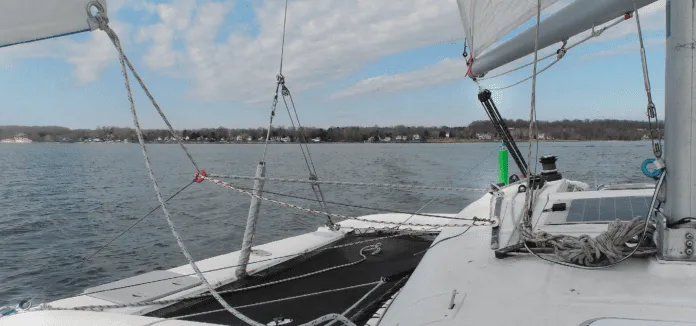
Ball bearing blocks are the low-friction answer for most tackle on board. However, racers and even cruisers, are increasingly making the switch to low friction rings for applications where compact size, low weight, and high strength are important: high load cascade tackles on Cunninghams, vangs, bobstays, and backstays, for example.
We can also use them where there is not a lot of friction involved; deflecting sheets with Barber haulers and twings are examples. Their light weight and compact size are also a plus for cruisers. There is less weight banging around, they run smoothly, they are immensely strong, and there is nothing to break.
We have quite a few low-friction rings on our test boat, but we stick with ball bearing blocks for all of our high-load turning blocks and most of our other tackle for running rigging. We reported on this in “Try a Barber Hauler for Better Sail Trim” (see PS September 2019) and “Sizing Up Improvements in Low Friction Rings” (see PS August 2021).

The solid ring is a variation on the low-friction ring. Instead of a doughnut with a wide groove around the outside, it is a plain ring. It is similar to the heavy stainless rings used in the clew of a sail or as a reefing pendant, but it is made from lightweight, high-strength anodized aluminum, and is much thicker, presenting a broader radius to any ropes passing through it. (The Antal “solid” rings have a shallow groove, but it is not used for splicing or lashing in place.)
The radius of a solid ring is less than that of a low friction ring of the same inside diameter. A solid ring can replace a smaller low-friction ring with a similar radius, or in scenarios where the smaller radius turn is not a problem (a lead that is only slightly redirecting a line, for example). Solid rings allow room in the center for multiple control lines, and they are easier to quickly thread, since their holes are bigger.
In terms of strength, solid rings are comparable to low friction ring designated for the same line size. They are heavier than low friction rings, but still much lighter than ball bearing blocks or stainless rings.
Now that we’ve addressed some of the pros and cons of solid rings as compared to low-friction rings, let’s dig a little deeper into their use.
THE “FLOATING” OR “3D” LEAD
A low-friction ring makes a fine Barber hauler for small boats. It requires no extra purchase and you can splice the control line directly to it. Larger boats, however, often require 2:1 or greater purchase, and that entails making room for tackle.
A common use for both solid rings and machined low-friction-rings is in “floating” genoa leads, which can allow adjustment in three dimensions (inboard-outboard, forward-aft, up-and down) as opposed to the one-dimensional lead track (fore-and-aft). Floating genoa leads on big boats require multiple control lines with a 2:1 or greater purchase on each line. A second reaching sheet, if required to avoid a shroud or other obstruction, can even be run through the same ring.
Of course, all of this can be accomplished with conventional blocks or low friction rings, but the hardware is big and heavy and additional components and connections are required. The result is a whole lot of hardware flopping around on the sheet. A solid ring does this far more simply.
CRUISING APPLICATIONS
A floating lead expands your sheeting options and is often used for tighter sheeting when going to windward. Twelve-meter racing yachts may tack through 70 degrees (35 degrees to each side), but most of us tack though something closer to 100 degrees as measured over the ground, or maybe 90 degrees in perfect conditions. A quick glance at Figure 1 on page 22 reveals that although sheeting angle for maximum driving force is 7.5 degrees or even less for boats that can point very high, for most of us, the best sheeting angle lies between 10 and 15 degrees, depending on the hull design, sail condition, and bottom fouling.
Even if you don’t want to commit to floating leads, you can still use a temporary one to squeeze out maximum milage during a long tradewind passage—or to improve your ability to punch to windward in a stiff breeze.
A temporary setup is also great method for locating the optimum position for a new track. To do this, rig a temporary floating lead using any available hard points, winches, and cleats. When you get the shape you want, place a straight edge on the sheet. Where the straight edge meets the deck is where you want the track.
Beware of mixed metals. For reefing pendants and Cunninghams that hook on a stainless-steel ram’s horn near the gooseneck, we prefer stainless rings because they are galvanically compatible with the stainless steel hook, and resist wearing better. But for applications where a line is fed through the solid ring for additional purchase, the greater radius of an aluminum ring offers less friction than a stainless ring and is easier to thread.
WHAT WE TESTED
We’re constantly tweaking our test boat, and in the process have added several low-friction rings to our running rigging (search “low friction rings” in the PS archives for several previous tests). In this report, we are testing a new range solutions where we think solid rings have advantages over low-friction rings.
FLOATING JIB LEADS
Our previous Barber hauler used low friction rings. However, the jib lead cars are secured by a spring-loaded pin, and we got tired of struggling to adjust them when a sail was flogging. We switched to a floating lead system, using the existing barber hauler control line, a 2:1 downhaul to a point well forward on the track, and a rappel ring. At the same time, we converted the Barber hauler control line from 7/16-inch polyester double braid to 6 mm Amsteel. We covered the Amsteel with 5/16-inch polyester where it is handled or cleated.
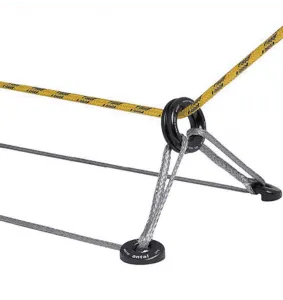
The conversion to Dyneema (Amsteel) control lines reduced friction. The 2:1 downhaul purchase is insufficient for large adjustments under full load, but we luff up when reefing anyway. Minor tweaks can be made with a single tug. Reaching adjustments require us to adjust the outhauler as well. We have not noticed any increased friction on the jib sheet since switching from a low friction ring to a rappel ring.
We combined the downhaul (AKA inhauler) and Barber hauler (AKA outhauler) lines into one continuous loop, eliminating loose tails and reducing total line length. Now, when the outboard Barber hauler is pulled to bring the genoa clew out, the tail of the inboard end gets longer, and the outboard tail gets shorter. A continuous loop also reduces tangles, since there is no free end to form knots.
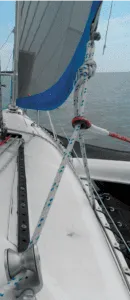
Dyneema is slippery and runs over low friction rings and solid rings with little friction. However, it is also too slippery and generally too small to handle or to hold in cam cleats or jammers. The solution is to either use a Dyneema core line with a polyester cover that can be removed, such as NER Endurabraid, or to splice a cover salvaged from a good polyester double braid scrap over Amsteel or another brand of Dyneema singlebraid. Cover any portion that will be handled (see “Adding a Cover to Dyneema Single Braid,” PS December 2018). See also instruction from Samson (www.samsonrope.com/docs/default-source/splice-instructions/dblbrd_c2_stripping_cover_web.pdf). There is also a video from Premium Ropes (www.youtube.com/watch?v=x62BoCSpReA).
You can use table on page 19 to match covers and cores. Remember that diameters vary slightly between brands and product lines.
KNOTS VS. SPLICES IN DYNEEMA SINGLE BRAID
Knots weaken Dyneema, more than other ropes, as much as 70 percent. All but a few knots will slip under moderate load. A bury splice, either lock stitched or with a Brummell splice is an easy way to avoid knots, but knots offer an advantage in control lines that are very lightly loaded.
Keep in mind that we are using Dyneema here for its slipperiness. We could actually use much smaller diameter Dyneema, but lines smaller than 5mm are hard to splice and will requires adding multiple covers make them large enough to grip.
In many cases, the maximum load may only be a few hundred pounds on a line that is rated at 4,500 pounds. That is less than 5 percent of breaking strength—so any strength lost in a knot isn’t critical. Knots are adjustable, which is an advantage for control lines that you may want change.
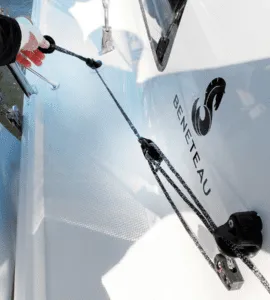
Even though we can quickly splice single-braid lines, you’ll see knotted Dyneema on our test boat. What knots work? In most cases, a bowline with the tail seized, or string of four or more half hitches with the tail taped down will usually do the job.
PRODUCTS
Recognizing that many of the low-friction rings used in the sailing market are variations of equipment that climbers also use, we again looked beyond the marine market for rings. One reassuring aspect of climbing hardware is that it has published load ratings verified to an international standard (see “Ocean Test: Rock Climbing Gear,” PS September 2013).
RAPPEL RINGS
Known as rap rings to climbers, these are used in place of carabineers to rig descents in the mountains. They are cheap enough to leave behind, are lower in friction than carabiners, and cannot unclip. They are UIAA-certified to a minimum strength of 20 kN (4,500 pounds), but most are stronger than that, up to 8,500 pounds.
Avoid non-certified rings and beware of Chinese-made copies. Many bear a “CE” stamp, masquerading as European Community-approved “CE” products, when in fact “CE” may only signify that the product is a Chinese export.
We like Kong brand for quality and price. Kong makes the Tango carabiners that have become the standard for jackline tether clips. The anodized coatings are smooth and reasonably hard wearing.
ANTAL SOLID RINGS
Compared to rappel rings, Antal rings are more expensive, much stronger, and 2.5 times heavier for a given size. They are available in sizes up to 50 mm inside diameter. The finish on the Antal rings is smoother, the anodizing is much thicker, and they will wear much longer under high loads. On boats under 35 feet and in most applications, the additional anodizing won’t make a big difference. For larger boats, the heavier Antal rings are safer for high loads and critical applications.
Antal does not state maximum line size for a solid ring. The assumption is that the line will be Dyneema and the deflection will be limited. We’ve used rings with polyester genoa sheets with diameters that are 33-percent of the ring’s inside diameter. For control lines that make 180-degree bends around the ring, ½-wide webbing and 6 mm Dyneema work well with the 12 mm ring thickness (see the photos of our Cunningham “deflector” on page 18). We’ve made two passes of 3/8-inch (9 mm) line through a ring used to lash the mainsail reef clew to the boom without trouble.
STAINLESS RINGS
These are a good solution anywhere high loads must bear against stainless shackles or hooks. Extreme point loading will crack the anodizing, allowing corrosion to start under it, peeling the coating. Stainless rings have a smaller diameter radius which adds friction, so they are seldom used to deflect control lines. They are also inefficient when used with lashings.
They are heavy and quality control is extremely variable. Stick with major brands. We had a no-name ¼-inch x 1 ½-inch ID stainless ring fail at only 5 percent of the listed breaking strength. Crevice corrosion of the weld may have been a factor (aluminum rings are forged, not welded).
Other applications for stainless rings include lashing down gear, or for securing a dinghy on deck or on davits.
CONCLUSIONS
Stainless rings have their uses, but not for running rigging where there is motion; the bend radius is too small. Antal Solid Rings are very well made and are well proven on race boat sail clews and floating jib leads. Anodized aluminum rappel rings provide a reliable but bargain solution for smaller boats and lower load applications. They don’t replace blocks or low friction rings, but rather add one more solution to your rigging tool box.
TECH SPECS: ROPE DIAMETERS
ROPE DIAMETER METRIC | CORE DIAMETER METRIC | ROPE DIAMETER INCHES | CORE DIAMETER INCHES |
---|---|---|---|
6 mm | 4 mm | 1/4 inches | 3/16 inches |
7 mm | 5 mm | 5/32 | 3/16 |
8 mm | 6 mm | 5/16 | 1/4 |
10 mm | 7 mm | 3/8 | 5/16 |
11 mm | 8 mm | 7/16 | 5/16 |
12 mm | 9 mm | 1/2 | 3/8 |
VALUE GUIDE: SOLID RINGS FOR RUNNING RIGGING
SOLID RINGS | ANTAL | OMEGA PACIFIC | CAMP | KONG | XINDA | SMC | WEST MARINE |
---|---|---|---|---|---|---|---|
MODEL | Solid Ring, R34.54 | Rappel Ring | Rappel Ring | ANA Rappel Ring | Rappel Ring | Rigging Ring | Stainless Ring |
INSIDE DIAMETER | 34 mm | 31 mm | 34 mm | 46 mm | 45 mm | 28 mm | 37 mm |
WEIGHT | 89 grams | 34 grams | 34 grams | 53 grams | 53 grams | 26 grams | 59 grams |
THICKNESS | 18 mm | 11 mm | 12 mm | 12 mm | 12 mm | 12 mm | 8 mm |
MIN. BREAK STRENGTH | Not given | 4,500 lbs. | 4,950 lbs. | 5,850 lbs. | 4,950 lbs. | 7,200 lbs. | 12,800 lbs. |
SAFE WORKING LOAD | 6,160 lbs. | 1,000 lbs. | 990 lbs. | 1,170 lbs. | 990 lbs. | 1,440 lbs. | 750 lbs. |
NYLON | 66% | 62% | Not tested | 62% | Not tested | Not tested | Not tested |
AMSTEEL | 72% | 66% | Not tested | 66% | Not tested | Not tested | Not tested |
PRICE | $36 | $5 | $14 | $10.50 | $6 | $6 | $7 |
1. Cunningham deflector. The test boat is rigged with roller boom furling, and so there is no positive attachment from the tack to the mast. The outhaul pulls the foot of the sail away from the mast, damaging the luff tape unless there is a firm forward pull on the tack, Cunningham, or reefing grommet. We use a strop around the mast, fitted with a rappel ring on either side, to deflect the Cunningham line forward, pulling the tack forward (see “Getting the most out of Older Sails,” PS January 2022). Previously, we used low friction rings, which worked, but were difficult to thread and dug into the mast. The rap rings are easier to thread (bigger hole and more to hold on to) and lie smoothly against the mast. Chafe tape protects the mast (see “Chafe Tape Plan,“ PS December 2020.)
2. Mainsail Clew Reefing Strop. Also a consequence of roller reefing, there is no fixed position to attach a clew reefing line or lashing. Friction can be high, and the rope can cut into the rolled sail. We fitted rap ring with a webbing loop that we choke around the boom end, and ran the reefing lashing around that. The ring is easy to thread, reduces friction, and allows room for lots of passes. A separate ring can be choked onto the boom for each subsequent reef. A low friction ring that is as easy to thread and large enough for all the lashings would be impractically large (see “A Custom-fitted Clew Strop,” PS August 2019).
1. A side-by-side comparison between stainless steel rings, and a rappel ring illustrates the difference in dimensions.
2. Kong’s rappel ring used for climbing is clearly rated for 25 kiloNewtons or 5,620 pounds.
3. Antal’s solid ring features a shallow groove and a thicker anodized protection. Antal also sells the conventional low friction rings with deeper grooves (see “Sizing Up Improvements in Low Friction Rings,” PS August 2021).
Hello, I have Re subscribed to Practical Sailor several months ago. Should I be receiving a link to the Practical Sailor magazine in my emails each month. This is not happening. I am still getting emails each month about “ subscribing”; which, as I said I have done so earlier. Please advise, regards John