The Knot really isn’t something that should make rope run screaming from the deck. The knot is something we’re used to. It’s a good thing.
Most experienced sailors know that any rope, when knotted or even rove over a bend (like a sheave in a block), undergoes some stress that detracts from the strength that its maker claims.
The part most likely to come close to the rated breaking strength is the straight, middle of the rope. Unless abraded in some unusual fashion, rope almost never breaks there. What fails are the secured ends.
A generalization on which you can rely almost universally is that the strongest end treatment on any rope is a splice. A neatly done splice, with a properly sized thimble, cuts the breaking strength of a line only about 10%. However, when knotted, the deterioration in a rope’s breaking strength is much more severe. (Proper terminology calls for distinguishing between knots, bends, and hitches; but in this report all will usually be called knots.)
Although you’ll see minor variations listed here and there, the figures for the percentage of retained strength for commonly used knots are said by the Cordage Institute to be: bowline, 67-75%; square knot, 43-47%; fisherman’s knot, 50-58%; sheet bend, 48-58%; Carrick bend, 55-60%; two half hitches (on a 5/8″ ring) 60-70%, and (on a 4″ diameter post) 65-75%; and an anchor bend (on a 5/8″ ring) 55-65% and (on a 4″ diameter post) 80-90%.
It gets more complicated. The Cordage Institute figures are for new rope and straight, static (slowly applied) loads rather than dynamic loads—what you might call shock loads. Further, in the market scan article on page 6 there are several references both to the difficulty of splicing modern synthetic rope and about the danger of using time-honored knots to belay these slippery lines.
Another warning came from Brion Toss, one of the world’s most respected riggers, in an article in a recent Sail magazine. Toss threw up a large red rocket about knotting any rope made of what he called “HM fibers,” meaning high-modulus fibers.
Speaking of the great all-purpose bowline, Toss said that its strength isn’t reduced by a mere 30% in high-modulus line, but more like “60, 70 or 80 percent.” As an example, he said a piece of 3/8″ line made of Spectra, with a breaking strength of about 8,500 pounds, would, when formed into a bowline, have a breaking strength of but 2,000 to 2,500 pounds. He said that with some HM line subjected to heavy loads near their breaking strength, the core would snake out of a bowline. That’s downright alarming.
His observations (including “…there simply is no way to tie a knot in an appropriately-sized HM line and still have any factor of safety…”) sent a lot eyebrows skyward around here.
Toss suggested that sailors go back to splicing or, if they wish to tie knots in high-tech line, they accept that the line must be “massively oversized, in which case it is far bigger, heavier, and more expensive than necessary; or it is the right size and probably on the edge of breaking.”
For those of us who have, for a handful of years now, been knotting, hitching and bending line like Yale’s MaxiBraid, New England Ropes’ T-900, and Samson’s Ultra-Tech, this was a piercing call for for a Practical Sailor bench test.
The Planning
The goal, really, was to see for ourselves just how much knots really do rob high-tech lines of their breaking strength.
Practical Sailor in years past has been given the use of pull-test equipment at both Tillotson-Pearson (the boatbuilder in Warren, Rhode Island) and at New England Ropes (www.neropes.com, now in Fall River, Massachusetts.) This time, Practical Sailor engaged the facilities of Aramid Rigging (www.aramidrigging.com) in Portsmouth, Rhode Island. The company, owned by Alex Wadson, does all kinds of rigging—from conventional to very high-tech approaches for large yachts and racing boats. As implied by the company name, Wadson and his crew know much about the advantages and limitations of man-made fibers.
After extensive discussions, it was decided to use line of four different categories.
To serve as a sort of base, we chose New England Ropes’ Sta-Set, a double-braid (Dacron cover and Dacron core) that is very popular with sailors. It was expected that our various end treatments (knots) would fare best with this “traditional” line.
As a example of moderately high-tech line, the choice was Yale’s Aracom-T, which has a Technora core and a Dacron cover. If there were problems with knots, it might be with line of this type. (As a rope component, Technora, which is similar to Kevlar, is fading and being superceded by Spectra and other even more technical and forgiving fibers.)
Moving up the line, the next choice was another popular line, Yale’s Maxi-Braid Plus. It has a braided Spectra core and a smooth Dacron cover.
For a very exotic line, Yale Light was chosen; it has a composite polyethylene-Spectra core and a cover of braided polyethylene. It seemed most likely that Yale Light would be trouble.
Finally, to test a specific splice recommended by Brian Toss, a piece of Samson’s most expensive line was chosen. It is Spectron 12 Plus, a 12-strand single braid made of coated Spectra.
It must be emphatically noted that this was not a test of one company’s line against another. New England Ropes, Yale, and Samson (and other companies, too) all market line that would fit in each of the three categories.
The size of the lines, six in each category, 18 in all, seemed not very important. The sizes were chosen for approximately equal breaking strength—with no consideration for cost. The 7/16″ Sta-Set (89¢ a foot) has a listed break strength of 6,600 pounds. Yale rates its 5/16″ Aracom T ($1.44 a foot) at 9,700 pounds. Yale’s 5/16” Maxi-Braid Plus ($1.70) has a break strength of 5,700 pounds. The 3/8″ Yale Light ($1.26 a foot), the largest size made, is rated at 5,000 pounds. Samson’s 1/4″ Spectron 12 Plus has a break strength of 9,200 pounds.
Next, it was decided to pull test most of these lines with five kinds of terminations. They are a bowline with a double turn, an anchor bend, a clove hitch with one half hitch, a constrictor knot (also known as an Ashley’s hitch, and said by Brion Toss to be the best of the knots), a plain eye splice, and, for the one piece of single braid, a Wadson adaptation of the multiple Brummel splice (which Toss said was developed by Margie MacDonald, a rigger in his Port Townsend, Washington, shop).
With one exception, one end of each of these pieces of line had conventional splices, as specified by each line’s manufacturer. And in some cases, some extra line samples were pulled to destruction with knots in both ends.
The Test Equipment
Working with a very patient Brian Fisher, Wadson’s production manager, the game plan called for mounting each piece of line in Aramid Rigging’s giant stretching machine, which runs 88 feet, from the front to the rear of the shop.
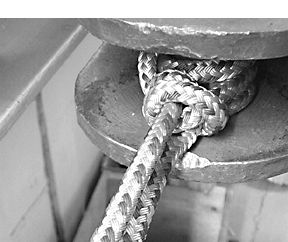
Basically, the machine is two 5″ I-beams, with trolley cars (secured by huge pins) and a pneumatic ram mechanism in the box-shaped space created by the beams. It applies the load very gradually.
The assorted rope spices and knots were tied over or slipped on smooth 2″ pins, to minimize the damage done by severe bending. (Our first couple of tests used a section of 3″ steel pipe around the shackle pin, but this quickly deformed and we discarded it.) No thimbles were used on the splices, because it was the knots that were expected to fail.
Everything in this linear line-up is firmly anchored. Along with intermittent snaps, cracks, and groans as knots and splices draw tight, the testing gets noisy (like rifle shots) when a good piece of line lets go.
Coupled to a computer read-out, the machine permits on-the-spot observation and also records data about properties like strength, elongation, creep, snap-back, hysteresis failure, extensibility, residual strength, and whether Michelle Pfeiffer is more beautiful than Deborah Kerr.
So, besides being observed visually, each of the pull-to-destruction segments produced a graph paper chart clearly showing at what poundage the breakage occurred—as well as a broken piece of rope to examine and photograph.
The Test Results
The data, shown in the chart, does not fall in patterns as neat as one might prefer. Practical Sailor suggests a careful look at both the chart and the boxed-off information entitled “Added Thoughts.”
The test figures certainly support the position of Brian Toss, which is that these HM lines lose a great deal of their strength when knotted.
The figures don’t do much to lend credence to his position that the Brummel splice solves the problems. The Brummel splice is a difficult splice, not known to many sailors and not even shown in most books on ropework. In addition, it is used mostly for single braid of the type used primarily by racing zealots or by removing the cover of a double braid and making the spice in the core. (On double-braid with, for instance, a Spectra core and a Dacron cover, the core has all of the strength.)
The test data shows which knots are best and that splices are better than any knot—except that in very slippery line (like Yale Light) splices tend to pull out.
So, it’s tempting to shout, “Don’t tie knots in exotic line!” However, that would be both an exaggeration and over-simplification.
If you like generalities, here are several: The more expensive the rope, the more strength is lost when knotted, and the more likely a knot can be expected to slip.
Mind you, all of this fancy rope is freely recommended, by the makers and in marine catalogs, for use in situations where knots are commonly used by most sailors. These include halyards; main, jib and spinnaker sheets; vangs; topping lifts; guys, and travelers. They’re often called “ideal” for winches and stoppers.
If you use these ultra-strong (and ultra-expensive) varieties of line for such purposes, there’s a way out of the dilemma that is created: It’ll take you to a black hole—the one in the most remote reaches of your wallet.
The Bitter End
It’s fine to say that all rope terminations should be splices.
Amateurs who do their own marlinespike work learned with the introduction several decades ago of three-strand nylon that a couple of extra tucks were called for—to counter nylon’s slipperiness.

The appearance of Dacron double-braid called for even more skill—and usually a diagram to keep track of the fid-length markings and the points at which the cover goes in the core and the core goes in the cover. At first, it all seemed very mysterious, but plenty of dedicated sailors set themselves to the task and overcame the problems.
But the times, they keep changing, and the question is, how long can the amateur be expected to keep up? How many sailors will be able or willing to take the next step and fit splices in the fancy line now available? Splicing the HMs can be very difficult, even for a professional rigger in his shop.
The sailor faced with the occasional need to attach a shackle to a halyard or attach a pair of sheets to a self-tailing jib, can stop by the rigger’s shop and pay to get it done. The rigger will even select the proper line—subtracting from its rated strength the weakness (which he should know) induced by the splice.
An alternative is to buy oversized line and tie knots in it. Although severely weakened even by knots like the bowline, over-sizing will take care of the problem. With this approach, the already-high cost could double.
As Brian Toss observed, you wind up with line that is “far bigger, heavier, and more expensive than necessary.” And you still have slipperiness to worry about.
The last alternative: Unless you are a fierce racer and intend to banish at any cost any excuse for losing, equip the entire boat (except for that nylon anchor rode) with any of the excellent varieties of Dacron double-braid.
Conclusions and Observations
• In virtually all cases when a knot held, the rope broke at the very front of the knot, at the first turn compressed by an overlay. If you have an important connection made with a knot of any kind, re-tie it occasionally in a slightly different place.
• Although rigger Brian Toss said he has seen the core crawl clean out of the cover of a line subjected to heavy loads, the PS tests turned up no similar instance.
• The only test made of the Brummel splice was on a piece of Samson’s Spectron 12 Plus. It’s an all-Spectra single braid with a rated breaking strength of 9,200 pounds. With splices in both ends, it broke at 7,078 pounds—77% of its rating.
• In defining a rope’s strength, manufacturers and catalogs currently tend to use “breaking strength” instead of “safe working load,” as they used to do. Breaking strength defines the load that produces a break or rupture. Long before a rope breaks, it undergoes severe and permanent damage. A better term from the user’s viewpoint is “safe working load” or simply “working load limit,” which is the load that can be endured repeatedly without doing damage. Unfortunately, the preferable term gets so complicated by things like “design factors,” dynamic loading, age, wear, UV attack, etc., that manufacturers no longer routinely specific the SWL.
• In the slippery lines (especially Yale Light), the splice occasionally pulled out before the knot broke. The splices failed when the cover broke, which released the splice enough to free the core.
• When synthetic line undergoes heavy stress, it heats up—sometimes dramatically—and creates a small welded mass of plastic. You can perhaps tell if a knot is getting near its breaking point by feeling it.
• The double turns over the pin used on the bowlines were useless, as they probably would be with any knot. Unless there is abrasion, the turn is not where the break occurs.
• Unless it’s used on a surface with some friction, like a rough piling or mooring bitt, the clove hitch shouldn’t be considered a reliable knot, even with an added half hitch. The figures on the chart are for this configuration. Early in the testing, PS took to adding a buntline hitch to get it to hold. That made it a different ballgame. The lines so secured then broke (at fairly respectable loads) at the buntline hitch.
• The most unusual result was with a piece of Yale’s Maxi-Braid Plus. With splices in both ends, the line broke the core (but not the cover) in the middle of the piece. Rated at 5,700 pounds, the break came with a load of 9,030 pounds. Why, we do not know.
• When using slippery line, it’s strange and unpleasant to watch a well-made knot like an anchor bend slowly but surely snake its way free when a load is applied.
• Practical Sailor’s seat-of-the-pants reaction to all of these readouts is simple: High-modulus fiber already has an accepted place in the standing rigging of high-performance boats, where all terminations are professionally made. It can and most likely will have a place in shackle-ended running rigging (mainsail and headsail halyards, topping lifts, maybe heavy-air spinnaker sheets) aboard a lot of weekend handicap racers, where 20 pounds of weight saved aloft can add several seconds per mile on the course. It can make a difference in the same way to performance-minded cruising sailors. But until the ropemakers figure out a way for this stuff to face up to The Knot without sacrificing The Wallet, it’s just can’t be a trusted mate on deck. Brion Toss, not surprisingly, is absolutely right.
Also With This Article
Original Sept. 1, 2001 issue with full report, tables, and data
As a mechanical engineer I love quantitative tests like this even though I dont do high performance sailing. Alas, all 3 links to charts were broken so I couldn’t see the good stuff.
I use 10mm Endura Braid from NERopes for my main halyard (42′ sloop). I tie a bowline directly to the headboard eye. When I lowered the sail I noticed that the core had pulled loose from the bowline. I trimmed the end and then sewed the core to the cover for about a foot with a stitch every cm forward and back and then repeat at 90 degrees. I haven’t had a problem since then.
My running backs are 10mm Endura 12, a hollow core line with no cover. I use an unlocked brummel splice about six tucks back and forth, then bury the line for about a foot and sew as above.
Darrell: I am a paid mail subscriber but may have missed this article. If not it is one of the important ones to publish because of just what you said… sailors tying knots instead of splicing because of cost. Plus the buntline hitch eliminates the long area of doubled diameter of a high tech splice which can’t go over a properly sized sheave and thus prevent full hoist. And as the comment above error 404 for all three links, the meat of the results. Please forward the charts of fix the links.
All 3 links broken
Important: as I use it for main halyard on my cruising catamaran.
I just don’t want to have an unexpected failure on a Gulfstream crossing, could mess up my day.
Thanks,
Yes, all three links are broken, however, I think it is pointless to request anything in this comment forum as it appears to be not monitored.