Long ago, aboard sailing ships trapped in the doldrums, the crew rigged long, vertical poles to support awnings. The awnings were needed to keep the decks from opening up and to prevent living things—man and beast—from dying in the heat.
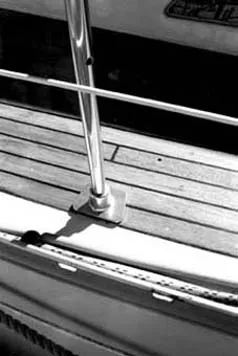
The poles became pipes, they got shorter and soon they were called “bulwark stanchions.”
And that’s how, as bulwarks extending above the weather deck shrank, lifelines came into being. Bulwarks, once needed to keep deck-loaded cargo from going over the side, added to the cost of construction; they also added a lot of windage and could scoop up tons of water.
Stanchions, threaded with strong, low-windage rope or wire lifelines, became slim and trim.
On modern ships and yachts, the lifelines the stanchions support are intended to keep the crew from going overboard. To be really effective, the lifelines should be taller than generally seen. Waist high should be the minimum. How the boat looks shouldn’t be an issue, but it is.
The lifelines and the supporting stanchions and bases must be strong enough to withstand a lurching fall by a large crew member.
Standards for stanchions and lifelines are meager. The Offshore Racing Council says the lifelines should be 18″ high on boats no more than 28′ LOA, 24″ on larger boats with both mounted on through-bolted, bonded or welded stanchions no more than 7′ apart. The Cruising Club of America’s Fastnet-inspired publication, Desirable and Undesirable Characteristics of Offshore Yachts, states only that stanchions be of stainless steel and through-bolted. A recent study sponsored by the United States Naval Academy and the United States Sailing Association suggested that plastic-coated lifeline wire should be replaced with bare wire and that, because pulpits and pushpits are weak attachment points for lifelines, their bases should be equipped with supporting struts.
For this Practical Sailor test, almost two dozen stanchions and close to three dozen bases were collected. The samples do not include all available lengths of stanchions and angled bases.
They all were examined closely for design, material, finish and workmanship. Extra scrutiny was given to fabricated items—those that are welded or made up of several pieces of stainless plate, tubing and rod.
Cast vs. Welded Bases
For those who prefer one-piece construction, the penalty for the solid bronze or stainless castings usually is weight.
For instance, a Vetus base in this test, which is made up of a piece of stainless plate bent to shape and to which is welded a piece of stainless tubing, weighs 8.5 ounces. That light weight was the goal clearly is indicated by a hole punched out to eliminate excess material. When combined with a Vetus tapered stanchion, the pair weigh 1 pound, 11 ounces.
By contrast, a cast stainless steel Spartan base weighs twice as much—18 ounces. Combine that Spartan base with the strongest Tops-In-Quality stanchion (the model reinforced with a fiberglass rod) and the weight soars to just over 3 pounds.
Multiply the weight differences in these combinations by the stanchions needed on most boats and the added weight can get significant…especially to a sailboat that is raced. The choice between fabricated and cast bases should be made by a boat owner; unfortunately, the selection usually is made by the boatbuilder, who too often goes not only for the lightest but also the cheapest.
As with any safety equipment, the primary objective is to have a lifeline system that will save a life. (But because of inherent weaknesses, oneshould never clip a safety harness to lifelines.) That means strength.
In the case of lifelines, it’s likely that when someone falls it will be more likely against the lifelines than against a single stanchion. Some say it’s better to have stanchions bend (to provide some cushion). It seems preferable, in our view, that the stanchions withstand the force.
How much force?
Practical Sailor has struggled with various ways to figure out how much force a grown adult might exert while falling hard. Various drop tests have been considered and rejected as not realistic. However, that does not preclude testing to establish which items in a group are the strongest. Tests that indicate in what manner failure presents itself also can help buyers match their preferences to the products they buy.
Bases sell for about $32-$45.
Design and Quality
Before testing was undertaken, the stanchions and bases were closely examined.
For the stanchions, the chart (click here to view) shows evaluations of finish, welding, aesthetics, weight, length and price.
Stanchions made of stainless tubing are manufactured from a flat strip. The ribbon is fed into an automatic machine that forms a tube and welds the seam. Because welds are prone to corrosion, the quality of the weld is important. So is the finish…the polishing of the stainless.
The top details may be a matter of appearance. The castellated tip, shaped like the battlements on the corners of a castle, surely ranks as the second best looking (next to the one-piece aluminum Goiot). As with the pipe tip and ring tip on two of the Tops-In-Quality stanchions, the castellated top is a separate piece that must be welded in place. That increases the possibility of corrosion.
One other consideration of stanchion tips involves comfort and safety. The small tips on tapered stanchions may be sleek and handsome, but the blunt tops on the Schaefer and two of the Tops-In-Quality models, all three on untapered tubing, would be a bit nicer to grab and somewhat safer if one fell on them. Tapered for good looks and with fairly large tips, the Goiot and Matella are good compromises.
Whatever the design, the hole for the lifeline must be smooth to avoid chafing either the plastic cover used on most lifelines or a bare wire lifeline. Because the plastic cover encourages corrosion, bare wire is preferable…except in an anodized aluminum stanchion where the stainless wire would quickly wear away the anodizing.
The mid-hole for the lower lifeline also must be smooth.
It should be noted that, although they may be sold as stanchion bases, some of these bases really are meant for powerboat railings. Included are models from Attwood, Buck Algonquin and Suncor. Others can be found in some discount marine stores. With fewer mounting holes, less material or with a low profile, these “railing bases” seem to satisfy powerboat owners, but should not be used on a sailboat.
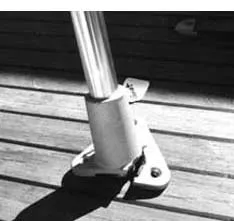
Sailboat bases should have a drain hole, because they collect water and debris. The result: Corrosion, which is unsightly but, more importantly, can lead to failure, especially of fabricated bases.
It’s important, too, how the stanchion is secured in the base. It’s not uncommon for someone hoping to avoid a fall to pull up on a lifeline, only to have the stanchion lift out of the base.
The poorest bases have one tiny set screw. Those with two set screws are twice as good as “very poor.”
A requirement, in our opinion, is a bolt, threaded into at least one side of the stanchion and base, but better if run all the way through and secured with an acorn nut, seated in Loc-tite, on the other side. If such bolts hold the stanchion up off the bottom of the base socket, they rarely rattle. Not one of these bases is so equipped, but some easily can be drilled and fitted with a proper through-bolt.
Several years ago we had Tops-In-Quality make up a number of bases for our Tartan test boat and they were quite happy to drill drain and through-bolt holes. We think this is an improvement well worth the modest price increase.
As one manufacturer put it, “Basically, stanchion bases should be inviolate.” They must not break or bend. They also must be powerfully mounted. If not, a failure probably will do some deck damage, which might be dangerous if at sea and expensive to fix anywhere.
Unless it’s light weight you desire, cast bronze and stainless bases are far better than fabricated bases. Fabricated bases always involve the ever-suspect welding and it takes little pressure to distort the fabricated bases, even those with reinforcing struts. When a base bends, it always pulls the mounting holes closer together and squeezes the deck unmercifully. The result: wobbly bases, deck cracks and leaks.
First Phase Testing
For the first phase of the testing, fabricated bases were tested with a strong aluminum stanchion…in this case the 1″ OD Matella.
A piece of Sta-Set line was shackled to the hole in the tip of the stanchion and led to a Harken winch mounted on the other end of the long workbench. Interposed in the line was a Dillon dynamometer. It took a pad eye and a block to produce a proper angle for the line to meet the winch. The pull on the stanchion was at about a 20° downward angle…about right for someone falling against the stanchion or lifeline from the opposite side.
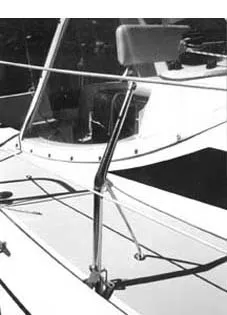
The pull, applied by the Harken #32 two-speed, self-tailing winch and registered on a dynamometer, was increased until damage could be seen.
The failure usually presented itself in the form of a bend in the base plate on the backside. When the bend was well-developed and permanent, the pull and angle were recorded.
Second Phase Testing
The second phase of the test involved stanchions. All except the big Matella and the metric Goiot are 1″ OD.
The wall thickness of the stainless steel tube stanchions is about .060″. However, because this was a simple strength test, any differences in the wall thickness are moot.
Further, although it is obvious that shorter stanchions would show up better in the testing, no allowance was made for length after it appeared that it wouldn’t make any difference in the final recommendations.
The Spartan plain bronze base ($40) was used for all but the Matella stanchion (which has its own base).
The pull was applied in the same manner as for the bases. With two exceptions, the stainless tubing stanchions all failed in the same manner. One exception was the braced Signet stanchion; it failed where the brace was welded to the main body of the stanchion. The other exception was the 30″ Ronstan; it has holes for three lifelines and bent at both the bottom hole and at the point where the tube entered the base.
Although it might be thought that a stanchion would bend at the mid-hole or, if tapered, near the top, all but the exceptions noted above failed at the compression point where the stanchion emerges from the base. (Tapering is a relatively inexpensive procedure costing a dollar or two.)
It starts with a slight depression and very quickly becomes a deep kink, at which point the integrity of the stanchion disappears.
The aluminum stanchions are different. Firstly, they have more flexibility, meaning that they recover from fairly severe bending. More importantly, they are very strong and retain most of their strength, even when bent severely.
The Bottom Line
Because the base should be of unquestioned strength, cast bases (bronze or stainless, but not aluminum) are so superior to fabricated bases that only cast bases are worthy of recommendation. It’s tempting to qualify that statement by saying that fabricated bases might be used if light weight was very desirable; however, making exceptions in safety equipment can lead to regrets.
Of the cast bases in this sampling, those sold by Spartan—especially the bronze model with the excellent drain hole—provided the greatest confidence. The large stainless model from Suncor also appears more than adequate to very heavy usage.
For stanchions, other than the Tops-In-Quality stainless version stiffened with a thick fiberglass rod, none of the hollow stainless tubes are equal to the two solid aluminum stanchions from Goiot and Matella.
The stainless tube stanchions all failed at from 120 to 200 pounds, which, in that emergency setting when someone is thrown hard against the lifelines, is not nearly as good as the reinforced Top-In-Quality, the Goiot or Matella.
The Goiot stanchion is a metric size, which makes it not usable (without some work) with a non-metric base. And the cast aluminum Goiot base fractured at 195 pounds.
That leaves as Practical Sailor’s top choice the new Matella.
Machined of solid 6061 aluminum, assembled with a 7075 aluminum machine screw, the heavily anodized stanchions come with backing plates and 5/8″ nuts. The base even has two O-rings, which makes caulking unnecessary. The Matella stanchions are available in three lengths—26″, 28″ and 30″ and Practical Sailor recommends the longest. They’re even available in colors—bronze, red, green, blue and any other on special order. They fit deck thicknesses from 3/8″ to 1-3/8″.
Two negatives about the Matella: (1) if one is damaged, perhaps by snagging an overhanging dock, the entire unit must be removed for straightening or replacement, which would be more difficult and more expensive than just replacing a bent stanchion; and (2) it is heavy, as mentioned earlier.
On the plus side is the price. A 30″ stanchion, complete, costs $85. By contrast, a chromed bronze Spartan base ($54.65) and the rodded Tops-In-Quality stanchion ($57.90) together cost $112.55 and you must supply your own backing plate and fasteners.
Contacts- Garhauer, 1082 W. Ninth St., Upland, CA 91786, 909/985-9993, www.garhauermarine.com. Goiot, Welmax Marine USA, 220 Lock Rd., Deerfield Beach, FL 33442-1516, e-mail Welmax@aol.com. Matella, Box 2849, Big Bear City, CA 92314, 909/584-0168, www.matella.com. Ronstan, 7600 Bryan Dairy Rd., Largo, FL 33777, 727/545-1911, www.ronstan.com. Schaefer, 158 Duchaine, New Bedford, MA 508/995-9511, www.schaefermarine.com. Signet, 505 Van Ness, Torrance, CA 90501, 310/320-4349, www.signetmarine.com. Spartan, Georgetown, ME 04548, 207/371-2542, www.robinhoodyachts.com. Tops-In-Quality, 314 E. Huron Blvd., Marysville, MI 48040, 810/364-7150, fax 810/364-7925, www.topsinquality.com. Vetus, Vetus Den Ouden, Box 8712, Baltimore, MD 21240, 410/712-0740, www.vetus.com. White Water Inc., White Water Marine Hardware, 13663 46th St. North., Clearwater, FL 33762, 800/572-8871, e-mail WhiteWaterMarine@msn.com.