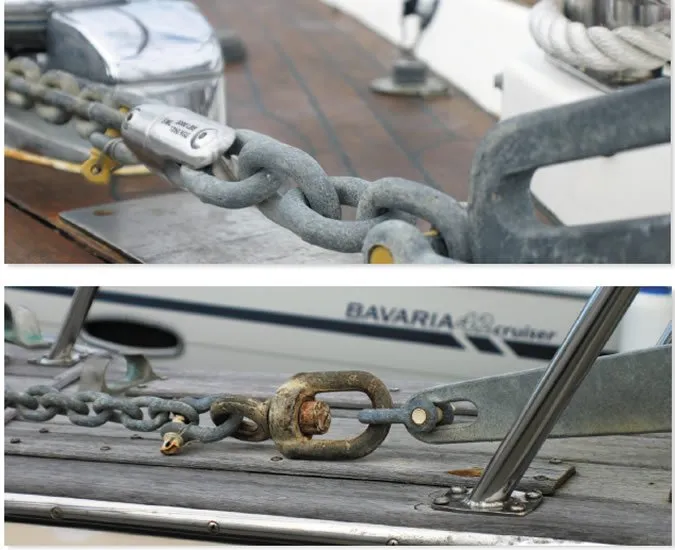
Photos by Jonathan Neeves
Stroll down the docks at any boat show, and youll see a surprising number of boats equipped with expensive, stainless-steel swivels between the anchor and the chain. Almost all of these swivels are highly polished, machined and/or welded gems that cost anywhere from $80 to $200 or more. By comparison, a galvanized anchor shackle rated to withstand the same or greater loads as the chain rode we rely on costs less than $15. (See PS August 2015 online.)
The rising popularity of anchor swivels can be traced to a number of factors. The swivel proponents say that it reduces the amount of twist in the chain so that the windlass can more easily flake the chain down a chain pipe and into the chain locker without jamming. A twist-free chain also spills more easily out of the locker when deploying.
A more commonly touted advantage is the swivels ability to help coax the anchor up into the anchor roller. The swivel helps the anchor to rotate into the right orientation so that it can self-stow.
In most cases, these problems amount to mere nuisances. You can usually overcome them without the use of an anchor swivel, and without too much expense or effort. (See Chain Jams and other Windlass Woes, Inside Practical Sailor, May 20, 2014.)
A few long-term cruisers, some windlass manufacturers, and others have promoted the use of anchor swivels, but we-like several anchor makers we spoke with-remain unconvinced.
Generally swivels are only really required when anchors spin (hydro-rotate) in the water on deployment and retrieval, said Ned Wood of Manson Anchors. Evidence of this would be when you hear the chain skipping on the gypsy.
One of our concerns is material. Stainless steel, in our view, is to be avoided for any load-bearing components in the anchor rode. (For more details regarding our aversion to stainless steel, see our special report, Marine Metal Warning PS February 2007 online).
In the course of researching this topic, we tracked down several examples of broken swivels, both stainless and galvanized. Although we have no data showing how widespread swivel failure is, the bottom line is that adding an anchor swivel adds a potential failure point, something we want to avoid in the anchor rode.
To get a better understanding of how they can fail, we conducted simple tests on a few swivel samples to induce various modes of failure. We also put several swivels to use in the field, hoping to discover how well they work and whether any advantages are worth the expense.
Types of Swivels
There are a few types of anchor swivels: box swivels, cup swivels, ball-and-socket swivels, and universal swivels. To further confuse things, box swivels are also sometimes called barrel swivels. In box swivels, the parts that rotate are largely hidden from view. Cup swivels, also known as open swivels because you can see nearly all of the working parts, are more easily inspected.
Box swivels have a common design. At each end is a two-pronged fork, and there is a clevis pin (often threaded) that closes the forks. In effect, each end is a shackle. One fork is slightly narrower, to fit the chain. The wider fork is often attached directly to the anchor.
The rotating swivel in a box swivel is a simple rod that joins the two forks in a manner that allows each end to independently rotate. AnchorLift, Imtra, West Marine, and Seadog all offer swivels of this type.
Cup swivels are commonly used for moorings (preferably above the water for easy inspection) and sometimes in anchor rodes. They are typically galvanized steel, but weve also seen stainless cup swivels. Cup swivels are relatively large and look more utilitarian than box swivels. A large number of unrated, no-name cup swivels (stainless and galvanized) come from factories in China. However, you can find load-rated, galvanized cup swivels from reputable U.S. makers like Peerless, Campbell, Crosby, and Chicago Hardware.
The ball-and-socket swivel is a cross between a cup and box swivel; the working parts are visible but some of the internal socket is hidden. Ball-and-socket swivels that have earned a good reputation among cruising sailors include Wasi Powerball and Ultra Flip Swivel, expensive swivels that have been designed from the start to eliminate weaknesses found in other designs. Apart from a voluntary, 2010 swivel recall by Ultra-importer Quickline (see Inside Practical Sailor blog, Dec. 15, 2010), were not aware of any of these brands being prone to specific problems. However, because of the relatively low numbers of these swivels in the field, its hard to draw any firm conclusions regarding their reliability. Nevertheless, it is prudent to steer clear of unrated, stainless-steel swivels selling for what seems like bargain prices.
The universal swivel is a variant of the box swivel.
The swivel mechanism not only rotates, it has an additional but separate articulation (a hinge). The joint slightly reduces the extra leverage on the forks when connected directly to the anchor shank, but the hinge is yet another potential point of weakness. Suncor is among the reputable brands of universal swivels.
Swivel styles can be described as eye and eye, eye and jaw, or jaw and jaw. When the swivel rod connects two forked ends, each of which is closed with a clevis pin or sexbolt, it is described as a jaw-and-jaw swivel. A swivel with one forked end with a clevis pin and one end that is metal ring (or eye) is called a jaw-and-eye swivel; one with two eyes connected by a swivel rod is appropriately called an eye-and-eye swivel. Most makers offer swivels in all three configurations.
Some makers advise against attaching swivels directly to the anchor, instead recommending a shackle and even a short length of chain leader to prevent any side loading on the forks. Some swivels are much weaker under side loads, making it more likely that the forks can be pried open, ultimately leading to a failure at the fork or clevis pin.
We would also worry about older swivels, even from well-known makers. Some older designs had thinner forks that were not strong enough to withstand the side loading that can occur when the swivel is no longer aligned with the load. Side-loading is more common with the newer, deep-setting anchors, which require far higher loads to reset when the wind shifts.
Failure Modes
The cause of failure in the field often remains a mystery because all or most of the evidence is never recovered. Based on our research, limited testing, and the samples we have received, the most typical failures are the following.
Bent Fork
Bending at the fork is very common. Many swivels we see are attached directly to the anchor with the clevis pin secured directly to the anchor shank. Modern anchors are capable of holding under very high loads, and don’t rotate so easily as the load direction changes. The swivel is quite long, so that the fork acts as a lever, amplifying any side load. When the angle of pull comes from one side of the anchor, something has to give. Usually, this is the swivel.
One way to prevent the fork from bending is by introducing a shackle, or a shackle and a few links of chain, between the fork and shank. In fact, Kong strongly recommends isolating the swivel using a shackle and length of chain in this manner, but few owners seem to follow this guidance.
Because stainless steel is not a very ductile alloy, a component showing signs of bending may be significantly weakened and should be replaced.
Pin Failure
The most typical failure occurs at the clevis pin on the end that is secured to the anchor. The failure is often preceded by the forks side loading. The side load causes one or both of the forks bend, and this, in turn, sheers the head off the clevis pin, or causes the threaded components to tear apart.
A close examination of the construction of an inexpensive box swivel reveals how these failures occur. In reality, the clevis pin is not a solid, high-tensile, clevis pin but a machined sex bolt, a bolt made of two threaded parts, one male and one female. The longitudinal center of the female part is drilled and tapped to accept the matching male bolt, and this assembly helps lock the clevis pin in place. Obviously, the hole in the center of the female component reduces its strength. The head of the male component is often welded on, and the weld can be weak.
In some of the swivels we examined, the failure occurred when the forks began to bend and the increased tension on the bolt assembly ripped the male bolt out of the threaded female part, or the head off the male bolt simply sheared off. In other cases, the clevis pin sheared near the center, because it simply could not withstand the load.
The clevis pin at the chain end of the swivel is a similarly engineered sex bolt. As a result of this two-part design, on some swivels, the 3/8-inch diameter pin is actually much weaker than a 5/16-inch G43 chain.
In our destructive testing, these clevis pins failed in the similar way bow anchor shackles failed in our previous tests (see PS July 2015 online). The forks began to spread, and the pin pulled out or sheared at the thread.
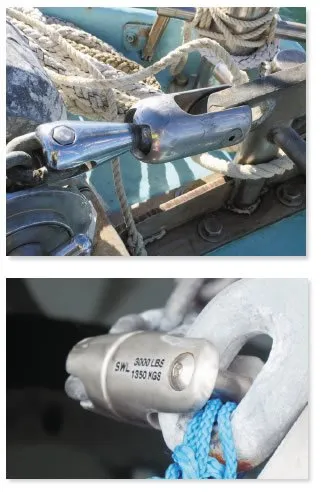
Bearing Failure
The bearing where the two forks join and rotate is also prone to failure. Commonly, the bearing is a threaded stud set into one-half of the component and secured by welding the stud (see A Closer Look on right on right). The bearing surface is a simple cap welded onto the stud. The quality of the welding at the cap can be questionable and the weld is often weakened by corrosion, which can lead to failure.
False Confidence
As we saw in our report on the hidden causes of rigging failure in the May 2015 issue, many swivel failures can be traced to our own ignorance. Because stainless-steel swivels are relatively expensive, we think they should last forever. But just as with rigging, the dynamic loading takes its toll over time. Moreover, the weak components are hidden from view. It is impossible to see the swivel mechanism at all, and unless you disassemble the swivel and inspect it regularly, the condition of the clevis pins remains a mystery.
The cup swivel lets you see all the critical components. We tested two galvanized cup swivels, one from Peerless (Acco) and another from Campbell; both U.S.-based manufacturers anchor shackles did well in our recent test (see PS July 2015 only). The two swivels were surprisingly similar; both were 5/16-inch models, for a 5/16th inch chain, and both failed at 7,500 pounds. One of them failed in the body of the swivel, and the other failed at the clevis pin.
The ultimate tensile strength (UTS) for these swivels is consistent with the advertised working load limit (WLL) of 1,250 pounds (with a 3:1 safety factor). But this is well below that of a typical 5/16-inch G30 chain, which has a UTS of 9,000 pounds. If you insist on having a swivel for your 5/16-inch anchor chain, you should at least upgrade to a 3/8-inch swivel (WLL of 2,250 pounds), or even a half-inch swivel (WLL of 3,600 pounds), if it fits. If you use larger chain, you also will want to upsize the swivel to match the chains UTS.
Unlike a box swivel, all the potential wear points in a cup swivel are easily visible. The swivel mechanism is a bolt with the nut welded on, so its secured by two means-the threads and the welded cap. The clevis pins are threaded like many anchor shackles (secured then Loctite applied and/or mousing), or use clevis pins locked.
Conclusions
Except in special circumstances, we have seen no evidence that a swivel solves any significant issues. There is evidence that the cheaper, stainless box swivels fail for a number of reasons related to poor engineering or poor assembly. Also, attaching swivels directly to the anchor shank can exacerbate the potential of failure.
If you must use a swivel-and we have great difficulty in endorsing the practice-then a galvanized, cup/open swivel that is the same size as the chain is too weak. Be sure to go up two sizes, and wed suggest choosing an eye-and-eye cup swivel so that you can attach a secure, quality shackle to each end. Steer clear of any low-priced, no-name stainless swivels, even if theyre oversized. In our opinion, no swivel should be attached directly to the shank of an anchor, because side loading greatly reduces the safety factor. Unless your swivel or shackle can match 100 percent of chains ultimate tensile strength at any angle of pull, it is not worth the risk.
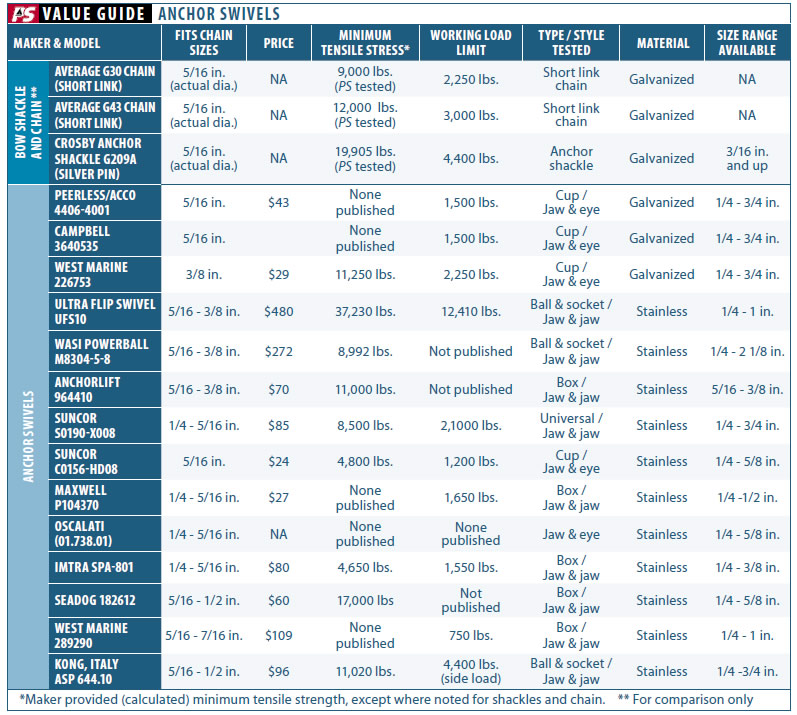
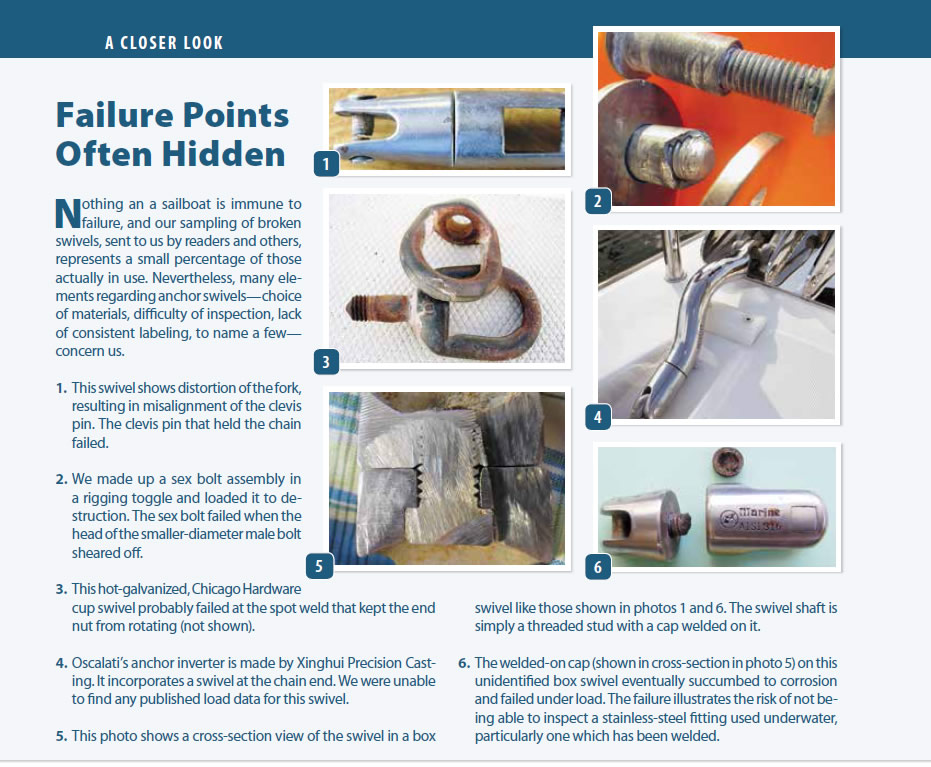
I have a concern about the Ultra Flip Swivel. This swivel appears to be very well made and quite robust in size and overall design. However, I feel that it is vulnerable to bending loads.
The swivel attaches to the anchor such that it can only rotate in one plane. If the anchor jams while the rode rotates, the swivel can be put into a bending load arrangement. Ultra has provided test data with the swivel in tension and these test results seem to agree estimated breaking strength from rough engineering calculations that I have done. This tension breaking strength is indeed very high. When I asked Ultra about bending, they tell me that they have tested the swivel in bending and that the ultimate strength in bending is equal to those in tension. When I asked for that test data, they told me that they were unable to share the data, which seems suspicious. I have done a rough engineering evaluation of this swivel in bending. With the rode load applied at a 90 degree angle to the main swivel pin, I find that the breaking load is less than 10% of that in pure tension. My calculations indicate that he swivel’s pivot arm will fail in bending near the ball joint. I’m curious if there are any known failures of the Ultra Flip Swivel due to this sort of off-axis loading.