Performance-oriented sailors recognize that leeway is one of the last variables left to be accurately quantified. It can be defined as a sailboats movement through the water in a direction that differs from the boats heading. Unfortunately, todays paddle-wheel transducers and most electronic speed sensors provide only inline velocity readings related to the direction that the boat is heading.
Electronic position-fixing systems like GPS give us velocity and course relative to the earths surface, which usually differ slightly, or on some occasions largely, from your boats actual speed and direction through the water. Comparing the two via some smart navigation software defines current set and drift. But when it comes to sailboats on an upwind heading, the effect of leeway clouds this picture, and the quest for a means to directly measure leeway remains a worthy goal, especially among racing sailors. The ability to measure the slight increases and decreases in this sideways movement is very valuable when it comes to making tactical decisions.
Until now, efforts to measure this side-slip through the water have been hampered by transducer technology. Even the recent switch from paddle wheel to electromagnetic (EM) sensing didnt quite do the trick. Part of the problem is the non-laminar, turbulent flow that occurs close to the hull in the boundary layer. Attempts to use ultrasonic sensing, like that offered by Airmar, were less effective because of the interference from entrained air bubbles. So the hunt for a transducer that yields accurate speed and leeway continues.
Leeway is a big deal when it comes to beating to windward. Its influenced by changes in sail trim, sail shape, heel, and the boats angle of attack-just to name a few variables. Leeway is relative to the water that the boat is sailing through, and a sailboats propensity toward side-slipping varies from one design to another.
In a nutshell, short, wide, shallow-draft hulls are most prone to this form of side slip. Sailboats equipped with a centerboard or daggerboard can convincingly display an improvement in upwind performance when the board is lowered. Sailmakers and serious racers also know that leeway is a derivative of much more than foil design.
Although variations in leeway are usually only tallied in 10ths of a knot, the net effect is significant. This data would give the crew a chance to alter heel angle, change sail shape and trim, and even affect slight course changes in order to lessen leeway and improve overall upwind performance. Altering leeway while checking its influence on boat speed through the water and noting velocity made good (VMG) and course over ground (COG) affords a tactical advantage.
Larry Marsh and his company, Brickhouse Innovations, have pioneered a logical approach to sensing multi-directional movement through the water column. A detailed description of Marshs efforts is described below, but before getting into that, some background in measuring boat speed through water is in order.
Speed Sensor Evolution
In the 14th century, European sailors relied on a novel invention called the Dutchmans log to record speed. The crew measured boat speed by tossing a buoyant item off the bow and counting the seconds it took for the object to reach the stern. They took that data and inserted it in a time-and-distance-based equation (Distance = Rate of speed x Time) that turned feet per second into nautical miles per hour.
This was a stride forward in the empirical approach to navigation, but the inaccuracy of counting off seconds and the inherent magnification of errors in such a snapshot greatly reduced accuracy.
The Brits, always ready to improve a good idea, came up with the chip log and string approach to speed measurement. This method involved a floating piece of timber connected to light line on a free-running spool. It was more or less an oversized fishing reel that was attached just above the taffrail of the vessel. A sandglass supposedly improved time-taking, and the measurement was based on how much line paid out over a given measure of time.
Eventually, the spinning walker log, which incorporated a propeller-like appendage trailing astern, replaced the chip log. It constantly provided torque to turn a set of smooth-spinning gears that drove the distance-recording dials on the face of the unit. These logs measured distance based on revolutions of the line. Speed could be calculated by once again using the familiar equation of rate of speed (R) equals distance (D) divided by time (T), or R = D / T.
Finally, 20th-century efforts to measure velocity through the water enlisted tubes and hydraulic pressure gauges to quantify boat speed. For a while, even lever-like appendages were used to directly measure boat speed. They would bend in accordance with water flow, defining boat speed; at least that was the case up until a bit of seaweed or other flotsam grabbed hold. Eventually, electron flow took over, and sensitive galvanometers were harnessed as knot meters.
Through-hull openings allowed small, paddle-wheel-driven mini generators to spin with the water flow. Sailors developed a love-hate relationship for the knot meter that threatened to flood the bilge each time the transducer had to be cleaned. But the biggest drawback was the turbulent flow in the boundary layer as water flowed close to the hull.
If you really want to know how fast you are going through the water, you need to measure velocity farther away from the hull skin. Water so close to the boat ends up being dragged along by friction, and its relationship to the free-stream velocity varies with boat speed, boat shape, and sensor placement.
The first, patented electromagnetic ships log was invented in 1917 by Smith and Slepian. And since that time, there have been many attempts to improve on the design with much of this effort focused on measuring the boat speed outside of the changing boundary layer. Some of these designs had sensors that were streamlined and located several feet away from the hull skin. They were extracted through a sea valve for cleaning or repair. Typically, these configurations were used on larger ships, both commercial and military, and they only measured the forward speed of the boat.
In the latter part of the 20th-century, several manufacturers marketed two-axis EM speedometers that could measure both the forward speed and the leeway speed. Unfortunately, these sensors energized only a small volume of water, typically less than the size of a ping-pong ball and located immediately adjacent the hull. Because all of the speed measurement was in the boundary layer, the measurements were not consistent or reliable, and the accuracy was not any better than that of a paddle wheel.
Brickhouse EM Sensor
Brickhouse Innovations new transducer uses a pulsating magnetic field to induce small electrical voltages in the water adjacent to the hull sensor. This novel design, however, creates voltages in water molecules up to six inches away from the hull, reaching out beyond the inner boundary layer.
The Brickhouse transducer, like previous EM sensors, fits most standard speedo through-hull fittings. Four, small, nonmoving, nub-like, stainless-steel electrodes are embedded in the removable through-hull insert and make contact with the water near the hull. However, unlike previous EM sensors that had both the electrodes and a small electromagnet contained within the sensor, the Brickhouse Innovations sensor has an electromagnetic coil that is separate from the electrode assembly.
The electromagnet that penetrates the non-metallic hull and energizes the water flowing by is a lightweight, donut-shaped coil that easily fits around the electrode assembly through-hull fitting on the inside of the hull. The large coil reaches deep into the water column that is passing by the boats hull. Small voltages are introduced into the water by the interaction of the magnetic field and the conductive water. Highly sensitive digital components continuously decode the velocity and directional movement of the water and convert it to vessel speed and leeway. Part of the genius of this methodology lies in how the system samples water outside the turbulent boundary layer and derives a more accurate fore-aft speed reading as well as leeway.
Over three years ago, Marsh focused his attention on developing a two-axis, EM boat speedometer that would be substantially free of boundary-layer effects. In his flow laboratory, which features a 120-foot-long towing tank and a recirculating flow loop, Marsh created a water sled that was attached to a movable tow carriage. The water sled simulated the passage of a boat hull through the stationary water of the tow-carriage basin. On the underside of the water sled and near its leading edge, Marsh placed various screens that altered the boundary layer of the water flowing near the bottom of the sled.
Using a specially developed profiling velocimeter, Marsh measured the velocity profile of each of the various boundary layer conditions. And then, like Thomas Edison, he tested scores of combinations of electrode configurations and electromagnetic coils to determine the best design of an EM boat speedometer. The result was a significant performance increase over prior EM speedometers without sacrificing the ability to fit into existing sensor through-hulls. Marsh also incorporated a novel means of removing the sensing electrodes (for maintenance and cleaning) without the large inflow of water into the boat.
The Brickhouse sensors latest iteration, which is undergoing field-testing, provides the user with direct measurements of both forward speed and leeway speed as well as the calculated value of leeway angle. In addition, a separate pulse signal mimics a standard paddle wheel, like those made by Airmar and other manufacturers. Because most existing marine displays are not currently programmed for displaying leeway speed or leeway angle, the demos that Brickhouse Innovations provides are equipped with a wireless Wi-Fi interface that allows for displaying the data on tablets or various smart phones.
Inside the EM Sensor
The Faraday Law of Electromagnetic Induction states that a conductor, moving in an electromagnetic field, will create a voltage that is proportional to the strength of the magnetic field and to the speed of the conductor through the magnetic field. The best example of the practical use of the Faraday Law is in electrical generators, where a coil of wire (the conductor) spins relative to a stationary magnet and generates a voltage that is used to power machinery or charge batteries.
When the Faraday Law is applied to the measurement of water flow, the voltages generated by the movement of water (the conductor) and the electromagnetic field create very small voltages throughout the magnetically energized water flow. These voltages are detected by electrodes that are in electrical contact with the water. The strength and direction of the magnetic field and the speed and direction of the water motion relative to the magnetic field affect the strength and direction of the generated voltages in the energized water column.
In the case of the boat speedometer, the water is the conductor and the magnetic field is created by a special electromagnet positioned inside the boat adjacent to the inner hull. The motion of the boat relative to the water creates small voltages throughout the water adjacent to hull where the magnetic field exists. Two pairs of electrodes are embedded within a removable sensor and detect these flow-induced voltages, which are subsequently processed into signals that can be used by onboard displays. The two electrode pairs are positioned at right angles to each other, with one pair sensitive only to the fore/aft speed and the other pair sensitive to port/starboard speed. Both the forward speed and the leeward speed are measured, and the leeway angle is easily computed for further integration into the ships systems.
Electromagnetic, velocity-reading instruments do not use a permanent magnet. Instead, an electromagnet driven by a pulsating current is used to create the magnetic field. When moving water flows across this magnetic field, the voltages generated by the Faraday effect are of the same shape and frequency as the pulsating magnetic field. This allows the sensing electronics (attached to the electrodes) to easily detect the flow-generated voltages and differentiate these flow signals from the stray electrical noise present in the water.
In recent years, some marine-equipment manufacturers have designed and marketed boat speedometers advertised as having no moving parts. Several of these designs have used the electromagnetic technique; some were configured for large commercial ships and military craft. These designs usually consisted of a sea valve and a probe-type sensor that protruded out from the hull to better measure the free stream flow away from the effects of the hull. Other designs were configured for recreational boating where protrusions beyond the hull are frowned on. Several of the recreational EM speedometers measured only the fore/aft speed. Only a few measured both the fore/aft as well as the leeway velocities.
Recreational boaters tend to be averse to having things protrude from their boats hull as they might add drag or could be damaged. Because of this, electronics makers have generally limited sensor protrusions to about a half-inch-which is approximately how far a paddle-wheel speedo sticks out from the hull. In attempt to match this status quo, the first-generation of EM sensors electromagnets were too small, and they energized only a small amount of water in the boundary layer. These units measured the boat speed in the disturbed boundary layer very near the hull-typically less than a half-inch away. This small measurement of volume makes it very difficult to calibrate the unit. The speedometer accuracy is non-linear with boat speed, and getting consistently accurate readings under the same conditions is difficult.
In contrast, Brickhouse Innovations EM speedometer utilizes a large, circular coil to energize the water in the vicinity of measurement. This coil, placed on the inside surface of the hull, produces a magnetic field that penetrates the fiberglass/composite hull and into the adjacent water. The volume of water that the Brickhouse system energizes is several hundred times larger than previous EM sensors. Thus, measurements using the patent-pending Brickhouse sensor include velocities taken from adjacent to the outer hull out to more than six inches from the hull (even greater for larger coils).
Status of Field Testing
The first installation of the Brickhouse EM sensor for field-testing was performed at the U.S. Naval Academy (USNA) in Annapolis, Md., in April 2014. As part of a midshipman research project, the academys varsity offshore-sailing team agreed to install an experimental EM speedo on Gallant, a Navy 44-foot sailboat. Gallant normally incorporates two speedos, one on the port side and the other on starboard-approximately one foot from the boats centerline-for accuracy when the boat is heeled. The starboard paddle-wheel speedo was replaced by the experimental EM speedo. The port paddle-wheel-type sensor was left in place.
The experimental sensor comprised a 6-inch-diameter coil placed against the inside of the fiberglass hull and centered on the hull penetrator; an electrode assembly that fits into a standard, 50-millimeter hull penetrator; and an electronics unit that contained the processing electronics. The setup uses a commercial display that shows both forward speed and leeway.
After Brickhouse technicians remedied some minor installation errors, the EM speedo operated without malfunction for all of the sailing season and was onboard Gallant for the Annapolis to Bermuda race. The data remained consistent over the entire trip. Unlike the port-side paddle-wheel sensor, the EM speedo, protected by antifouling paint (except the electrodes), had no fouling problems.
Multiple demo units of the Brickhouse EM sensor will be field-tested this summer. The test boats will include a Navy 44, J/109, Corsair 37 trimaran, and a Cal 40. Practical Sailor will be following this technology as it develops. Stay tuned.
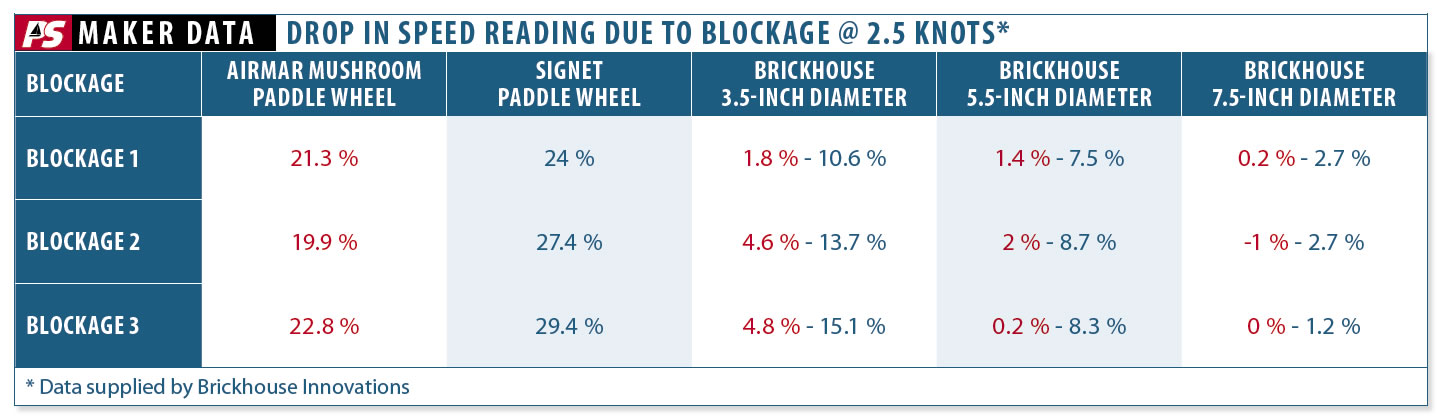
The above data was collected from a series of tests. In one test series, prototype sensors from Brickhouse Innovations were pitted against a paddle-wheel sensor from Airmar (red data). In the other series, the prototype sensors were matched against a paddle wheel sensor from Signet (blue data). Three types of obstructions were used to disrupt water flow around the sensors; the percentage of error was recorded. As the diameter of the prototypes induction coil increased, the accuracy of the reading improved.
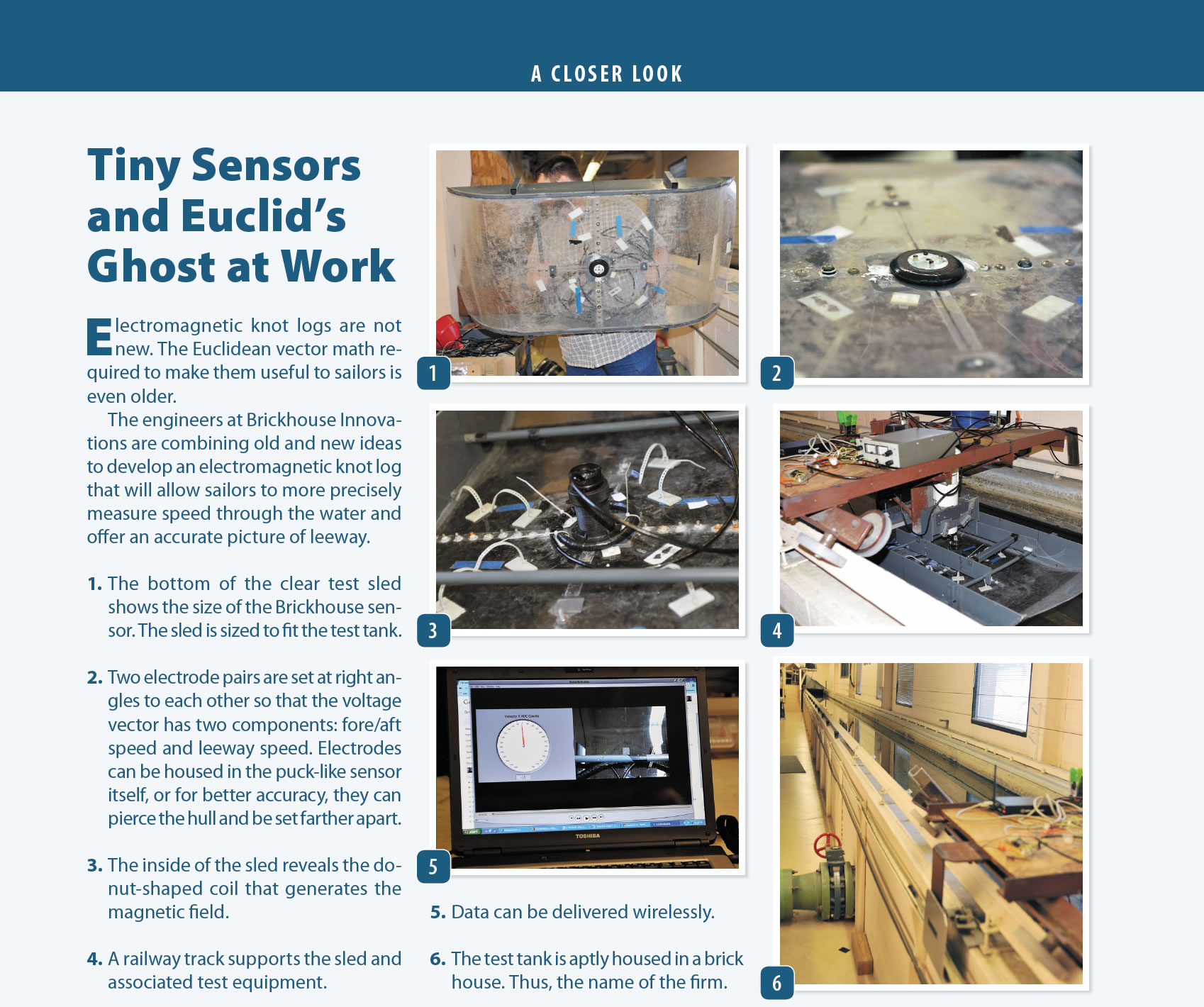
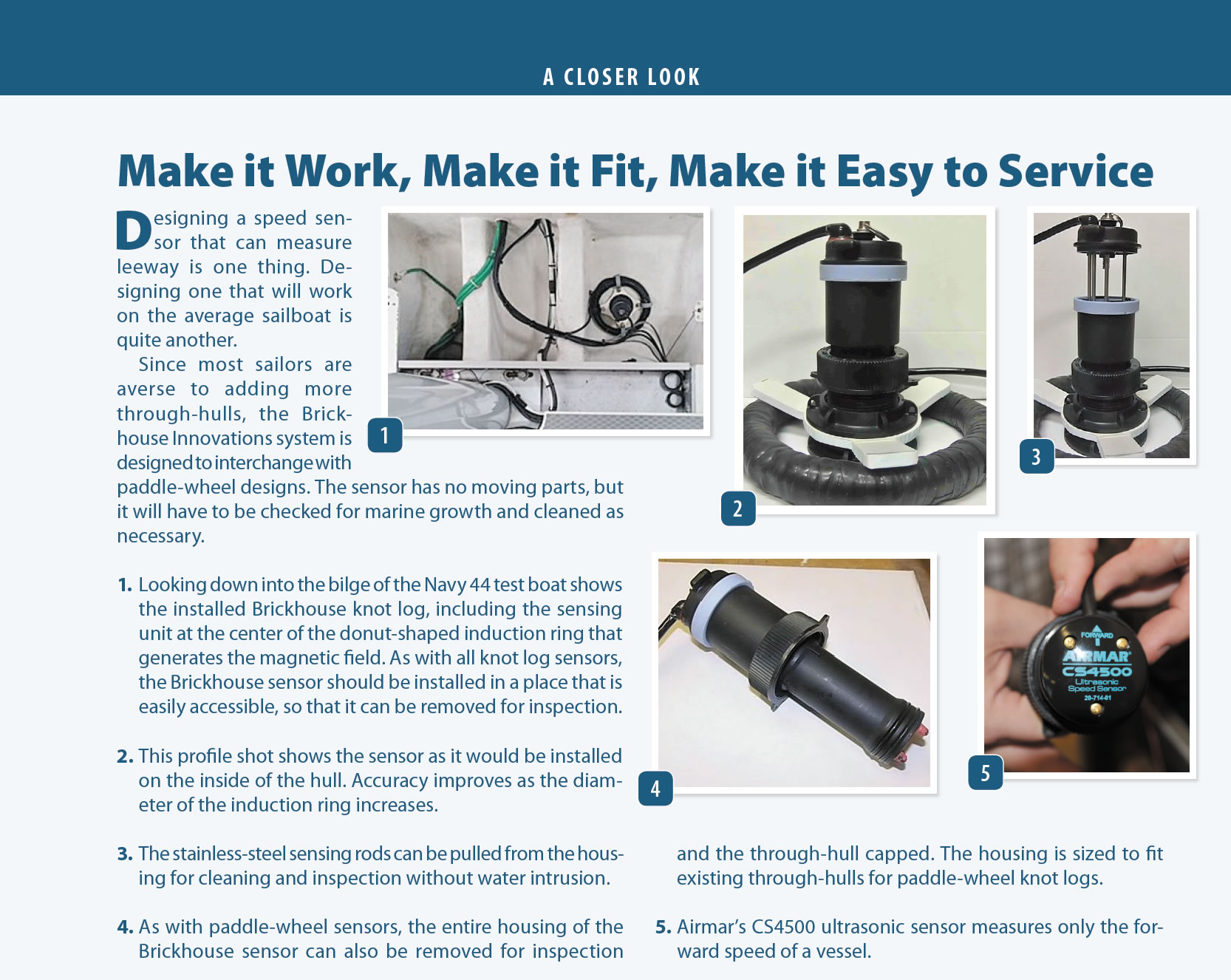
Hi Darrell,
Curious do know whether further tests were conducted and what the results were. I have been trying to get in touch with Larry / Brickhouse… to no avail. Could you help me establish contact please?
Thanks,
JL
Hello, Darrel. I was wondering if any progress to a commercially available version has been made. Looking forward to hearing back from you. Thank you, PA.