Standing rigging, stays, and lifelines; these have always been steel cable, terminated with a shackle or ball at one end and a turnbuckle at the other. Steel fittings for steel rigging. For synthetic rigging, lashings seem like the logical replacement. They have a simple ruggedness that we think we understand, and like seems to fit with like.
But walking through the Annapolis Boat Show, we couldn’t help but notice that even amongst the over 50-foot boats, where engineering is advanced and rigging cost is surely a minor cost issue, synthetic rigging is sometimes terminated with low lashings and sometimes with turnbuckles. Why? The reason has to do with differing pre-tension requirements and how rigging is tuned, but we’ll come back to that.
Do we really understand how strong a lashing is? A proper splice is very nearly as strong as the rope, but knots reduce strength by 30-50 percent, the result of sharp bends and uneven distribution of load between fibers. As a lashing winds round and round, sometimes bearing on itself, strength is reduced.
Unlike ball bearing tackles, friction results in uneven sharing of the load between strands. And strength is unavoidably lost at the ends, since lashings begin and end with knots. Are there rules of thumb for how much these imperfections weaken a lashing, and thus how many more passes we must allow?
We’ve been using more and more HMPE on our test boats.
HMPE stands for High Modulus Polyethylene. This material is known for its exceptional strength-to-weight ratio and is commonly used in various applications, particularly in the production of ropes and fibers. HMPE fibers exhibit low elongation, high tear resistance, and are resistant to abrasion, chemicals, moisture, and UV radiation.
HMPE is often recognized under brand names such as Dyneema and Spectra, considered high-performance fibers in the industry. The properties of HMPE make it a suitable alternative to heavier materials like steel ropes. It’s lightweight, flexible, and has a long lifespan while being easier to splice.
Our next re-rig will almost certainly use fiber rigging for all of the standing rigging, other than the forestay (chafe under the furler remains a concern), so its time we learned more about it.
WHAT WE TESTED
We made lashings using both Colligo Terminators and Antal low friction rings. We tested using nylon, polyester, and Dyneema cord.
HOW WE TESTED
Lashings were made up using several variety of starting attachments, including figure-8 stopper knots, bowlines, and splices. The lashings were tied off using Colligo instructions, a string of half hitches around the bundle (four hitches minimum), or half hitches around the last leg only. The polyester and nylon lashings were pulled to failure, and the Dyneema lashings were pulled to their working load limit (the breaking strength of the Dyneema lashings exceeded the capacity of our test stand). All lashings were equalized before tightening the half hitches, something that will not always happen in practice.
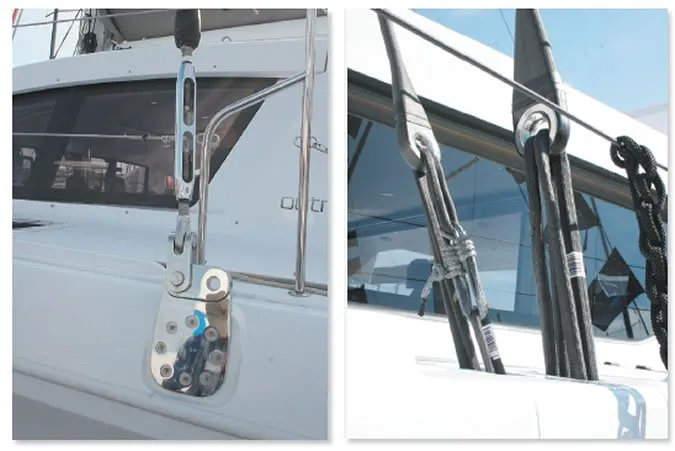
OBSERVATIONS
First, we calculated probable lashing efficiency based on what we have learned about line friction with low-friction rings. When first tensioned, the working end is put under full tension, but every subsequent leg gets 25-35 percent less tension, the result being that half of the lashing is working and the other half is lazy. Even after equalization, when a lashing is pulled to the breaking point, the string of half hitches may slip just a little, recreating those imbalances just when it matters most. Common sense suggests that if the lashing is allowed to become loose and equalize, all of the legs should carry equal strain, but in practice imbalances remain.
TIGHTENING
Let’s say you’ve taken four wraps (8 legs) around a pair of low friction rings. That should be 8:1 purchase, so to get 1000 pounds of pre-load, you should only have to pull 1000/8 = 125 pounds, right? Wrong. Friction around the eyes, reduces the effective purchase to about 3:1. Depending on the line, the rings, and how it is wrapped, you will need to pull over 300 pounds. The line may be damaged by abrasion, and the last leg will carry only 40 pounds of tension. This is a far cry from equal division of labor. In practice, the load will redistribute to some extent, but we measured leg-to-leg discrepancies as high as 3:1. This is also the reason that lashings can never be as efficient as turnbuckles for creating substantial and accurate pretension.
COLLIGO TERMINATORS TEST
If the line is undersized or the wrong stopper knot is used to anchor the beginning of the lashing, it can pull through a deadeye. Colligo has successfully tested a double figure 8 with their terminators to very high load, so stick rigorously to recommended line type and size (see chart).
The stopper knot does not materially lower line strength because friction through the eye reduces the load on the knot. We used bowlines to start the polyester and nylon lashings.
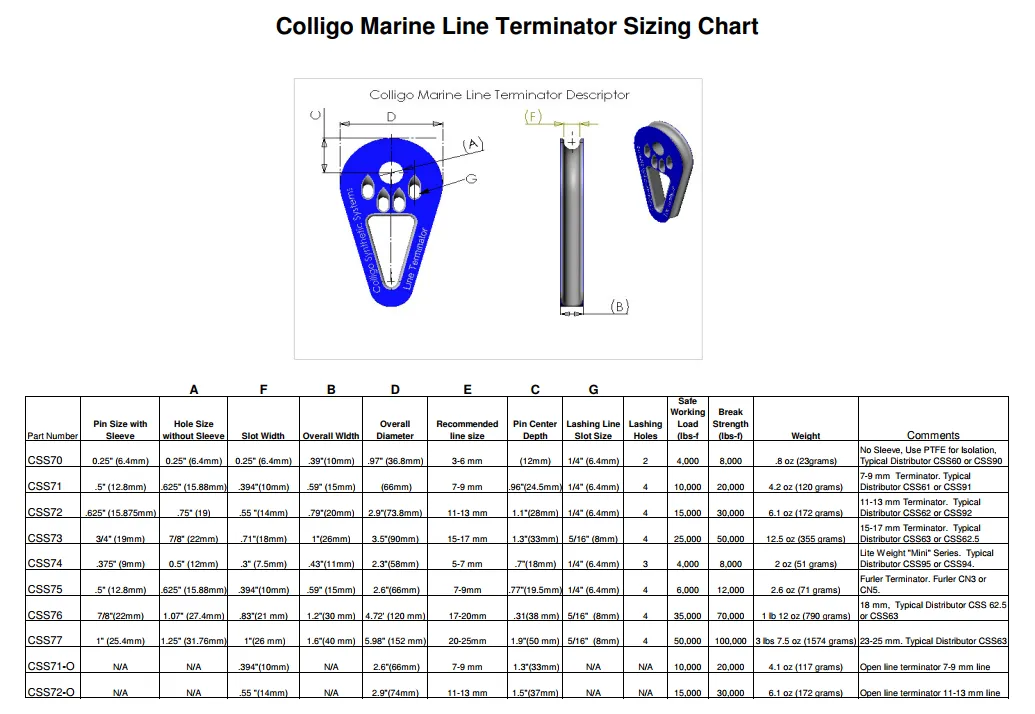
We were not able to break the Dyneema lashings (Colligo CSS 74 Terminator, 4,000 lbs. mean working load, 8,000 lbs. breaking strength) because the strength exceeded our test stand capacity, but there was no evidence of strain at the working load limit. Polyester and nylon lashings broke at about 60- 70-percent of the theoretical value (number of legs times breaking strength). Half of these failed at the bowline and the other half failed in midlashing, suggesting that leg-to-leg tension imbalance, even after equalization, weakens line about as much as a knot, which as a rule of thumb, weakens the line by about 50 percent.
ANTAL LOW-FRICTION RING TEST
For security, use an eyesplice to secure Dyneema to low friction rings. Knots do not hold well, and when they do, they reduce line strength by more than 50 percent.
We used bowlines to secure the polyester and nylon to the low friction rings. We expected lower strength than using the Colligo terminators, but the difference was less than test-to-test variations cause by minor differences in wrapping. The leg-to-leg imbalances were similar and the failure modes were similar.
In both cases, slippage in the lashing termination hitches contributed to imbalances. If the half hitches are snugged down hard, the hitches do not slip. However, as the stress nears the breaking point, the lashing shifts towards the ring or terminator, causing considerable imbalance. Make your tie-off very tight, and seize the end tightly to the last leg.
CENTER TIE-OFF VS. SINGLE STRAND
Fewer imbalances result if the final half hitches are made only around the last strand of the lashing, rather than around the whole lashing. The hitches are less prone to slipping, the legs share the load equally. This is similar to the way wooden deadeyes were tied off on square riggers.
If you tie the hitches around the whole lashing bundle, the lashing is clamped and restricted from equalizing. On the other hand, this clamping turns also slow the unwinding process if the line chafes through. More than a few dinghy sailors have experienced hiking strap lashing failures, and they were glad they had a few seconds to shift their weight inboard. Whether this benefit has merit on standing rigging or jacklines, for example, is debatable. A possible compromise is to either seize or tie off the end to itself, and then proceed to lock off the entire splice with a string of half hitches.
The maximum number of lashings is limited by these same factors, plus several more. Lashing terminals are limited to seven legs by geometric constraints. Low friction ring lashings become progressively less efficient when lines become stacked upon one another, and wear becomes difficult to monitor.
Thinner lines are more vulnerable to cutting, abrasion, and UV. Thus, the lashing should be accomplished with no more than eight legs. If we aim for a 2:1 safety factor, this means the lashing line should be not less than one-half the diameter and one quarter the strength of line that lashing is being used to tension.
A sailor can estimate the extent of tension imbalances using several simple methods. On lines that stretch (nylon, and to a lesser extent, polyester) the diameter shrinks as lines stretch under high load. With long lashings, push each stand with your finger; do they all deflect about the same amount? For high tensioned lashings, pluck them like a guitar string. None should ring dull.
The Colligo terminators offer considerable advantage regarding inspections, both initial and ongoing; the lines are well spaced and you can see everything. Additionally, if tensions are badly imbalanced, the terminator will cock to one side, indicating the imbalance. Low friction rings will have similar imbalances, but they will not be visible.
TIE-OFF METHODS
Colligo recommends starting about one-third of the way up the lashing with what amounts to a rolling hitch. This is followed by a string of at least four half hitches, but more is better. Seize the tail to the last leg. They feel that this location, 1/3 of the way up, helps further tighten the lashing and that it prevents jamming if retensioning is required. For low friction rings, simply pull it tight and run a string of at least six tight half hitches, seizing the tail to the last leg.
CALCULATING LASHING EFFICIENCY
Calculation, Colligo experience, and PS testing all agree that an efficiency factor of about 1.4:1 is required to make up for inefficiencies and resist wear. For example, Colligo specifies a 5 mm Amsteel Blue lashing (7 x 5,400 pounds = 38,800 pounds) for required for 9 mm Dux shrouds (26,800 pounds), or a 1.4:1 safety factor. We like a 2:1 safety factor for low-friction rings, to make up for inspection difficulty.
CONCLUSIONS
For lighter duty lashings, we like low friction rings. They are far easier on the line than thimbles, efficient, light, inexpensive, and easy to work with. The downside is that they are difficult to inspect for tension imbalances and internal wear, and more difficult to adjust if slack needs to be taken up. We like the Colligo Terminators for standing rigging, largely because we can see everything and inspect them.
Remember your safety factors. For Colligo products, stay with the factory recommendations; the designs include conservative, well-proven safety factors.
With low friction rings, we think a 2:1 safety factor, on top of the safety factor applied to the line is prudent. It’s impossible to see what is happening on the inside. Lashings should contain no more than 8 legs and the lashing line should be not less than the strength of the main line it connects.
Dyneema vs. Polyester. After multiple pulls, we concluded that the required safety factors are the same. Although the lower friction of Dyneema should result in less imbalance, the greater stretch of polyester compensates.
Why would you use polyester instead of the stronger Dyneema? You may not need incredible strength; an 8-leg lashing of 3/16-inch polyester is rated at (8 x 1200)/3 = 3200 pounds breaking strength, enough for many applications.
The higher friction also means fewer half hitches are required to secure it. That said, Dyneema is more UV and abrasion resistant, and World Sailing specifies Dyneema lashings for lifelines.
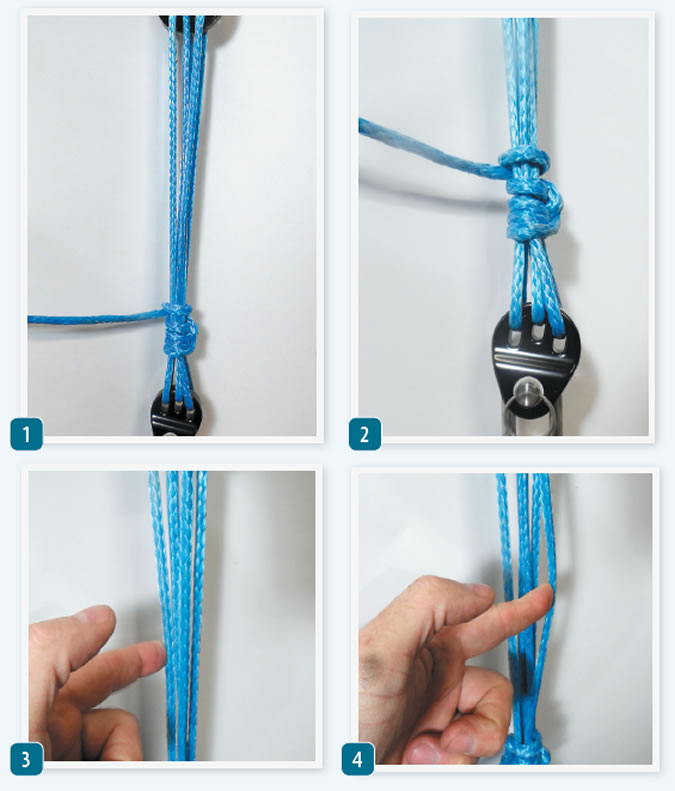
Fewer imbalances result if the final half hitches are made only around the last strand of the lashing, rather than around the whole lashing. The hitches are less prone to slipping, the legs share the load equally. This is similar to how wooden deadeyes were tied off on square riggers.
- Bundling all of the lashes around all of the lines through the dead-eye restrict movement and results in imbalanced loads.
- This aluminum deadeye terminal is cocked sideways because of uneven loading. The last leg has actually slipped some.
- A simple tension test reveals one leg is extremely hard to push in.
- The opposite leg on the same setup as image #3 is loose and easy to deflect in the same simple tension test.
The Colligo Terminators have considerable advantage regarding inspections, both initial and ongoing; the lines are well spaced and you can see everything. Additionally, the terminator will cock to one side, indicating an imbalance. Low friction rings will have similar imbalances, but they will not be so clearly visible for inspection.
- This low friction ring is strained up to its working load. Note the middle strand is squeezed and compressed, while the other two are not.
- An imbalanced load cocks this deadeye. Notice the smaller diameter of the highly loaded line on the right .
- Lashings in low friction rings are most efficient if they are not stacked on top of eachother. Dont scrimp on ring size.
This piece was originally published on May 23, 2019 and has been updated.
At least for me, as I read the last section, it appears that the associated photos are missing for the box titled “Colligo Terminators Versus Low Friction Rings”.
Please rerun this article with photos of the Colligo Terminators. If space is an issue, drop Darrell Nicholson’s bio. It’s long and overused.
Agree the above two comments… as I’m debating a change to Colligo Terminators and want to know what YOU know.
Interesting…put in DrewFrey’s bio for Nicholson’s but still no pictures! So, someone is doing something, just not what we are looking for! (Truly looking for the information though it sounds like I’m busting chops…)
Frye not Frey…sorry!
First picture shows a frapped tensioning setup with one line not included in the frapping. That is intentional, not unbalanced. The last wrap is the bitter end used for attaching to the tightening winch and cannot be included in the frapping. The editor had a basic misunderstanding of the process of tightening and securing.
I think we understand. The point of picture 1 was to illustrate that the last (tensioning) pass cannot be counted towards the total. Obvious and agreed. Additionally, other pull testing suggest that other far lesser imbalances remain within the frapped bundle; the lashings always failed below the theoretical limit, and always in the last pass, which carries the highest tension. Just as the load side and tail side of a winch will never carry the same tension, even if locked in a cam cleat, even if the sail flogs, the individual passes in a frapped lashing always retain some imbalance. If they did not, then the last (not frapped) pass would eventually also reach full tension, frapping or not, which we can see it does not.
Although there are many variations in imbalance, depending on how tension was applied and the history of how the frapping was applied (have there been unloaded cycles?), there will always be some imbalances. This is why an additional safety factor of 40-100% is required with lashings (less with Colligo terminators, more with low friction rings) . Additionally, since thin lines are more vulnerable to UV and chafe than larger lines, additional safety factor may be desired.
I have Dux shrouds on my 1988 Catana 40. Colligo made, with their terminals and turnbuckles.
I always tension my rig on the lee side to take all the slack out of it, consequently the tension at that moment is a lot less than the tension applied at the dock.
Two points:
A lashing tensioned on the lee side in this way would be equalised very quickly by the reduced tension and friction on setup, as well as the varying load during sailing..
The Dux is chosen not for its working load capacity, but for its creep characteristics under the working load ….. and hence the lashings too. This would imply that the lashing nor the shroud ever get close to your slipping load in practice.
No, I’m sorry but in many or most case the lashing does not equalize during sailing anymore than the load on the tail of a winch line secured in a self tailor or on a cleat slowly increases. They don’t. Isn’t that odd. This is counter intuitive, I know, but no, they do not usually equalize. That was the point of the article.
The first image in the article was from a boat that had sailed tens of thousands of miles. The owner vehemently argued that I had employed a trick to take the picture, but in fact, the first pass never tightened. I was not even straining. The tension was applied to the shroud with a separate tackle and the lashing drawn up by hand. This is the usual way, since a lashing is very difficult to draw up tight enough.
Thanks for this analysis. I recently replaced my lifelines using eye splice thimbles in 5mm Amsteel Blue and 1/8” Dynema lashings at 6:1. The lashing thickness and reduction was a guess based on available space on the thimble.
Interested in replacing my 38 yr-old rod rigging with synthetic. Would love to see an addendum or accompanying article on mast and spreader fittings.
5 mm is about 2.8 times as strong as 3 mm (1/8-inch), so even with the efficiency loss, you are right there. This is the normal way. Good job!
There are a few challenges with mast fittings. First, it is VERY difficult to draw them up tight enough. Riggers typically use a turnbuckle or other tackle to create the pretension. The lashing just holds it. Second is the problem of creep (Dyneema gets longer under load). This is reduced by using pre-stretched Dyneema and by going oversized. Another thing is that all of the lines need to stretch in proportion, or wind the wind comes up, the mast won’t stay straight (in column). Dyneema is not used for diamond wires because of stretch. And then there is a the matter of fittings and chafe. We suggest contacting Collego. It’s doable, but it is not a one-for-one drop in replacement.
Note on lashings for low load applications and application where the load is zero to start (for example, if a lashing is used to replace a short dogbone with eyes in both ends). The tension will equalize in this case, because friction is not holding the rope.
Often a lashing or loop makes more sense than trying to splice a very short dogbone. Instead, splice a loop 2or 4 times longer than need, secure the ends, and add chafe gear as needed. The center can be seize of covered if desired.