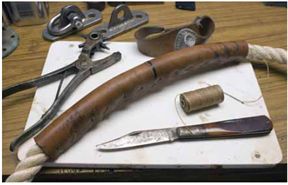
288
Being a team of diehard do-it-yourselfers, we decided to try our own hand at devising a workable solution to defeating line chafe. After fiddling with canvas, old fire hose, and even messing around with some Kevlar, we settled on leather—an old rigger’s standby. It proved to be rugged and remained unholed after a ride on the belt sander. The fabrication process was kids craft 101, and there was something quite seafaring about the result.
Our approach was straight out of the old-salt column. Using a sharp knife and metal straight edge, we lopped off the size patch we needed. Holes were punched opposite each other at ¾-inch intervals, and for temporary use, we zigzagged small cord the length of the leather. For a more permanent installation, we handstitched the leather in place, tucking locking stitches into the rope at each end. Holes were made with a pliers-like hole punch, and we fashioned our chafe strips to be long enough to cover the hard points, adding an additional 25 percent to the length to handle stretch and any minor slippage.
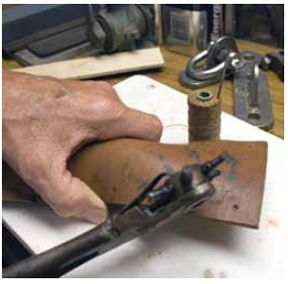
288
Whether laced on for short-term use or stitched more permanently in place, the leather rode smoothly in chocks and prevented the hard edge of an alloy rail from damaging rope fibers. Care needs to be taken to keep the more fragile stitched seam from facing the action and becoming the surface that handles the abrasion. But the same holds true for commercial products the rely on hook-and-loop fabric closures.
All in all, we concluded that if you have the time and enjoy the tradition of handworking a seamanship solution, definitely go find some leather. If you would rather spend the time sailing, purchase one of the tested over-the-counter solutions. But above all, be ready to add anti-chafe gear to your lines when the good weather turns bad; a good outcome is all about staying put.