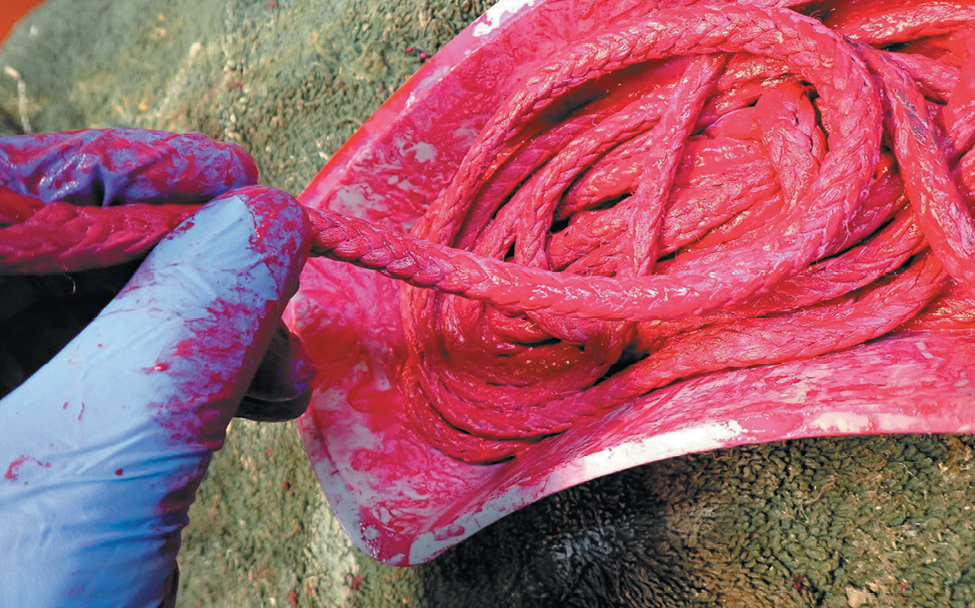
WHAT WE TESTED
We tested Yale Maxijacket, Flexabar Rope Dip, and Marlow ArmourCoat. Maxijacket is typically used full strength. It’s a little thicker than house paint, so we thinned it 5:1 with water until it was runny enough to soak into the Dyneema. Rope Dip is more of a paste, and we diluted it 10:1. ArmourCoat is supplied ready to use. (There are two other coatings that are used full strength that we did not test: INO Rope Coating and Gator Dip).
HOW WE TESTED
We liberally applied all three coatings. We used a brush on lines that were spliced in place and could be slackened. You cannot recoat any lines that are under tension, the weave will not allow good penetration. We dipped ropes in a bucket, mashing the rope about to coat the interior fibers as completely as we could.
We wiped off the excess coating using our gloved fingers. Too much coating will stiffen the rope. Prior to coating any splices, we milked them—squeezing firmly in the direction away from the rope end or loop. This helped reset them for coating.
You need to allow the coated ropes to dry for about three days. We used coat hanger hooks to hang them from the ceiling.
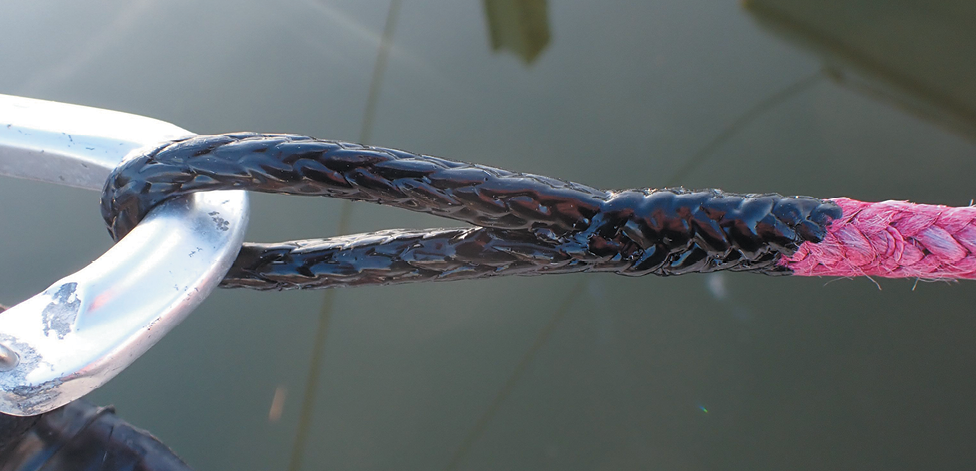
CONCLUSION
After drying for a week, we put the coated ropes on both side-to-side and end-to-end chafe machines. All the coatings performed similarly; they significantly reduced side-to-side chafe and reduced end-to-end chafe by a lesser degree. No product was an obvious winner. We can no longer find Flexabar Rope Dip, so Maxijacket, which has become increasingly hard to find, is our top pick.